
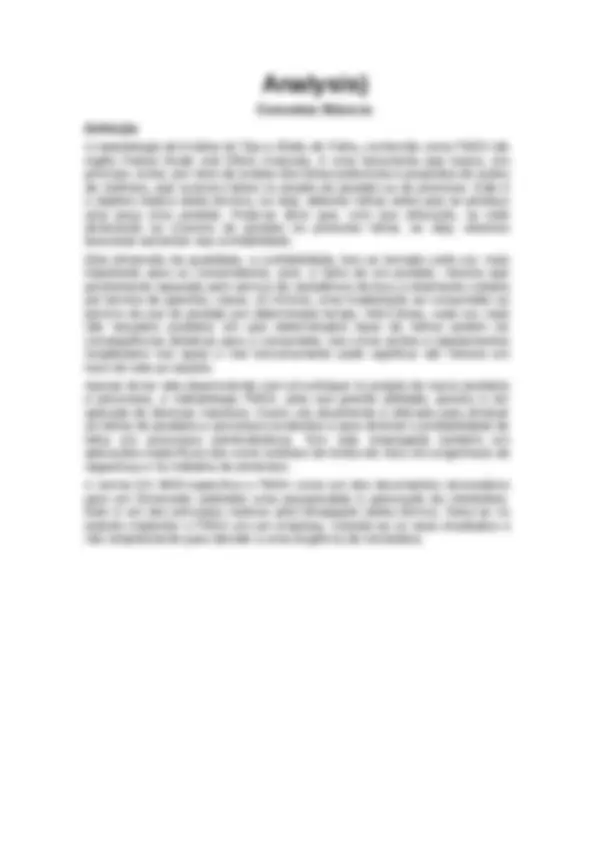
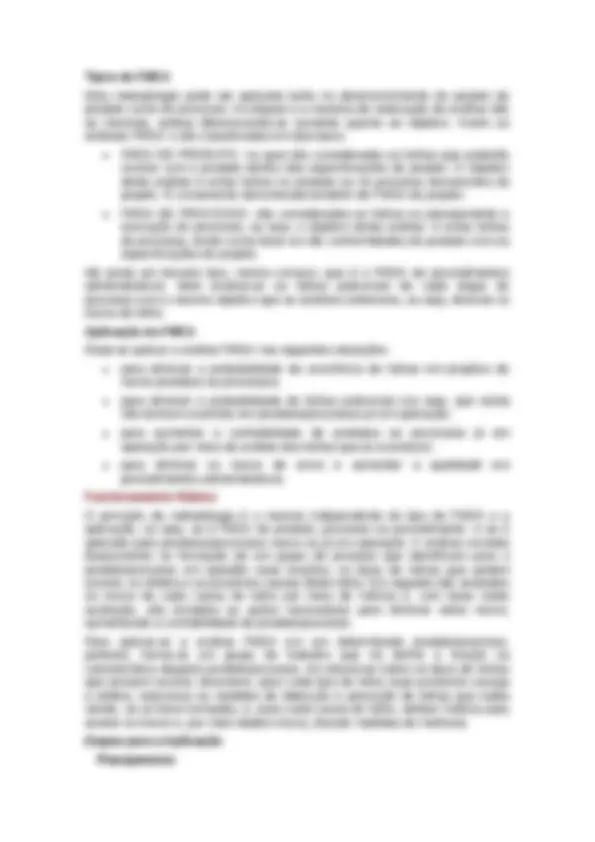
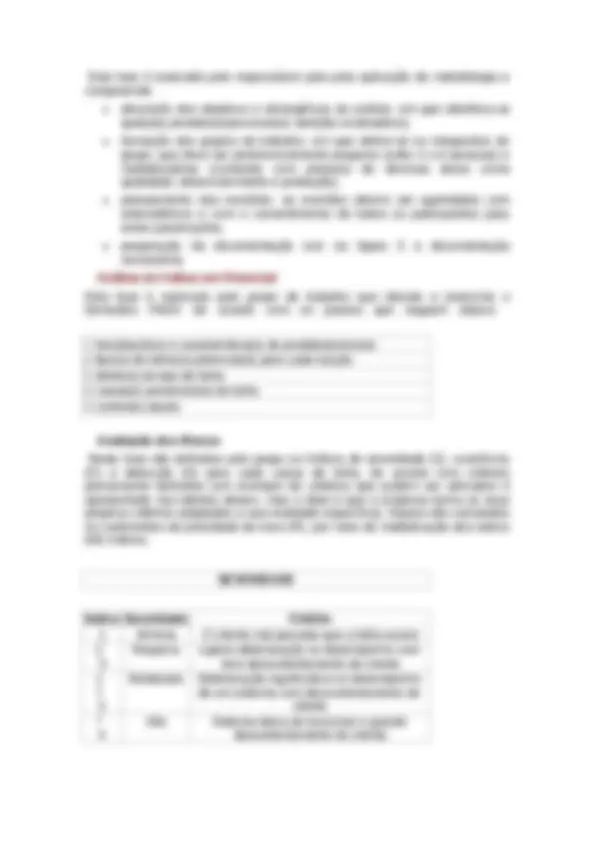
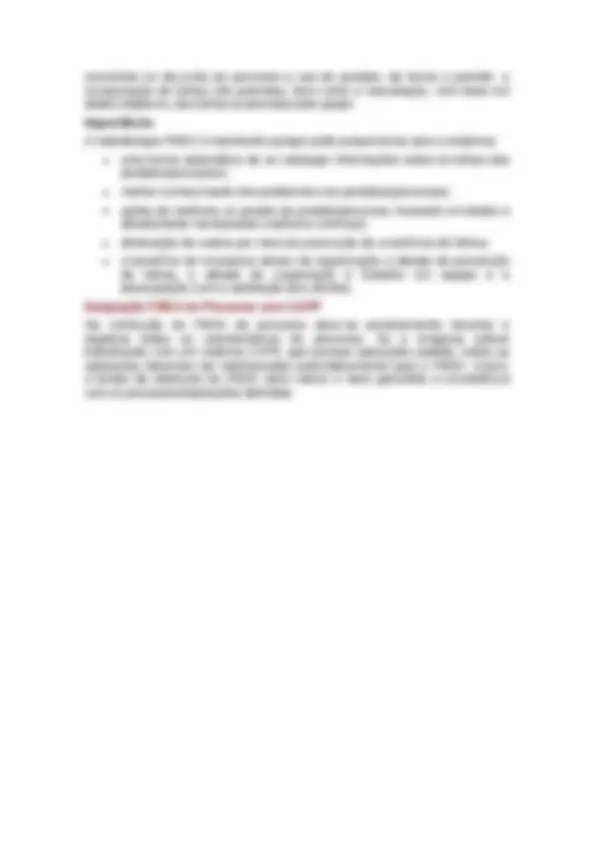
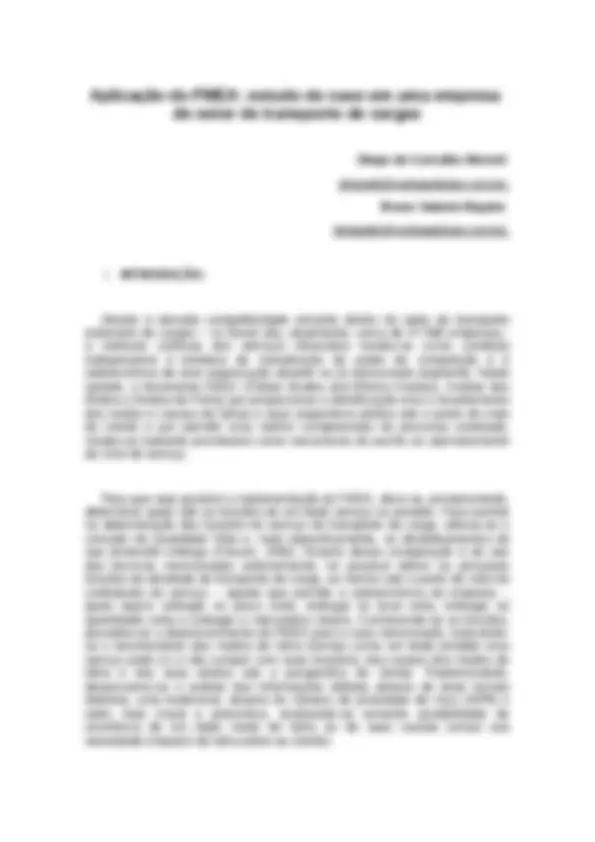
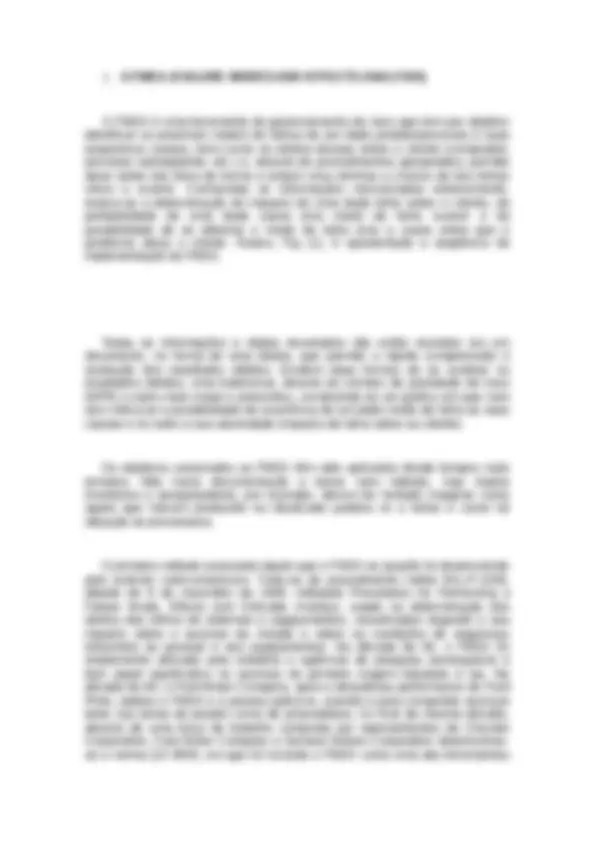
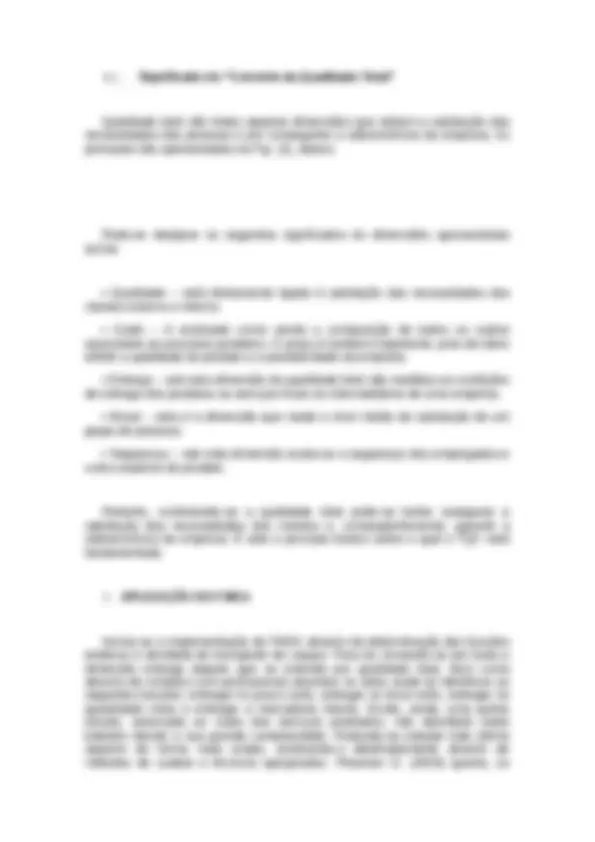

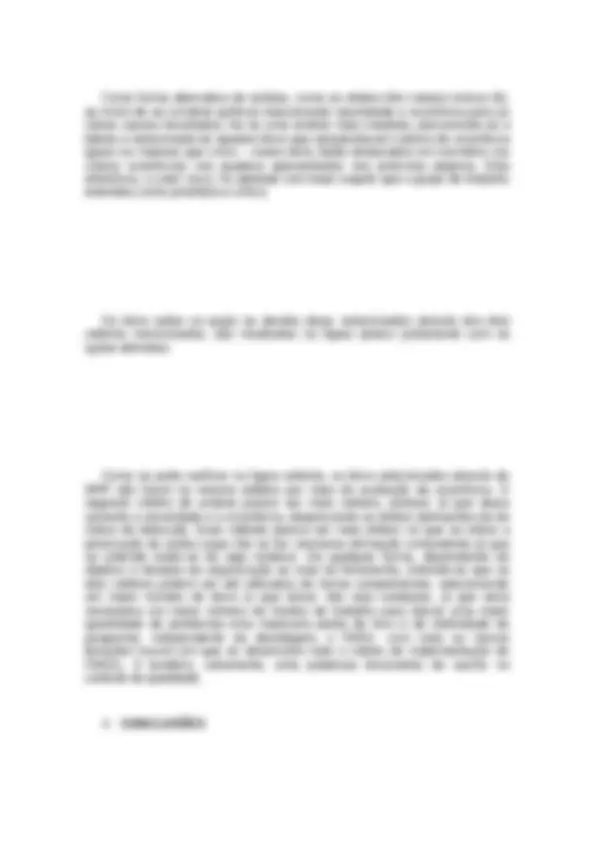
Estude fácil! Tem muito documento disponível na Docsity
Ganhe pontos ajudando outros esrudantes ou compre um plano Premium
Prepare-se para as provas
Estude fácil! Tem muito documento disponível na Docsity
Prepare-se para as provas com trabalhos de outros alunos como você, aqui na Docsity
Os melhores documentos à venda: Trabalhos de alunos formados
Prepare-se com as videoaulas e exercícios resolvidos criados a partir da grade da sua Universidade
Responda perguntas de provas passadas e avalie sua preparação.
Ganhe pontos para baixar
Ganhe pontos ajudando outros esrudantes ou compre um plano Premium
Comunidade
Peça ajuda à comunidade e tire suas dúvidas relacionadas ao estudo
Descubra as melhores universidades em seu país de acordo com os usuários da Docsity
Guias grátis
Baixe gratuitamente nossos guias de estudo, métodos para diminuir a ansiedade, dicas de TCC preparadas pelos professores da Docsity
Estudo de Caso sobre a aplicação do FMEA para melhoria da qualidade em empresa do ramo de transportes.
Tipologia: Trabalhos
1 / 17
Esta página não é visível na pré-visualização
Não perca as partes importantes!
FMEA (Failure Model and Effect
Tipos de FMEA
Esta metodologia pode ser aplicada tanto no desenvolvimento do projeto do produto como do processo. As etapas e a maneira de realização da análise são as mesmas, ambas diferenciando-se somente quanto ao objetivo. Assim as análises FMEA´s são classificadas em dois tipos:
Há ainda um terceiro tipo, menos comum, que é o FMEA de procedimentos administrativos. Nele analisa-se as falhas potenciais de cada etapa do processo com o mesmo objetivo que as análises anteriores, ou seja, diminuir os riscos de falha.
Aplicação da FMEA
Pode-se aplicar a análise FMEA nas seguintes situações:
Funcionamento Básico
O princípio da metodologia é o mesmo independente do tipo de FMEA e a aplicação, ou seja, se é FMEA de produto, processo ou procedimento e se é aplicado para produtos/processos novos ou já em operação. A análise consiste basicamente na formação de um grupo de pessoas que identificam para o produto/processo em questão suas funções, os tipos de falhas que podem ocorrer, os efeitos e as possíveis causas desta falha. Em seguida são avaliados os riscos de cada causa de falha por meio de índices e, com base nesta avaliação, são tomadas as ações necessárias para diminuir estes riscos, aumentando a confiabilidade do produto/processo.
Para aplicar-se a análise FMEA em um determinado produto/processo, portanto, forma-se um grupo de trabalho que irá definir a função ou característica daquele produto/processo, irá relacionar todos os tipos de falhas que possam ocorrer, descrever, para cada tipo de falha suas possíveis causas e efeitos, relacionar as medidas de detecção e preveção de falhas que estão sendo, ou já foram tomadas, e, para cada causa de falha, atribuir índices para avaliar os riscos e, por meio destes riscos, discutir medidas de melhoria.
Etapas para a Aplicação
Planejamento
Esta fase é realizada pelo responsável pela pela aplicação da metodologia e compreende:
Esta fase é realizada pelo grupo de trabalho que discute e preenche o formulário FMEA de acordo com os passos que seguem abaixo:
1 função(ções) e característica(s) do produto/processo
2 tipo(s) de falha(s) potencial(is) para cada função
3 efeito(s) do tipo de falha
4 causa(s) possível(eis) da falha
5 controles atuais
Avaliação dos Riscos Nesta fase são definidos pelo grupo os índices de severidade (S), ocorrência (O) e detecção (D) para cada causa de falha, de acordo com critérios previamente definidos (um exemplo de critérios que podem ser utilizados é apresentado nas tabelas abaixo, mas o ideal é que a empresa tenha os seus próprios critérios adaptados a sua realidade específica). Depois são calculados os coeficientes de prioridade de risco (R), por meio da multiplicação dos outros três índices.
Índice Severidade Critério 1 Mínima O cliente mal percebe que a falha ocorre 2 3
Pequena Ligeira deterioração no desempenho com leve descontentamento do cliente 4 5 6
Moderada Deterioração significativa no desempenho de um sistema com descontentamento do cliente 7 8
Alta Sistema deixa de funcionar e grande descontentamento do cliente
Índice Detecção Critério
1 2
Muito grande Certamente será detectado
Grande Grande probabilidade de ser detectado
Moderada Provavelmente será detectado
Pequena Provavelmente não será detectado
Muito pequena Certamente não será detectado
Observações Importantes:
Continuidade
O formulário FMEA é um documento “vivo”, ou seja, uma vez realizada uma análise para um produto/processo qualquer, esta deve ser revisada sempre que ocorrerem alterações neste produto/processo específico. Além disso, mesmo que não haja alterações deve-se regularmente revisar a análise confrontando as falhas potenciais imaginadas pelo grupo com as que realmente vem
ocorrendo no dia-a-dia do processo e uso do produto, de forma a permitir a incorporação de falhas não previstas, bem como a reavaliação, com base em dados objetivos, das falhas já previstas pelo grupo. Importância A metodologia FMEA é importante porque pode proporcionar para a empresa:
Na confecção do FMEA de processo deve-se primeiramente levantar e registras todas as características do processo. Se a empresa estiver trabalhando com um sistema CAPP, que possua operações padrão, todas as operações deveriam ser interfaceadas automaticamente para o FMEA. Assim, o tempo de obtenção do FMEA seria menor e seira garantida a consistência com os processos/operações definidas.
O FMEA é uma ferramenta de gerenciamento de risco que tem por objetivo identificar os possíveis modos de falhas de um dado produto/processo e suas respectivas causas, bem como os efeitos dessas sobre o cliente (comprador, processo subseqüente, etc.) e, através de procedimentos apropriados, permite atuar sobre tais itens de forma a reduzir e/ou eliminar a chance de tais falhas virem a ocorrer. Conhecidas as informações mencionadas anteriormente, realiza-se a determinação do impacto de uma dada falha sobre o cliente, da probabilidade de uma dada causa e/ou modo de falha ocorrer e da possibilidade de se detectar o modo de falha e/ou a causa antes que o problema atinja o cliente. Abaixo, Fig (1), é apresentada a seqüência de implementação do FMEA.
Todas as informações e dados levantados são então reunidos em um documento, na forma de uma tabela, que permite a rápida compreensão e avaliação dos resultados obtidos. Existem duas formas de se analisar os resultados obtidos, uma tradicional, através do número de prioridade de risco (NPR) e outra mais visual e preventiva, construindo-se um gráfico em que num eixo indica-se a possibilidade de ocorrência de um dado modo de falha ou suas causas e no outro a sua severidade (impacto da falha sobre ao cliente).
Os objetivos associados ao FMEA têm sido aplicados desde tempos mais remotos. Não havia documentação e talvez nem método, mas muitos inventores e pesquisadores, por exemplo, devem ter tentado imaginar como aquilo que haviam produzido ou idealizado poderia vir a falhar e como tal situação se processaria.
O primeiro método associado àquilo que o FMEA se propõe foi desenvolvido pelo exército norte-americano. Trata-se do procedimento militar MIL-P-1629, datado de 9 de novembro de 1949, intitulado Procedures for Performing a Failure Mode, Effects and Criticality Analisys, usado na determinação dos efeitos das falhas de sistemas e equipamentos, classificadas segundo o seu impacto sobre o sucesso da missão e sobre as condições de segurança referentes ao pessoal e aos equipamentos. Na década de 60, o FMEA foi amplamente utilizado pela indústria e agências de pesquisa aeroespacial e teve papel significativo no sucesso da primeira viagem tripulada à lua. Na década de 80, a Ford Motor Company, após a desastrosa performance do Ford Pinto, adotou o FMEA e a passou aplica-lo, usando-o para conquistar avanços tanto nas áreas de projeto como de pmanufatura. Ao final da mesma década, através de uma força de trabalho composta por representantes da Chrysler Corporation, Ford Motor Company e General Motors Corporation desenvolveu- se a norma QS 9000, em que foi incluído o FMEA como uma das ferramentas
de planejamento avançado da qualidade. Em fevereiro de 1993, a AIAG (Automotive Industry Action Group) e a ASQC (American Society for Quality Control) patentearam os padrões relacionados ao FMEA, criando um manual. O mesmo vale para a SAE (Society of Automotive Engineers) detentora do procedimento SAE J-1739 que trata do FMEA.
O modelo de desenvolvimento adotado no Brasil na segunda metade do século XX privilegiou as rodovias como fator de integração da ocupação territorial. Como resultado, a matriz do transporte de cargas foi direcionada para o modal rodoviário.
O transporte rodoviário de cargas é um segmento essencial ao apropriado funcionamento da cadeia logística. É ele, atualmente, ao menos no Brasil, o principal elo entre fornecedor e produtor e deste último com o consumidor. Sem o transporte rodoviário de cargas o ciclo característico da cadeia logística jamais poderia se desenrolar. Trata-se de uma atividade de pujança notória e em relação a qual o Brasil demonstra significativa dependência – o que fica evidente quando se compara o Brasil com outros países de dimensões territoriais similares às suas. Enquanto aqui o modal rodoviário reponde por 60% do total transportado, nos EUA esta participação é de cerca de 26%, na Austrália 24% e na China 8%. Um fator preocupante, e que demonstra a grande aplicabilidade do FMEA no aprimoramento da performance do setor, é o fato de que a produtividade do segmento no Brasil, medida através da quantidade de toneladas quilômetro útil produzida por mão-de-obra empregada no setor, é equivalente a 22% da produtividade dos EUA. Logicamente, cabe destacar, que aqui os problemas são muito amplos e, em geral, fogem da alçada das corporações. Um exemplo é a questão da segurança, tanto no que diz respeito ao roubo de cargas quando aos índices de acidentes e mortes nas rodovias brasileiras. O roubo de cargas nas estradas vem crescendo de forma acelerada. Entre 1994 e 2001, o número de ocorrências por ano cresceu de 3000 para 8000, ao mesmo tempo em que o valor das cargas roubadas passaram de R$ 100 milhões para R$ 500 milhões. Segundo estimativas do programa de redução de acidentes nas estradas do Ministério dos Transportes, os acidentes de trânsito no Brasil são o segundo maior problema de saúde pública do país, só perdendo para a desnutrição. O mesmo estudo indica que o número de mortes por quilômetro em estradas brasileiras é de 10 à 70 vezes superior aos dos países desenvolvidos. Além disso, 62% dos leitos de traumatologia dos hospitais são ocupados por vitimas de acidentes de trânsito (COPPEAD, CNT, 2002).
Outro problema é a insuficiência de infra-estrutura de transporte em termos de extensão e qualidade das vias. Tomando-se como base o indicador de disponibilidade, medido pelo índice km de via por km^2 de espaço territorial, a oferta de vias de transporte no Brasil é equivalente a 69% da verificada na
4.1.. Significado do “Controle da Qualidade Total”
Qualidade total são todas aquelas dimensões que afetam a satisfação das necessidades das pessoas e por conseguinte a sobrevivência da empresa. As principais são apresentadas na Fig. (2), abaixo.
Pode-se designar os seguintes significados às dimensões apresentadas acima:
Portanto, controlando-se a qualidade total pode-se tentar assegurar a satisfação das necessidades dos clientes e, conseqüentemente, garantir a sobrevivência da empresa. É este o princípio básico sobre o qual o TQC está fundamentado.
Iniciou-se a implementação do FMEA através da determinação das funções relativas à atividade de transporte de cargas. Para tal, tomando-se por base a dimensão entrega daquilo que se entende por qualidade total, bem como através de contatos com profissionais atuantes no setor, pode-se identificar as seguintes funções: entregar no prazo certo, entregar no local certo, entregar na quantidade certa e entregar a mercadoria intacta. Existe, ainda, uma quinta função, associada ao custo dos serviços prestados, não abordada neste trabalho devido a sua grande complexidade. Pretende-se estudar este último aspecto de forma mais ampla, analisando-o detalhadamente através de métodos de custeio e técnicas apropriados. Plowman G. (2003) aponta, os
“cinco certos” de um sistema logístico são: fornecer ao consumidor o produto certo, no momento certo, no lugar certo e nas condições certas pelo custo certo. Apoiando-se nas funções, agora conhecidas, e seguindo o roteiro de aplicação do FMEA, Tab (1), procurou-se, através de cessões de brainstorming, das quais participaram profissionais atuantes no segmento em estudo, determinar quais seriam os modos de falha (já bastante óbvios, devido a especificidade das funções) e o efeito destes - sob a perspectiva do cliente. As informações obtidas são mostradas na tabela abaixo.
Aos resultados obtidos relativos aos modos de falha foram atribuídos valores, conhecidos como ocorrência, referentes á probabilidade desses se desenvolverem. O mesmo foi feito em relação aos efeitos encontrados. A eles foram associados valores relacionados à gravidade do impacto que esses produziram no cliente. Tal índice é denominado severidade. Os valores de ocorrência e severidade variam de 1 a 10 e representam, respectivamente, em ordem crescente, a probabilidade de ocorrência de um dado modo de falha e/ ou de uma dada causa e a gravidade do impacto de um dado modo de falha sobre o cliente.
Em seguida, novamente através de cessões de brainstorming, procurou-se levantar as prováveis causas dos modos de falha, para as quatro funções mencionadas. Como exemplo, os resultados obtidos para a função de entregar no prazo certo são apresentados abaixo, Fig (3). Para tornar a visualização mais fácil, os resultados obtidos são apresentados através de árvores de decisão. Nelas, pode-se perceber que as causas estão estratificadas em dois níveis. Tais níveis são resultado das várias rodadas de brainstorming efetuadas na tentativa de se chegar às causas primárias, básicas.
Com base nas informações obtidas nos passos anteriores, foram avaliados os controles e formas de detecção das causas potencias, associando-se aos mesmos valores referentes á sua eficácia. Tais valores variam de 1 a 10 e representam, em ordem decrescente, a possibilidade de se detectar uma dada causa e/ou modo de falha (ao valor um associa-se a total possibilidade de detecção e ao dez possibilidade remota).
Após terem sido determinadas todas as informações necessárias, passou- se ao preenchimento do formulário característico do FMEA. Os resultados são mostrados na página seguinte.
Definiu-se - consenso da equipe envolvida no trabalho -, que se deveria atuar sobre os itens com NPR superior a 150. Desta forma, como pode ser visto no formulário mostrado a seguir, destacaram-se, em vermelho (na coluna NPR), os itens que se enquadravam nesse grupo e a cada um deles foi atribuída uma ou mais ações, de forma a permitir, quando implementadas, a redução do NPR.
Pôde-se concluir, através deste trabalho, que o FMEA mostra-se uma como uma ferramenta de grande utilidade no que se refere ao controle da qualidade. Através da aplicação das duas diferentes abordagens de análise foi possível analisar o comportamento de ambas e verificar que as duas são válidas, estando o uso de uma ou de outra associado às intenções e condições da organização quando da utilização do FMEA. Neste caso, se fosse desejado atacar, de forma mais efetiva, um menor número de itens (otimizando recursos) provavelmente a abordagem visual, gráfica seria mais interessante.
Falconi, V. C., 1992, “TQC Controle da Qualidade Total (no estilo japonês)”, Editora EDG, São Paulo, Brasil.
Guerra A., 2003, “A Logística Ainda Continua Uma Promessa”, Brazil.
COPPEAD, CNT, 2002, “Transporte de Carga no Brasil – Ameaças e Oportunidades para o Desenvolvimento do País”, Rio de Janeiro, Brasil, 20p.
FIESP, 2002, “Pontos Fundamentais para a Indústria na Área de Logística de Transporte de Carga”, São Paulo, Brasil, 19p.
Hammet, P., 2000, “Failure Modes and Effects Analysis, Michigan, USA, 9p.
Bibliografia
Manuais da QS 9000. Análise de Modo e Efeitos de Falha Potencial (FMEA): Manual de Referência. 1997.
CLAUSING, D. (1994). Better decisions. In:Total quality development: a step-by- step guide to worldclass concurrent engineering. 2.ed., Nova Iorque, The American Society of Mechanical Engineers. Cap. 3, p.60-73. (t: 322). (Disponível na biblioteca da EESC - USP).
CLAUSING, D. (1994). The design. In:Total quality development : a setp-by-step guide to worldclass concurrent engineering. 2. ed., Nova Iorque, The American Society of Mechanical Engineerss. Cap. 5, p. 175-273. (t: 322). (Disponível na biblioteca da EESC - USP).
OLIVEIRA, C. B. M.; ROZENFELD, H. (1997). Desenvolvimento de um módulo de FMEA num sistema comercial de CAPP. (CD ROM). In: ENCONTRO NACIONAL DE ENGENHARIA DE PRODUÇÃO,17., Gramado, 1997. Anais. Porto Alegre, UFRGS. (t :662).
Quality Associates International http://www.quality-one.com/ Empresa de consultoria e treinamento em qualidade. Apresenta conteúdo básico sobre FMEA, além de outras ferramentas como QFD e QS 9000.
A empresa KSR (http://www.ksr.com.br) possui um sistema de confeçcão de FMEA integrado com um sistema CAPP, que já garantiu a várias empresas a cerificação da QS 90000. Na página da KSR tem um local onde várias perguntas práticas sobre um FMEA são respondidas (http://www.ksr.com.br/ oqufmea.htm).