
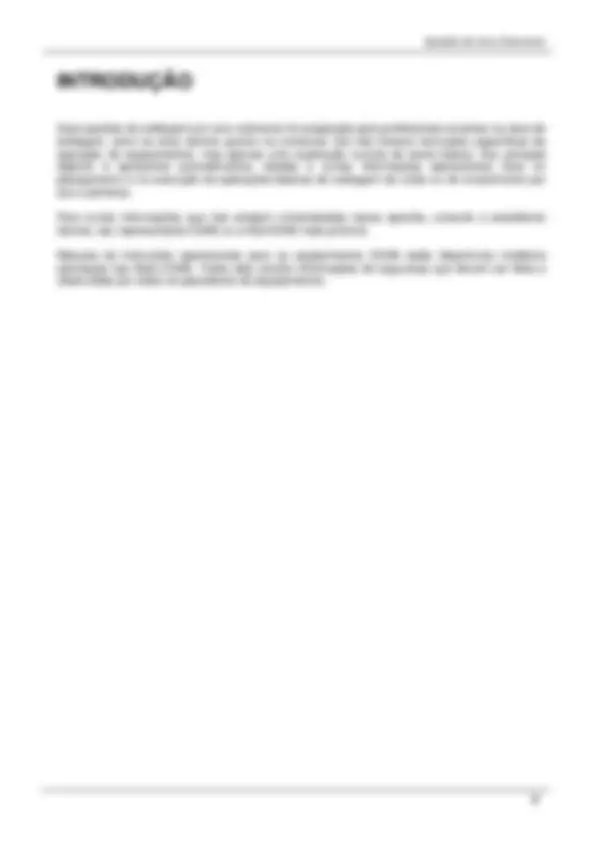
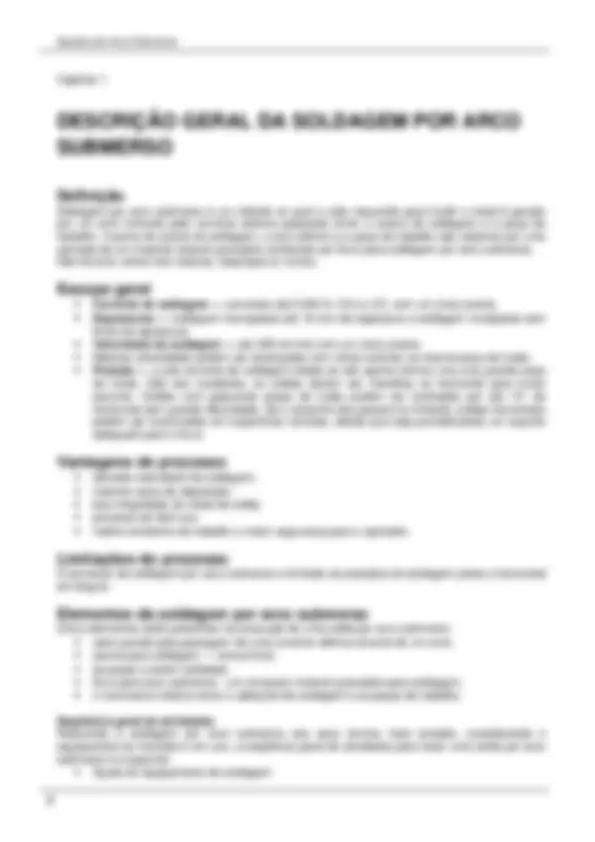
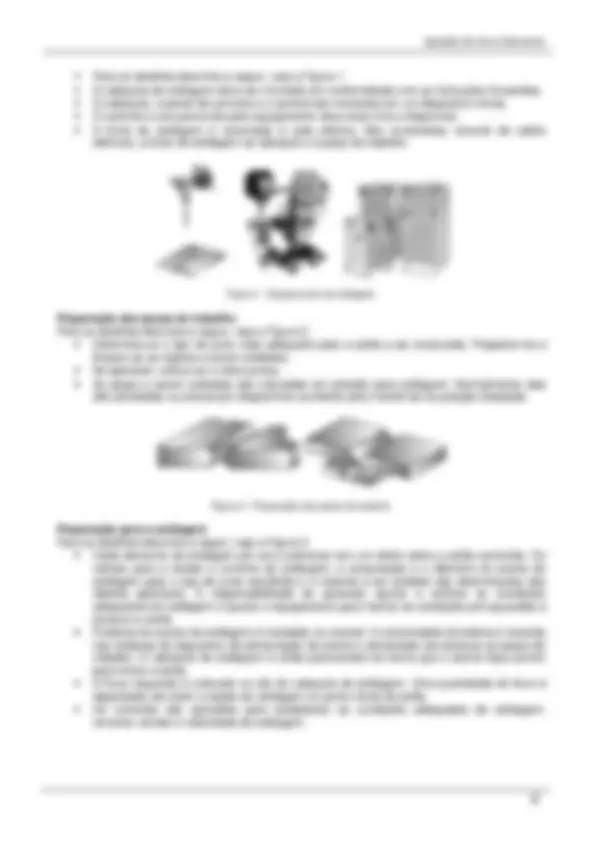
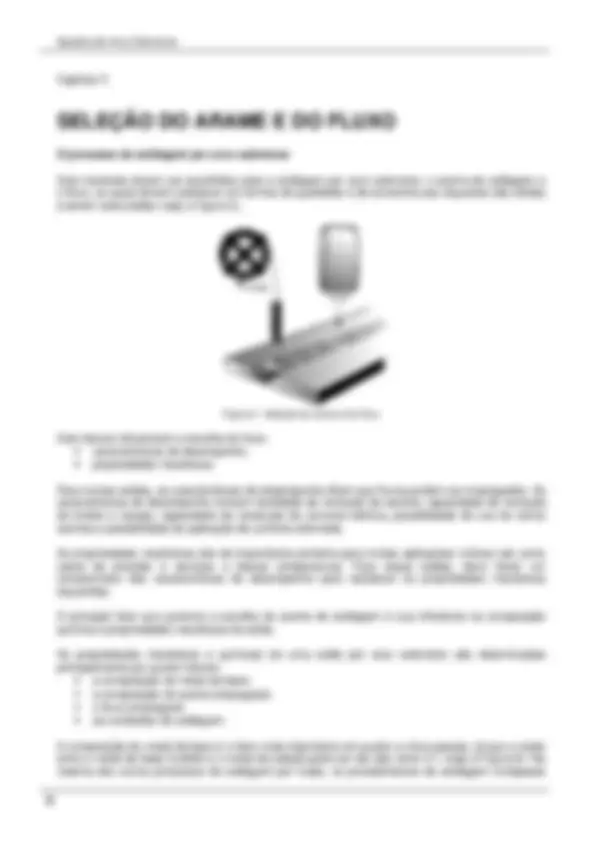
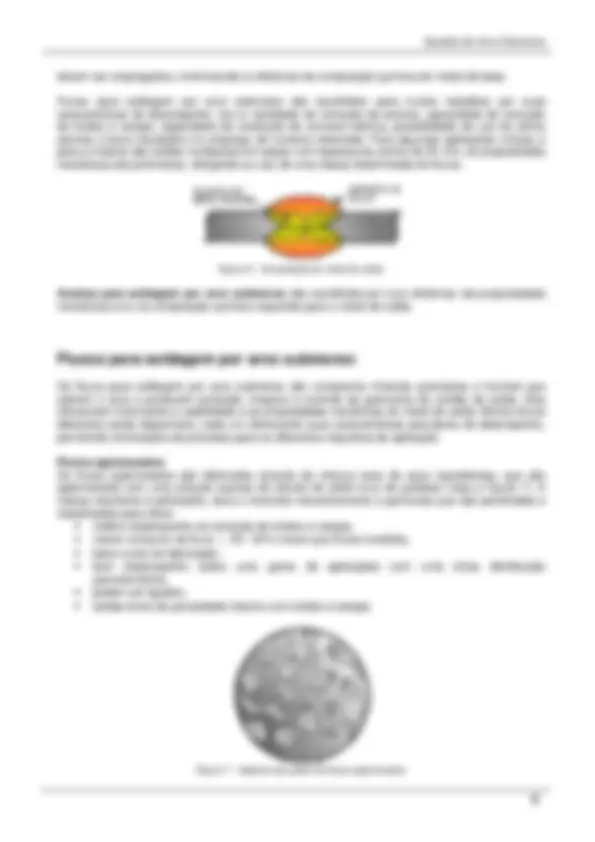
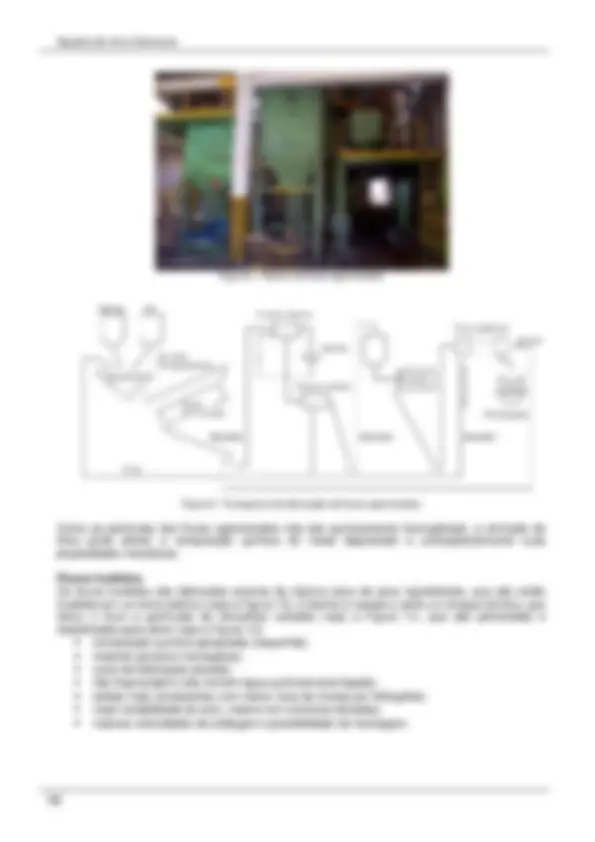
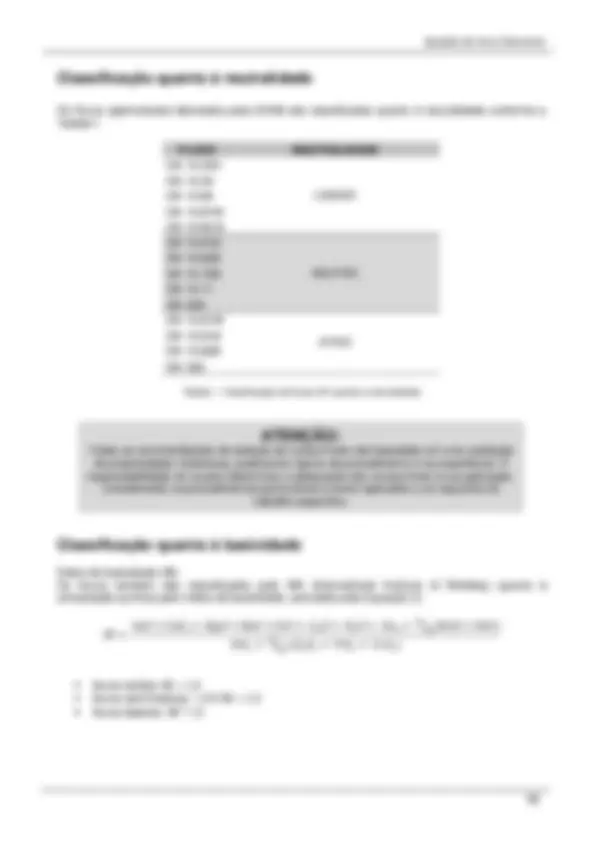
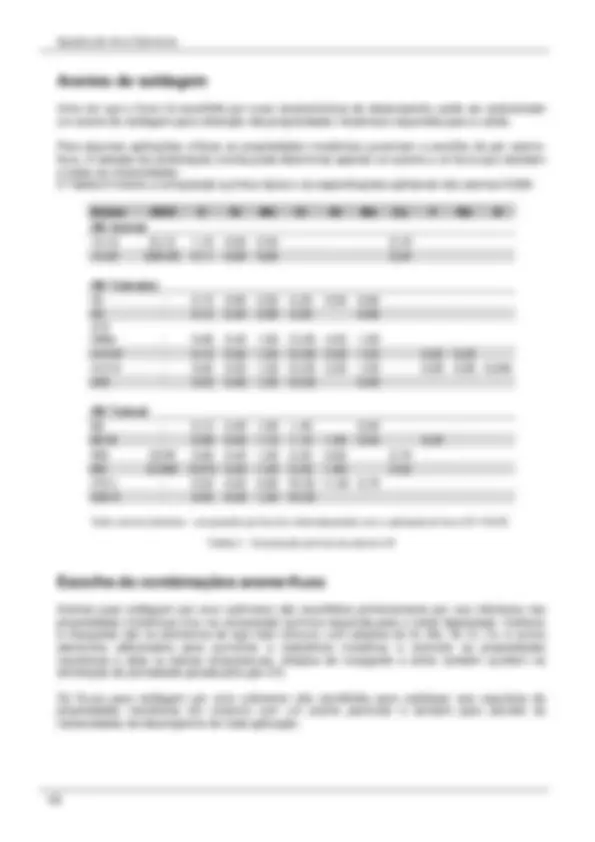
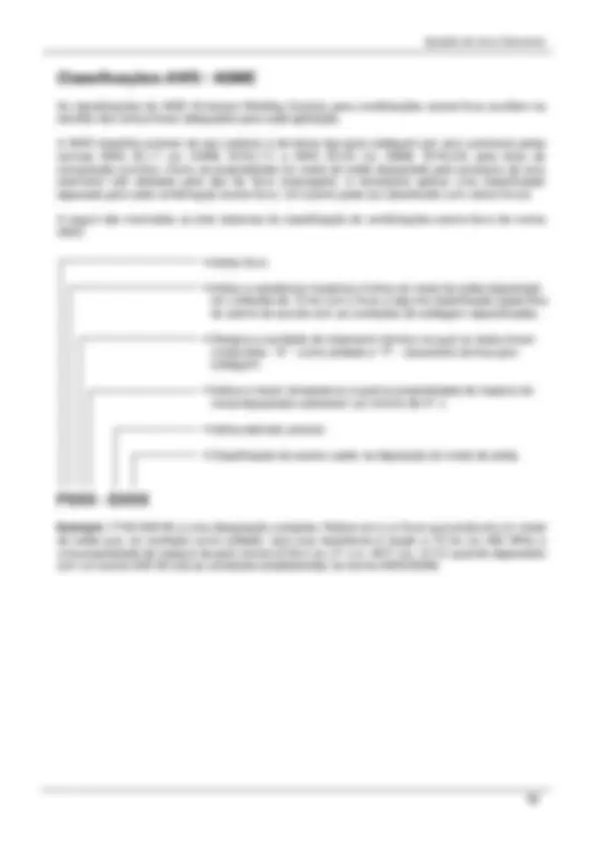
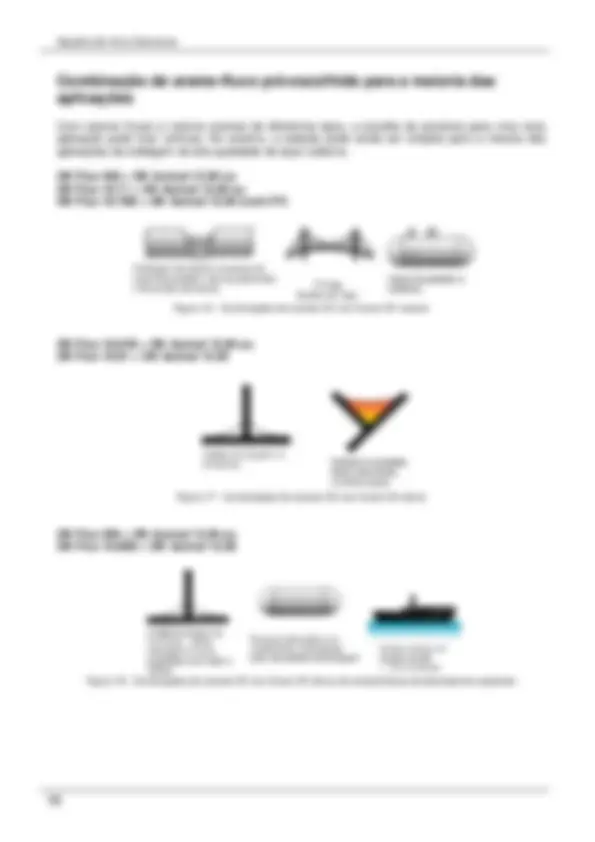
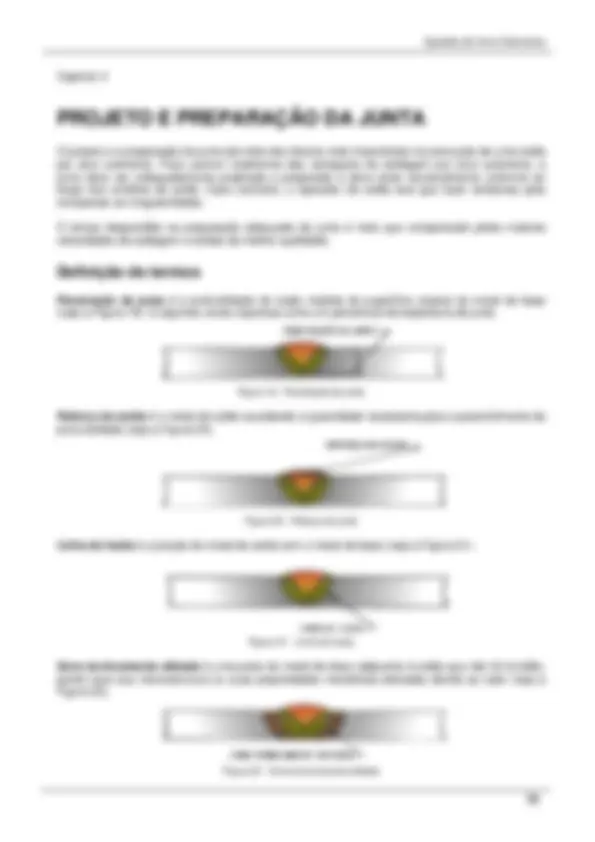
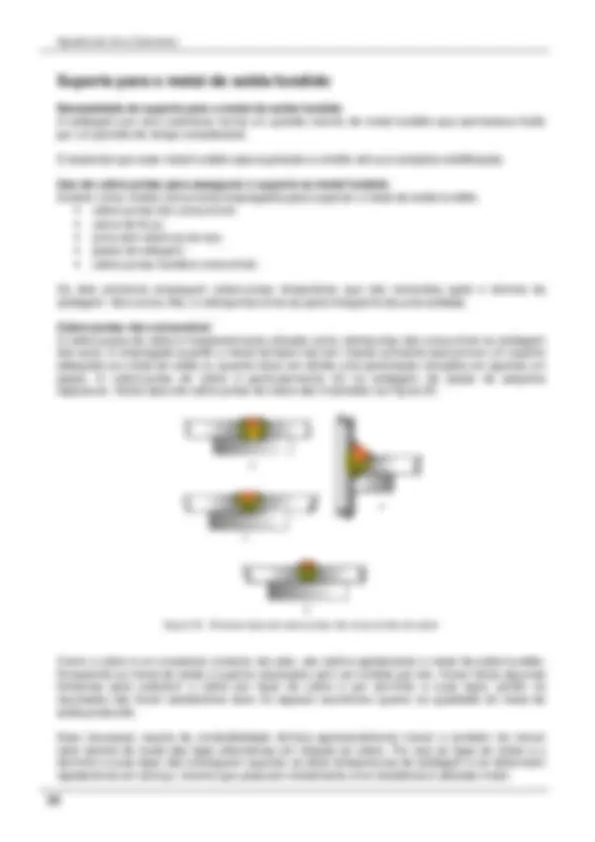
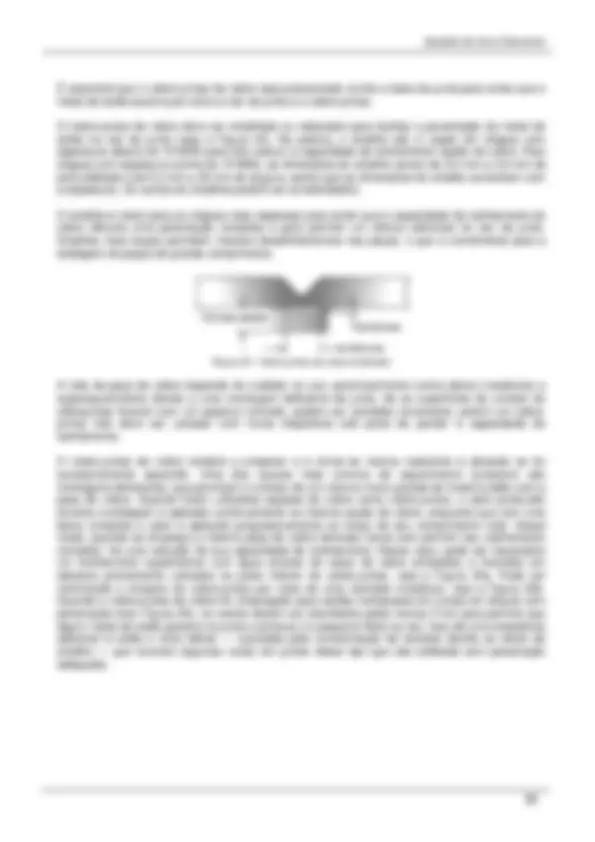
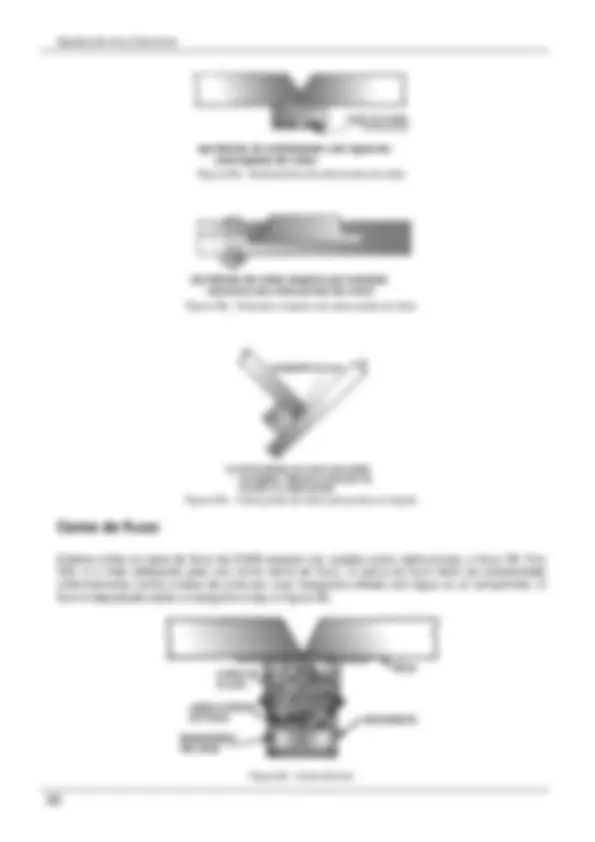
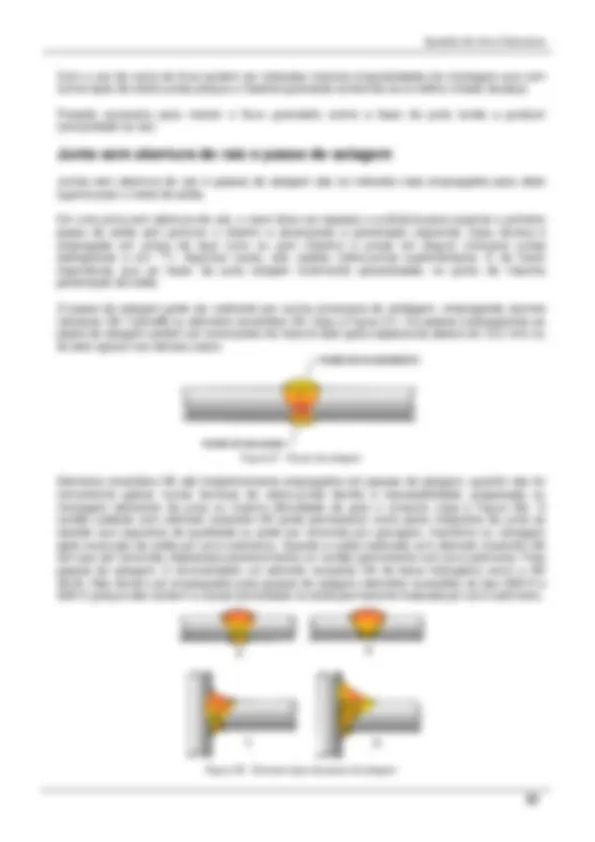
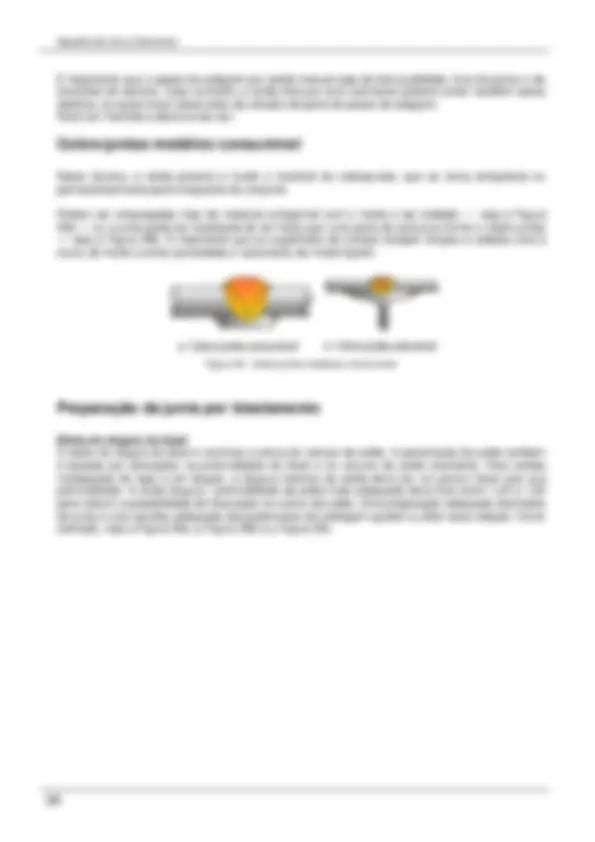
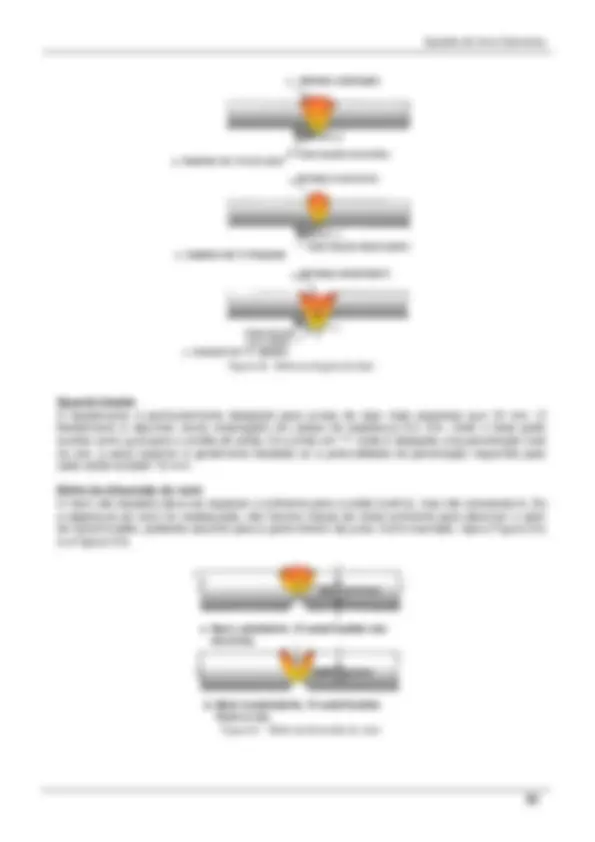
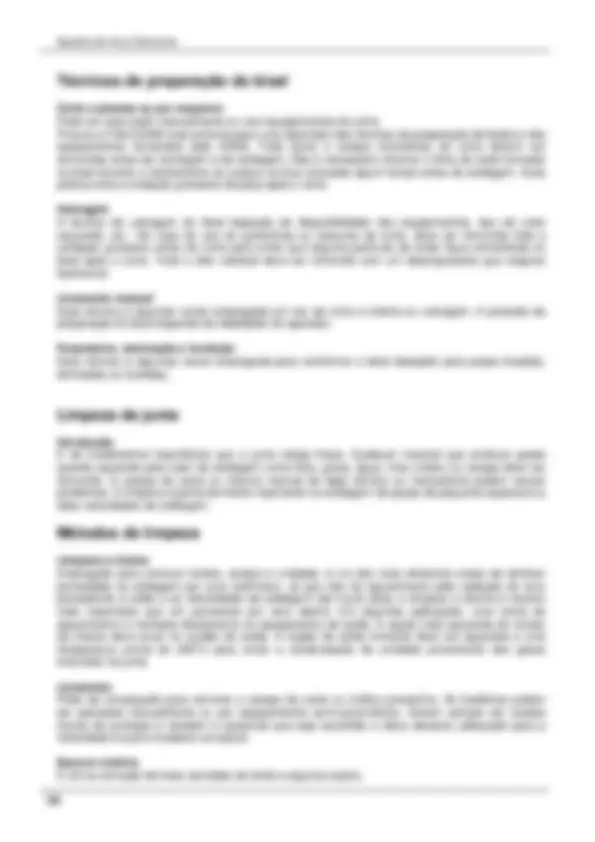
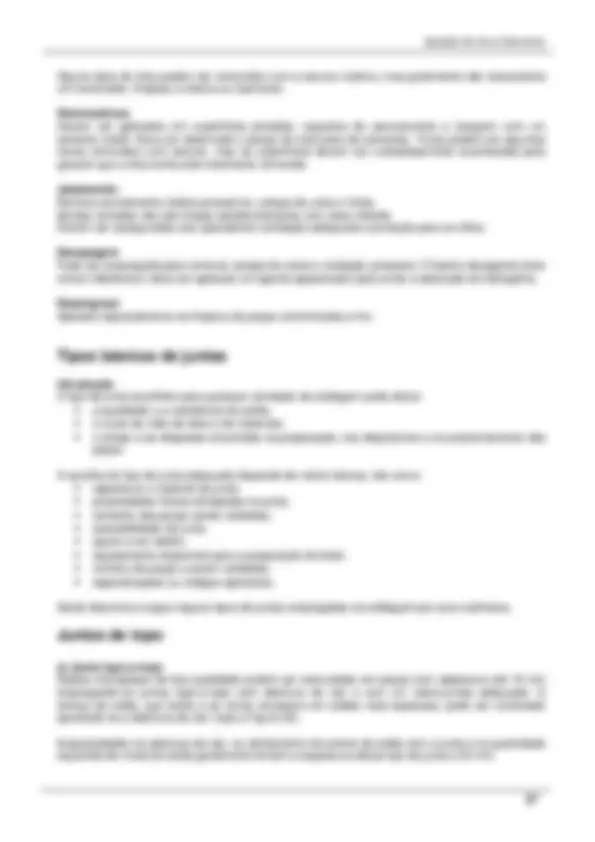
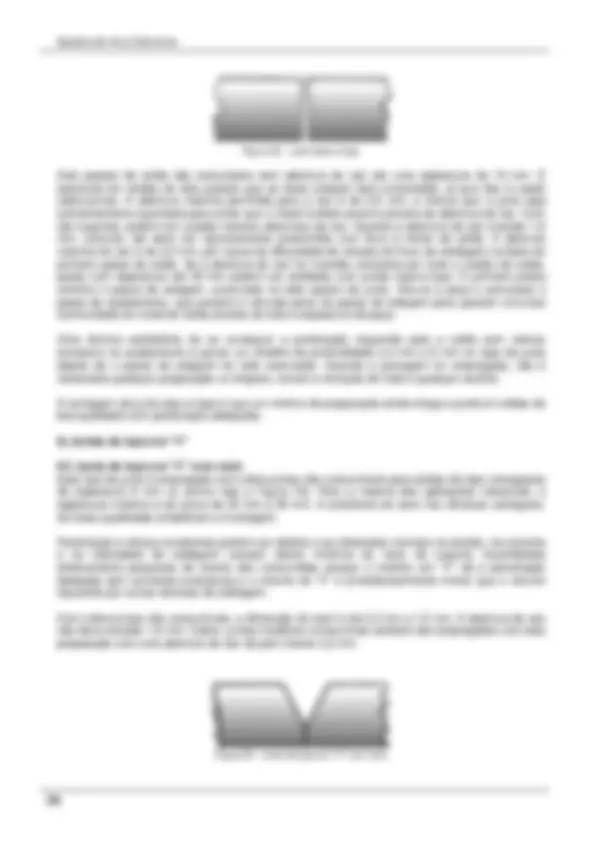
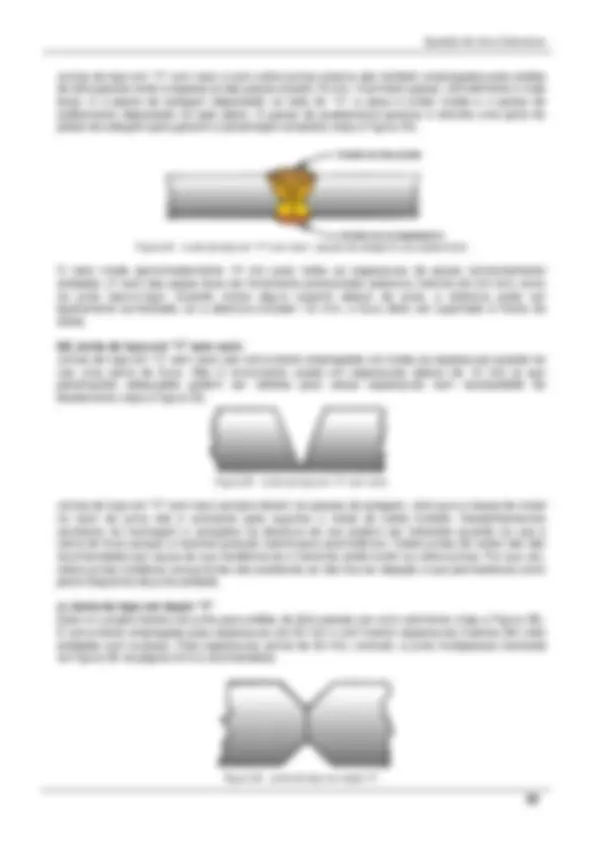
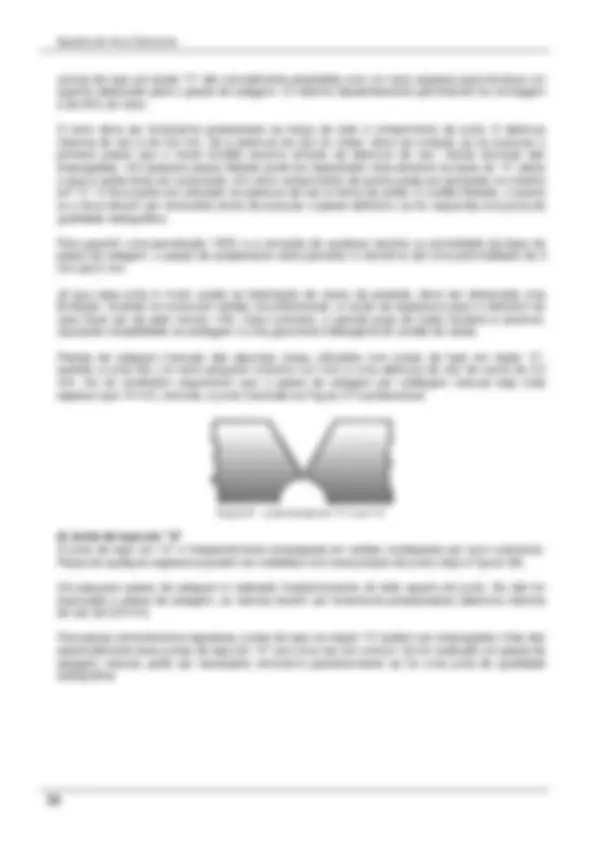
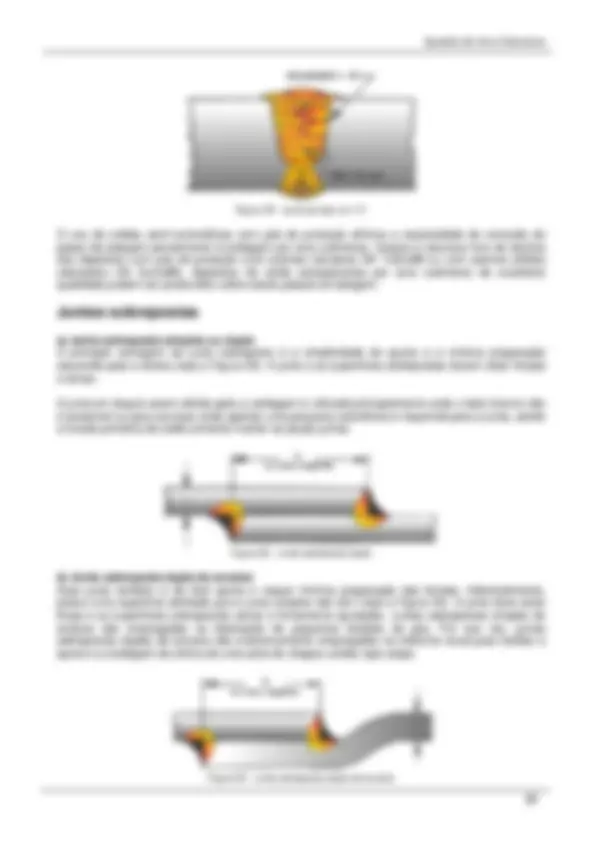
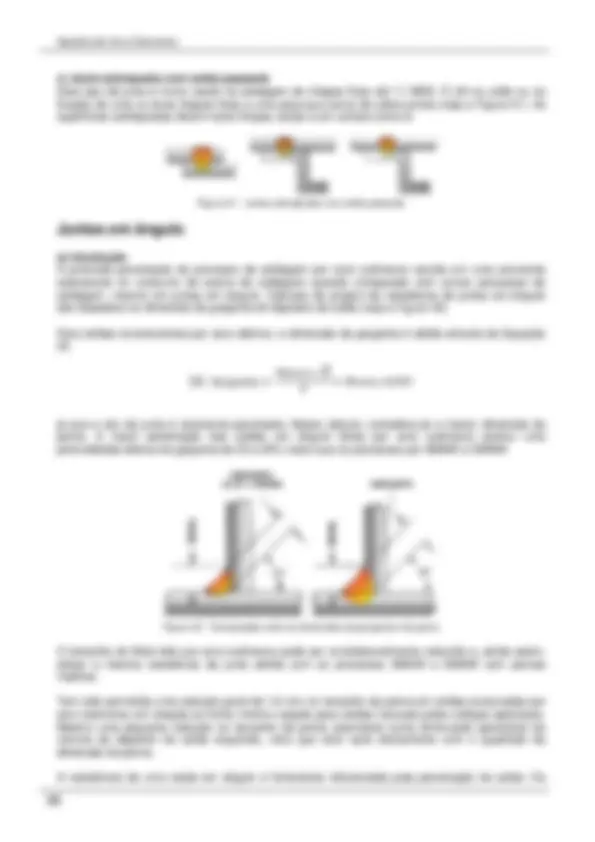
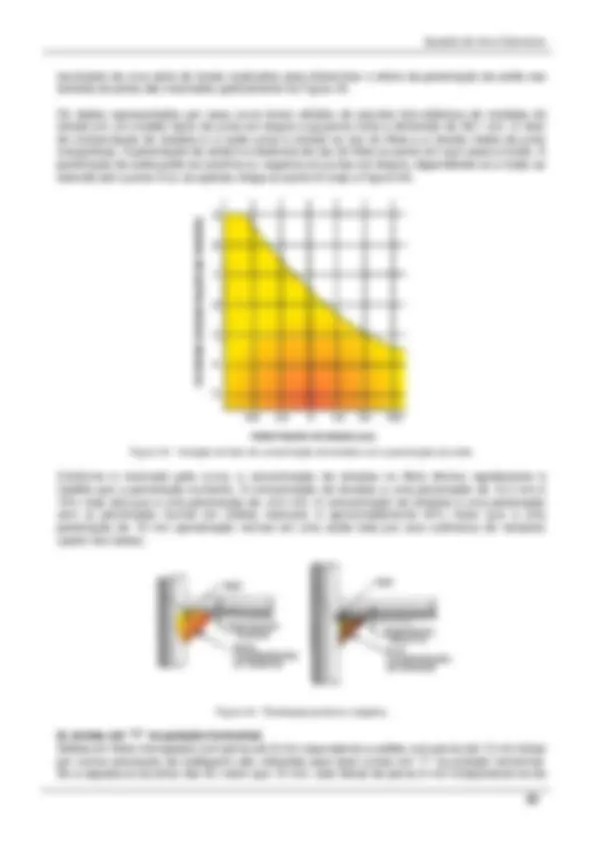
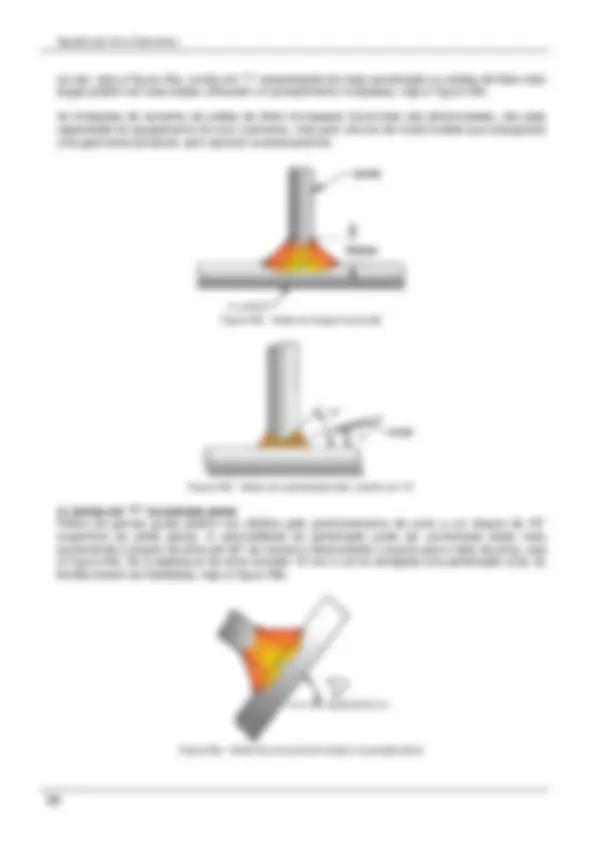
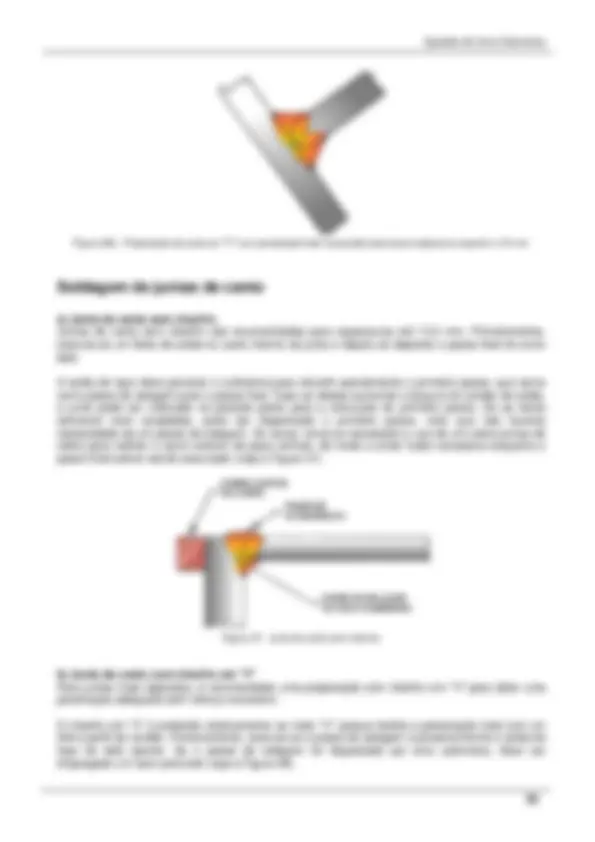
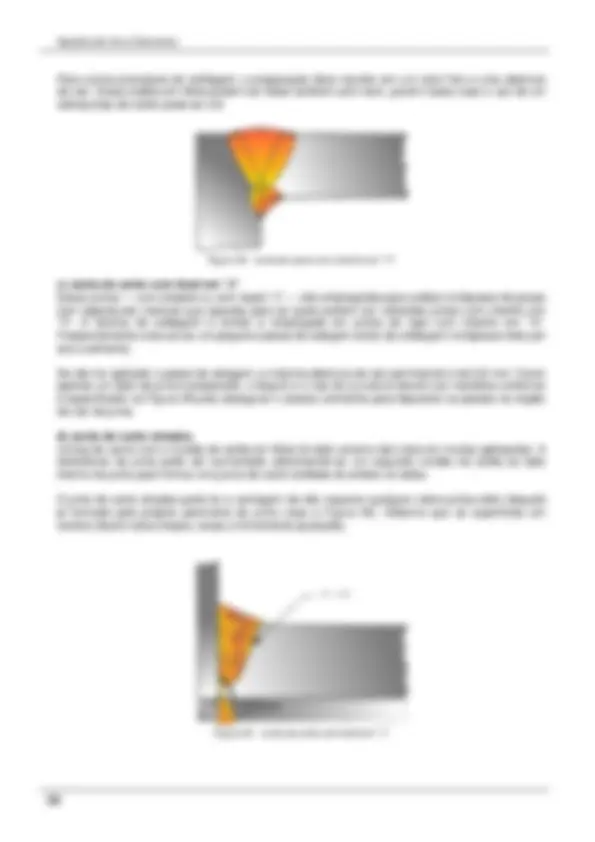
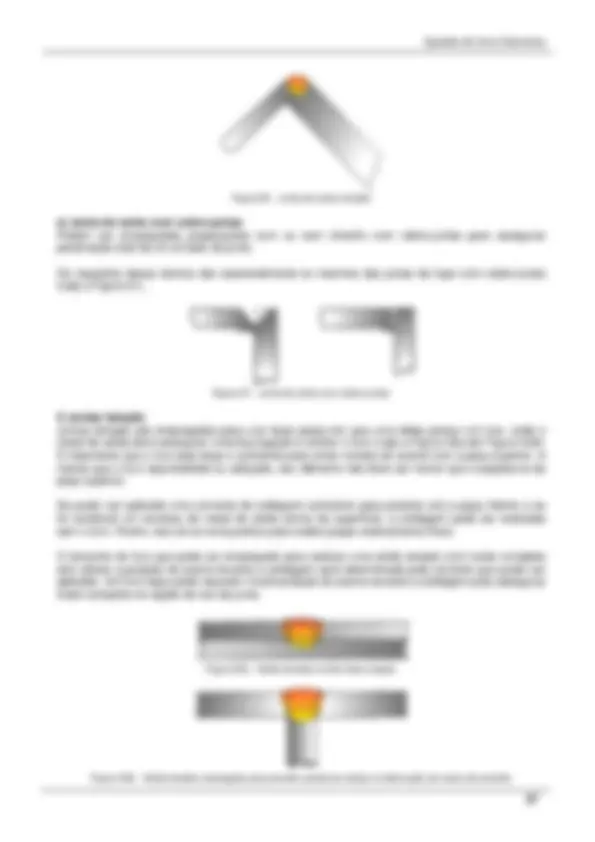
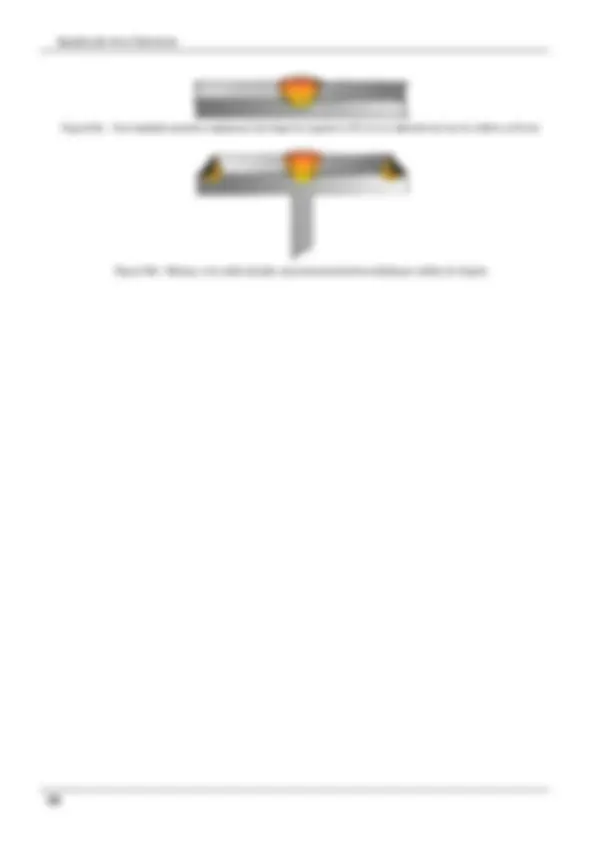
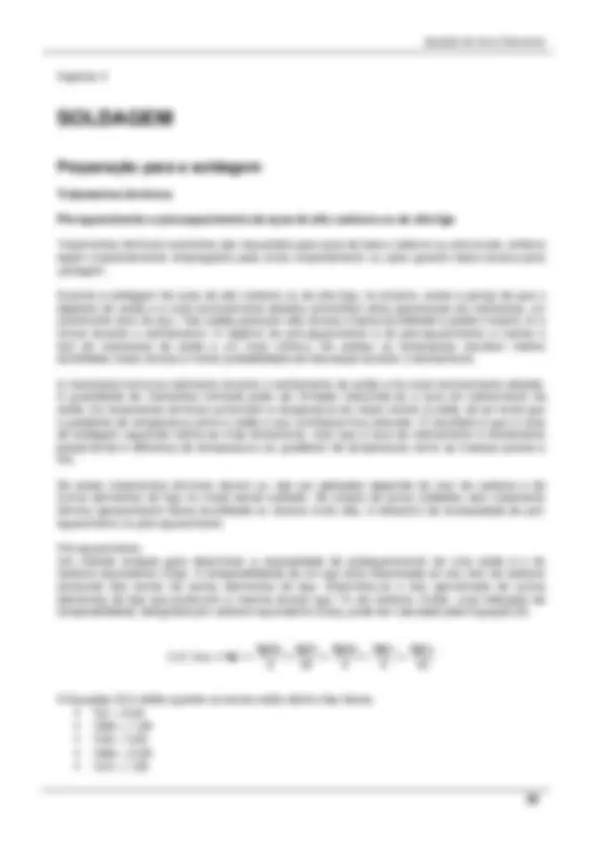
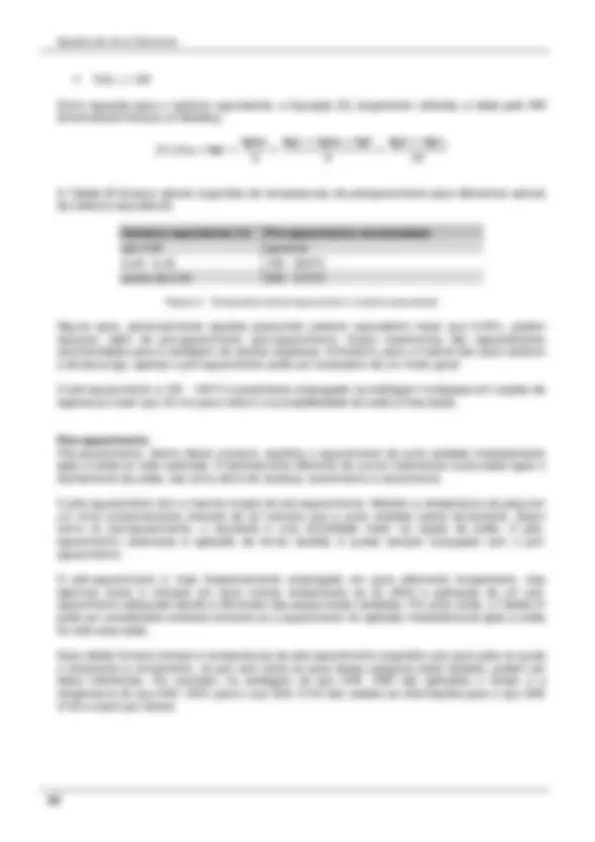
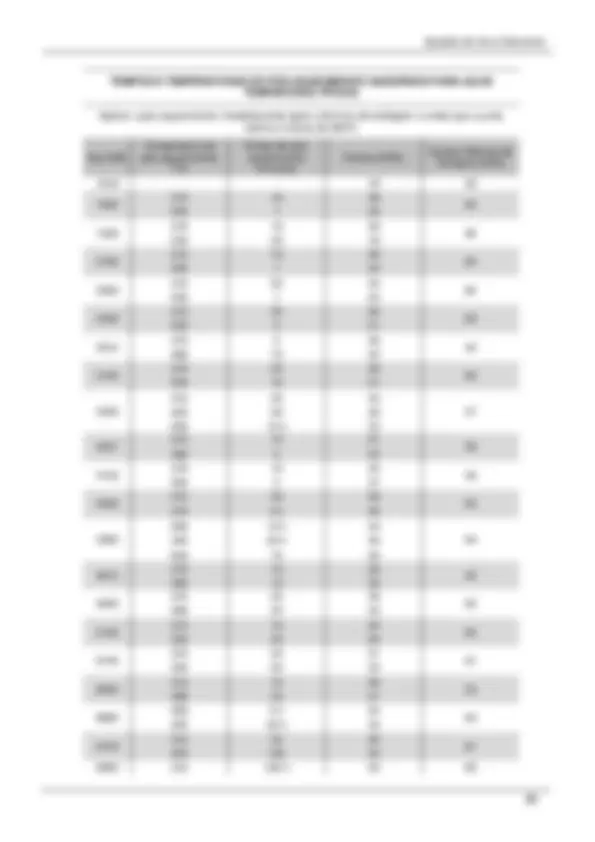
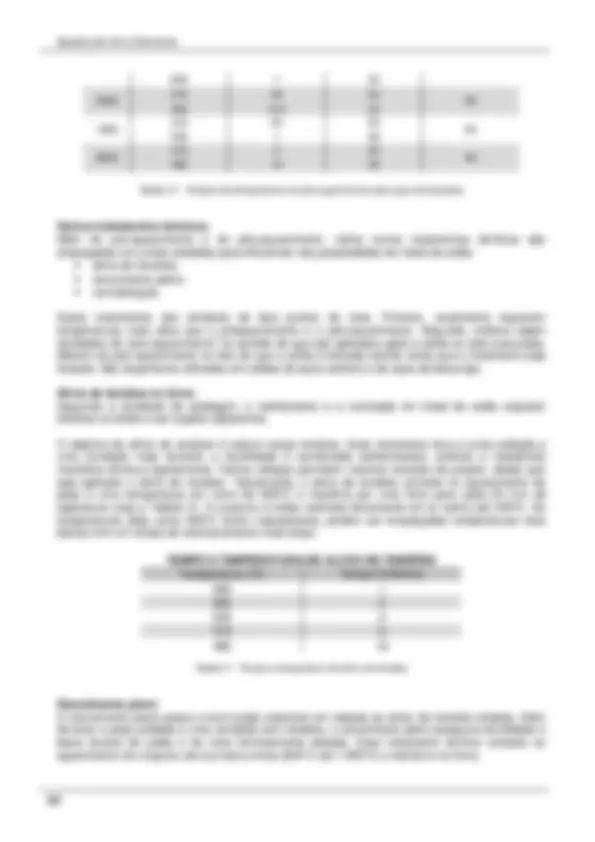
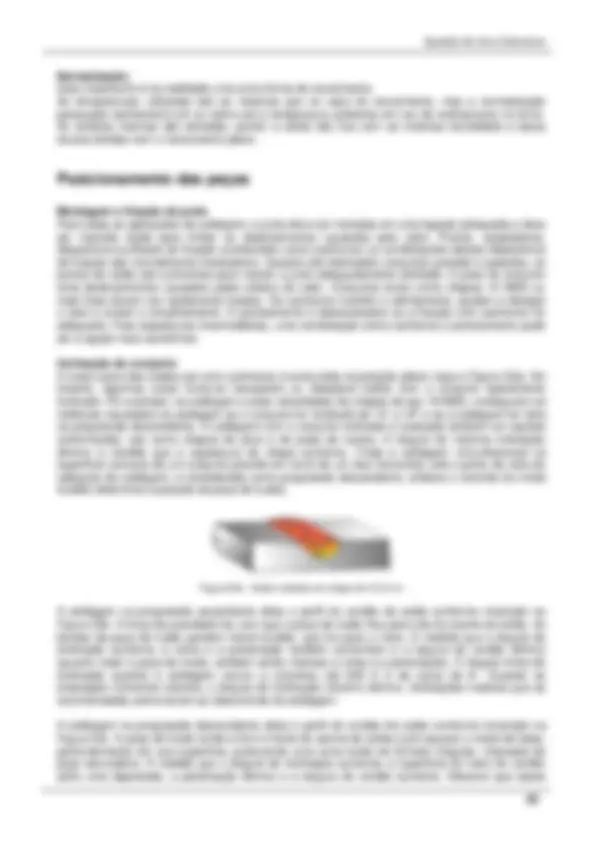
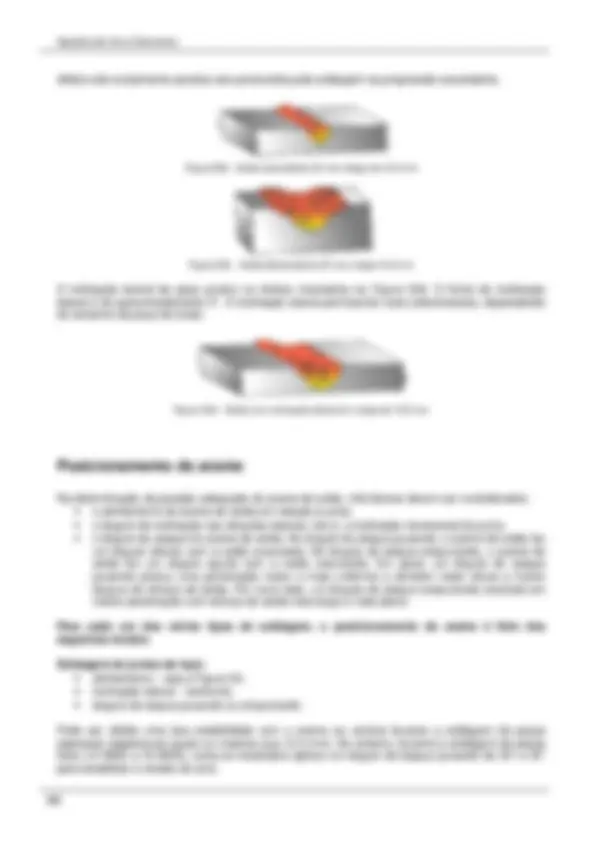
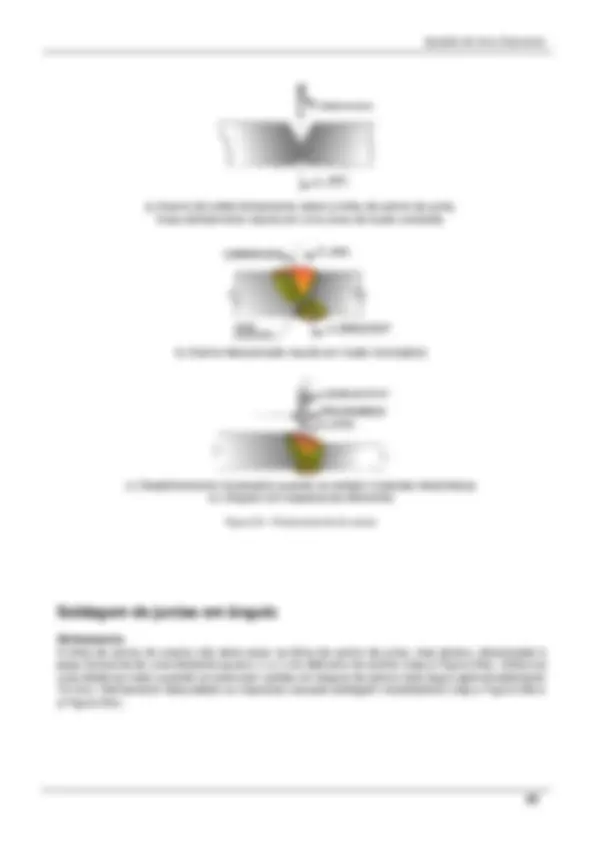
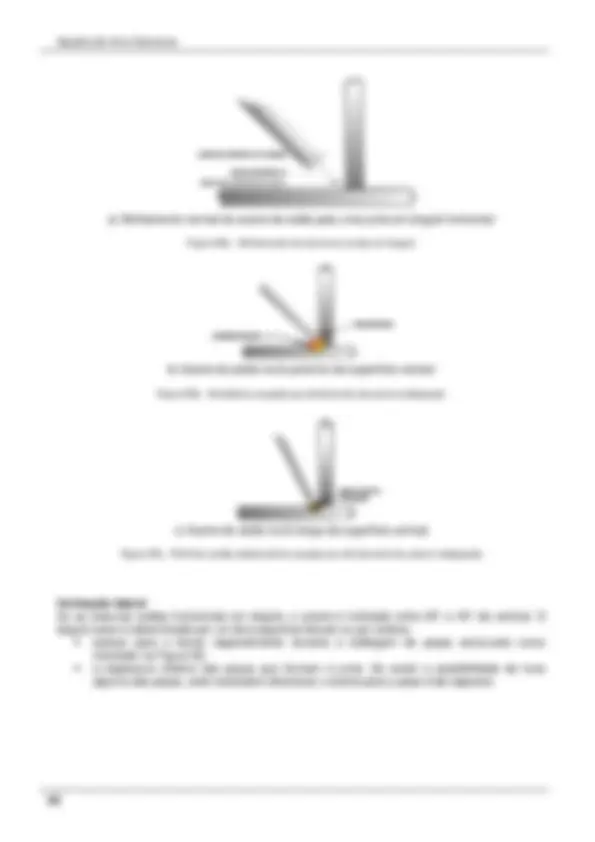
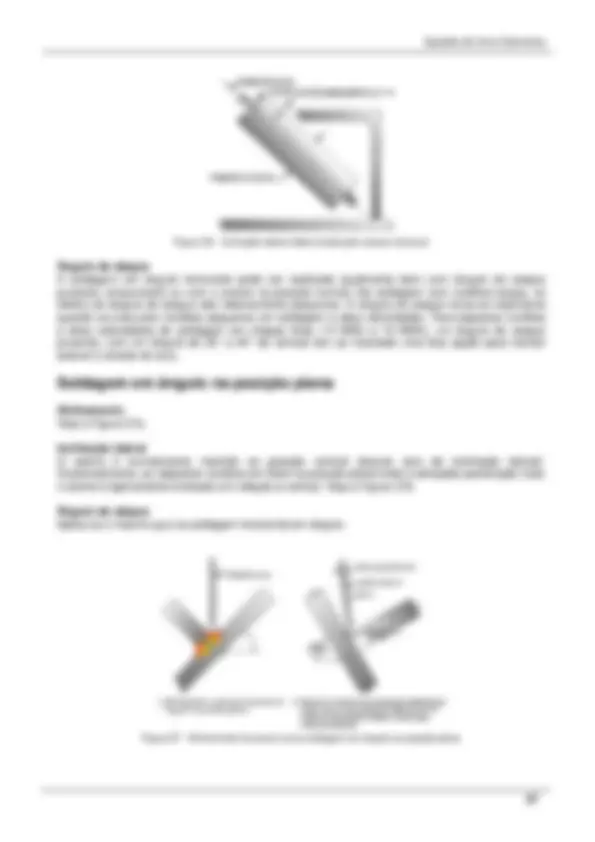
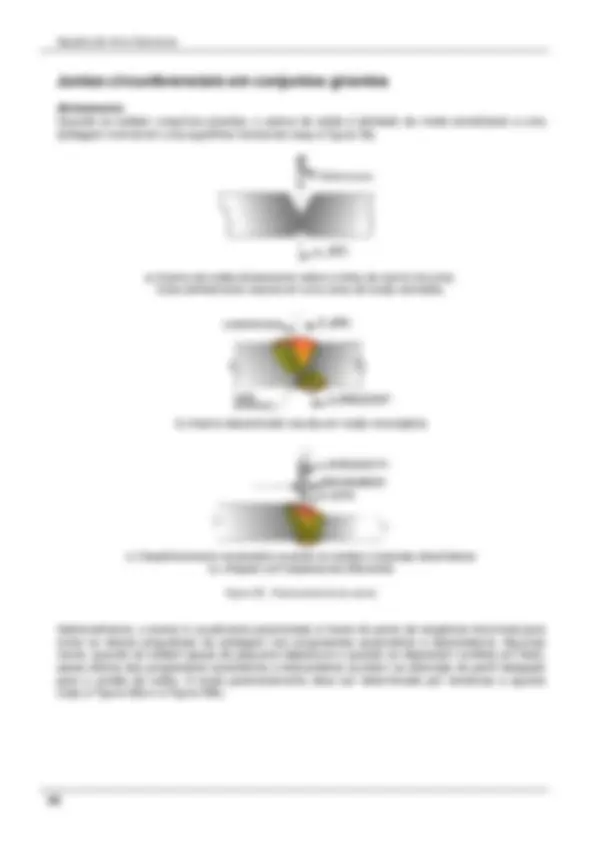
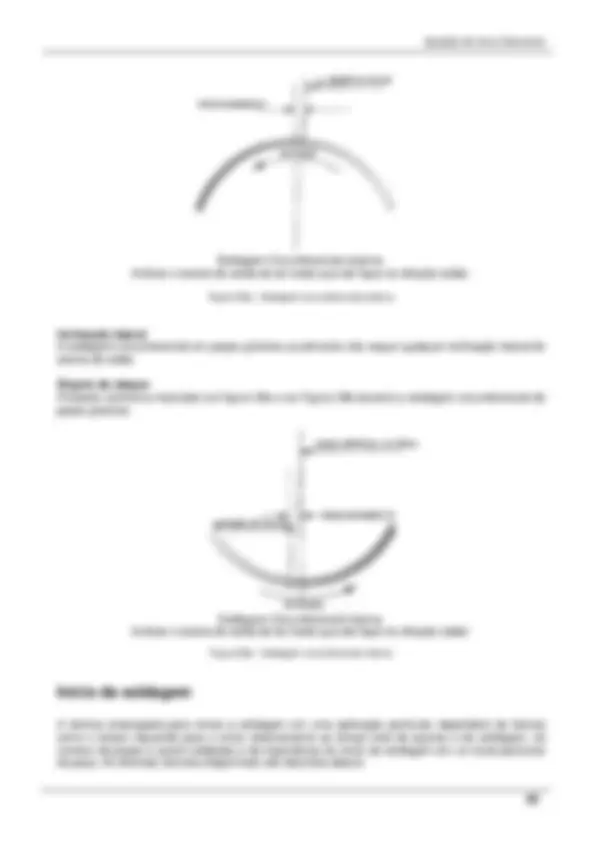
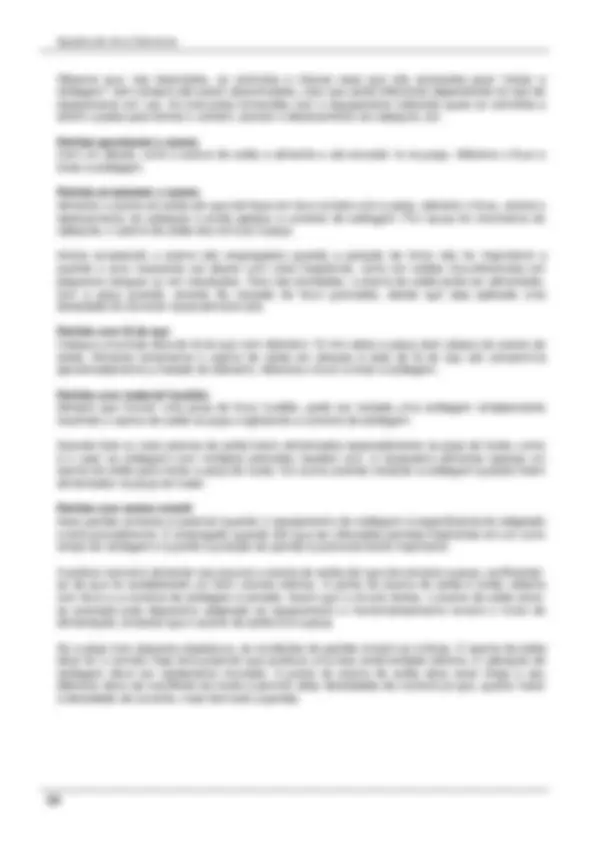
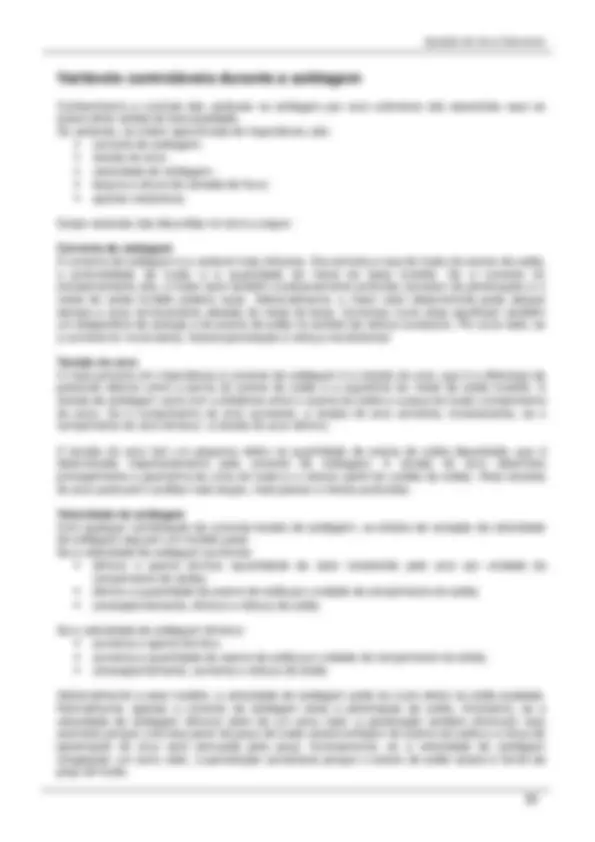
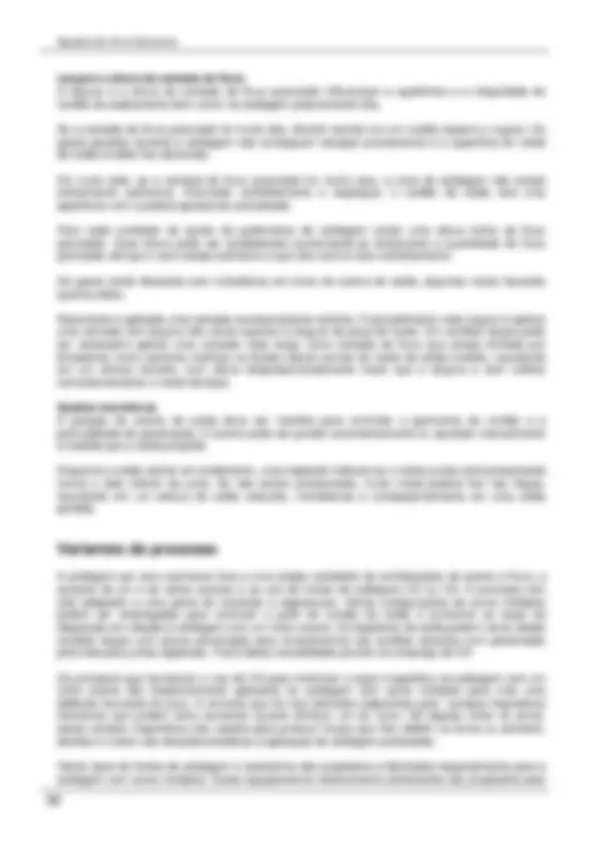
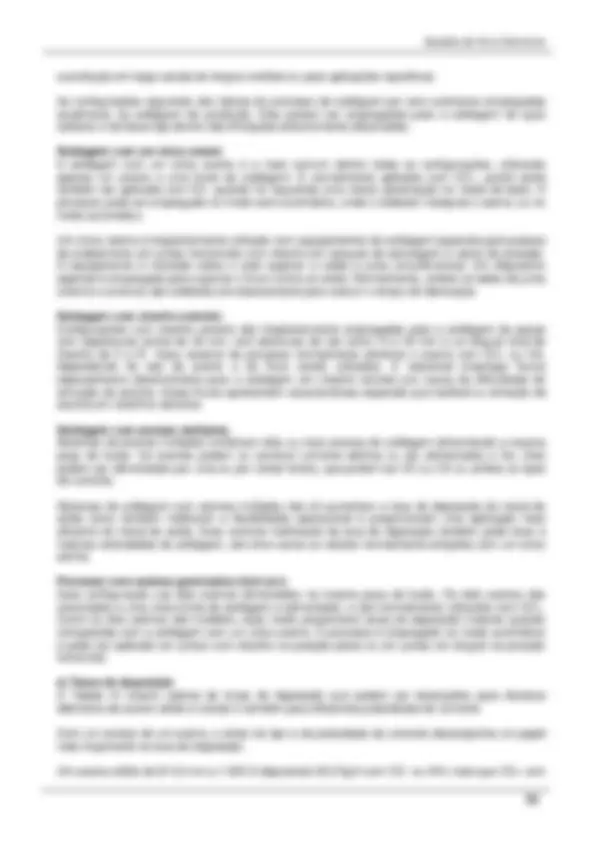
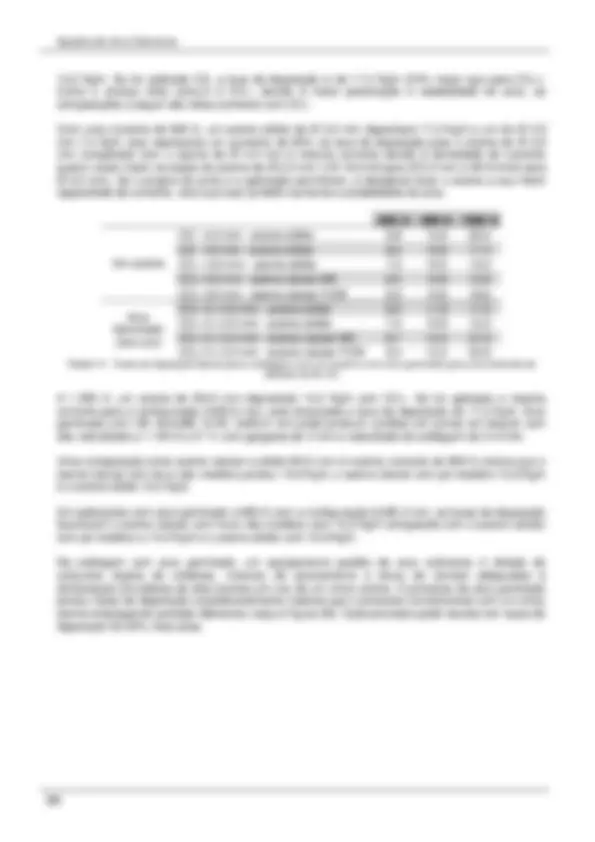
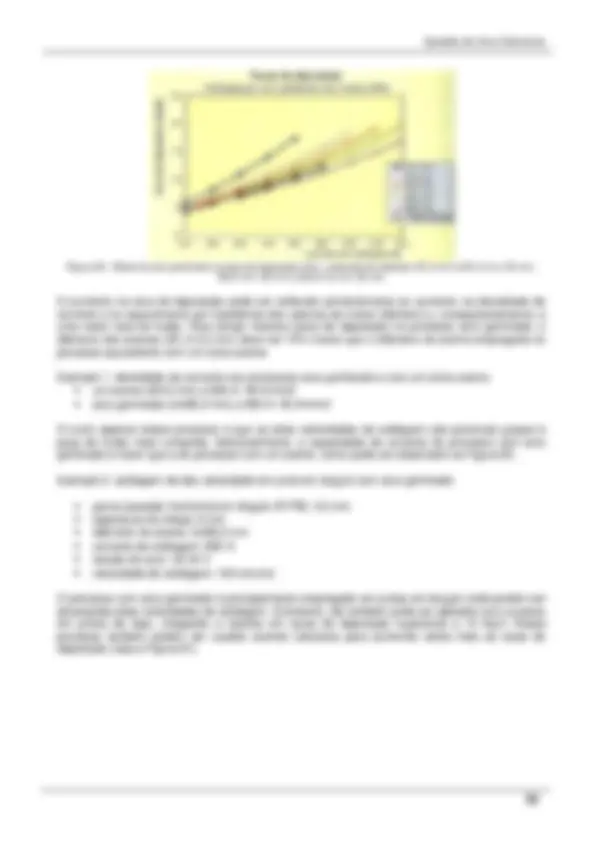
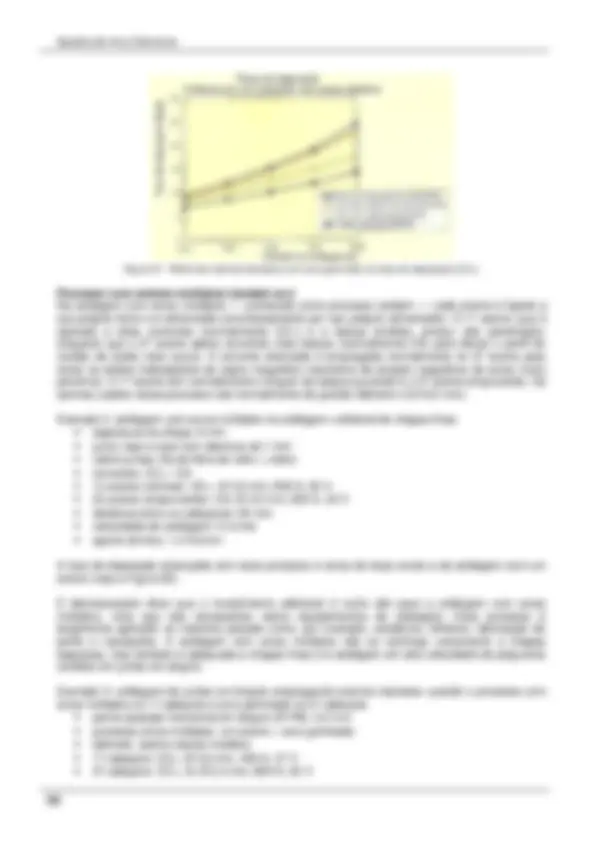
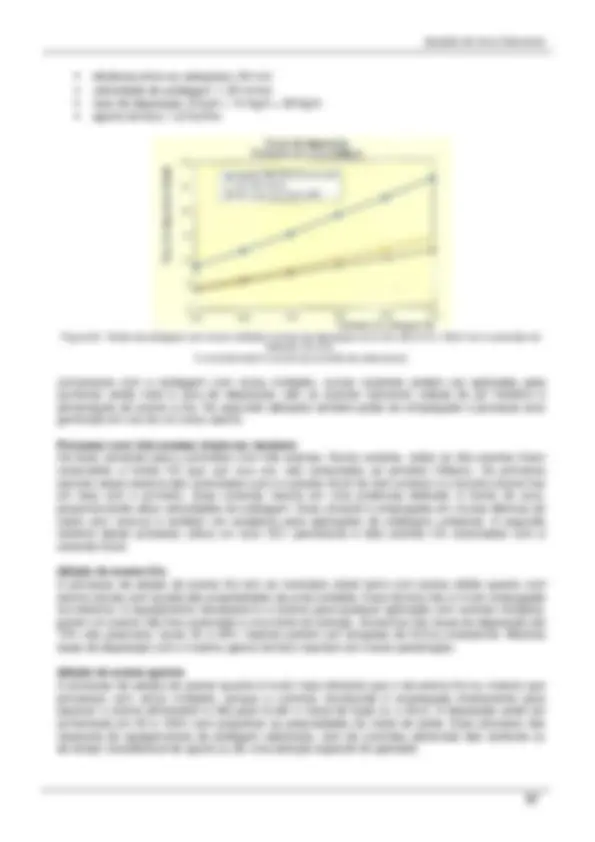
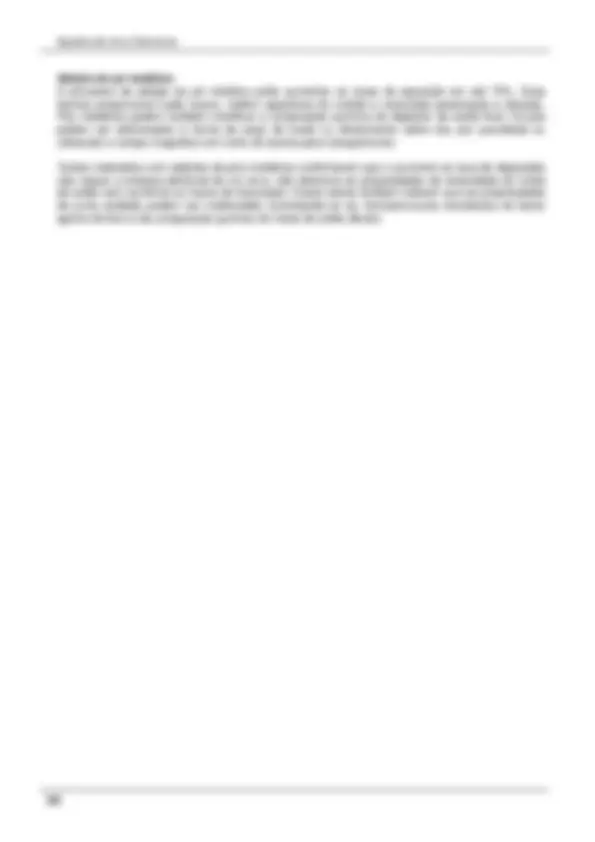
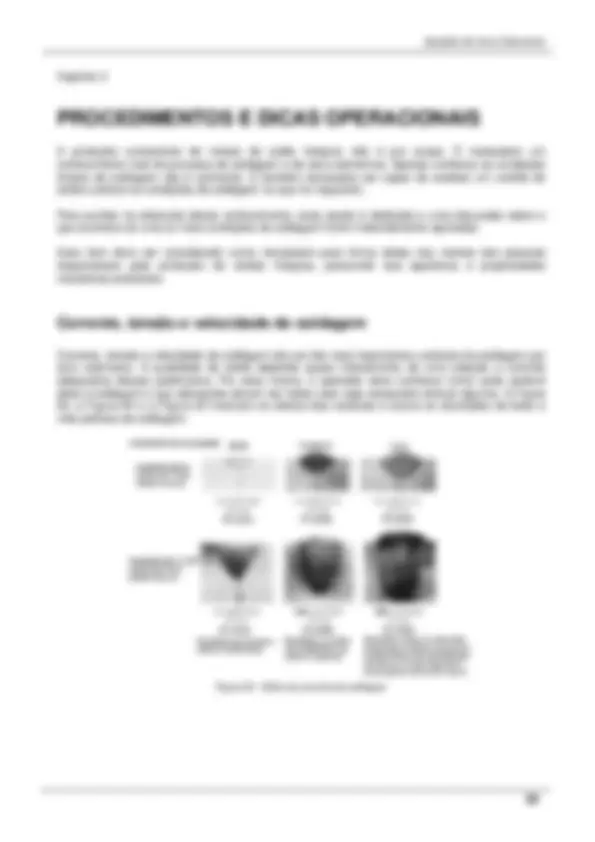
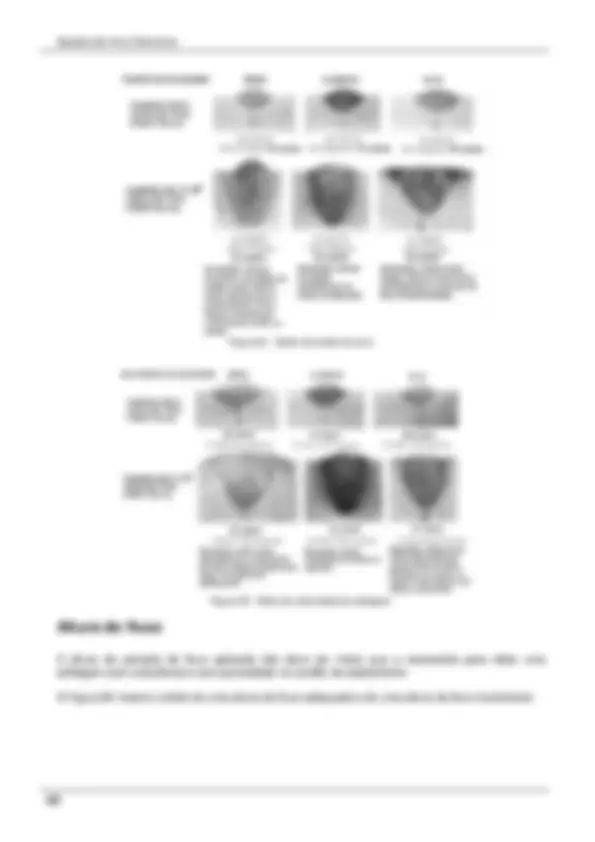
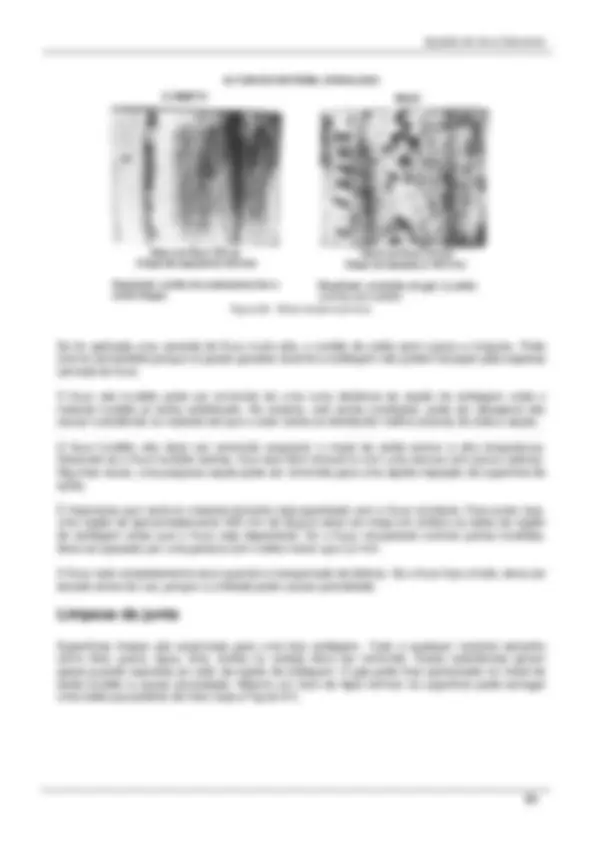
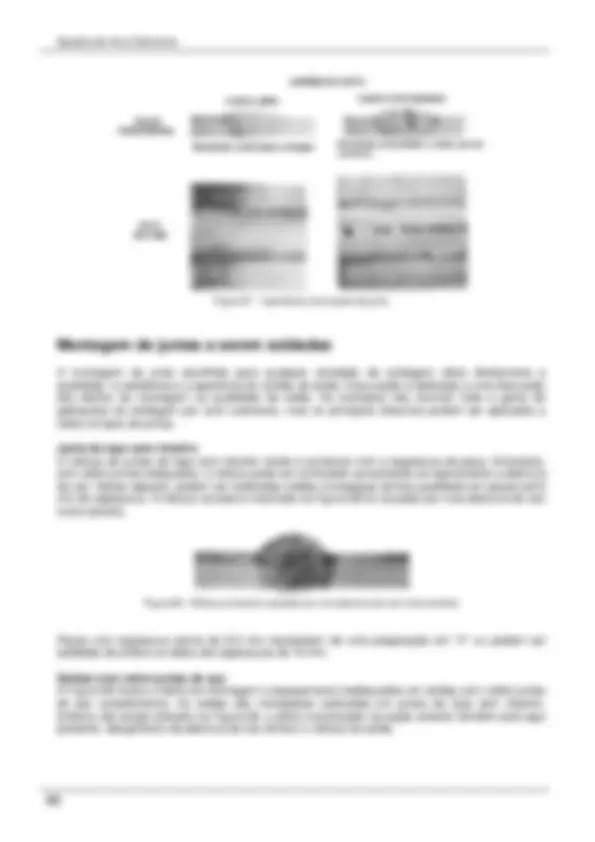
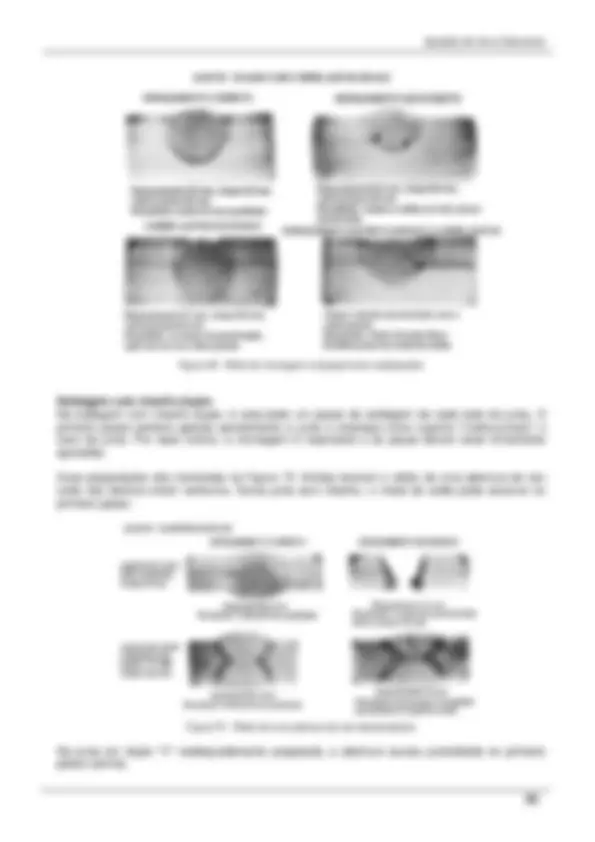
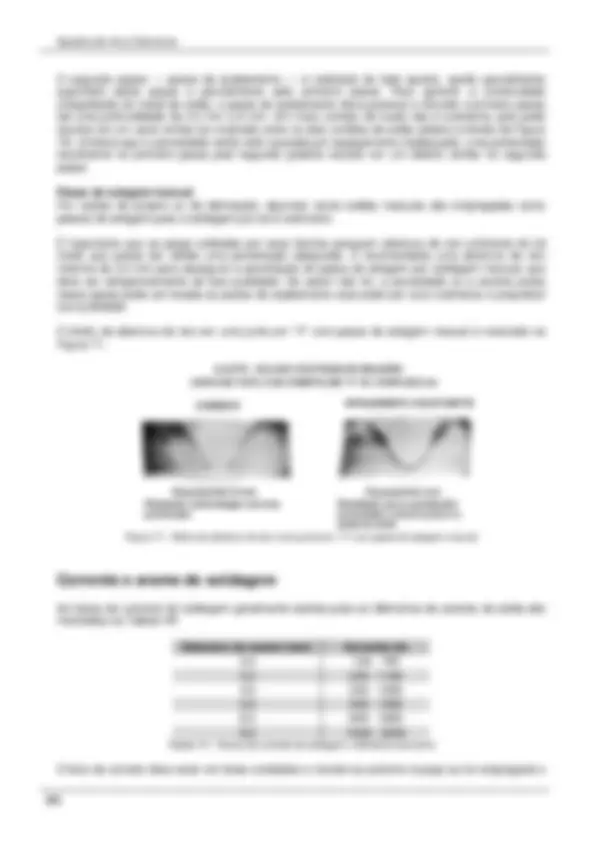
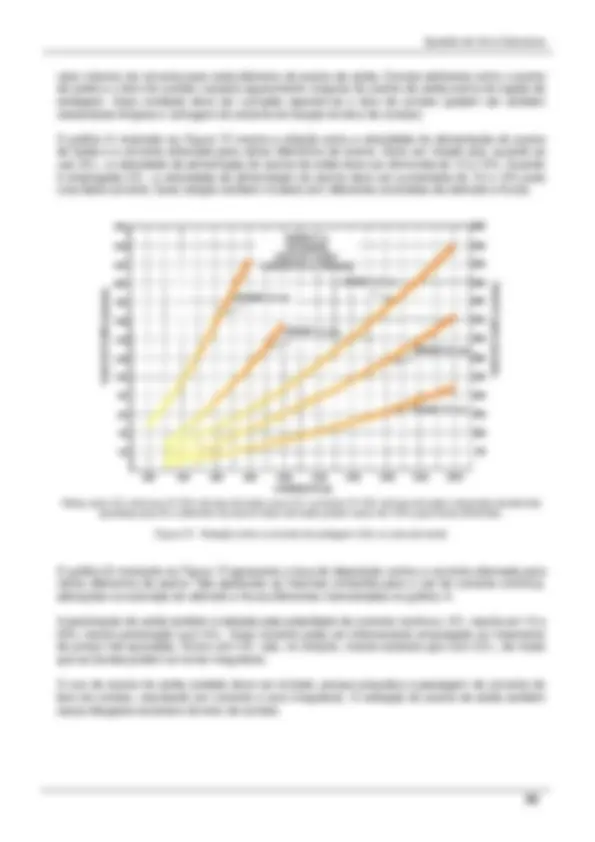
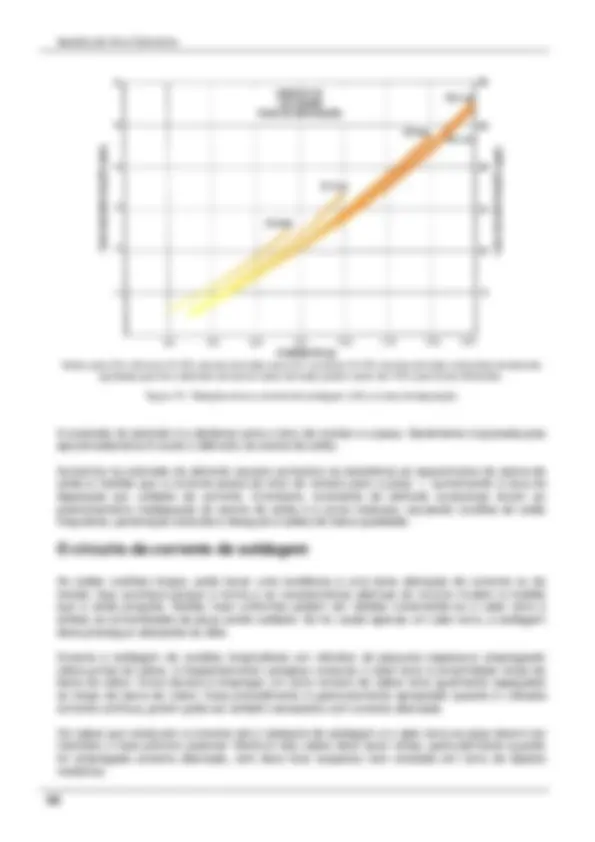
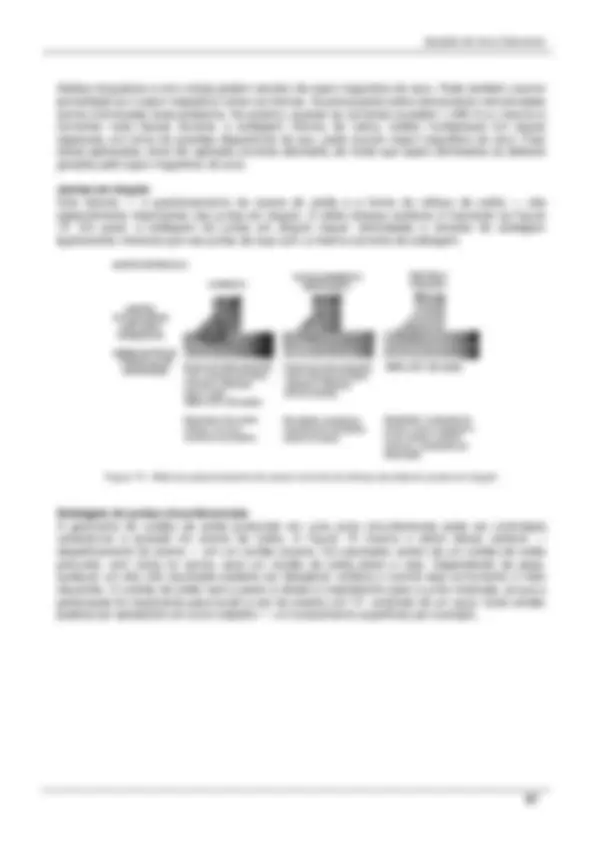
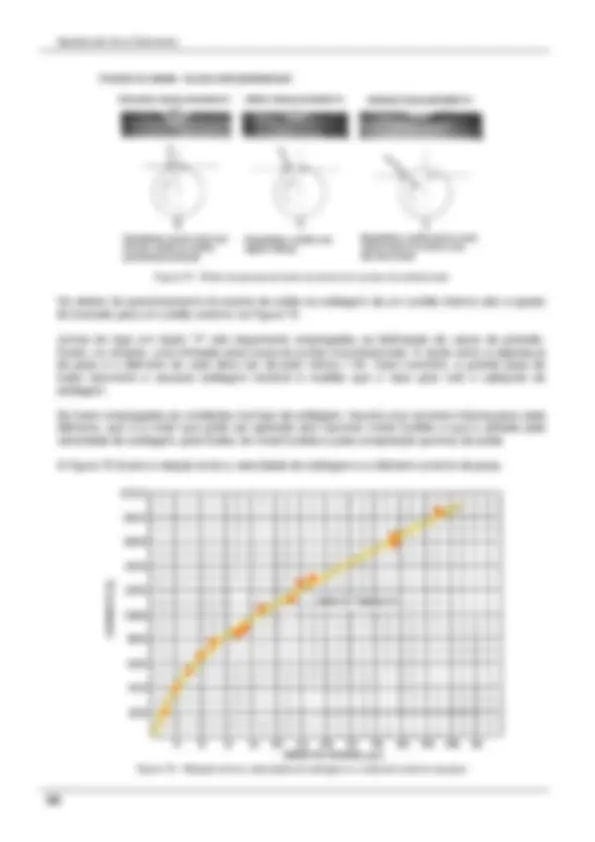
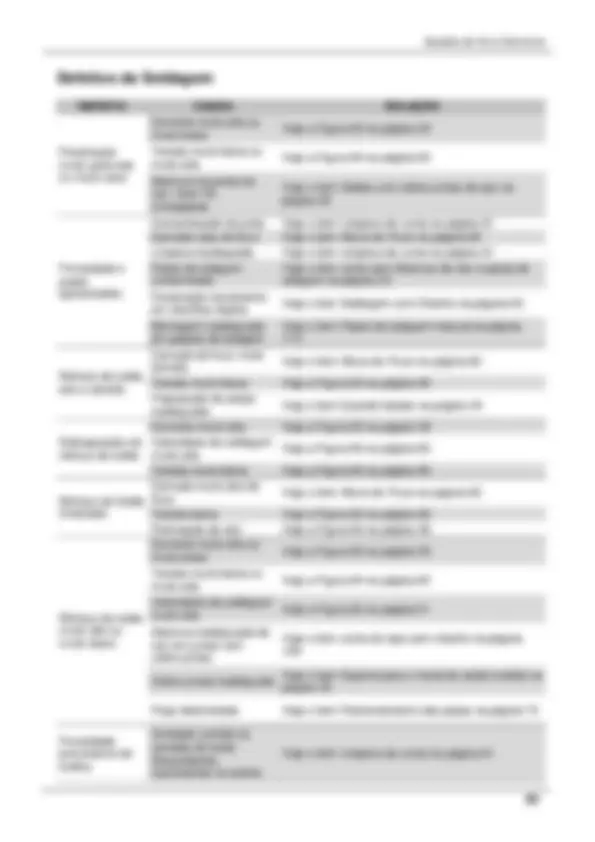
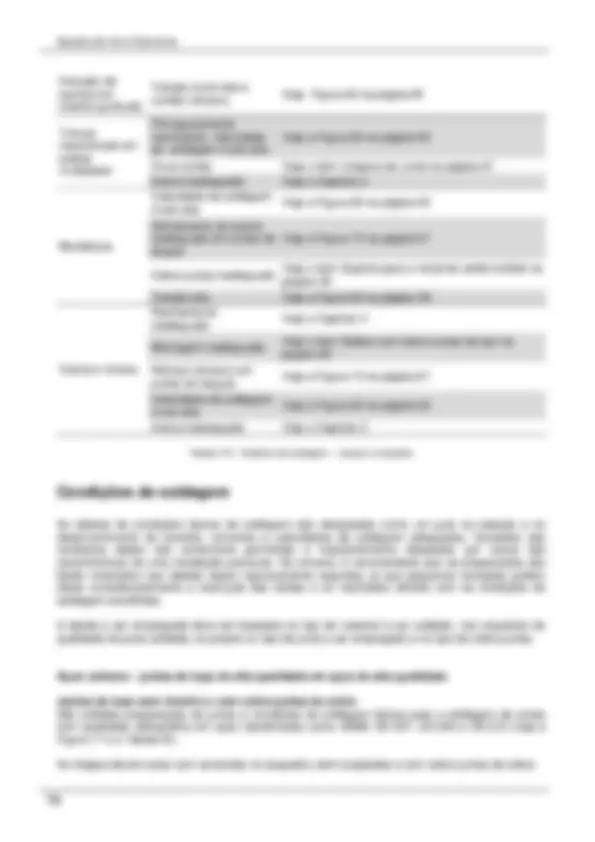
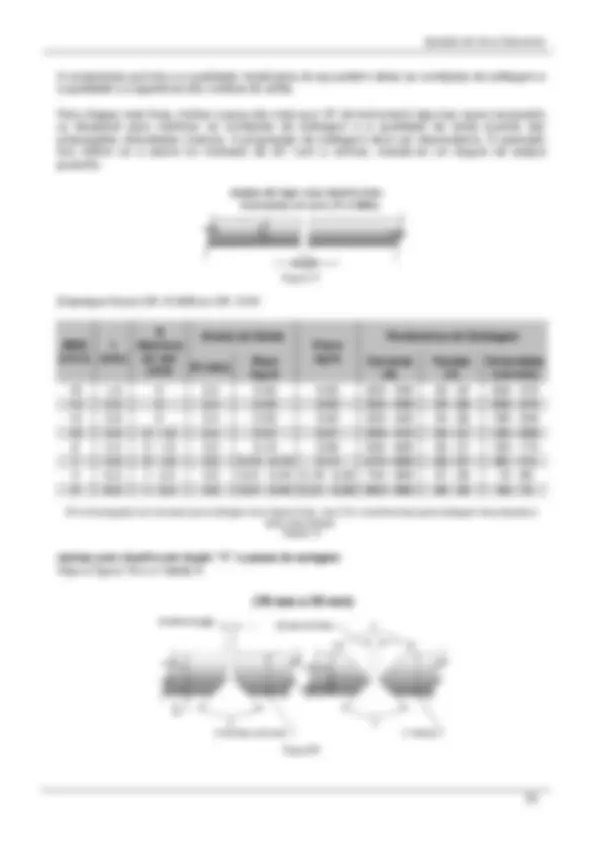
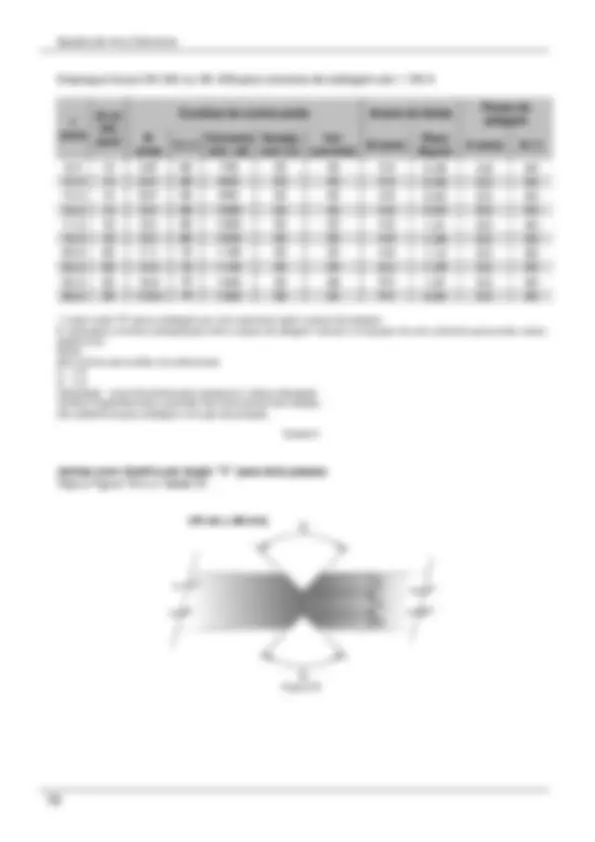
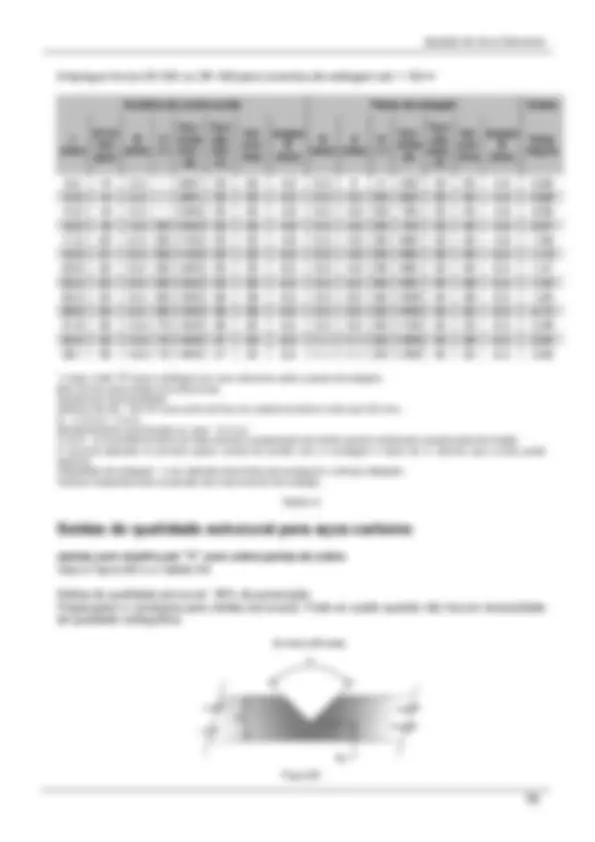
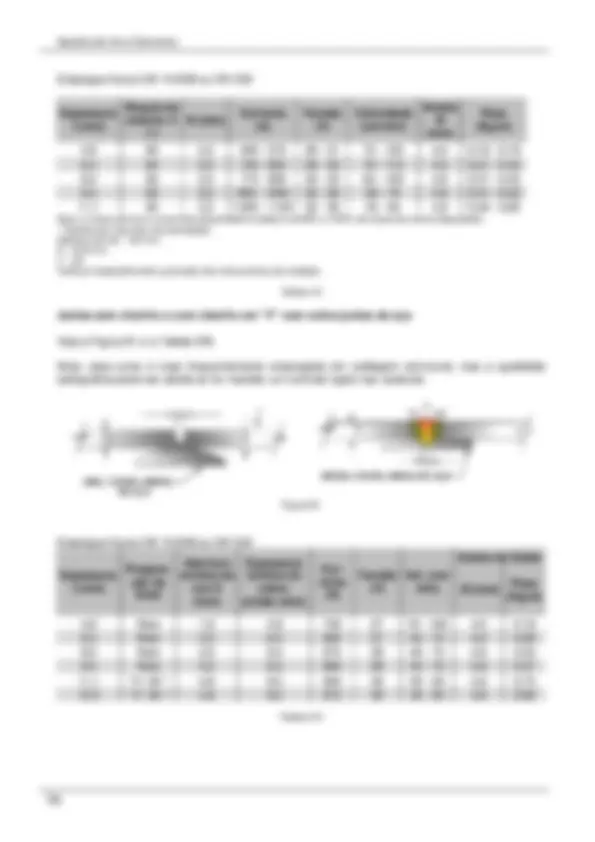
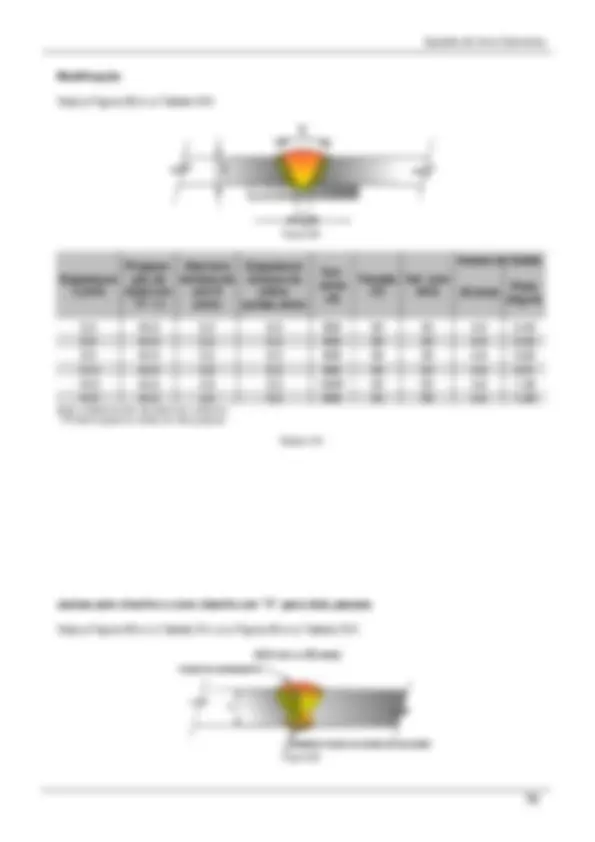
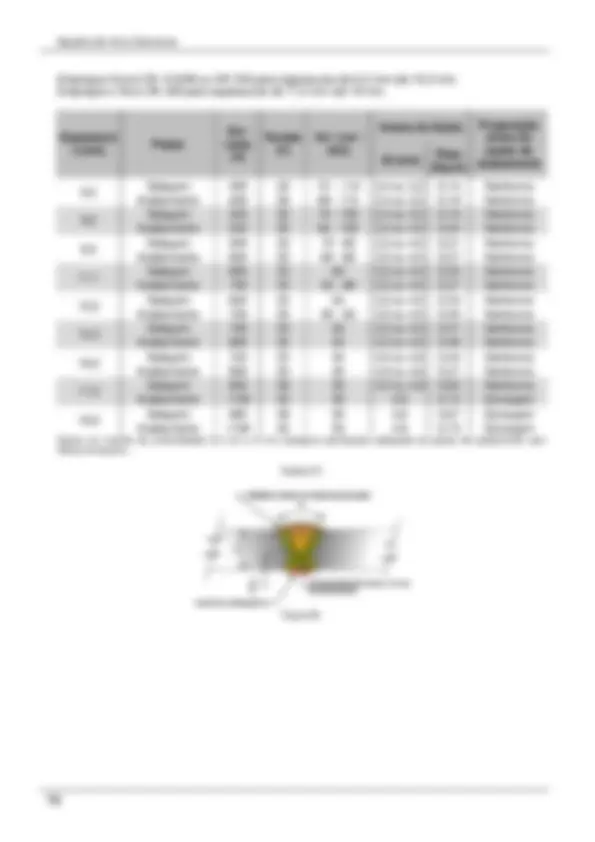
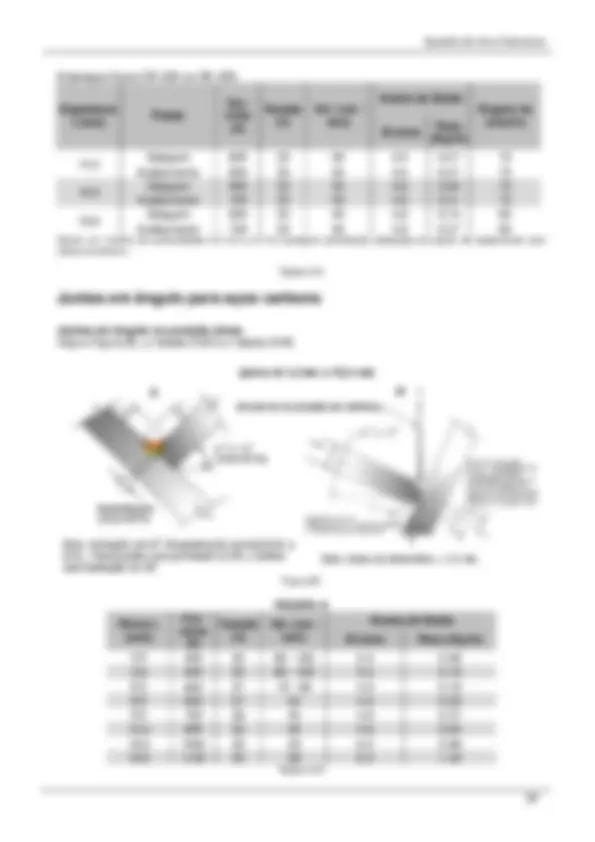
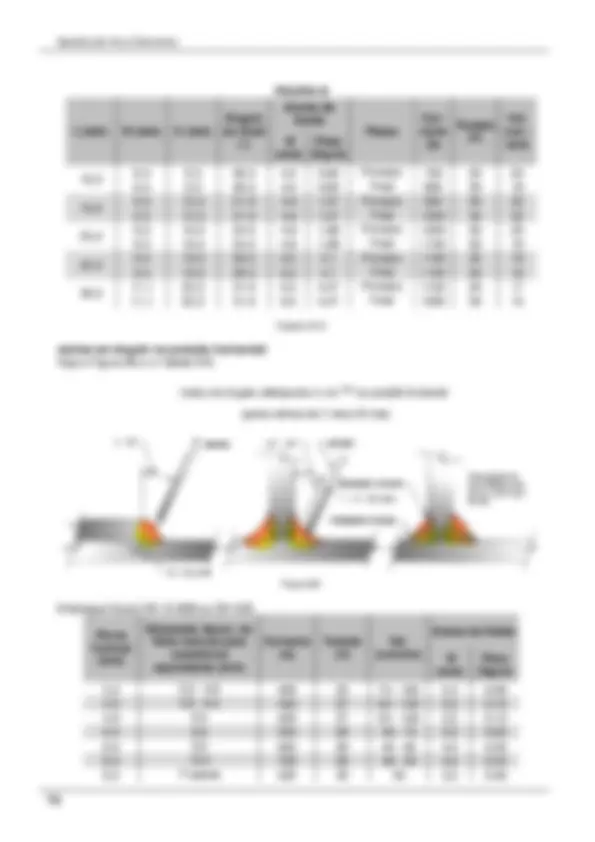
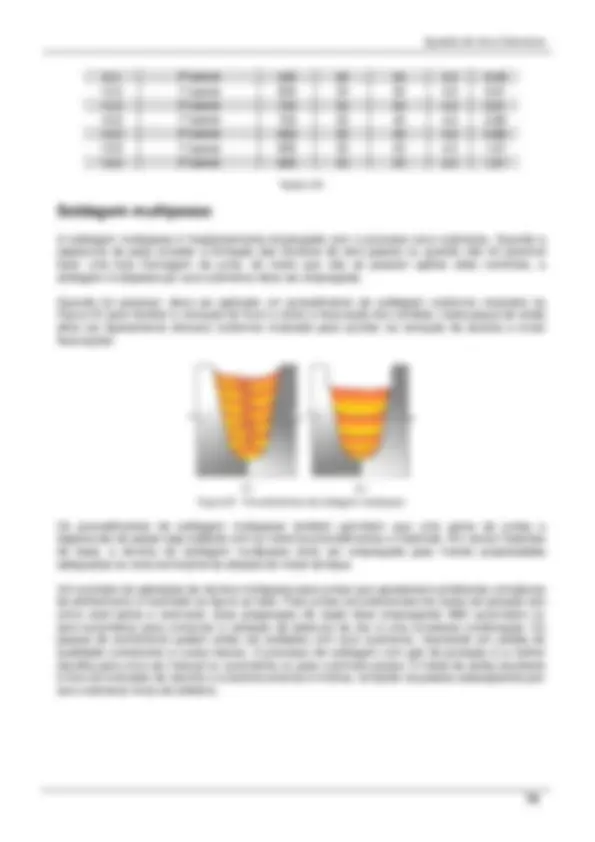
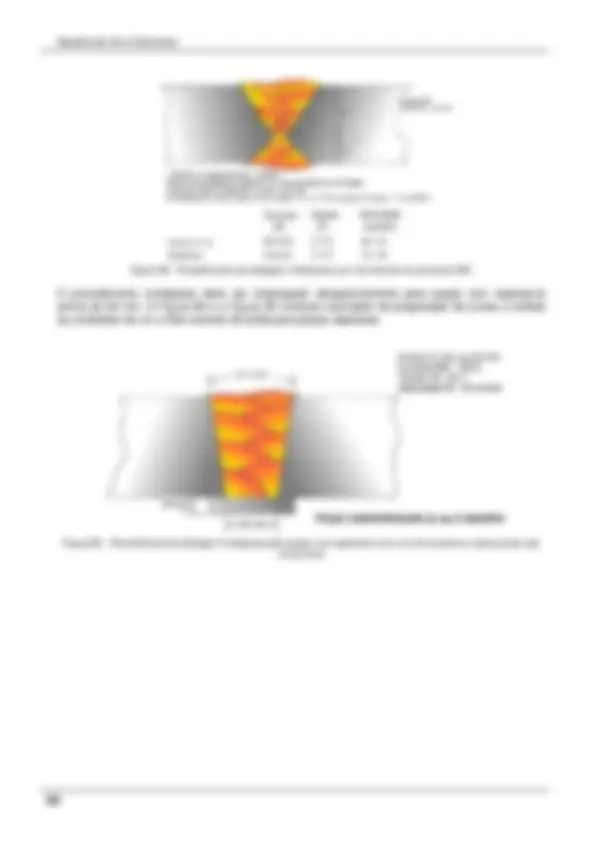
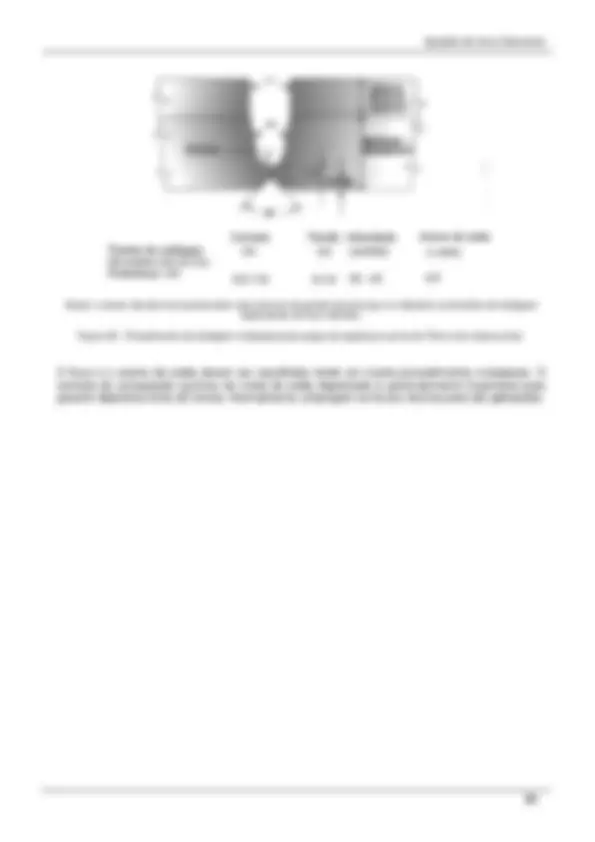
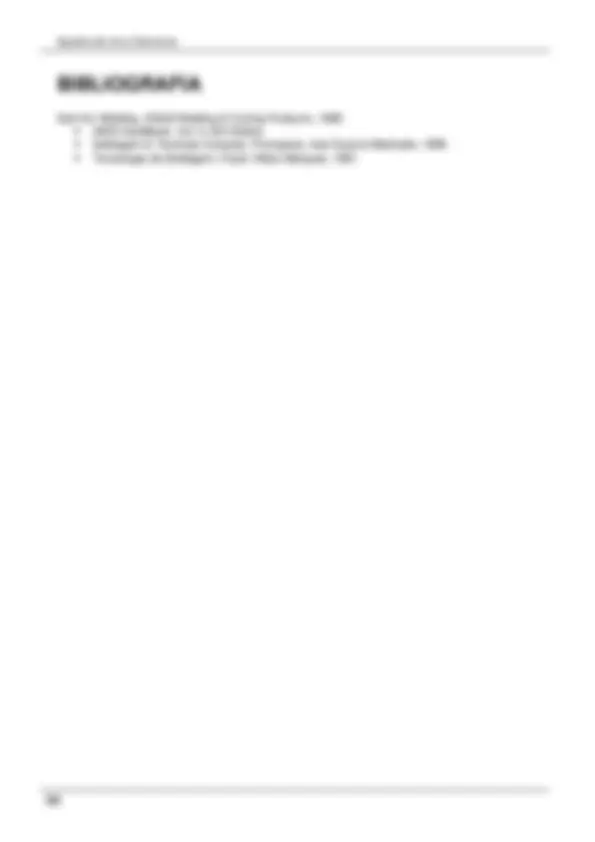
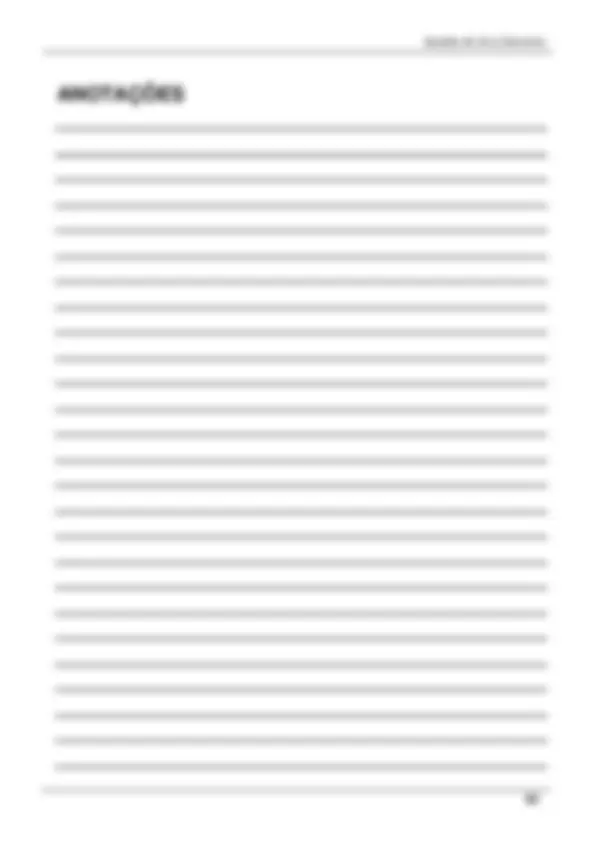
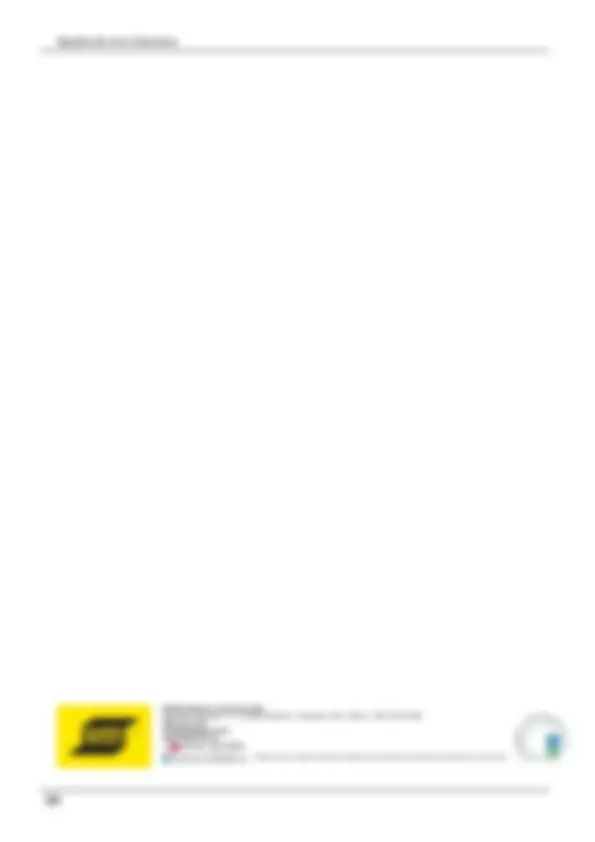
Estude fácil! Tem muito documento disponível na Docsity
Ganhe pontos ajudando outros esrudantes ou compre um plano Premium
Prepare-se para as provas
Estude fácil! Tem muito documento disponível na Docsity
Prepare-se para as provas com trabalhos de outros alunos como você, aqui na Docsity
Os melhores documentos à venda: Trabalhos de alunos formados
Prepare-se com as videoaulas e exercícios resolvidos criados a partir da grade da sua Universidade
Responda perguntas de provas passadas e avalie sua preparação.
Ganhe pontos para baixar
Ganhe pontos ajudando outros esrudantes ou compre um plano Premium
Comunidade
Peça ajuda à comunidade e tire suas dúvidas relacionadas ao estudo
Descubra as melhores universidades em seu país de acordo com os usuários da Docsity
Guias grátis
Baixe gratuitamente nossos guias de estudo, métodos para diminuir a ansiedade, dicas de TCC preparadas pelos professores da Docsity
Soldagem por arco submerso (SAS) ou também conhecido em inglês como Submerged arc welding (SAW), é um método em que o calor necessário para fundir o metal é produzido por um arco elétrico criado entre a peça de trabalho e a ponta do arame de soldagem.
Tipologia: Notas de estudo
1 / 84
Esta página não é visível na pré-visualização
Não perca as partes importantes!
Elaborado, traduzido (parte) e adaptado por Cleber Fortes – Engenheiro Metalúrgico, M.Sc. Assistência Técnica Consumíveis – ESAB BR Revisado por Welerson Araújo – Engenheiro Metalurgista, M.Sc. Desenvolvimento e Pesquisa – ESAB BR Última revisão em 24 de maio de 2004
Capítulo 1
DESCRIÇÃO GERAL DA SOLDAGEM POR ARCO
SUBMERSO
Soldagem por arco submerso é um método no qual o calor requerido para fundir o metal é gerado por um arco formado pela corrente elétrica passando entre o arame de soldagem e a peça de trabalho. A ponta do arame de soldagem, o arco elétrico e a peça de trabalho são cobertos por uma camada de um material mineral granulado conhecido por fluxo para soldagem por arco submerso. Não há arco visível nem faíscas, respingos ou fumos.
O processo de soldagem por arco submerso é limitado às posições de soldagem plana e horizontal em ângulo.
Cinco elementos estão presentes na execução de uma solda por arco submerso:
Seqüência geral de atividades Reduzindo a soldagem por arco submerso aos seus termos mais simples, considerando o equipamento já montado e em uso, a seqüência geral de atividades para fazer uma solda por arco submerso é a seguinte:
Figura 1 - Equipamento de soldagem
Preparação das peças de trabalho Para os detalhes descritos a seguir, veja a Figura 2.
Figura 2 - Preparação das peças de trabalho
Preparação para a soldagem Para os detalhes descritos a seguir, veja a Figura 3.
À medida que o cordão de solda é constituído, a parte fundida do fluxo se resfria e endurece, formando um material duro e vítreo, que protege a solda até seu resfriamento, sendo normal seu completo destacamento da solda.
Desde que adequadamente executadas, as soldas por arco submerso não apresentam fagulhas, tornando desnecessários equipamentos de proteção contra a radiação. Não há respingos a serem removidos.
As altas velocidades de soldagem e altas taxas de deposição que são características do processo de soldagem por arco submerso requerem um controle automático do motor que alimenta o arame de soldagem à solda. Nenhuma mão de soldador seria capaz de alimentar suavemente o arame de soldagem a velocidades comparáveis às de uma máquina de soldagem por arco submerso. Tampouco ele poderia manter o controle preciso das mesmas condições de soldagem. O sistema de controle automático e a fonte de energia empregados na soldagem por arco submerso atuam para manter constantes a tensão e a corrente de soldagem.
Relação entre a tensão de soldagem e a distância entre o arame e a peça de trabalho A tensão de soldagem é proporcional ao comprimento do arco:
Taxa de fusão versus taxa de alimentação do arame
Fonte de corrente constante
Fonte de tensão constante
Capítulo 2
SELEÇÃO DO ARAME E DO FLUXO
O processo de soldagem por arco submerso
Dois materiais devem ser escolhidos para a soldagem por arco submerso: o arame de soldagem e o fluxo, os quais devem satisfazer em termos de qualidade e de economia aos requisitos das soldas a serem executadas (veja a Figura 5).
Figura 5 - Seleção do arame e do fluxo
Dois fatores influenciam a escolha do fluxo:
Para muitas soldas, as características de desempenho ditam que fluxos podem ser empregados. As características de desempenho incluem facilidade de remoção da escória, capacidade de remoção de óxidos e carepa, capacidade de condução de corrente elétrica, possibilidade de uso de vários arames e possibilidade de aplicação de corrente alternada.
As propriedades mecânicas são de importância primária para muitas aplicações críticas tais como vasos de pressão e serviços a baixas temperaturas. Para essas soldas, deve haver um compromisso das características de desempenho para satisfazer às propriedades mecânicas requeridas.
O principal fator que governa a escolha do arame de soldagem é sua influência na composição química e propriedades mecânicas da solda.
As propriedades mecânicas e químicas de uma solda por arco submerso são determinadas principalmente por quatro fatores:
A composição do metal de base é o fator mais importante em quatro a cinco passes, já que a razão entre o metal de base fundido e o metal de adição pode ser tão alta como 2:1 (veja a Figura 6). Na maioria dos outros processos de soldagem por fusão, os procedimentos de soldagem multipasse
Figura 8 - Fábrica de fluxos aglomerados
Figura 9 - Fluxograma de fabricação de fluxos aglomerados
Como as partículas dos fluxos aglomerados não são quimicamente homogêneas, a remoção de finos pode alterar a composição química do metal depositado e conseqüentemente suas propriedades mecânicas.
Fluxos fundidos Os fluxos fundidos são fabricados através da mistura seca de seus ingredientes, que são então fundidos em um forno elétrico (veja a Figura 10). O banho é vazado e sofre um choque térmico, que reduz o fluxo a partículas de tamanhos variados (veja a Figura 11), que são peneiradas e classificadas para obter (veja a Figura 12):
Figura 10 - Forno elétrico para a fabricação de fluxos fundidos
Figura 11 - Forno elétrico e mesa resfriadora empregados na fabricação de fluxos fundidos
Figura 12 - Aspecto dos grãos de fluxos fundidos
Os fluxos aglomerados fabricados pela ESAB são classificados quanto à neutralidade conforme a Tabela I:
Tabela I - Classificação de fluxos OK quanto à neutralidade
Índice de basicidade (IB) Os fluxos também são classificados pelo IIW (International Institute of Welding) quanto à composição química pelo índice de basicidade, calculado pela Equação [1]
Todas as recomendações de seleção de consumíveis são baseadas em uma avaliação de propriedades mecânicas, parâmetros típicos de procedimento e na experiência. É responsabilidade do usuário determinar a adequação dos consumíveis à sua aplicação, considerando os procedimentos particulares a serem aplicados e os requisitos do trabalho específico.
Uma vez que o fluxo foi escolhido por suas características de desempenho, pode ser selecionado um arame de soldagem para obtenção das propriedades mecânicas requeridas para a solda.
Para algumas aplicações críticas as propriedades mecânicas governam a escolha do par arame- fluxo. A seleção da combinação correta pode determinar apenas um arame e um fluxo que atendam a todas as necessidades. A Tabela II mostra a composição química típica e as especificações aplicáveis dos arames ESAB.
Arame AWS C Si Mn Cr Ni Mo Cu V Nb N OK Autrod 12.10 EL12 1,10 0,04 0,44 0, 12.20 EM12K 0,11 0,26 0,95 0,
OK Tubrodur 35 - 0,10 0,80 2,00 0,20 0,20 0, 40 - 0,12 0,40 2,90 3,00 0, 410 NiMo - 0,06 0,40 1,00 13,00 4,50 1, 410 M - 0,12 0,45 1,25 12,00 2,30 1,25 0,25 0, 412 N - 0,05 0,50 1,30 12,00 4,50 1,00 0,08 0,08 0, 420 - 0,23 0,50 1,25 12,50 0,
OK Tubrod B2 - 0,13 0,40 1,00 1,40 0, B2 M - 0,08 0,50 1,10 1,10 1,20 0,50 0, WS ECW 0,06 0,40 1,00 0,55 0,65 0, M2 ECM2 0,075 0,45 1,40 0,35 1,90 0, 316 L - 0,03 0,50 0,90 18,50 11,50 2, 430 S - 0,05 0,50 1,20 16,
Nota: arames tubulares - composição química do metal depositado com a aplicação do fluxo OK 10.61B.
Tabela II - Composição química de arames OK
Arames para soldagem por arco submerso são escolhidos primeiramente por sua influência nas propriedades mecânicas e/ou na composição química requerida para o metal depositado. Carbono e manganês são os elementos de liga mais comuns, com adições de Si, Mo, Ni, Cr, Cu e outros elementos adicionados para aumentar a resistência mecânica e controlar as propriedades mecânicas a altas ou baixas temperaturas. Adições de manganês e silício também auxiliam na eliminação da porosidade gerada pelo gás CO.
Os fluxos para soldagem por arco submerso são escolhidos para satisfazer aos requisitos de propriedades mecânicas em conjunto com um arame particular e também para atender às necessidades de desempenho de cada aplicação.
Exemplo: F9P0-Eb3-B3 é uma designação completa. Refere-se a um fluxo que produzirá um metal de solda que, na condição de tratado termicamente pós-soldagem, terá uma resistência à tração superior a 90 ksi (ou 620 MPa) e uma propriedade de impacto de pelo menos 20 lb.ft (ou 27 J) a 0°F (ou -18°C) quando depositado com um arame sólido EB3 sob as condições estabelecidas na norma AWS / ASME. A composição do metal de solda será EB3.
Para atender aos requisitos de uma norma de fabricação, as propriedades mecânicas mínimas dos consumíveis são usualmente bem definidas. No entanto, quando é exigida uma conformidade com uma norma específica como, por exemplo a AWS D1.1 Structural Code, as listas de conformidade dos produtos ESAB devem ser estudadas.
Quando sua aplicação diferir das condições do corpo de prova em itens como aporte térmico, diluição (veja a Figura 14), espessura da peça ou tratamento térmico, seus efeitos nas propriedades mecânicas podem ser estimados. Como uma regra geral, quando o aporte térmico ultrapassa o valor de 2,3 kJ/mm empregado nos testes conforme a norma AWS, a tenacidade e a resistência da solda ficarão menores que os valores publicados nos catálogos. Quando são empregadas altas correntes, o aumento da diluição do metal de base em mais de 20% também diminuirá a tenacidade da solda relativamente aos dados de catálogo.
Figura 14 - Diluição
O comprimento do cordão e a taxa de resfriamento, medidos através do aporte térmico definido pela Equação [2],
[ 2 ] (^) 𝐴𝐴𝐴𝑍𝐴𝐹𝑇é𝑍𝑟𝑆𝑟𝐴 �
𝑇𝐹𝑀𝑇ã𝐴 𝑑𝐴 𝐴𝑍𝑟𝐴 𝑥 𝐶𝐴𝑍𝑍𝐹𝑀𝐴𝐹 𝑥 60 𝑉𝐹𝐴𝐴𝑟𝑆𝑑𝐶𝑑𝐹 𝑑𝐹𝑆𝐴𝐴𝑑𝐶𝑀𝐹𝑟(𝑟𝑟/𝑟𝑆𝑀) 𝑥 1000
têm um efeito maior nas propriedades mecânicas. Em aplicações críticas, portanto, é normalmente necessário avaliar o desempenho do material, empregando a condição de soldagem em serviço ou através de um teste de um procedimento de soldagem previamente executado.
Quando se escolhe uma combinação arame-fluxo para uma determinada aplicação, as características de desempenho desejadas devem ser atendidas:
Em muitos casos, deve existir um compromisso — a combinação arame-fluxo que atenderá às propriedades mecânicas requeridas com o melhor desempenho possível na soldagem. Essa é a razão pela qual a combinação de catorze fluxos e catorze arames da ESAB pode tornar esse compromisso o mais aceitável!
A combinação do desempenho com a maioria das propriedades mecânicas abrangendo a maior parte das indústrias, tais como caldeiraria, naval, e automotiva, pode ser simplificada. O exemplo seguinte ilustra o que pode ser feito com a pré-seleção de combinações simplificadas de arame- fluxo.
3 fluxos + 1 arame
Figura 15 - Consumíveis OK para a soldagem por arco submerso
Capítulo 3
PROJETO E PREPARAÇÃO DA JUNTA
O projeto e a preparação da junta são dois dos fatores mais importantes na execução de uma solda por arco submerso. Para usufruir totalmente das vantagens da soldagem por arco submerso, a junta deve ser adequadamente projetada e preparada e deve estar razoavelmente uniforme ao longo dos cordões de solda. Caso contrário, o operador de solda terá que fazer tentativas para compensar as irregularidades.
O tempo despendido na preparação adequada da junta é mais que compensado pelas maiores velocidades de soldagem e soldas de melhor qualidade.
Penetração da junta é a profundidade de fusão medida da superfície original do metal de base (veja a Figura 19). É algumas vezes expressa como um percentual da espessura da junta.
Figura 19 - Penetração da junta
Reforço da solda é o metal de solda excedendo a quantidade necessária para o preenchimento da junta soldada (veja a Figura 20).
Figura 20 - Reforço da junta
Linha de fusão é a junção do metal de solda com o metal de base (veja a Figura 21).
Figura 21 - Linha de fusão
Zona termicamente afetada é uma parte do metal de base adjacente à solda que não foi fundido, porém teve sua microestrutura ou suas propriedades mecânicas alteradas devido ao calor (veja a Figura 22).
Figura 22 - Zona termicamente afetada
Necessidade de suporte para o metal de solda fundido A soldagem por arco submerso forma um grande volume de metal fundido que permanece fluido por um período de tempo considerável.
É essencial que esse metal fundido seja suportado e contido até sua completa solidificação.
Uso de cobre-juntas para assegurar o suporte ao metal fundido Existem cinco modos comumente empregados para suportar o metal de solda fundido:
Os dois primeiros empregam cobre-juntas temporários que são removidos após o término da soldagem. Nos outros três, o cobrejuntas torna-se parte integrante da junta soldada.
Cobre-juntas não consumível O cobre-juntas de cobre é freqüentemente utilizado como cobrejuntas não consumível na soldagem dos aços. É empregado quando o metal de base não tem massa suficiente para prover um suporte adequado ao metal de solda ou quando deve ser obtida uma penetração completa em apenas um passe. O cobre-juntas de cobre é particularmente útil na soldagem de peças de pequena espessura. Vários tipos de cobre-juntas de cobre são mostrados na Figura 23.
Figura 23 - Diversos tipos de cobre-juntas não consumíveis de cobre
Como o cobre é um excelente condutor de calor, ele resfria rapidamente o metal de solda fundido, fornecendo ao metal de solda o suporte necessário sem ser fundido por ele. Foram feitas algumas tentativas para substituir o cobre por ligas de cobre e por alumínio e suas ligas, porém os resultados não foram satisfatórios tanto no aspecto econômico quanto na qualidade do metal de solda produzido.
Esse insucesso resulta da condutibilidade térmica apreciavelmente menor e também do menor calor latente de fusão das ligas alternativas em relação ao cobre. Por isso as ligas de cobre e o alumínio e suas ligas não conseguem suportar as altas temperaturas de soldagem e se deterioram rapidamente em serviço, mesmo que possuam inicialmente uma resistência à abrasão maior.