
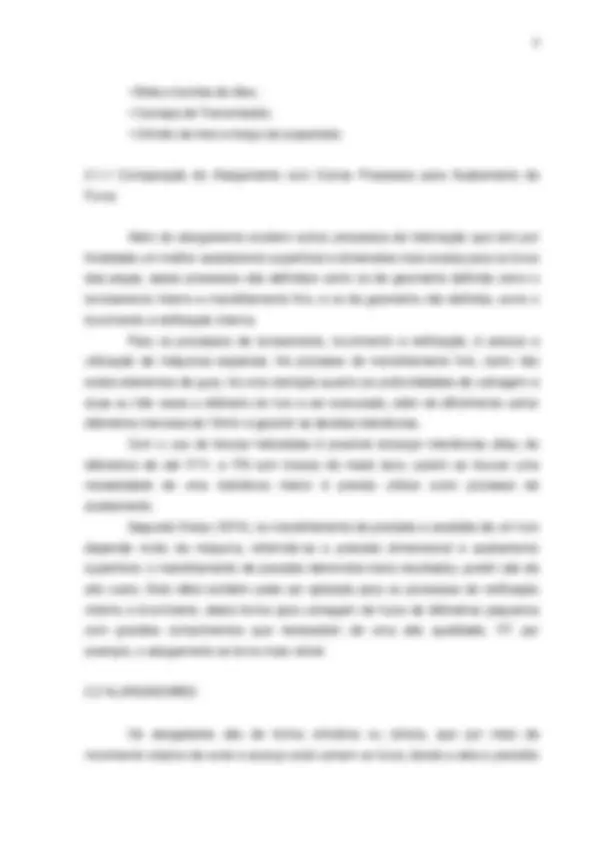
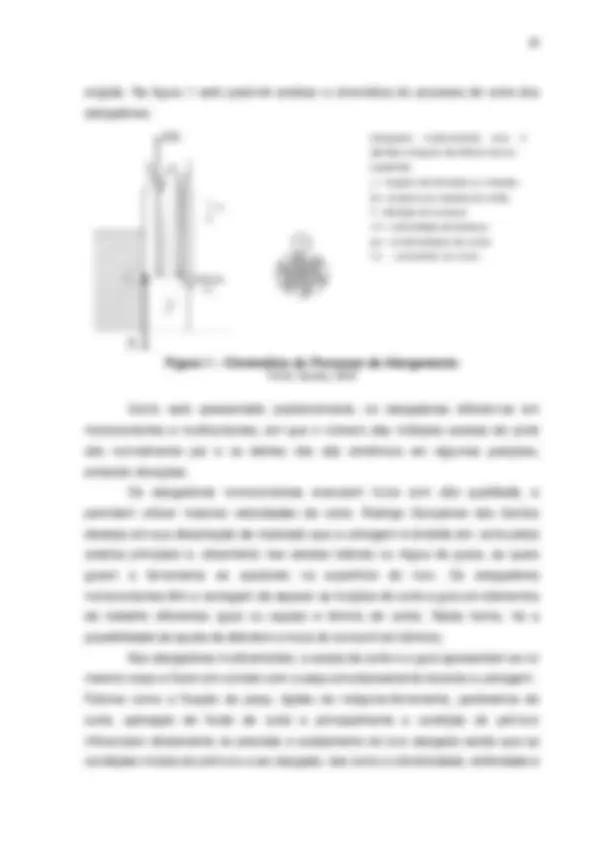
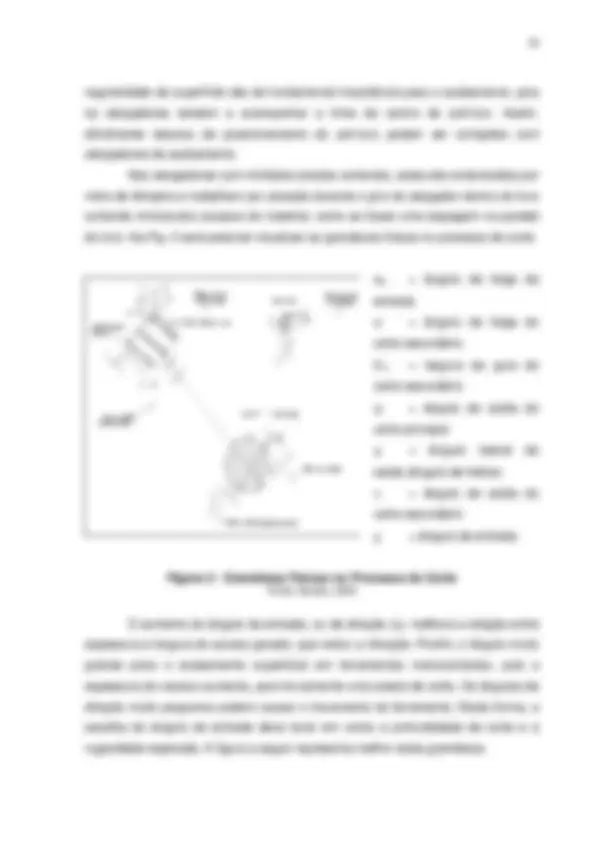
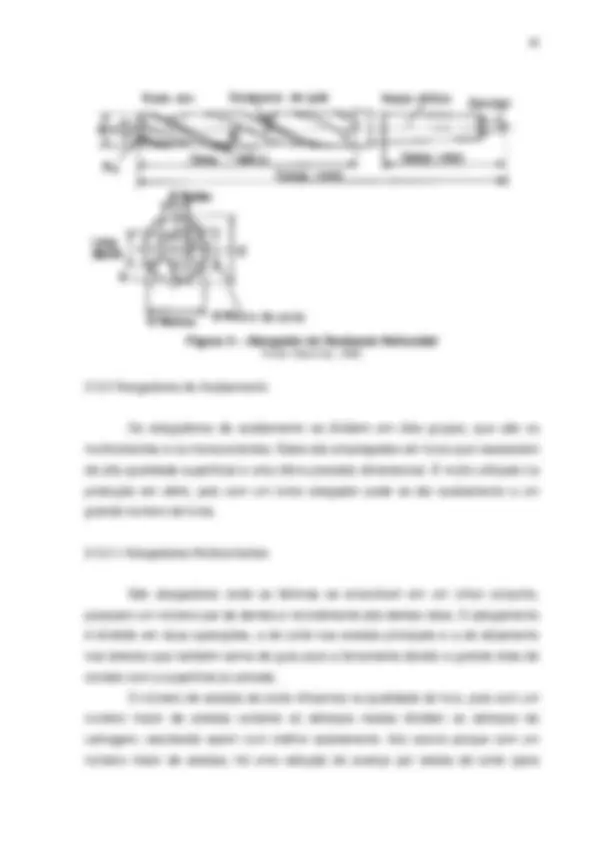
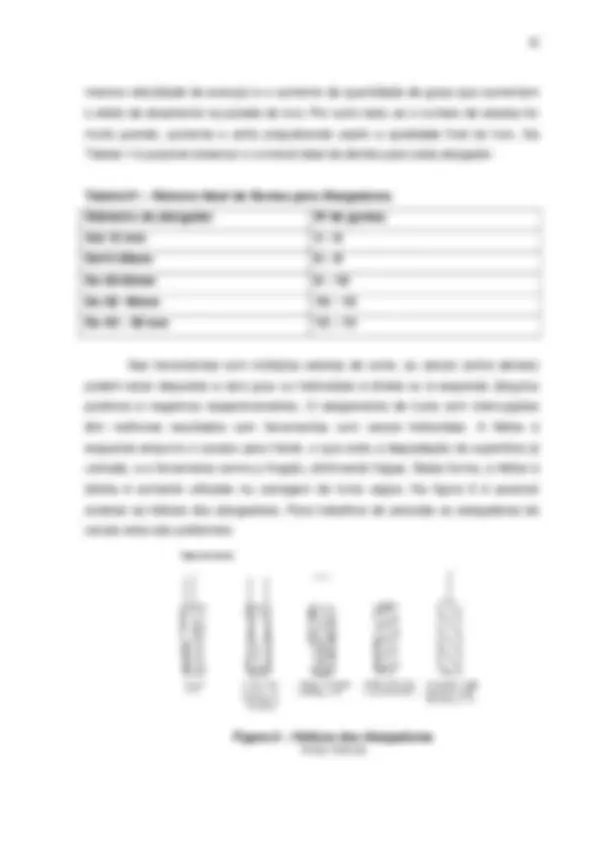
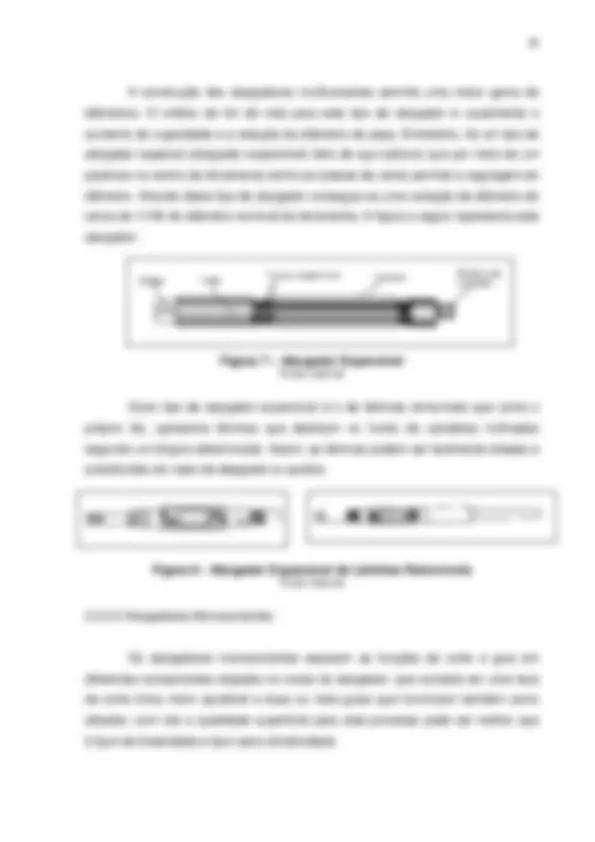
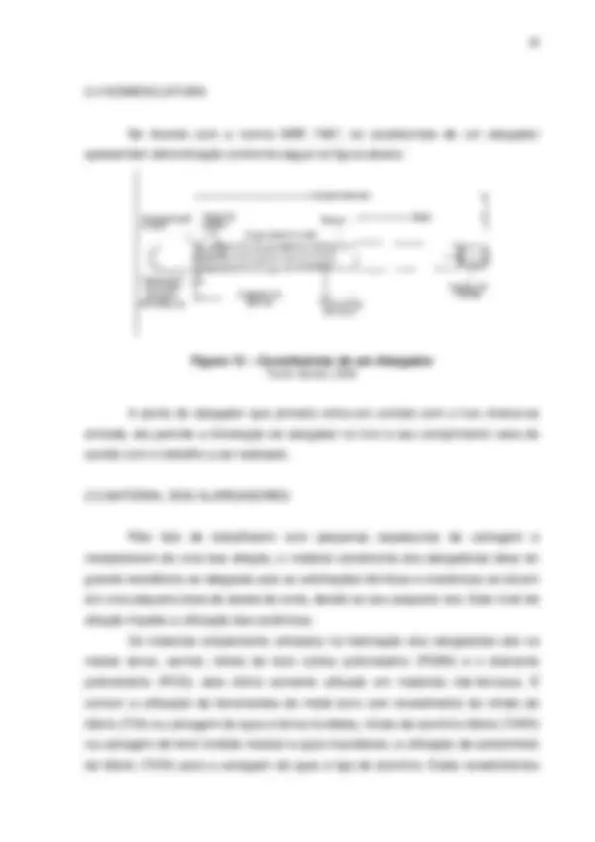
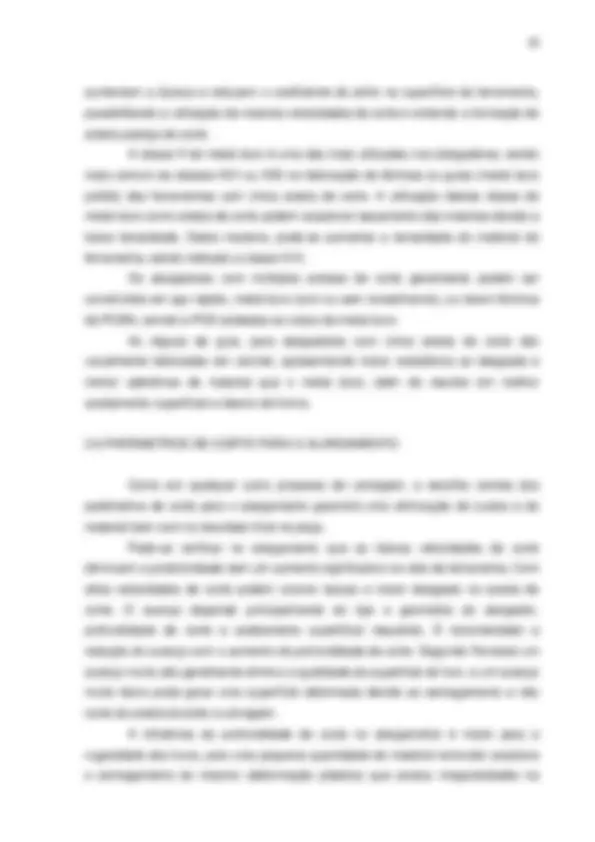
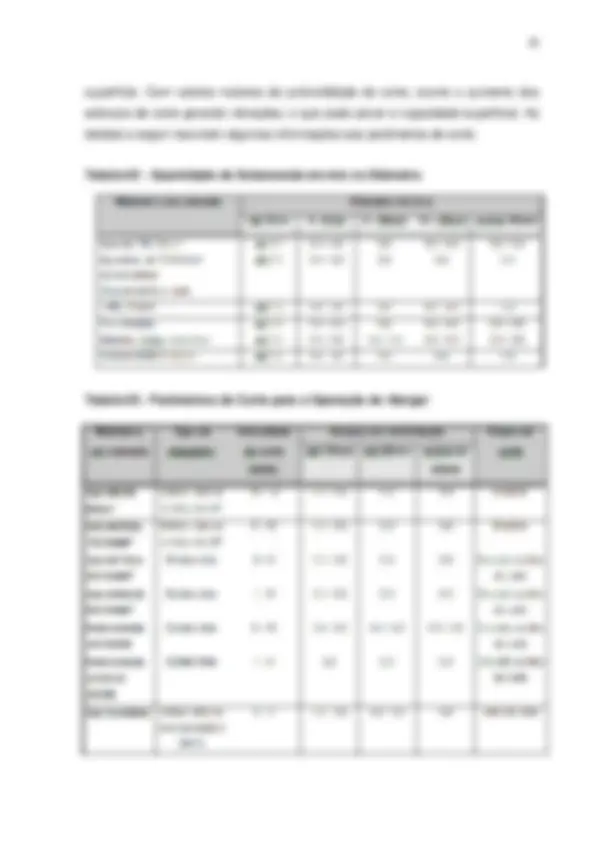
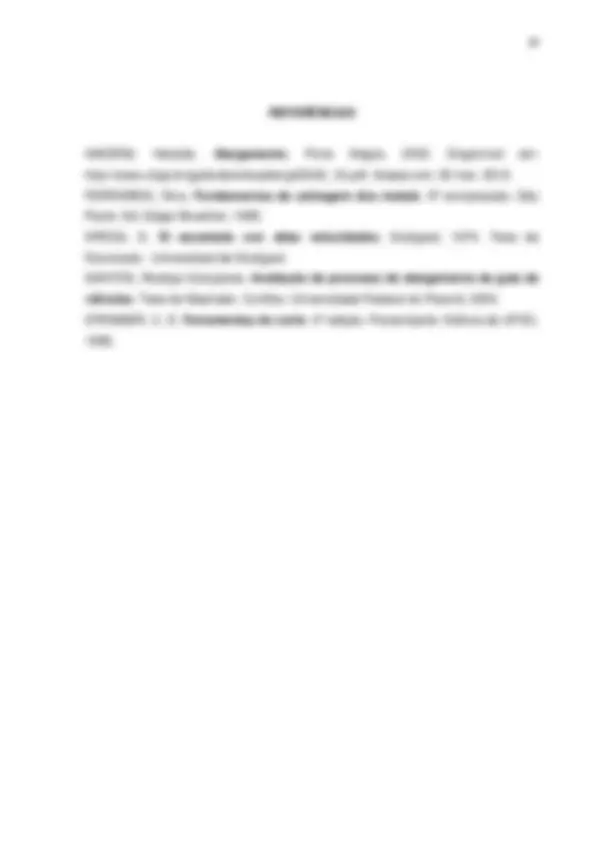
Estude fácil! Tem muito documento disponível na Docsity
Ganhe pontos ajudando outros esrudantes ou compre um plano Premium
Prepare-se para as provas
Estude fácil! Tem muito documento disponível na Docsity
Prepare-se para as provas com trabalhos de outros alunos como você, aqui na Docsity
Os melhores documentos à venda: Trabalhos de alunos formados
Prepare-se com as videoaulas e exercícios resolvidos criados a partir da grade da sua Universidade
Responda perguntas de provas passadas e avalie sua preparação.
Ganhe pontos para baixar
Ganhe pontos ajudando outros esrudantes ou compre um plano Premium
Comunidade
Peça ajuda à comunidade e tire suas dúvidas relacionadas ao estudo
Descubra as melhores universidades em seu país de acordo com os usuários da Docsity
Guias grátis
Baixe gratuitamente nossos guias de estudo, métodos para diminuir a ansiedade, dicas de TCC preparadas pelos professores da Docsity
Trabalho teórico na disciplina de Processo de Fabricação I mostrando as características do processo de usinagem alargamento.
Tipologia: Trabalhos
1 / 18
Esta página não é visível na pré-visualização
Não perca as partes importantes!
A usinagem tem como característica principal a obtenção de peças através da remoção progressiva de material por corte (cisalhamento). O material removido é denominado cavaco e o processo em si confere melhores tolerâncias dimensionais e acabamentos superficiais às peças fundidas ou forjadas, por exemplo. Os principais movimentos que ocorrem num processo de usinagem são o movimento de corte, movimento de avanço e movimento de penetração, sendo que cada um é caracterizado por parâmetros chamados de parâmetros de corte. Os principais processos de fabricação por usinagem são o torneamento, o fresamento, o aplainamento, a furação, a serragem, dentre outros. O processo de furação como o próprio nome já diz consiste na obtenção de furos de baixo grau de exatidão de dimensões variando entre 1 e 50 mm, com a utilização de uma ferramenta denominada broca. É dentro do contexto do processo de furação que se encontra o processo de alargamento, tema deste trabalho, que tem por principal finalidade melhorar o acabamento superficial e tolerâncias dimensionais em furos obtidos pelo processo de furação ou outro. Logo, será de grande relevância então expor nas páginas seguintes algumas características deste processo tais como a sua cinemática e as ferramentas utilizadas, as quais são denominadas alargadores. Assim, se terá uma idéia melhor se tal processo pode ser empregado em alguma produção seriada, por exemplo, onde há a necessidade de obter peças com furos de excelente qualidade dimensional.
O processo de fabricação por furação é um processo de desbaste que proporciona tolerâncias baixas nas peças e, como a execução de furos com seus formatos e dimensões tem que ser exatas conforme é exigido na produção, são necessários melhores acabamentos superficiais e tolerâncias, com isto é necessário o uso de ferramentas que os permitam. Segundo Rodrigo Gonçalves dos Santos (Dissertação: Avaliação do Processo de Alargamento de Guias de Válvulas, 2004. Pág. 4) “O alargamento é uma tecnologia que utiliza ferramenta de corte com geometria definida.”. O alargamento é um processo de fabricação que proporciona alto grau de acabamento e ótima precisão dimensional, ou seja, o uso dos alargadores tem por finalidade promover ótimas tolerâncias e acabamentos a furos já existentes, tanto para furos obtidos na fundição como também pela furação.
2.1 POR QUE UTILIZAR O ALARGAMENTO
No processo de furação, o furo executado pela broca não é tão preciso e isto pode ocorrer pelos seguintes motivos: a superfície do furo é rugosa; o furo não é perfeitamente cilíndrico porque há uma folga no eixo na máquina; o diâmetro não tem medidas exatas, geralmente a classe de tolerância é H12, isso ocorre pela afiação imperfeita ou deficiência na máquina. O alargador é uma ferramenta de corte para usinagem, usada para acabamentos com medidas exatas que permitem melhores ajustes de eixos, pinos e buchas, e ele é capaz de proporcionar ao furo: rugosidade Ra da ordem de 0,8μm; diâmetro de medidas exatas, quase sempre da classe de tolerância H7; e proporciona uma ligeira correção quando o furo estiver desviado. O alargamento pode ser empregado na usinagem de diferentes peças. Além de usinar válvulas hidráulicas e componentes da indústria aeronáutica, este processo é muito utilizado na fabricação de motores de combustão interna, principalmente nos componentes citados abaixo:
exigida. Na figura 1 será possível analisar a cinemática do processo de corte dos alargadores.
Figura 1 – Cinemática do Processo de Alargamento Fonte: Santos, 2004
Como será apresentado posteriormente, os alargadores diferem-se em monocortantes e multicortantes, em que o número das múltiplas arestas de corte são normalmente par e os dentes não são simétricos em algumas posições, evitando vibrações. Os alargadores monocortantes executam furos com alta qualidade, e permitem utilizar maiores velocidades de corte. Rodrigo Gonçalves dos Santos destaca em sua dissertação de mestrado que a usinagem é dividida em: corte pelas arestas principais e, alisamento nas arestas laterais ou régua de guias, as quais guiam a ferramenta se apoiando na superfície do furo. Os alargadores monocortantes têm a vantagem de separar as funções de corte e guia em elementos de trabalho diferentes (guia ou sapata e lâmina de corte). Desta forma, há a possibilidade de ajuste de diâmetro e troca do consumível (lâmina). Nos alargadores multicortantes, a aresta de corte e a guia apresentam-se no mesmo corpo e ficam em contato com a peça simultaneamente durante a usinagem. Fatores como a fixação da peça, rigidez da máquina-ferramenta, parâmetros de corte, aplicação de fluido de corte e principalmente a condição do pré-furo influenciam diretamente na precisão e acabamento do furo alargado sendo que as condições iniciais do pré-furo a ser alargado, tais como a cilindricidade, retilinidade e
regularidade da superfície são de fundamental importância para o acabamento, pois os alargadores tendem a acompanhar a linha de centro dificilmente desvios de posicionamento do pré alargadores de acabamento. Nos alargadores com meio de têmpera e trabalham por pressão durante o giro do cortando minúsculos cavacos do material, como se fosse uma raspagem na parede do furo. Na Fig. 2 será possível visualizar as g
Figura 2
O aumento do ângulo de entrada, ou de direção ( espessura e largura do cavaco gerado, que reduz a vibração. Porém, o ângulo muito grande piora o acabamento superficial em ferramentas monocortantes, pois espessura do cavaco aumenta, pois há somente uma aresta de corte. direção muito pequenos podem causar o travamento da ferramenta. Desta forma, a escolha do ângulo de entrada deve levar em conta a profundidade de corte e a rugosidade esperada. A figura a seguir representa melhor estas grandezas.
regularidade da superfície são de fundamental importância para o acabamento, pois os alargadores tendem a acompanhar a linha de centro do pré dificilmente desvios de posicionamento do pré-furo podem ser corrigidos com alargadores de acabamento. es com múltiplas arestas cortantes, estas são endurecidas por trabalham por pressão durante o giro do alargador dentro do furo cortando minúsculos cavacos do material, como se fosse uma raspagem na parede 2 será possível visualizar as grandezas físicas no processo de corte.
α 0 = ângulo de folga da entrada α = ângulo de folga do corte secundário b’α = largura da guia do corte secundário γ 0 = ângulo de saída do corte principal γf = ângulo lateral de saída (ângulo de hélice) γ = ângulo de saída do corte secundário χ = ângulo da entrada
Figura 2 - Grandezas Físicas no Processo de C Fonte: Santos, 2004
aumento do ângulo de entrada, ou de direção (χ), melhora a rela espessura e largura do cavaco gerado, que reduz a vibração. Porém, o ângulo muito grande piora o acabamento superficial em ferramentas monocortantes, pois espessura do cavaco aumenta, pois há somente uma aresta de corte. direção muito pequenos podem causar o travamento da ferramenta. Desta forma, a escolha do ângulo de entrada deve levar em conta a profundidade de corte e a A figura a seguir representa melhor estas grandezas.
regularidade da superfície são de fundamental importância para o acabamento, pois do pré-furo. Assim, furo podem ser corrigidos com
são endurecidas por alargador dentro do furo cortando minúsculos cavacos do material, como se fosse uma raspagem na parede randezas físicas no processo de corte.
= ângulo de folga da
= ângulo de folga do secundário = largura da guia do corte secundário = ângulo de saída do corte principal = ângulo lateral de saída (ângulo de hélice) = ângulo de saída do corte secundário = ângulo da entrada
Corte
), melhora a relação entre espessura e largura do cavaco gerado, que reduz a vibração. Porém, o ângulo muito grande piora o acabamento superficial em ferramentas monocortantes, pois a espessura do cavaco aumenta, pois há somente uma aresta de corte. Os ângulos de direção muito pequenos podem causar o travamento da ferramenta. Desta forma, a escolha do ângulo de entrada deve levar em conta a profundidade de corte e a A figura a seguir representa melhor estas grandezas.
Figura 4 – Classificação dos Alargadores Fonte: Santos, 2004
2.3.1 Alargadores de Desbaste
Estes alargadores são usados para aumentar o diâmetro dos furos brutos de fundição ou forjamento, ou ainda de furos que anteriormente já foram desbastados. A sua diferença com as brocas é pelo fato de possuírem no mínimo 3 (três) dentes de corte, o diâmetro do furo deve ser no mínimo igual ou ainda maior que o diâmetro da broca e a escolha do alargador deve ser feito baseado na precisão e no acabamento necessários. Na fig. 5 pode ser observado um alargador de desbaste.
Figura 5 – Alargador de Desbaste Helicoidal Fonte: Stemmer, 1995
2.3.2 Alargadores de Acabamento
Os alargadores de acabamento se dividem em dois grupos, que são os multicortantes e os monocortantes. Estes são empregados em furos que necessitam de alta qualidade superficial e uma ótima precisão dimensional. É muito utilizado na produção em série, pois com um único alargador pode se dar acabamento a um grande numero de furos.
2.3.2.1 Alargadores Multicortantes
São alargadores onde as lâminas se encontram em um único conjunto, possuem um número par de dentes e normalmente são dentes retos. O alargamento é dividido em duas operações, a de corte nas arestas principais e a de alisamento nas laterais que também serve de guia para a ferramenta devido a grande área de contato com a superfície já usinada. O número de arestas de corte influencia na qualidade do furo, pois com um numero maior de arestas cortante os esforços nestas dividem os esforços de usinagem, resultando assim num melhor acabamento. Isto ocorre porque com um número maior de arestas, há uma redução do avanço por aresta de corte (para
A construção dos alargadores multicortantes permite uma maior gama de diâmetros. O critério de fim de vida para este tipo de alargador é usualmente o aumento da rugosidade e a redução do diâmetro da peça. Entretanto, há um tipo de alargador especial (alargador expansível) feito de aço-carbono que por meio de um parafuso no centro da ferramenta (entre as arestas de corte) permite a regulagem do diâmetro. Através deste tipo de alargador consegue-se uma variação de diâmetro de cerca de 1/100 do diâmetro nominal da ferramenta. A figura a seguir representa este alargador:
Figura 7 – Alargador Expansível Fonte: Internet
Outro tipo de alargador expansível é o de lâminas removíveis que como o próprio diz, apresenta lâminas que deslizam no fundo de canaletas inclinadas segundo um ângulo determinado. Assim, as lâminas podem ser facilmente afiadas e substituídas em caso de desgaste ou quebra.
Figura 8 - Alargador Expansível de Lâminas Removíveis Fonte: Internet
2.3.2.2 Alargadores Monocortantes
Os alargadores monocortantes separam as funções de corte e guia em diferentes componentes alojados no corpo do alargador, que consiste em uma faca de corte única micro ajustável e duas ou mais guias que funcionam também como alisador, com isto a qualidade superficial para este processo pode ser melhor que 0,5μm de linearidade e 5μm para cilindricidade.
Estes alargadores de corte único são intercambiáveis, e isso permite a variação do material da lâmina para ajustar a necessidade do produto usinado. Na figura 8 será observado um alargador de corte único intercambiável e suas partes móveis.
Figura 9 – Componente dos Alargadores Monocortantes Fonte: Santos, 2004
A fabricante Seco recomenda uma folga entre as guias e a lâmina do alargador de 0,015 mm para diâmetros menores e iguais a 10 mm e 0,020 mm para as ferramentas com diâmetros maiores que 10 mm. Se há uma grande distância entre a lâmina em relação às guias, podem aparecer oscilações durante a usinagem, pois as guias não entram em contato continuamente com a parede do furo, não guiando e alisando o mesmo. A figura a seguir representa esta folga.
Figura 10 – Folga entre Lâminas e Guias Fonte: Santos, 2004
De Acordo com a norma NBR 7487, os constituintes de um alargador apresentam denominação conforme segue na figura
Figura
A ponta do alargador que primeiro entra em entrada, ela permite a introdução do alargador no furo e seu comprimento varia de acordo com o trabalho a ser realizado.
2.5 MATERIAL DOS ALARGADORES
Pelo fato de trabalharem com pequenas espessuras de usinagem e necessitarem de uma boa afiação, o material grande resistência ao desgaste em uma pequena área da aresta de corte, devido ao seu pequeno raio. Este nível de afiação impede a utilização das cerâmicas Os materiais amplamente utilizados na fabricação dos alargadores são os metais duros, cermet, nitreto de boro cúbico policristalino (PCBN) e o diamante policristalino (PCD); este último somente utilizado em materiais não comum a utilização de ferramentas de metal duro com revestimento de nitreto de titânio (TiN) na usinagem de aços e ferros fundidos, nitreto de alumínio titânio (TiAlN) na usinagem de ferro fundido nodular e aços inoxidáveis, e utilização de carbonitreto de titânio (TiCN) para a usinagem de aços e liga de alumínio. Estes revestimentos
De Acordo com a norma NBR 7487, os constituintes de um alargador denominação conforme segue na figura abaixo:
Figura 12 – Constituintes de um Alargador Fonte: Santos, 2004
A ponta do alargador que primeiro entra em contato com o furo chama entrada, ela permite a introdução do alargador no furo e seu comprimento varia de acordo com o trabalho a ser realizado.
DOS ALARGADORES
Pelo fato de trabalharem com pequenas espessuras de usinagem e de uma boa afiação, o material constituinte dos alargadores deve ter grande resistência ao desgaste pois as solicitações térmicas e mecânicas se situam em uma pequena área da aresta de corte, devido ao seu pequeno raio. Este nível de zação das cerâmicas. Os materiais amplamente utilizados na fabricação dos alargadores são os metais duros, cermet, nitreto de boro cúbico policristalino (PCBN) e o diamante policristalino (PCD); este último somente utilizado em materiais não a utilização de ferramentas de metal duro com revestimento de nitreto de titânio (TiN) na usinagem de aços e ferros fundidos, nitreto de alumínio titânio (TiAlN) na usinagem de ferro fundido nodular e aços inoxidáveis, e utilização de carbonitreto itânio (TiCN) para a usinagem de aços e liga de alumínio. Estes revestimentos
De Acordo com a norma NBR 7487, os constituintes de um alargador
Constituintes de um Alargador
contato com o furo chama-se entrada, ela permite a introdução do alargador no furo e seu comprimento varia de
Pelo fato de trabalharem com pequenas espessuras de usinagem e constituinte dos alargadores deve ter pois as solicitações térmicas e mecânicas se situam em uma pequena área da aresta de corte, devido ao seu pequeno raio. Este nível de
Os materiais amplamente utilizados na fabricação dos alargadores são os metais duros, cermet, nitreto de boro cúbico policristalino (PCBN) e o diamante policristalino (PCD); este último somente utilizado em materiais não-ferrosos. É a utilização de ferramentas de metal duro com revestimento de nitreto de titânio (TiN) na usinagem de aços e ferros fundidos, nitreto de alumínio titânio (TiAlN) na usinagem de ferro fundido nodular e aços inoxidáveis, e utilização de carbonitreto itânio (TiCN) para a usinagem de aços e liga de alumínio. Estes revestimentos
aumentam a dureza e reduzem o coeficiente de atrito na superfície da ferramenta, possibilitando a utilização de maiores velocidades de corte e evitando a formação de aresta postiça de corte. A classe K de metal duro é uma das mais utilizadas nos alargadores, sendo mais comum às classes K01 ou K05 na fabricação de lâminas ou guias (metal duro polido) das ferramentas com única aresta de corte. A utilização destas classe de metal duro como aresta de corte podem ocasionar lascamento das mesmas devido a baixa tenacidade. Desta maneira, pode-se aumentar a tenacidade do material da ferramenta, sendo indicado a classe K10. Os alargadores com múltiplas arestas de corte geralmente podem ser construídos em aço rápido, metal duro (com ou sem revestimento), ou terem lâminas de PCBN, cermet e PCD soldadas ao corpo de metal duro. As réguas de guia, para alargadores com única aresta de corte são usualmente fabricadas em cermet, apresentando maior resistência ao desgaste e menor aderência de material que o metal duro; além de resultar em melhor acabamento superficial e desvio de forma.
2.6 PARÂMETROS DE CORTE PARA O ALARGAMENTO
Como em qualquer outro processo de usinagem, a escolha correta dos parâmetros de corte para o alargamento garantirá uma otimização de custos e de material bem com no resultado final na peça. Pode-se verificar no alargamento que as baixas velocidades de corte diminuem a produtividade sem um aumento significativo na vida da ferramenta. Com altas velocidades de corte podem ocorrer lascas e maior desgaste na aresta de corte. O avanço depende principalmente do tipo e geometria do alargador, profundidade de corte e acabamento superficial requerido. É recomendado a redução do avanço com o aumento da profundidade de corte. Segundo Ferraresi um avanço muito alto geralmente diminui a qualidade da superfície do furo, e um avanço muito baixo pode gerar uma superfície deformada devido ao esmagamento e não corte da aresta durante a usinagem. A influência da profundidade de corte no alargamento é maior para a rugosidade dos furos, pois uma pequena quantidade de material removido ocasiona o esmagamento do mesmo (deformação plástica) que produz irregularidades na
Vários fatores influenciam na escolha da operação de usinagem feita com o alargador, tanto para a escolha da ferramenta, quanto para as condições de trabalho, os fatores que devem ser analisados são: a aplicação se é manual ou com máquina; as características do furo; a resistência e usinabilidade do furo; a velocidade de corte; o avanço; o sobremetal que está interligado ao tipo de material e o acabamento desejado e profundidade do furo; o alinhamento da peça; a vibração; o fluido de corte; a reafiação da ferramenta para o seu máximo rendimento. Os alargadores removem cavacos para melhorar o acabamento de furos pré furados, em que se deseja obter uma qualidade de tolerância IT7. O Resultado dessa operação depende da furação anterior.
A utilização do processo de alargamento confere uma precisão dimensional muito melhor a furos que necessitam destes ajustes. Observou-se os tipos de alargadores comumente empregados, destacando que os monocortantes apresentam vantagens tais como um melhor acabamento devido a divisão de funções entre a lâmina e a guia e facilidade em trocar a lâmina quando esta apresentar desvios dimensionais devido ao tempo de utilização. Viu-se que os alargadores podem ser fabricados com diversos materiais destacando-se os metais duros, cermet, nitreto de boro cúbico policristalino (PCBN) e o diamante policristalino (PCD). Observou-se os parâmetros de corte que devem ser utilizados através das tabelas apresentadas e através destas tem-se uma boa noção de como deve ser a característica do alargador para cada tipo de material a ser usinado.