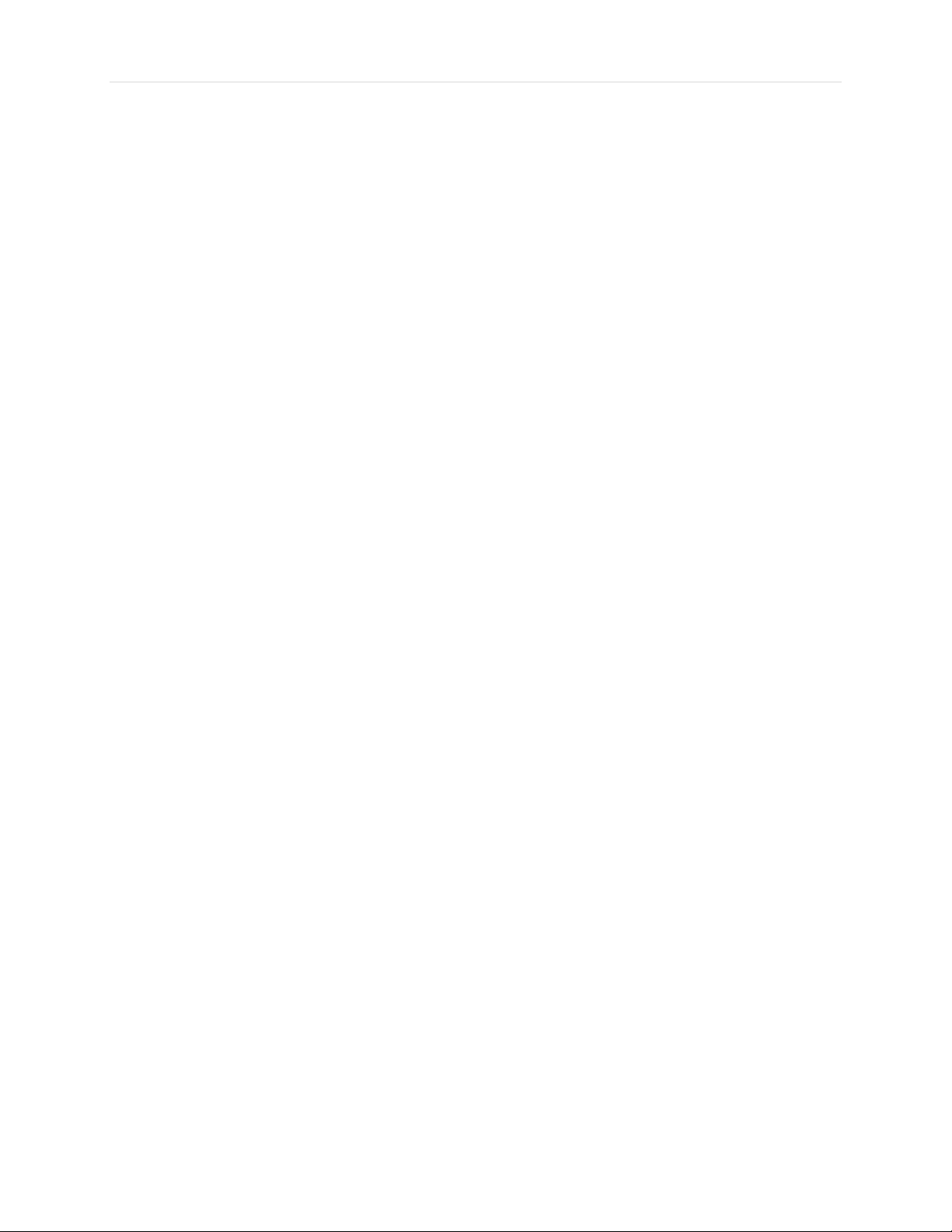
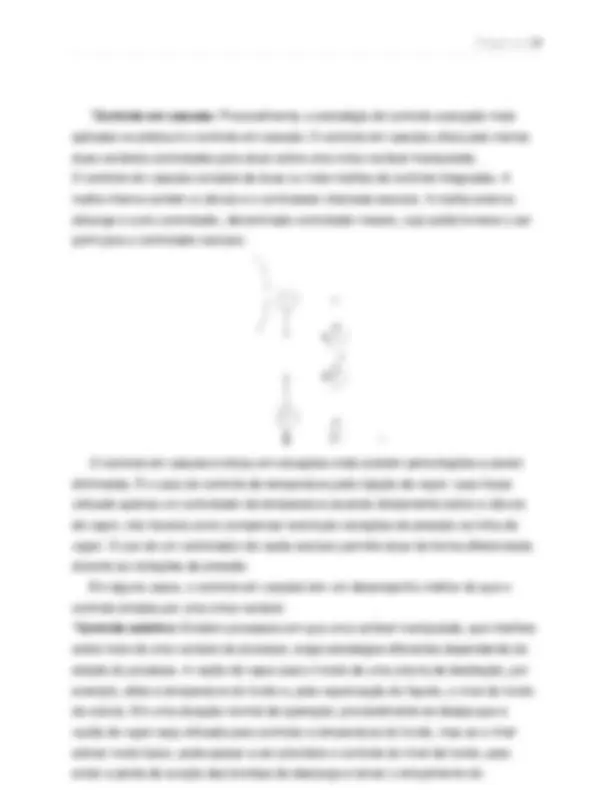
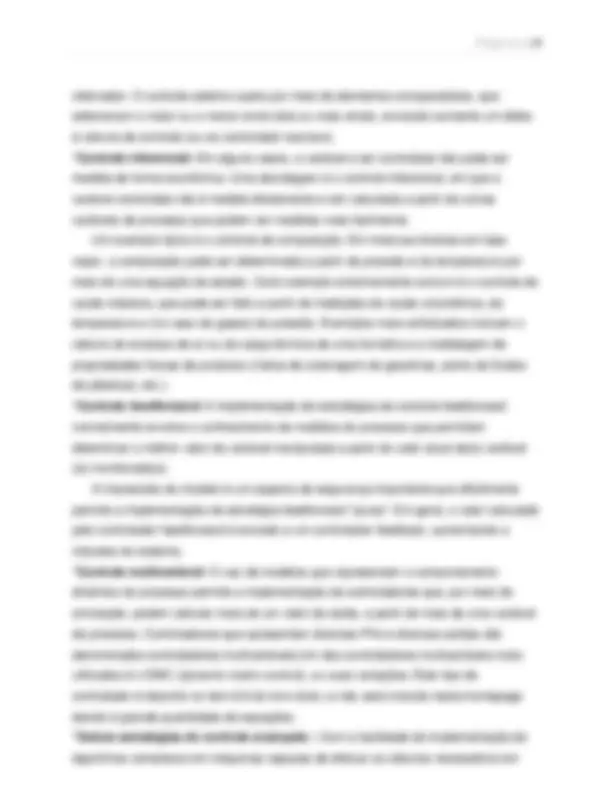
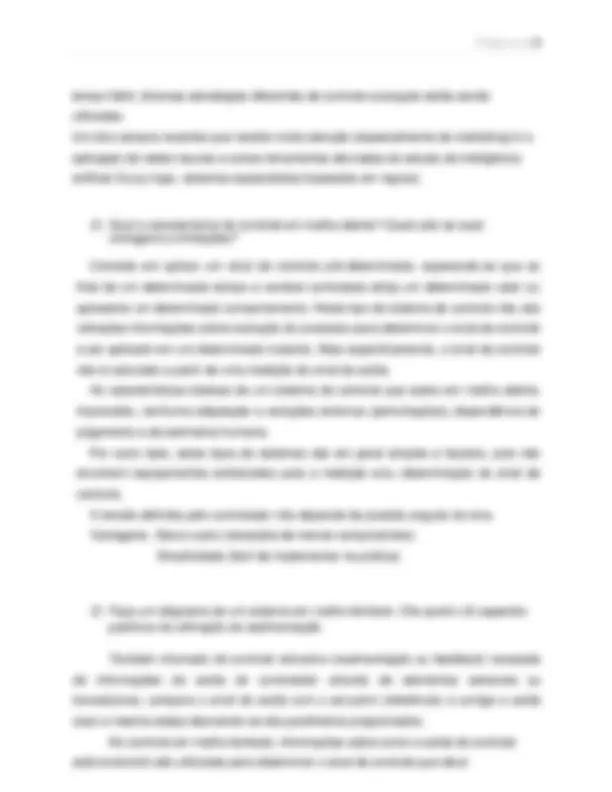
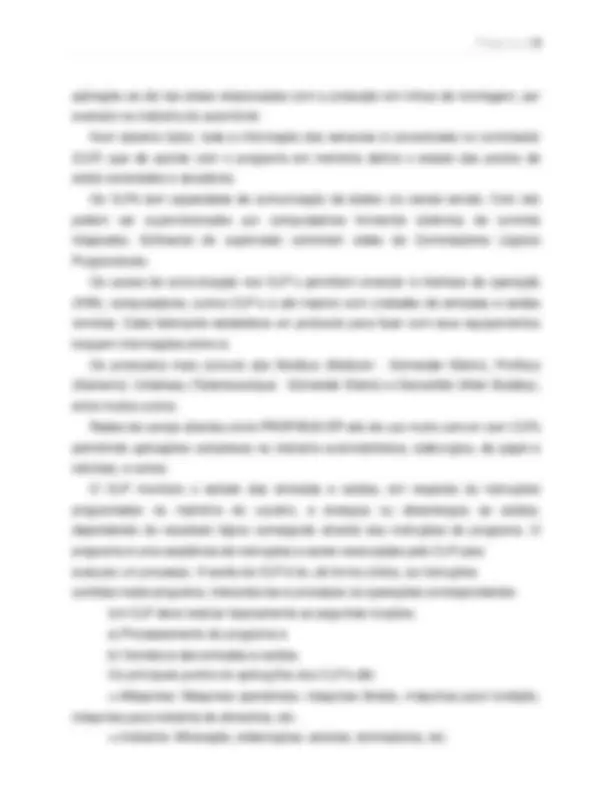
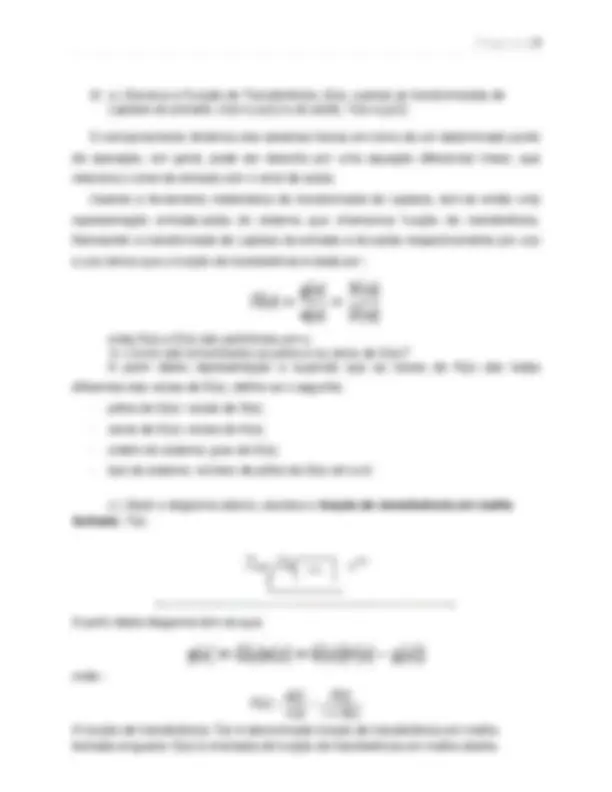
Estude fácil! Tem muito documento disponível na Docsity
Ganhe pontos ajudando outros esrudantes ou compre um plano Premium
Prepare-se para as provas
Estude fácil! Tem muito documento disponível na Docsity
Prepare-se para as provas com trabalhos de outros alunos como você, aqui na Docsity
Os melhores documentos à venda: Trabalhos de alunos formados
Prepare-se com as videoaulas e exercícios resolvidos criados a partir da grade da sua Universidade
Responda perguntas de provas passadas e avalie sua preparação.
Ganhe pontos para baixar
Ganhe pontos ajudando outros esrudantes ou compre um plano Premium
Comunidade
Peça ajuda à comunidade e tire suas dúvidas relacionadas ao estudo
Descubra as melhores universidades em seu país de acordo com os usuários da Docsity
Guias grátis
Baixe gratuitamente nossos guias de estudo, métodos para diminuir a ansiedade, dicas de TCC preparadas pelos professores da Docsity
Neste documento, aprenda sobre as estratégias de controle de processos industriais, incluindo controle de razão, cascata, seletivo, inferencial e feedforward. Saiba como controladores de processo utilizam algoritmos específicos, como pid, lógica fuzzy e redes neurais, para manter o controle de processos industriais. Desde a comunicação pneumática até a utilização de redes sem fio, exploraremos a evolução da comunicação entre controladores e outros componentes de sistemas de controle.
Tipologia: Notas de estudo
1 / 9
Esta página não é visível na pré-visualização
Não perca as partes importantes!
Uergs – Unidade Bento Gonçalves Engenharia de Bioprocessos e Biotecnologia Instrumentação & Controle Monichara Marinello 3ª Lista de Exercícios
1) Cite quatro (4) estratégias de controle de processo.
Na automação industrial, controladores de processo são equipamentos responsáveis pelo controle de processo industrial ou parte dele através de algoritmos de controle específicos, tais como PID, lógica fuzzy ou redes neurais. Podem ser ainda equipamentos programáveis capazes de realizar diversos tipos de algoritmos lógicos e matemáticos. Em grande parte das configurações, um controlador é responsável por uma única malha de controle. Esses instrumentos são dedicados em sua função e podem enviar dados diversos para outros dispositivos ou outras malhas no processo. Entre outros, podemos encontrar em diversos tipos de plantas industriais, controladores de temperatura (pirômetros), vazão, pressão, nível, posicionamento, etc. A comunicação entre os controladores e demais componentes de sistemas de controle evoluiu de maneira semelhante, passando de sinais e comandos pneumáticos para transmissão através de corrente e tensão e posteriormente evoluíram para a utilização de redes, sendo que já existem inclusive instrumentos e controladores com comunicação wireless. As estratégias de controle que fazem uso de mais de duas variáveis em uma malha de controle fechada são:
Geralmente, uma das vazões é determinada por outros sistemas da unidade ou fora dela. O objetivo do sistema de controle, então, é manipular a outra vazão para que, mesmo que a primeira vazão varie, a razão permaneça o mais constante possível. Uma forma de implementar o controle de razão consiste em medir as duas vazões e calcular a razão entre elas. Este valor calculado passa a ser a PV para um controlador de razão (FFC), que recebe um set point e manipula uma das vazões para que ela fique proporcional à outra.
Esta implementação apresenta uma desvantagem: em determinadas situações (partida, emergências), pode ser necessário controlar a vazão e não a razão. Um outro esquema, freqüentemente utilizado na prática, é o de utilizar um controlador de vazão para a segunda corrente de processo que opere em três modos: manual, automático e razão. Os modos manual e automático são os tradicionais; o modo automático permite que o operador forneça um set point de vazão. O modo razão utiliza um elemento (FY) que multiplica a vazão da primeira corrente por um set point de razão, determinando assim o set point do controlador de vazão.
refervedor. O controle seletivo opera por meio de elementos comparadores, que selecionam o maior ou o menor entre dois ou mais sinais, enviando somente um deles à válvula de controle (ou ao controlador escravo).
tempo hábil, diversas estratégias diferentes de controle avançado estão sendo utilizadas. Um dos campos recentes que recebe muita atenção (especialmente de marketing) é a aplicação de redes neurais e outras ferramentas derivadas do estudo de inteligência artificial (fuzzy logic, sistemas especialistas baseados em regras).
2) Qual a característica do controle em malha aberta? Quais são as suas vantagens e limitações? Consiste em aplicar um sinal de controle pré-determinado, esperando-se que ao final de um determinado tempo a variável controlada atinja um determinado valor ou apresente um determinado comportamento. Neste tipo de sistema de controle não são utilizadas informações sobre evolução do processo para determinar o sinal de controle a ser aplicado em um determinado instante. Mais especificamente, o sinal de controle não é calculado a partir de uma medição do sinal de saída. As características básicas de um sistema de controle que opera em malha aberta: imprecisão, nenhuma adaptação a variações externas (perturbações), dependência do julgamento e da estimativa humana. Por outro lado, estes tipos de sistemas são em geral simples e baratos, pois não envolvem equipamentos sofisticados para a medição e/ou determinação do sinal de controle. A tensão definida pelo controlador não depende da posicão angular do eixo. Vantagens : Baixo custo (necessita de menos componentes); Simplicidade (fácil de implementar na prática).
3) Faça um diagrama de um sistema em malha fechada. Cite quatro (4) aspectos positivos da utilização da realimentação.
Também chamado de controle retroativo (realimentação ou feedback) necessita de informações da saída do controlador através de elementos sensores ou transdutores, compara o sinal da saída com o set-point (referência) e corrige a saída caso a mesma esteja desviando-se dos parâmetros programados. No controle em malha fechada, informações sobre como a saída de controle está evoluindo são utilizadas para determinar o sinal de controle que deve
5) O que é um Controlador Lógico Programável (CLP ou PLC)? O sinal de controle gerado pelo controlador PID é assim genericamente dado como: u(t) = K [ e(t) + 1/Ti ∫e(τ)dτ + Td.(d e(t)/dt) ] Quais são os três parâmetros de sintonia no controlador? Um Controlador Lógico Programável ou Controlador Programável, conhecido também por suas siglas CLP ou CP e pela sigla de expressão inglesa PLC (Programmable Logic Controller), é um computador especializado, baseado num microprocessador que desempenha funções de controle de diversos tipos e níveis de complexidade. Geralmente as famílias de Controladores Lógicos Programáveis são definidas pela capacidade de processamento de um determinado numero de pontos de Entradas e/ou Saídas (E/S). Controlador Lógico Programável Segundo a ABNT (Associação Brasileira de Normas Técnicas), é um equipamento eletrônico digital com hardware e software compatíveis com aplicações industriais. Segundo a NEMA (National Electrical Manufacturers Association), é um aparelho eletrônico digital que utiliza uma memória programável para armazenar internamente instruções e para implementar funções específicas, tais como lógica, seqüenciamento, temporização,contagem e aritmética, controlando, por meio de módulos de entradas e saídas,vários tipos de máquinas ou processos. Um CLP é o controlador indicado para lidar com sistemas caracterizados por eventos discretos (SEDs), ou seja, com processos em que as variáveis assumem valores zero ou um (ou variáveis ditas digitais, ou seja, que só assumem valores dentro de um conjunto finito). Podem ainda lidar com variáveis analógicas definidas por intervalos de valores de corrente ou tensão elétrica.As entradas e/ou saídas digitais são os elementos discretos, as entradas e/ou saídas analógicas são os elementos variáveis entre valores conhecidos de tensão ou corrente. Os CLP's estão muito difundidos nas áreas de controle de processos ou de automação industrial. No primeiro caso a aplicação se dá nas indústrias do tipo contínuo, produtoras de líquidos, materiais gasosos e outros produtos, no outro caso a
aplicação se dá nas áreas relacionadas com a produção em linhas de montagem, por exemplo na indústria do automóvel. Num sistema típico, toda a informação dos sensores é concentrada no controlador (CLP) que de acordo com o programa em memória define o estado dos pontos de saída conectados a atuadores. Os CLPs tem capacidade de comunicação de dados via canais seriais. Com isto podem ser supervisionados por computadores formando sistemas de controle integrados. Softwares de supervisão controlam redes de Controladores Lógicos Programáveis. Os canais de comunicação nos CLP´s permitem conectar à interface de operação (IHM), computadores, outros CLP´s e até mesmo com unidades de entradas e saídas remotas. Cada fabricante estabelece um protocolo para fazer com seus equipamentos troquem informações entre si. Os protocolos mais comuns são Modbus (Modicon - Schneider Eletric), Profibus (Siemens), Unitelway (Telemecanique - Schneider Eletric) e DeviceNet (Allen Bradley), entre muitos outros. Redes de campo abertas como PROFIBUS-DP são de uso muito comum com CLPs permitindo aplicações complexas na indústria automobilística, siderurgica, de papel e celulose, e outras. O CLP monitora o estado das entradas e saídas, em resposta às instruções programadas na memória do usuário, e energiza ou desenergiza as saídas, dependendo do resultado lógico conseguido através das instruções de programa. O programa é uma seqüência de instruções a serem executadas pelo CLP para executar um processo. A tarefa do CLP é ler, de forma cíclica, as instruções contidas neste programa, interpreta-las e processar as operações correspondentes Um CLP deve realizar basicamente as seguintes funções: a) Processamento do programa e b) Varredura das entradas e saídas. Os principais pontos de aplicações dos CLP’s são: =>Máquinas: Máquinas operatrizes, máquinas têxteis, máquinas para fundição, máquinas para indústria de alimentos, etc. =>Indústria: Mineração, siderúrgicas, aciarias, laminadoras, etc.