
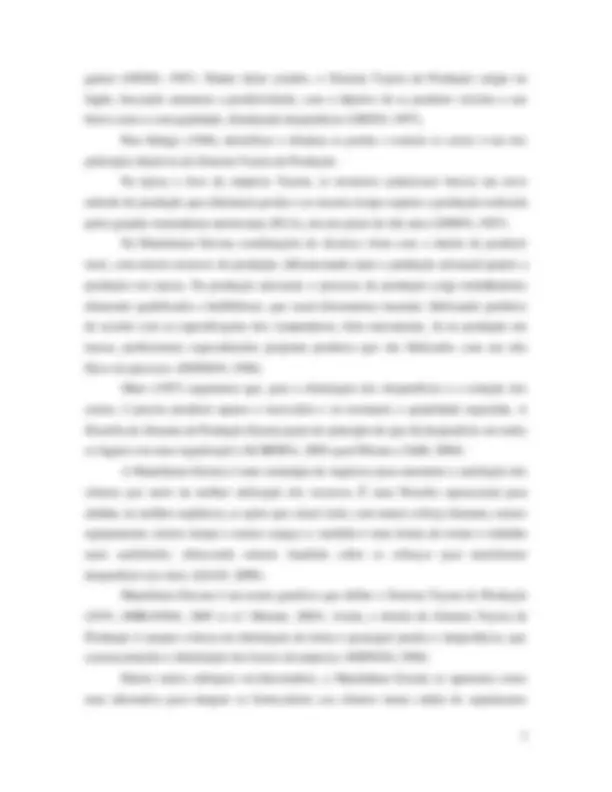
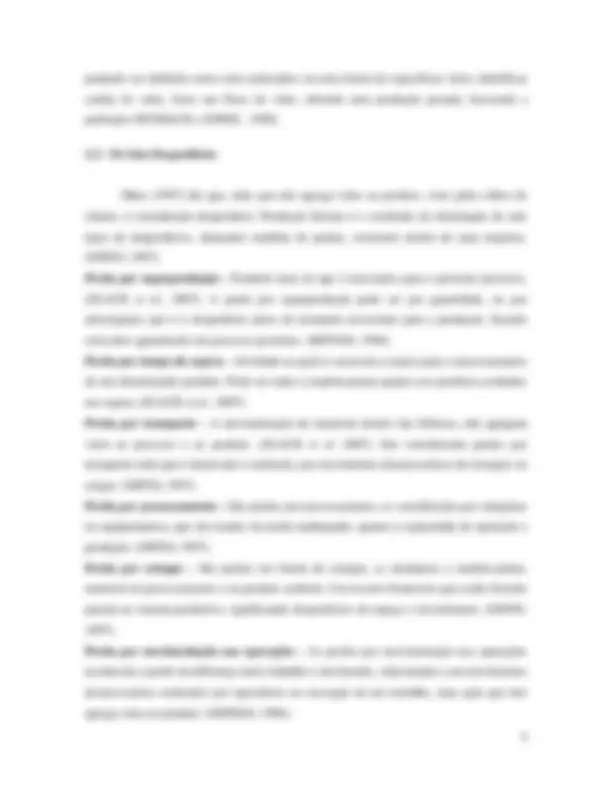
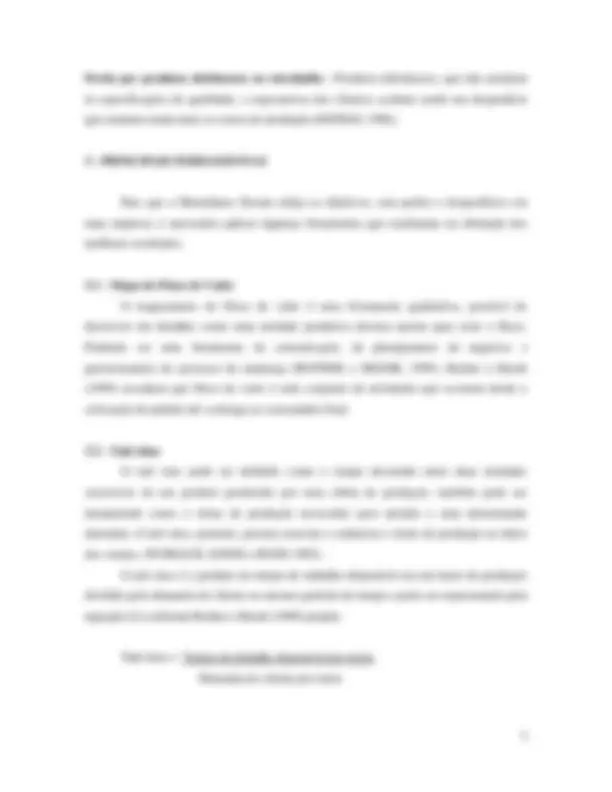
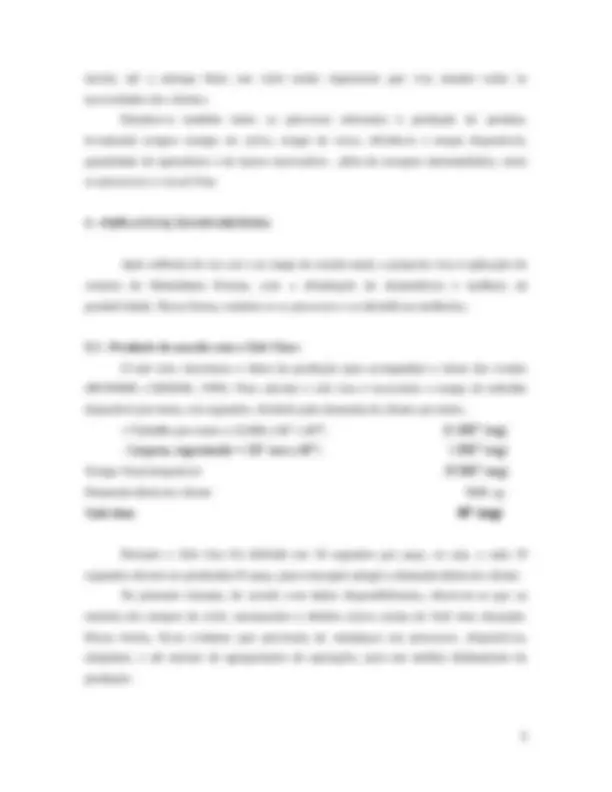
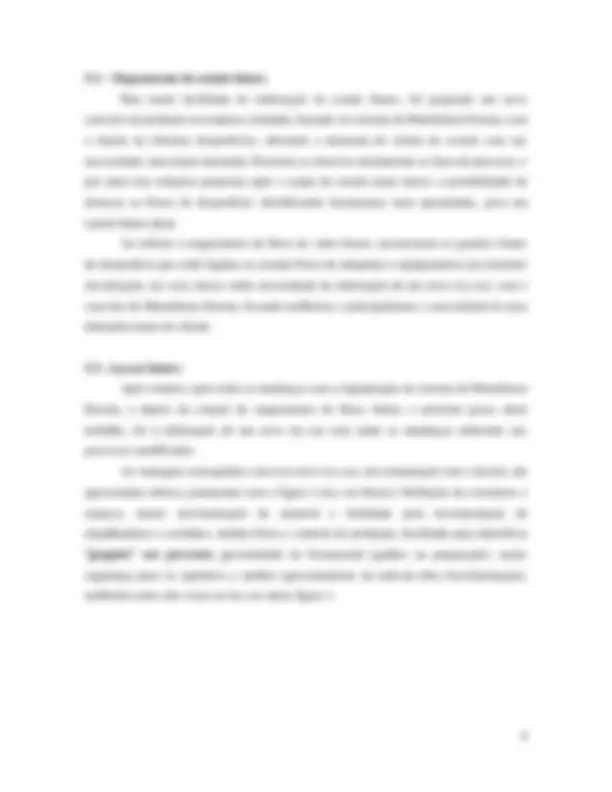
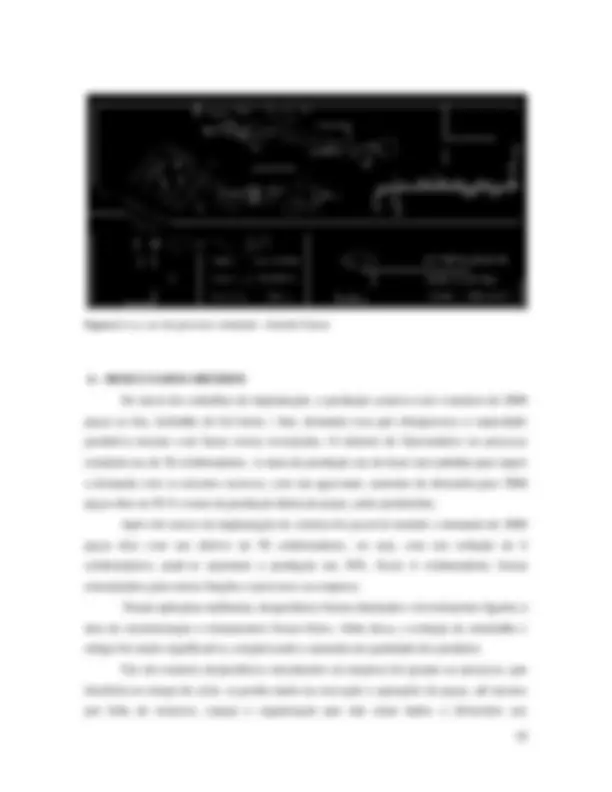
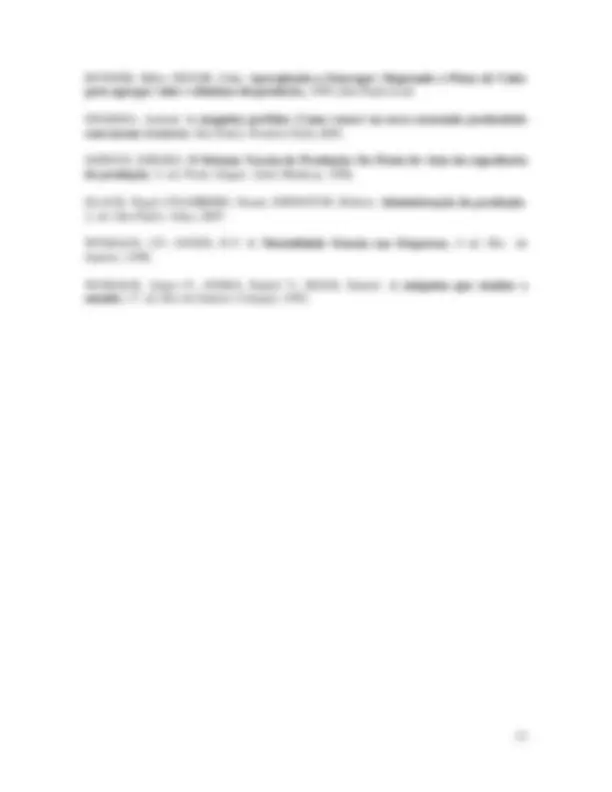
Estude fácil! Tem muito documento disponível na Docsity
Ganhe pontos ajudando outros esrudantes ou compre um plano Premium
Prepare-se para as provas
Estude fácil! Tem muito documento disponível na Docsity
Prepare-se para as provas com trabalhos de outros alunos como você, aqui na Docsity
Os melhores documentos à venda: Trabalhos de alunos formados
Prepare-se com as videoaulas e exercícios resolvidos criados a partir da grade da sua Universidade
Responda perguntas de provas passadas e avalie sua preparação.
Ganhe pontos para baixar
Ganhe pontos ajudando outros esrudantes ou compre um plano Premium
Comunidade
Peça ajuda à comunidade e tire suas dúvidas relacionadas ao estudo
Descubra as melhores universidades em seu país de acordo com os usuários da Docsity
Guias grátis
Baixe gratuitamente nossos guias de estudo, métodos para diminuir a ansiedade, dicas de TCC preparadas pelos professores da Docsity
Em um processo produtivo - Produção Enxuta
Tipologia: Notas de estudo
1 / 13
Esta página não é visível na pré-visualização
Não perca as partes importantes!
Pedro Augusto da Cunha Prof. Dani Marcelo Nonato Marques Tecnologia em Produção Faculdade de Tecnologia de Garça (FATEC) Caixa Postal 17400 – 000 – Garça – SP – Brasil pedrin.cunha@hotmail.com danimarcelo@uol.com.br Abstract - Since the global marketing has been yet more competitive, and with the client’s needs of obtaining his/her product faster and faster, the companies have been intensely looking for new managing tools that direct them to an increased competitiveness, flexibility, quality and productivity. Due to this context, the Lean Manufacturing philosophy raises as a primordial managing methodology, applying concepts linked to production, always focusing on the decrease of wasting rates, either on the process or on the product itself. The aim of this paper is to relate a case study of a company that has implanted Lean Manufacturing, eliminating losses on the process and increasing quality on the manufactured products. The choice of this theme is linked to the Production context itself; besides, a need of the company of applying process and managing new tools have raised. The methodology will be done from a case study concerning concepts linked to Lean Manufacturing, as a way of obtaining results, eliminating processes that do not aggregate values to the product. We will also show the importance of this system and its improvements on setting up a company Resumo - Com o mercado global ainda mais competitivo e a necessidade do cliente em obter o produto ainda mais rápido, as empresas buscam intensamente novas ferramentas de gerenciamento, que as direcionem para uma maior competitividade, flexibilidade, qualidade e produtividade. Diante deste cenário a filosofia da Produção Enxuta ou Manufatura Enxuta, surge como uma metodologia fundamental às empresas, aplicando conceitos ligados a produção, sempre com o foco na redução de desperdício, seja no processo ou no produto. Este trabalho tem como objetivo principal relatar um estudo de caso de uma organização que implantou a Manufatura Enxuta, eliminando perdas no processo e qualidade nos produtos fabricados. A escolha do tema está relacionada ao próprio contexto da produção, além disso, surgiu de uma necessidade da empresa em aplicar uma nova ferramenta de processo e gerenciamento. A metodologia será feita a partir de um estudo de caso, seguindo conceitos ligados a produção enxuta, utilizando ferramentas que
compõem a Manufatura Enxuta, como auxílio para alcançar resultados, eliminando processos e serviços que não agregam valor ao produto, mostrando também a importância deste sistema e suas melhorias na implantação em uma organização.
1 - INTRODUÇÃO Com o processo de globalização em curso, o mercado mundial se tornou ainda mais competitivo, exigindo a redução de custos e melhores níveis de produtividade e qualidade, entre outras necessidades. O desafio das organizações, aliado à competitividade e à agilidade tecnológica, fez emergir novas técnicas gerenciais, as quais buscam manter as organizações em um cenário constante de mudanças, desenvolvendo sistemas administrativos eficientemente. A Manufatura Enxuta é embasada nos conceitos produtivos do Japão pós Segunda Guerra Mundial, com a necessidade das empresas japonesas do setor automobilístico, em especial a Toyota Motor Company , de desenvolver métodos diferentes para fabricar veículos com métodos mais adequados ao cenário japonês, resultou em um sistema de produção , conhecido como Sistema Toyota de Produção. Para implementá-la é necessária uma mudança de pensamento de todos que fazem parte da organização, desde a alta gerência até os operadores, tendo conhecimento constante em todas as fases do processo do produto, desde o fornecedor até a entrega do produto final ao cliente, passando por todo fluxo de material e de informações ao longo da cadeia produtiva. O conhecimento sobre os processos é importante dentro do contexto organizacional, porque possibilita enxergar oportunidades de melhorias para os processos, melhorias essas que devem ser rápidas e com pouco custo de implementação.
2.1- Manufatura enxuta Após a Segunda Guerra Mundial, um grande passo foi dado no desenvolvimento de um novo sistema de gestão de manufatura, o Sistema Toyota de Produção, criado em uma economia totalmente abalada e com condições econômicas afetadas pela depressão pós-
podendo ser definida como cinco princípios ou uma forma de especificar valor, identificar cadeia de valor, fazer um fluxo de valor, obtendo uma produção puxada, buscando a perfeição (WOMACK e JONES , 1998).
2.2 - Os Sete Desperdícios
Ohno (1997) diz que, tudo que não agrega valor ao produto, visto pelos olhos do cliente, é considerado desperdício. Produção Enxuta é o resultado da eliminação de sete tipos de desperdícios, chamados também de perdas, existentes dentro de uma empresa. (OHNO, 1997). Perda por superprodução - Produzir mais do que é necessário para o próximo processo. (SLACK et al ., 2007). A perda por superprodução pode ser por quantidade, ou por antecipação, que é o desperdício antes do momento necessário para a produção, ficando estocados aguardando um processo posterior. (SHINGO, 1996). Perda por tempo de espera - Atividade na qual se necessita a espera para o processamento de um determinado produto. Pode ser tanto à matéria-prima quanto aos produtos acabados em espera. (SLACK et.al ., 2007). Perda por transporte - A movimentação de materiais dentro das fábricas, não agregam valor ao processo e ao produto. (SLACK et al. 2007). São consideradas perdas por transporte tudo que é deslocado e realizado, por movimentos desnecessários de estoques ou cargas. (OHNO, 1997). Perda por processamento - São perdas por processamento, as consideradas por máquinas ou equipamentos, que são usados de modo inadequado, quanto à capacidade de operação e produção. (OHNO, 1997). Perda por estoque - São perdas em forma de estoque, as mediantes a matéria-prima, material em processamento e ou produto acabado. Um recurso financeiro que acaba ficando parado no sistema produtivo, significando desperdícios de espaço e investimento. (OHNO, 1997). Perda por movimentação nas operações - As perdas por movimentação nas operações acontecem a partir da diferença entre trabalho e movimento, relacionados com movimentos desnecessários realizados por operadores na execução de um trabalho, uma ação que não agrega valor ao produto. (SHINGO, 1996).
Perda por produtos defeituosos ou retrabalho - Produtos defeituosos, que não atendam às especificações de qualidade, e expectativas dos clientes; acabam sendo um desperdício que aumenta ainda mais os custos de produção.(SHINGO, 1996).
3 - PRINCIPAIS FERRAMENTAS
Para que a Manufatura Enxuta atinja os objetivos, sem perdas e desperdícios em uma empresa, é necessário aplicar algumas ferramentas que auxiliaram na obtenção dos melhores resultados.
3.1 - Mapa de Fluxo de Valor O mapeamento do fluxo de valor é uma ferramenta qualitativa, possível de descrever em detalhes como uma unidade produtiva deveria operar para criar o fluxo. Podendo ser uma ferramenta de comunicação, de planejamento de negócios e gerenciamento do processo de mudança (ROTHER e SHOOK, 1999). Rother e Shook (1999) ressaltam que fluxo de valor é todo conjunto de atividades que ocorrem desde a colocação do pedido até a entrega ao consumidor final.
3.2 - Takt time O takt time pode ser definido como o tempo decorrido entre duas unidades sucessivas de um produto produzido por uma célula de produção, também pode ser interpretado como o ritmo de produção necessário para atender a uma determinada demanda. O takt time , portanto, procura associar e cadenciar o ritmo de produção ao ritmo das vendas. (WOMACK, JONES e ROOS 1992). O takt time é o produto do tempo de trabalho disponível em um turno de produção dividido pela demanda do cliente no mesmo período de tempo e pode ser representado pela equação [1] conforme Rother e Shook (1999) propõe.
Takt time = Tempo de trabalho disponível por turno Demanda do cliente por turno
Figura 1: Lay-out do processo estudado – Estado Atual
Antes da Implantação do sistema de Manufatura Enxuta, a área estudada não obedecia a um critério referente à eliminação dos setes desperdícios, não era interessante até então para a empresa ter um estudo especificado na área. Mas com a necessidade não só da eliminação dos desperdícios e sim, para o aperfeiçoamento de processos e do produto em si, foi feito o estudo inicial, descrito no Lay out do estado atual. Observou-se muitos pontos falhos como arranjos físicos inadequados, estoques no processo, manuseio do produto, desbalanceamento de processos e movimentações desnecessárias. Logo após este estudo inicial do lay-out , o próximo passo foi mapear todo o fluxo de valor no intuito de verificar quais os pontos de melhoria.
4.2 Mapeamento do estado atual O mapeamento do estado atual foi iniciado, com o levantamento (mensurado) de todos os itens em processo. Na empresa analisada, o Planejamento e Controle da Produção possue uma estratégia de previsão de vendas, e os pedidos de matéria prima, de acordo com uma análise de determinado período de vendas anteriores. Após o levantamento de todos os itens em processo, foi dimensionada a expedição final do produto, local onde todos os produtos fabricados ficam armazenados, de maneira que os processos ficam de forma continua, ligados diretamente ao cliente, um processo contínuo, desde o processamento
inicial, até a entrega final, um valor muito importante que visa atender todas às necessidades dos clientes. Estudou-se também todos os processos referentes à produção do produto, levantando tempos (tempo de ciclos, tempo de troca, eficiência e tempo disponível), quantidade de operadores e de turnos necessários , além de estoques intermediários, entre os processos e o Lead Time
5 - IMPLANTAÇÃO DO SISTEMA
Após reflexão do lay-out e no mapa do estado atual, a proposta visa à aplicação do sistema de Manufatura Enxuta, com a eliminação de desperdícios e melhora da produtividade. Dessa forma, estudou-se os processos e se identificou melhorias.
5.1 - Produzir de acordo com o Takt Time : O takt time sincroniza o ritmo da produção para acompanhar o ritmo das vendas (ROTHER e SHOOK, 1999). Para calcular o takt time é necessário o tempo de trabalho disponível por turno, em segundos, dividido pela demanda do cliente por turno.
Portanto o Takt time foi definido em 10 segundos por peça, ou seja, a cada 10 segundos deverá ser produzida 01 peça, para conseguir atingir a demanda diária do cliente. No primeiro instante, de acordo com dados disponibilizados, observou-se que na maioria dos tempos de ciclo, mensurados e obtidos estava acima do Takt time desejado. Dessa forma, ficou evidente que precisaria de mudanças em processos, dispositivos, máquinas, e até mesmo de agrupamento de operações, para um melhor alinhamento da produção.
Figura 2: Lay-out do processo estudado – Estado Futuro
No inicio dos trabalhos de implantação, a produção contava com o número de 2000 peças ao dia, (trabalho de 8,8 horas / dia), demanda essa que ultrapassava a capacidade produtiva mesmo com horas extras executadas. O número de funcionários no processo estudado era de 56 colaboradores. A meta da produção era de fazer um trabalho para suprir a demanda com os mesmos recursos, com um agravante, aumento da demanda para 3000 peças dias ou 50 % a mais da produção diária de peças, antes produzidas. Após três meses da implantação do sistema foi possível atender a demanda de 3000 peças dias com um efetivo de 50 colaboradores, ou seja, com um redução de 6 colaboradores, pode-se aumentar a produção em 50%. Esses 6 colaboradores foram remanejados para outras funções e processos na empresa. Foram aplicadas melhorias, desperdícios foram eliminado e investimentos ligados à área de reestruturação e treinamentos foram feitos. Além disso, a redução de retrabalho e refugo foi muito significativa, comprovando o aumento da qualidade dos produtos. Um dos maiores desperdícios encontrados na empresa foi quanto ao processo, que interferia no tempo de ciclo, se perdia muito na execução e operações de peças, até mesmo por falta de recursos, espaço e organização que não eram dados e oferecidos aos
colaboradores que tinham dificuldades e muitas vezes não conseguiam manter uma seqüência de trabalho padronizada. A figura 3 mostra o resultado final por meio de um comparativo entre o tempo de processo anterior a implantação do novo processo com o takt time calculado e operando no processo.
PROCESSO ESTADO ATUAL
13
17
12 13 11 13
14 14 12
14
4
7
15 15 12
15 (^12 )
14 12
7
0
2
4
6
8
10
12
14
16
18
PROCESSO 1 PROCESSO 2 PROCESSO 2.1 PROCESSO 2.2 PROCESSO 2.3 PROCESSO 2.4 PROCESSO 2.5 PROCESSO 2.6 PROCESSO 2.7 PROCESSO 2.8 PROCESSO 3 PROCESSO 3.1 PROCESSO 3.2 PROCESSO 3.3 PROCESSO 3.4 PROCESSO 3.5 PROCESSO 3.6 PROCESSO 3.7 PROCESSO 4 PROCESSO 5 PROCESSO 5.1 PROCESSO 5. PROCESSO
TEMPO
Takt Time (10segundos)
Figura 3: Comparativo de tempos no processo – Estado Atual
Após as mudanças na forma de trabalho, criação de dispositivos, balanceamento e alinhamento de trabalho, todas as operações ficaram dentro do takt-time estabelecido e da implantação do sistema de Manufatura Enxuta, conforme pode ser observado na figura 4.
PROCESSO ESTADO FUTURO
7 8
10 8
2
9 10 8 9 10 10
5
0
2
4
6
8
10
12
PROCESSO 1 PROCESSO 2 PROCESSO 2.1 PROCESSO 2.2 PROCESSO 3 PROCESSO 3.1 PROCESSO 3.2 PROCESSO 3.3 PROCESSO 3.4 PROCESSO 4 PROCESSO 5 PROCESSO 5. PROCESSO
TEMPO
PROCESSO Takt Time (10 segundos)
Figura 4: Takt Time em relação aos processos – Estado Futuro
ROTHER, Mike; SHOOK, John. Aprendendo a Enxergar: Mapeando o Fluxo de Valor para agregar valor e eliminar desperdícios, 1999 , São Paulo:Lean
SHARMA, Amand. A maquina perfeita: Como vencer na nova economia produzindo com menos recursos. São Paulo: Prentice Hall , 2003.
SHINGO, SHIGEO. O Sistema Toyota de Produção: Do Ponto de vista da engenharia de produção. 2. ed. Porto Alegre: Artes Medicas, 1996.
SLACK, Nigel; CHAMBERS, Stuart; JOHNSTON, Robert_._ Administração da produção.
WOMACK, J.P.; JONES, D.T. A Mentalidade Enxuta nas Empresas , 4 ed. Rio de Janeiro ,1998.
WOMACK, James P.; JONES, Daniel T.; ROOS, Daniel. A máquina que mudou o mundo. 17. ed. Rio de Janeiro: Campus, 1992.