
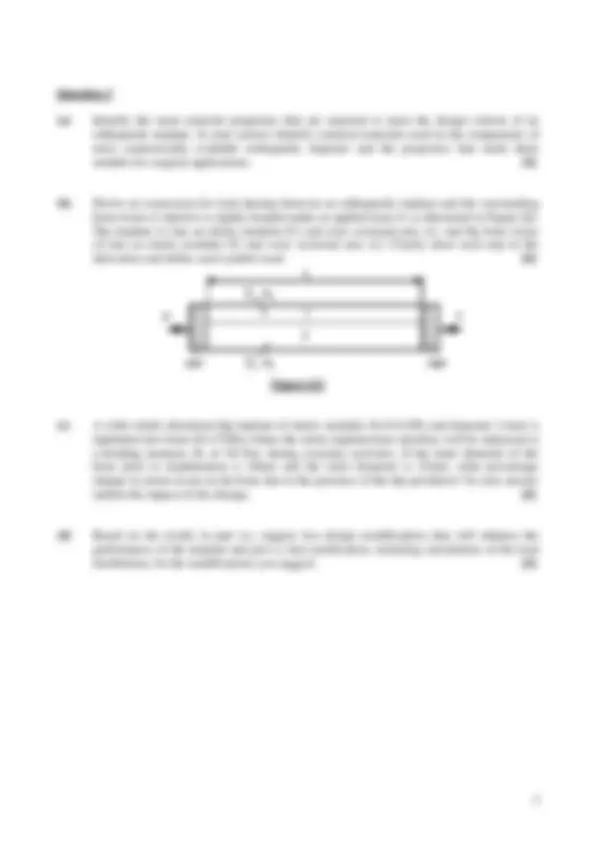
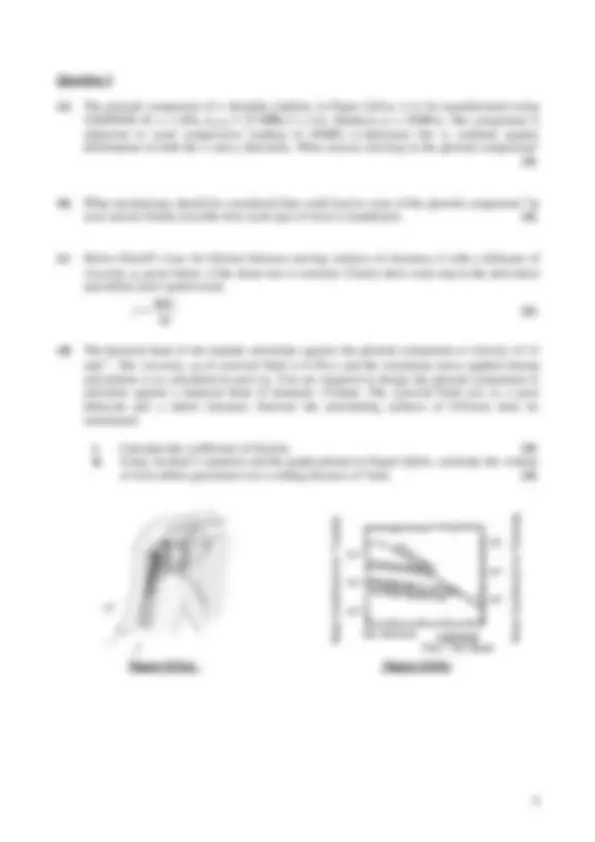
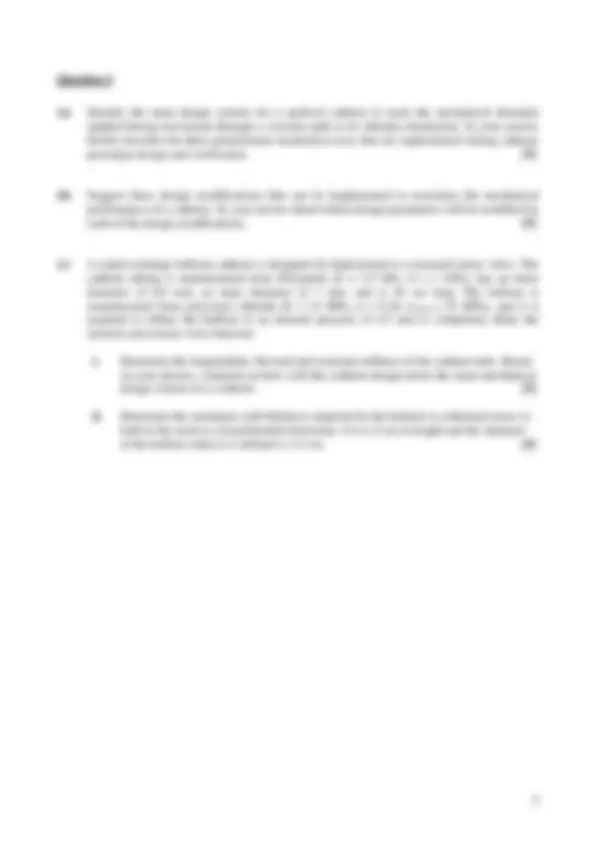
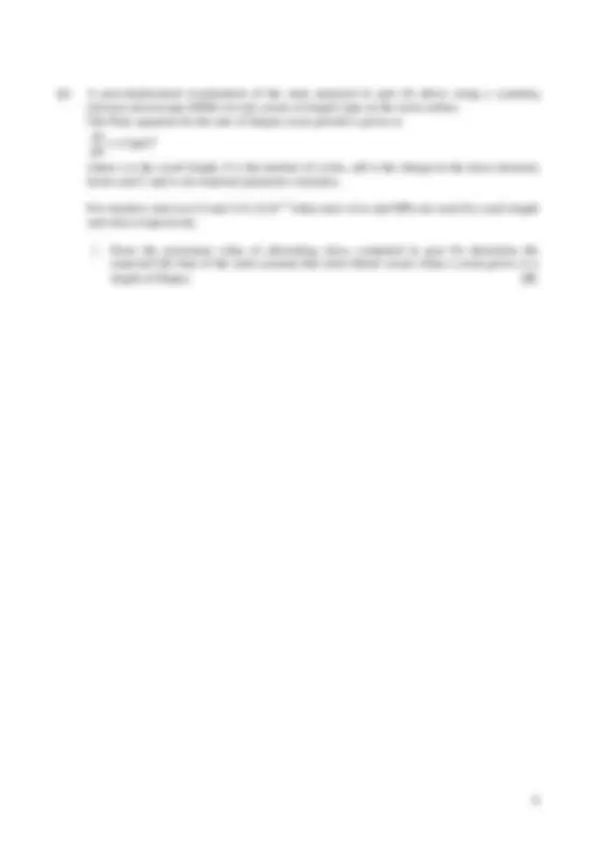
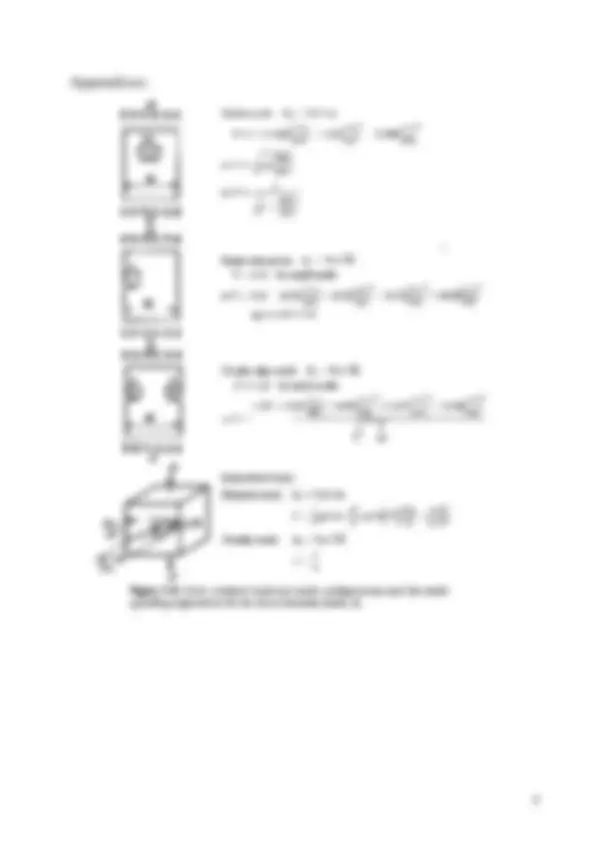
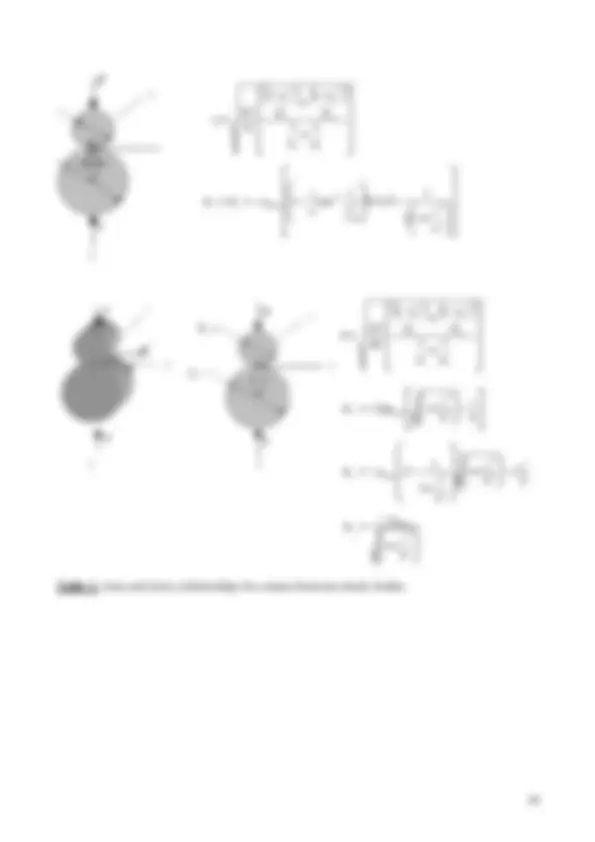
Study with the several resources on Docsity
Earn points by helping other students or get them with a premium plan
Prepare for your exams
Study with the several resources on Docsity
Earn points to download
Earn points by helping other students or get them with a premium plan
Community
Ask the community for help and clear up your study doubts
Discover the best universities in your country according to Docsity users
Free resources
Download our free guides on studying techniques, anxiety management strategies, and thesis advice from Docsity tutors
Main points of this past exam paper are: Prosthesis Implanted, Quadriceps Muscle, Muscle Force, Acts, Angle, Muscle, Joint Reaction Force, Implant, Titanium, Femoral Component
Typology: Exams
1 / 12
This page cannot be seen from the preview
Don't miss anything!
Exam Code(s) 4 BG
Exam(s) 4
th Biomedical Engineering
Module Code(s) ME
Module(s) Medical Implant and Device Design
Paper No. 1
Repeat Paper
External Examiner(s) Professor David Taylor
Internal Examiner(s) Professor Peter McHugh
Dr. Laoise McNamara
Dr. Patrick McGarry
Instructions: (^) Answer 5 questions.
All questions will be marked equally.
Use a separate answer book for each section.
No. of Pages 12
Department(s) Mechanical & Biomedical Engineering
Course Co-ordinator(s) Dr. Laoise McNamara, Dr. Patrick McGarry
Requirements:
Statistical/ Log Tables
Release to Library: Yes
Section A
Question 1
(a) A knee prosthesis implanted into a man of mass 80 Kg generates a body weight W. During
single leg stance the quadriceps muscle, with muscle force M , is active and acts at an angle
of 12 Āŗ from the vertical (Figure Q1(a)). The mass of the lower leg is W / 3 and the muscle
force is 3. 2W. Calculate the joint reaction force, J , and the angle at which it is acting.
(b) The femoral component of the implant is made of titanium (E = 105 GPa, ļ®=0.3 3 ) with a
radius of curvature 58 mm. The curved polethylene tibial tray (E = 20 MPa, ļ®=0.46, Ļyield= 20
MPa) has an internal radius of curvature of 58.1mm. The thickness, l , of the contact between
the femoral component and the tibial tray is 1 4 mm. Assuming that the contact conditions
can be idealised as shown in Figure Q1(b), calculate the contact area half width, b , under the
applied joint reaction force. [4]
(c) Determine the maximum pressure in the assembly under the applied joint reaction force
which is distributed over the contact area. [2]
(d) Determine the maximum shear stress generated in the tibial tray at the point A located a
distance 0. 45 b from the contact surface (Figure Q1b). Will failure occur in the tibial tray due
to the applied contact forces? [4]
Figure Q1(a) Figure Q1(b)
0.45 b
Question 3
(a) The glenoid component of a shoulder implant, in Figure Q3(a), is to be manufactured using
UHMWPE (E = 1 GPa, Ļyield = 25 MPa, ν = 0.4, Hardness p = 35 MPa). The component is
subjected to axial compressive loading of 30MPa (z-direction) but is confined against
deformation in both the x and y directions. What stresses develop in the glenoid component?
(b) What mechanisms should be considered that could lead to wear of the glenoid component? In
your answer briefly describe how each type of wear is manifested. [ 4 ]
(c) Derive Petroffās Law for friction between moving surfaces of clearance h with a lubricant of
viscosity ļ, given below, if the shear rate is constant. Clearly show each step in the derivation
and define each symbol used.
hp
f
(d) The humeral head of the implant articulates against the glenoid component at velocity of 12
rads
articulation is as calculated in part (a). You are required to design the glenoid component to
articulate against a humeral head of diameter 15. 6 mm. The synovial fluid acts as a poor
lubricant and a radial clearance between the articulating surfaces of 0. 01 mm must be
maintained.
i. Calculate the coefficient of friction. [ 4 ]
ii. Using Archardās equation and the graph plotted in Figure Q3(b), calculate the volume
of wear debris generated over a sliding distance of 5 mm. [ 4 ]
Wear Coefficient for Transfer
No lubricant (^) Lubricant
Poor Fair Good
10
10 -^4
10
10 -^2
10 -^4
10 -^6
Wear Coefficient for Transfer^ Wear Coefficient for Particles
No lubricant (^) Lubricant
Poor Fair Good
10
10 -^4
10
10 -^2
10 -^4
10 -^6
Wear Coefficient for Particles
Figure Q3(a) Figure Q3(b)
Question 4
(a) Identify the main design criteria for a medical catheter to meet the mechanical demands
applied during movement through a vascular path to its ultimate destination. In your answer
briefly describe the three predominant mechanical tests that are implemented during catheter
prototype design and verification. [ 5 ]
(b) Suggest three design modifications that can be implemented to maximize the mechanical
performance of a catheter. In your answer detail which design parameters will be modified by
each of the design modifications. [ 5 ]
(c) A rapid exchange balloon catheter is designed for deployment to a stenosed aortic valve. The
catheter tubing is manufactured from Polyimide (E = 3.5 GPa, G = 1 GPa), has an inner
diameter of 0.8 mm, an outer diameter of 1 mm, and is 36 cm long. The balloon is
manufactured from polyvinyl chloride (E = 23 MPa, ν = 0.3 8 , Ļyield = 25 MPa), and it is
required to inflate the balloon to an internal pressure of 4. 5 atm to completely dilate the
stenosis and restore valve function.
i. Determine the longitudinal, flexural and torsional stiffness of the catheter tube. Based
on your answer, comment on how well this catheter design meets the main mechanical
design criteria for a catheter. [ 5 ]
ii. Determine the minimum wall thickness required for the balloon to withstand stress in
both in the axial or circumferential directions, if it is 4 cm in length and the diameter
of the balloon when it is inflated is 2.5 cm. [ 5 ]
Section B
Question 6
(a) In order to correct a dental mis-alignment an orthodontist fixes a Nitinol wire to three teeth,
as shown in Figure Q6. The objective is to pull the middle tooth into alignment with the other
two. When inserting the wire the orthodontist bends it to an initial curvature. The curvature
then gradually decreases during the course of the treatment until the curvature is zero (i.e. the
wire is straight).
Figure Q
The wire is circular in cross-section with a diameter of 1mm has the following material
properties:
EAUS=83 GPa
ļ MAR=18 GPa
S tL=ļ³
E tL=414 MPa
S tU=ļ³
E tU=100 MPa
Calculate the maximum bending stress in the wire when the curvature reduces to 0.03mm
from an initial curvature of:
i. 0.1 mm
ii. 0.034 mm
(b) In a finite element plane stress stent analysis, following simulation of deployment and recoil,
a pressure load equivalent to 80mmHg is applied to a stent geometry. At a point near the
surface of the stent plastic hinge the stresses computed before and after the application of this
load are given in Table Q6.
ļ³xx (MPa) ļ³yy (MPa) ļ³xy (MPa)
before fatigue load 200 - 50 0
after fatigue load 300 10 100
Table Q
Construct a Goodman diagram for a stainless steel stent based on the data in Table Q6. Does
failure occur? [5]
Straight wire
prior to
attachment
Arrangement of teeth
at beginning of
treatment
Arrangement of
teeth at end of
treatment
tooth
tooth
tooth
tooth
tooth
tooth
Straight wire
prior to
attachment
Arrangement of teeth
at beginning of
treatment
Arrangement of
teeth at end of
treatment
tooth
tooth
tooth
tooth
tooth
tooth
tooth
tooth
tooth
(c) A post-deployment examination of the stent analysed in part (b) above using a scanning
electron microscope (SEM) reveals cracks of length 1ļm on the stent surface.
The Paris equation for the rate of fatigue crack growth is given as
ļØ ļ©
m C K
dN
da
ļ½ ļ
where a is the crack length, N is the number of cycles, ļ K is the change in the stress intensity
factor and C and m are material parameter constants.
For stainless steel m =3.4 and C =1.2x
and stress respectively.
i. From the maximum value of alternating stress computed in part (b) determine the
expected life time of the stent (assume that stent failure occurs when a crack grows to a
length of 20ļm). [5]
Table 1: Area and stress relationships for contact between elastic bodies
3
1 2
2
2
2
1
2 1
d d
a
ļ
2
2
1
max
1 tan
a
z a
a^ z
z
p x y
1 2
2
2
2
1
2
1
d d
l
b
b
z
b
z
p x (^) 2
2
max
b
z
b
z
b
z
p y
2
2
2
max (^2)
2
2
max
b
z
p
z