
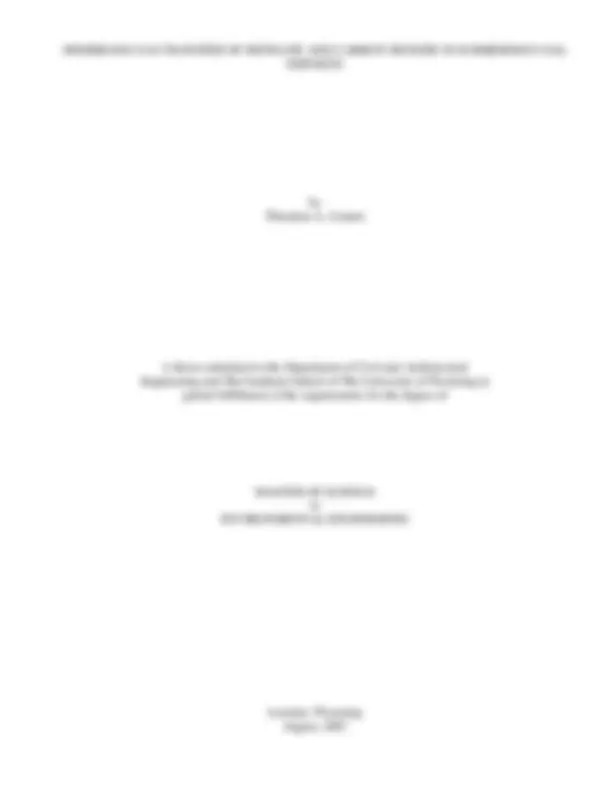
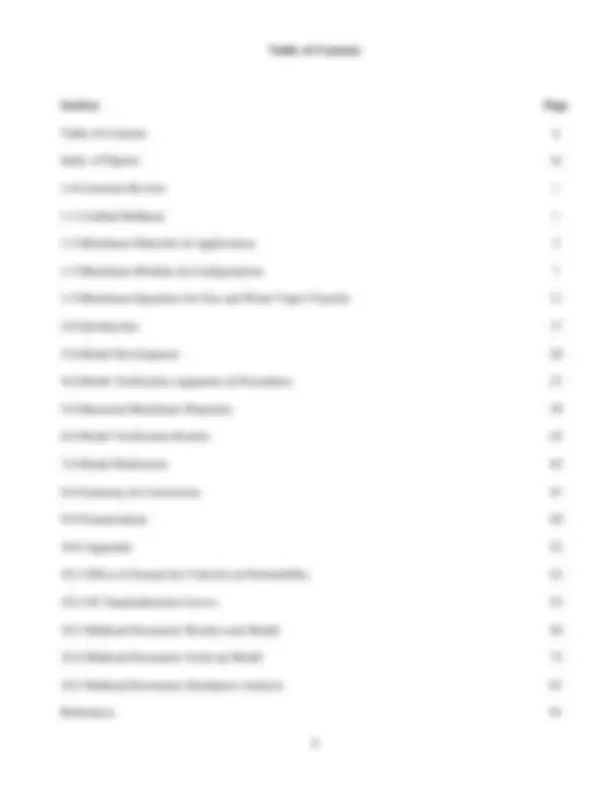
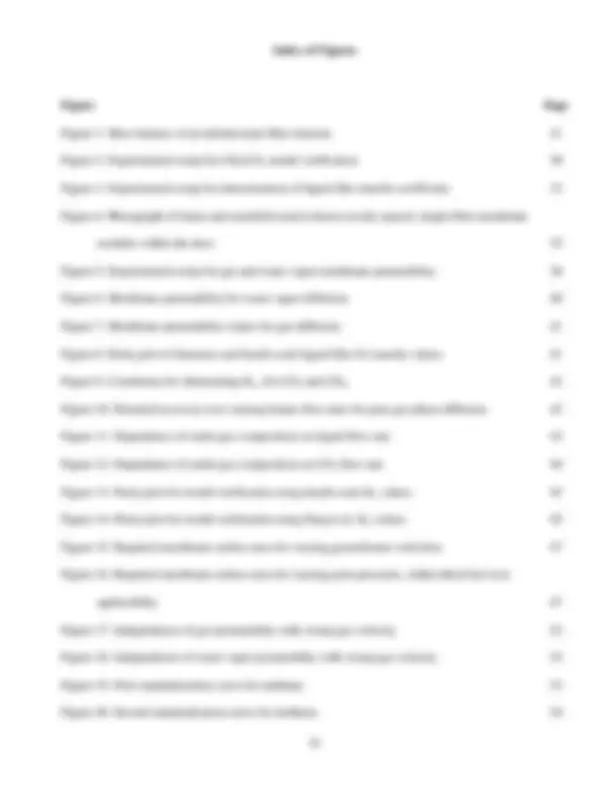
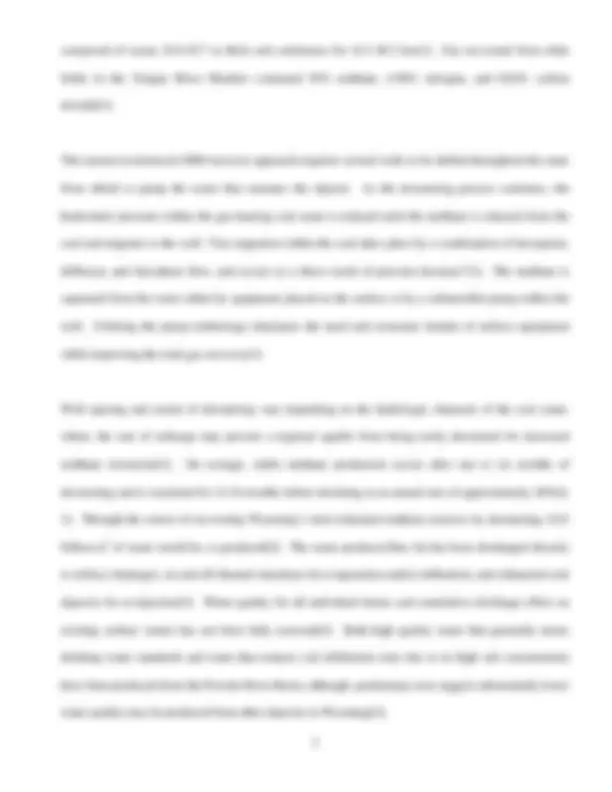
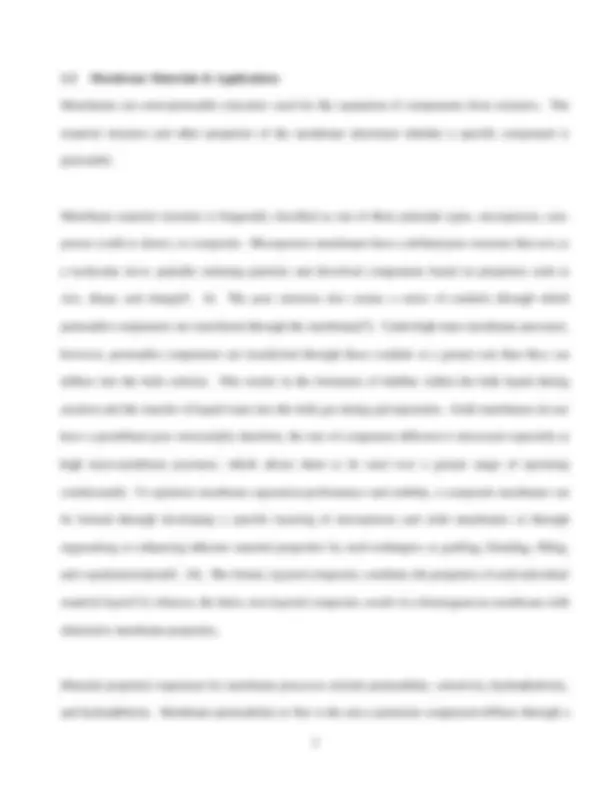
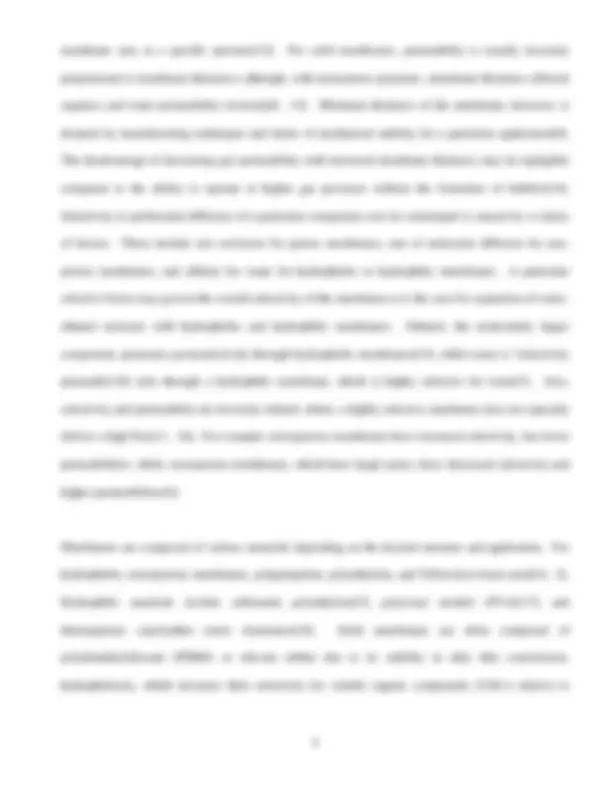
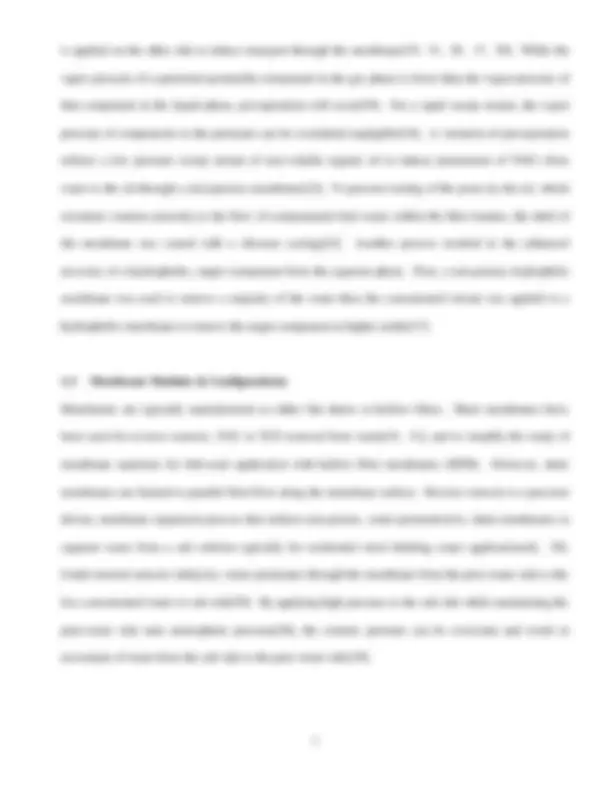
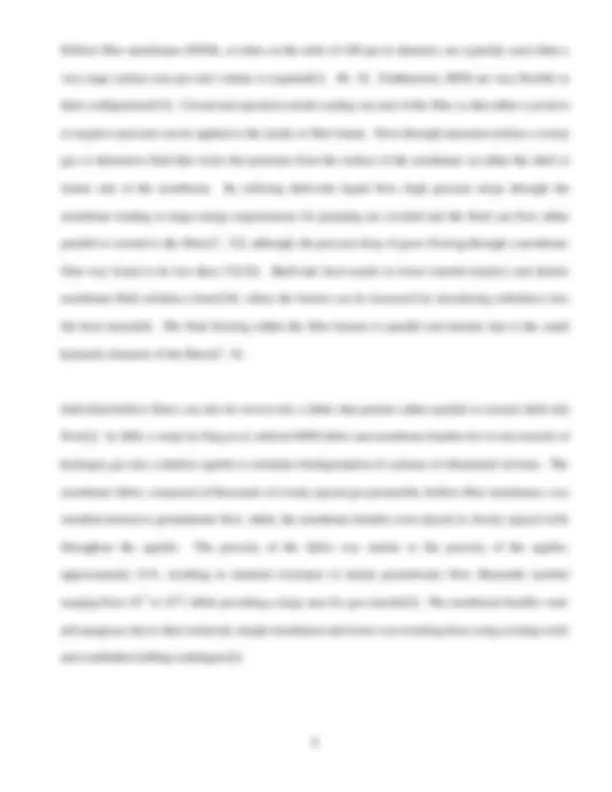
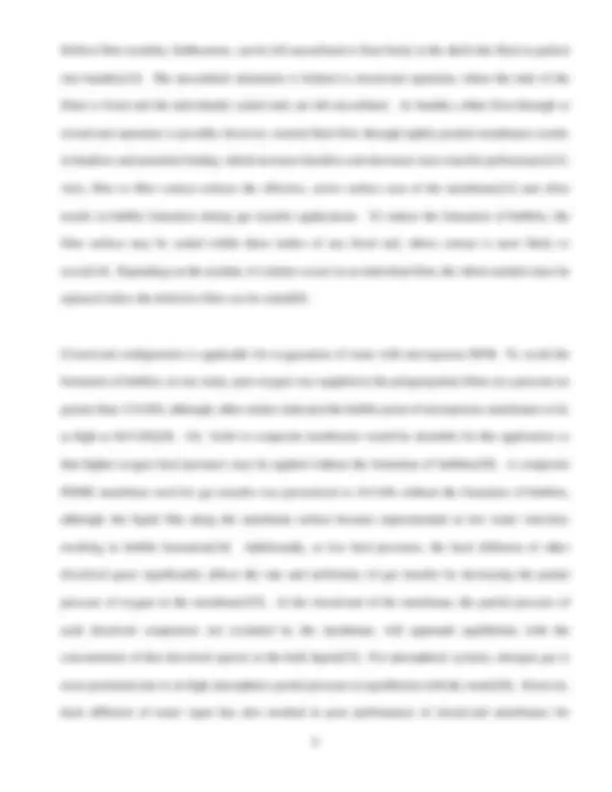
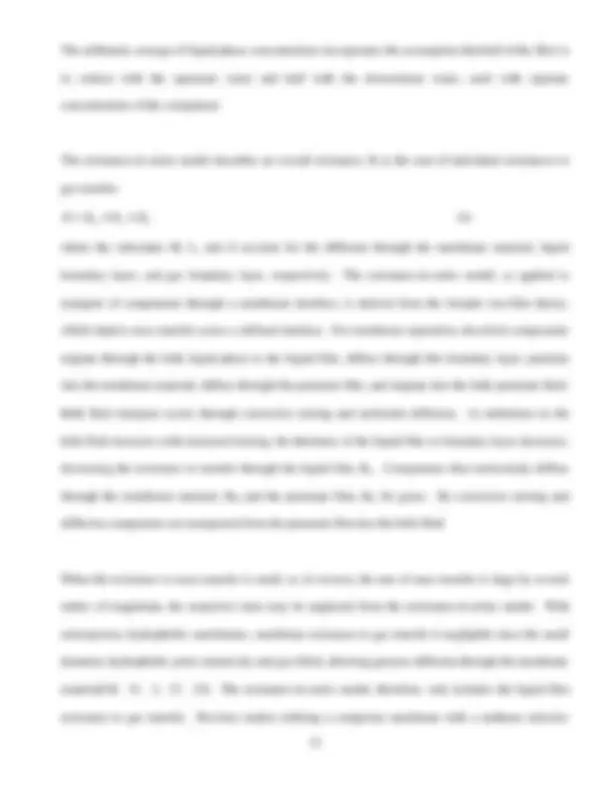
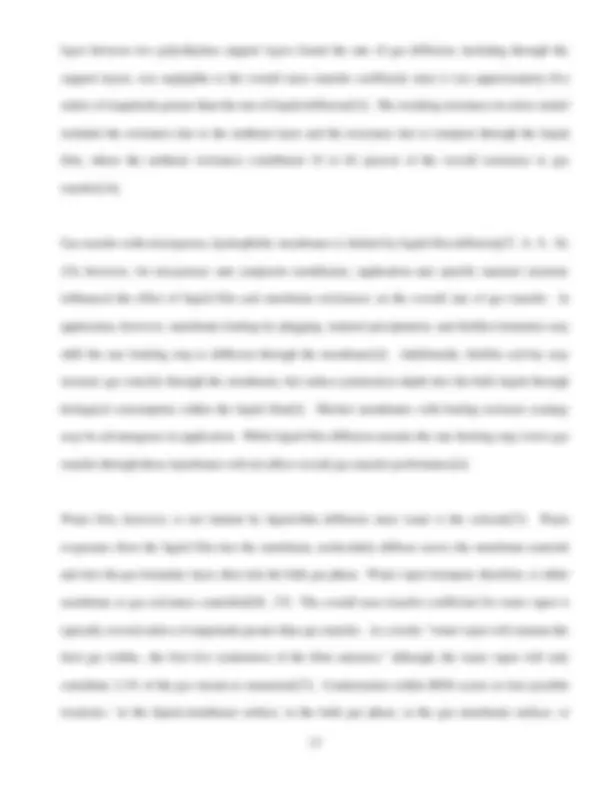
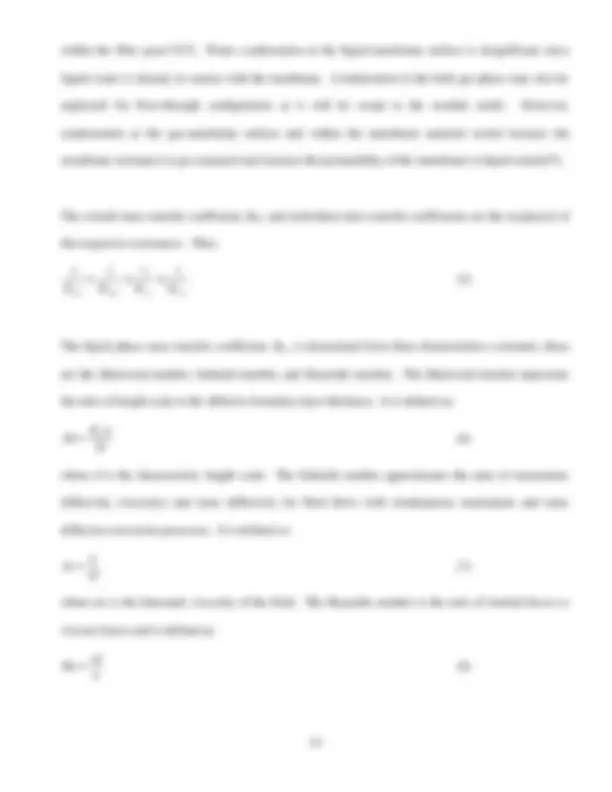
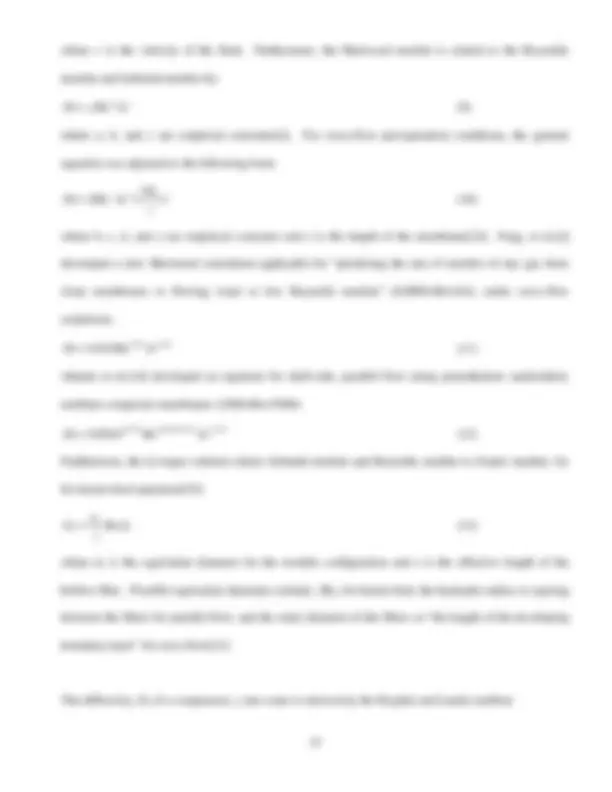
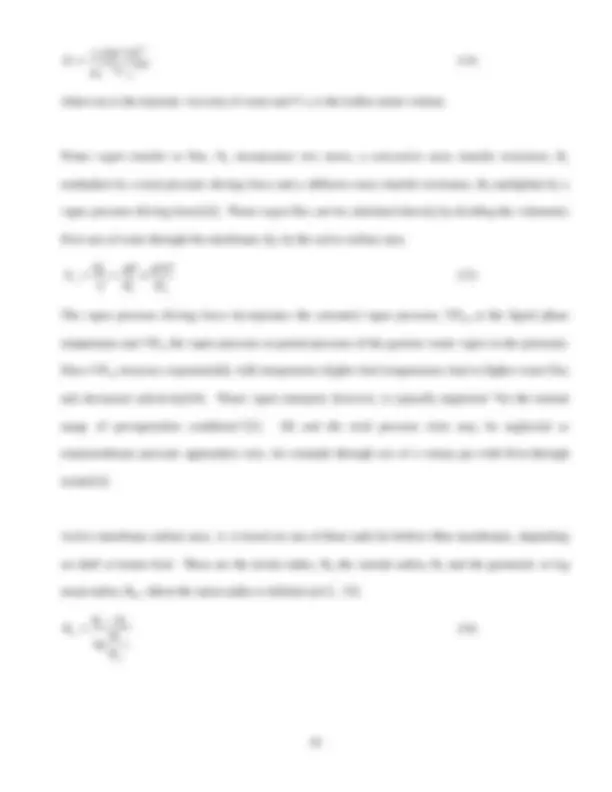
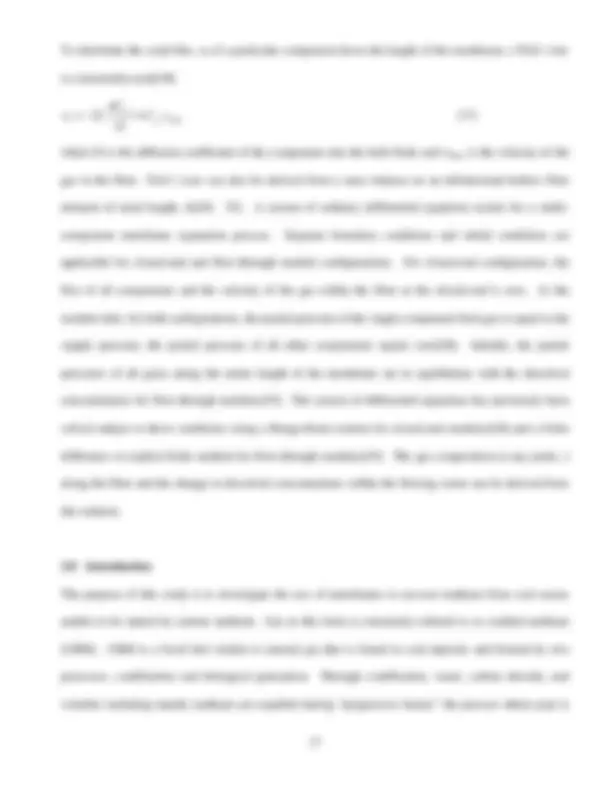
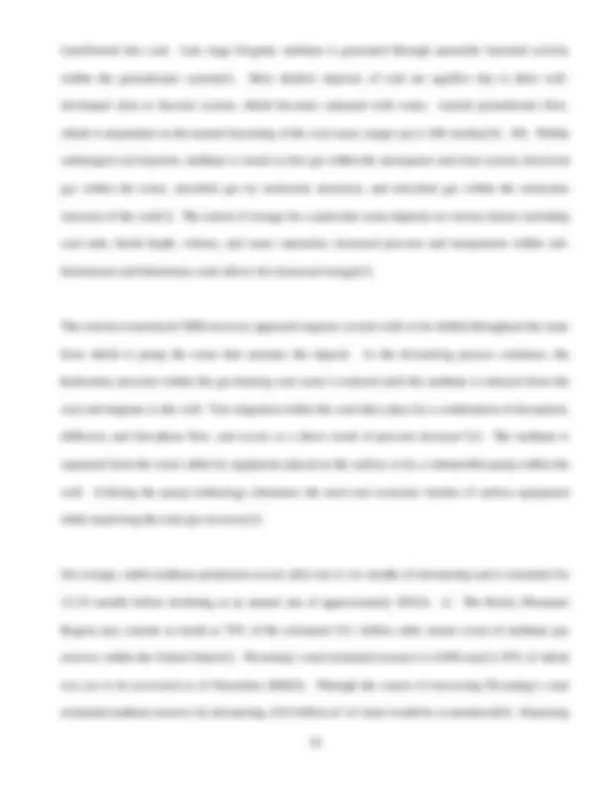
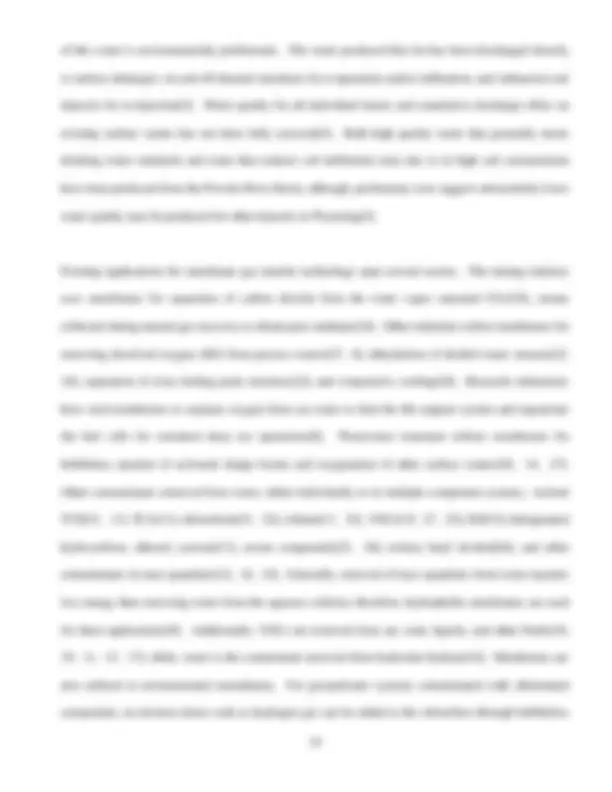
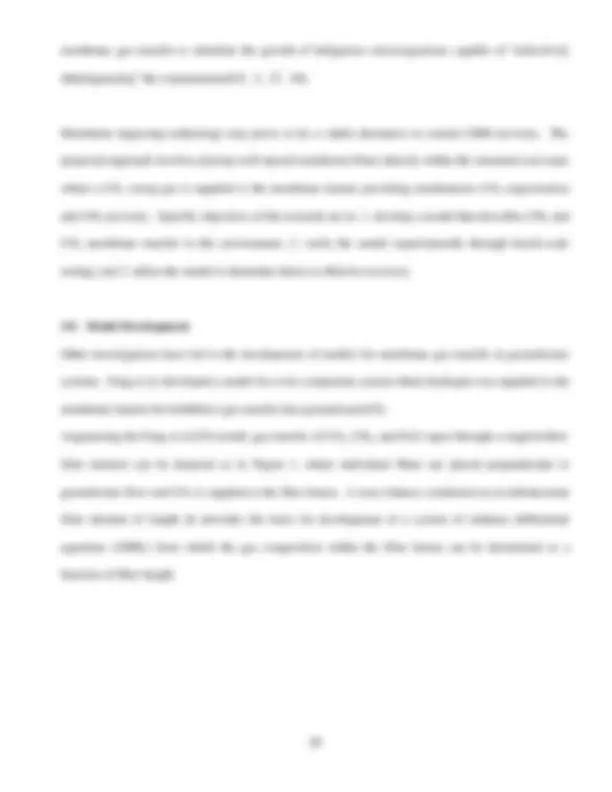
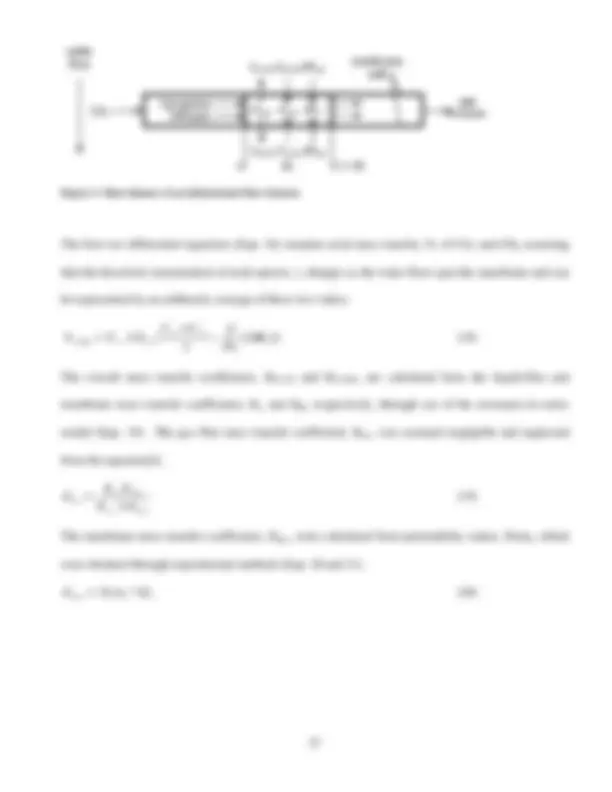
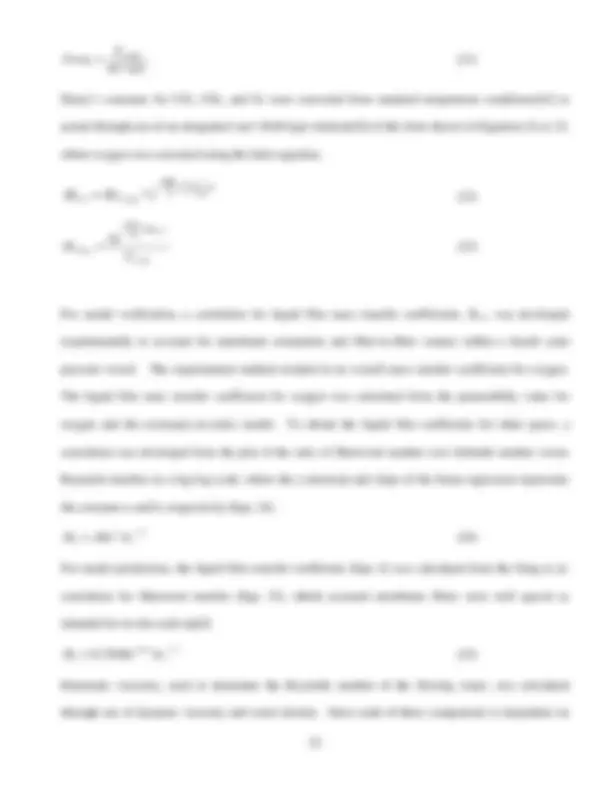
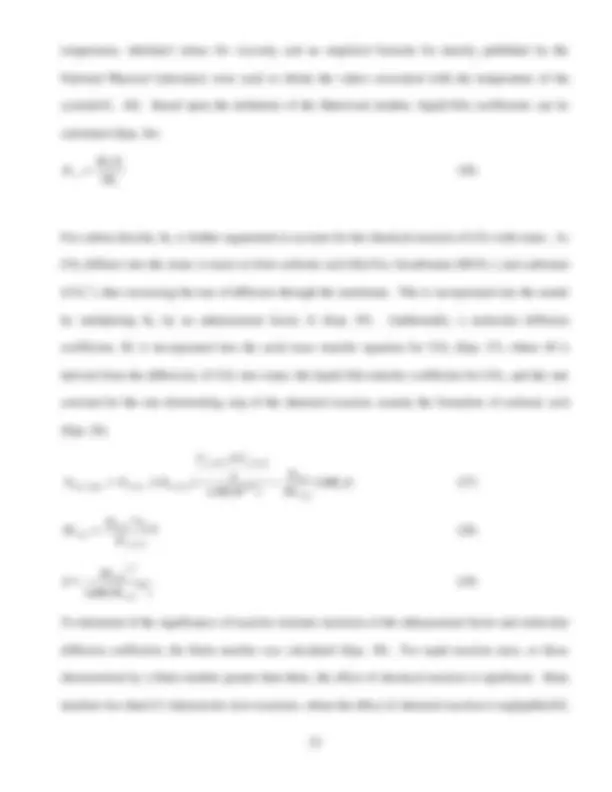
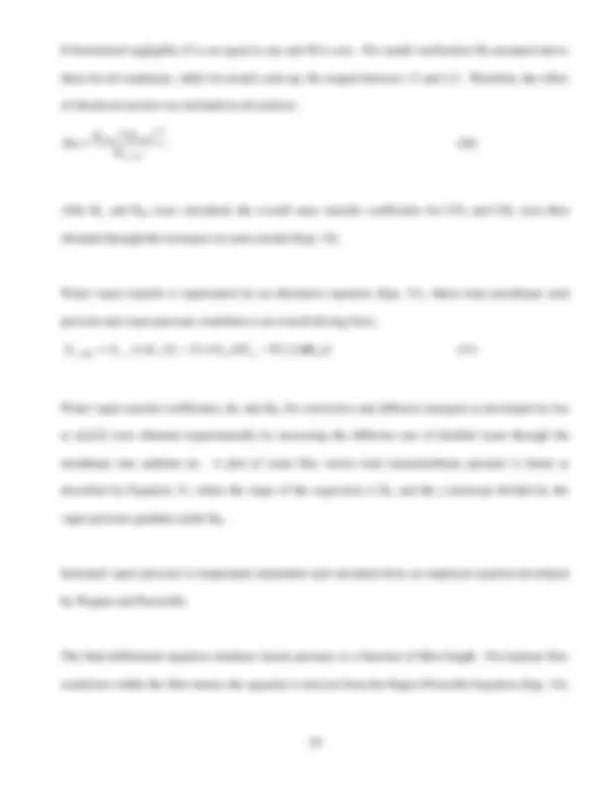
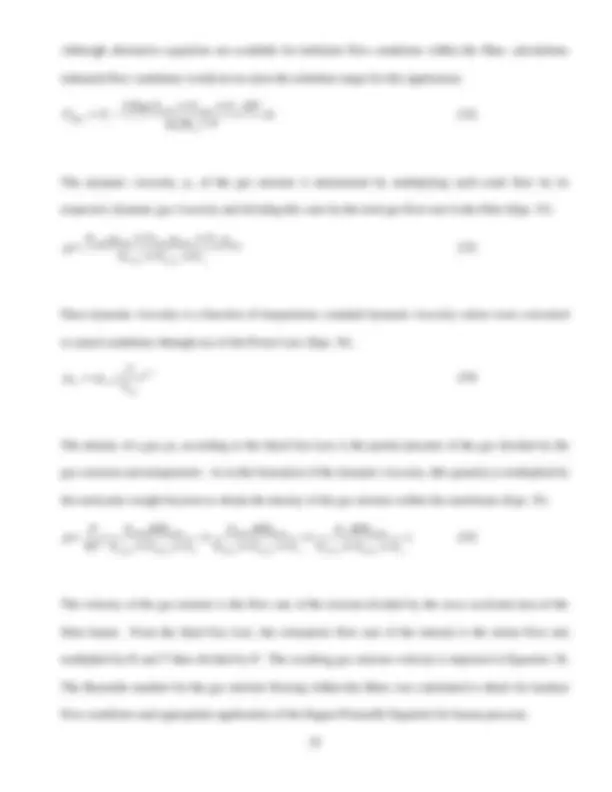
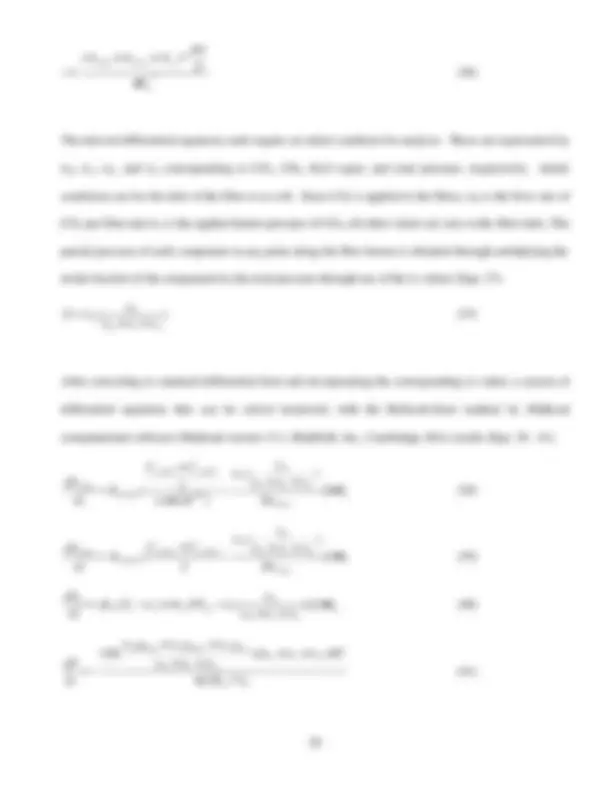
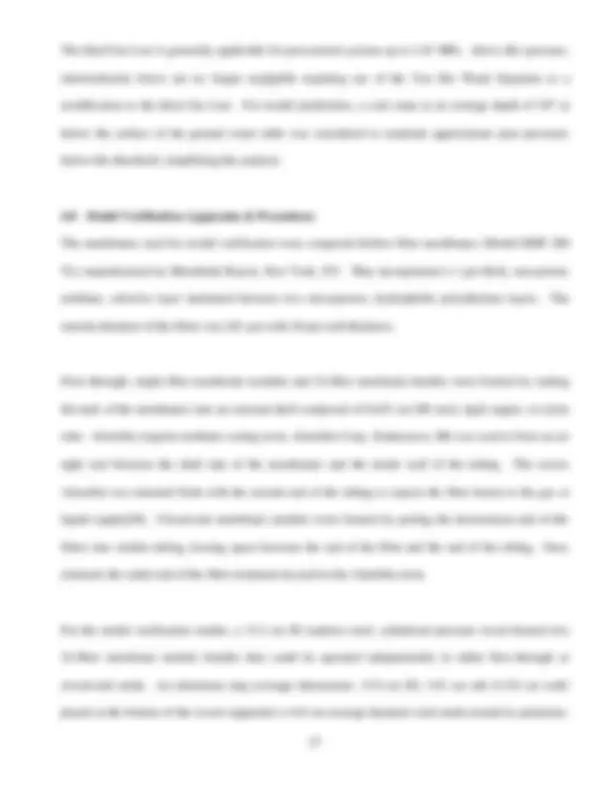
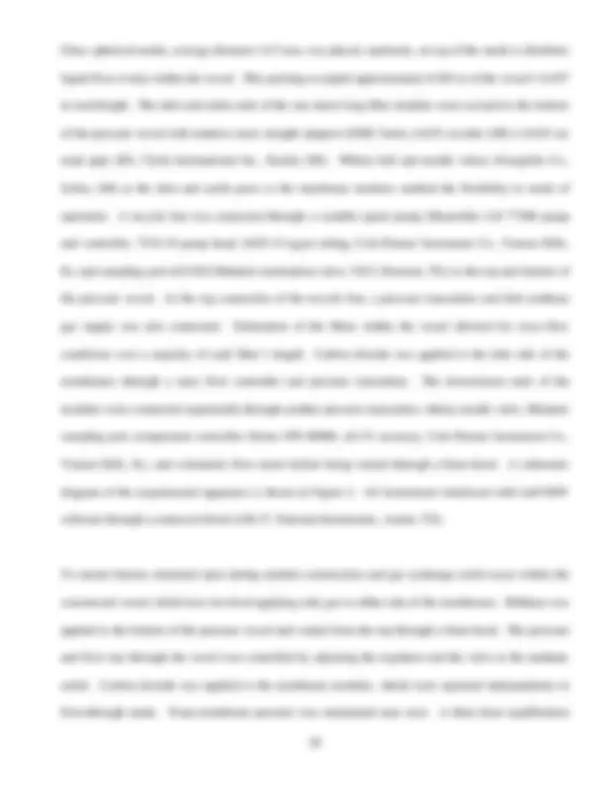
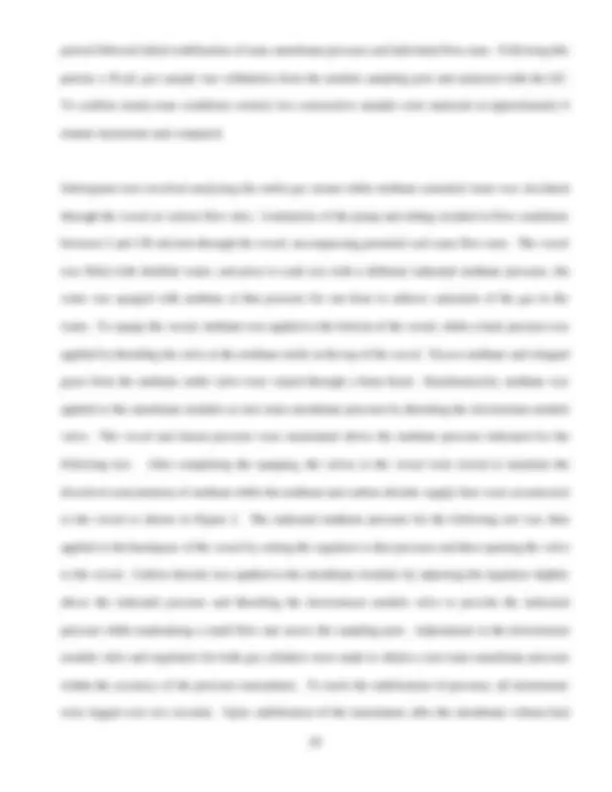
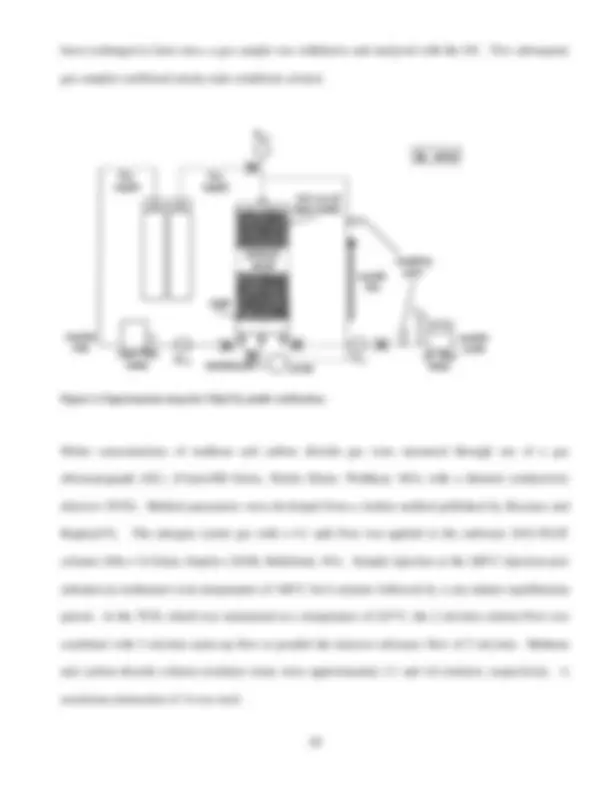
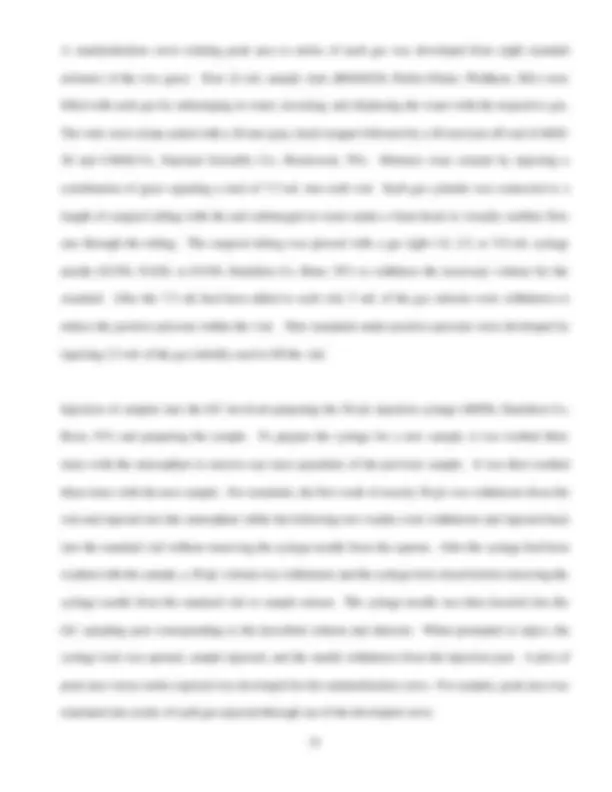
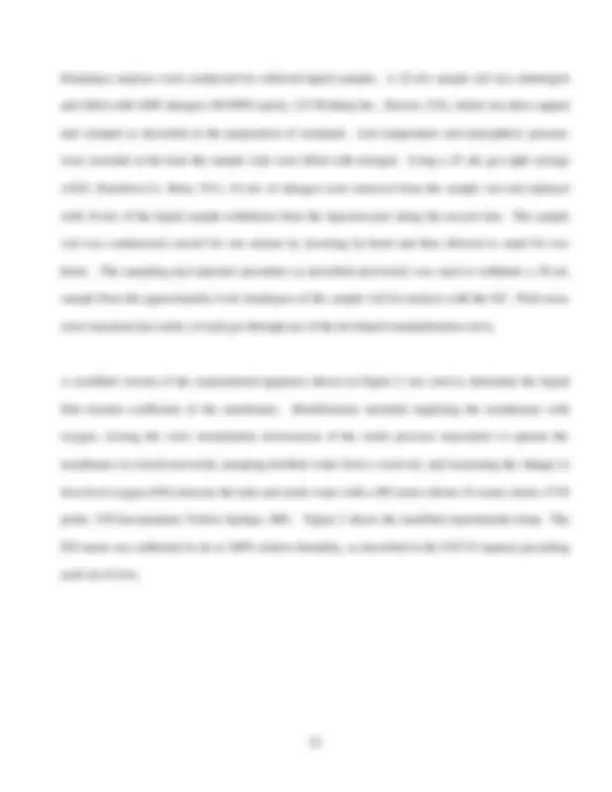
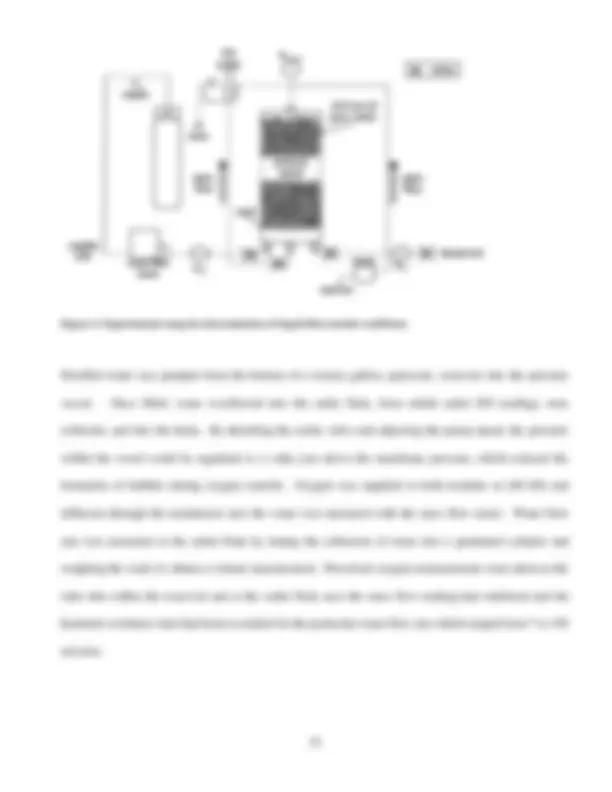
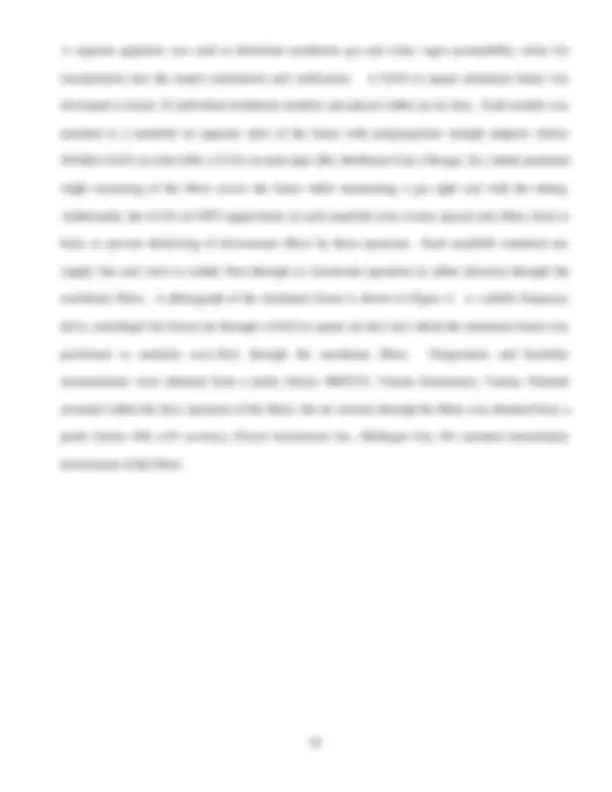
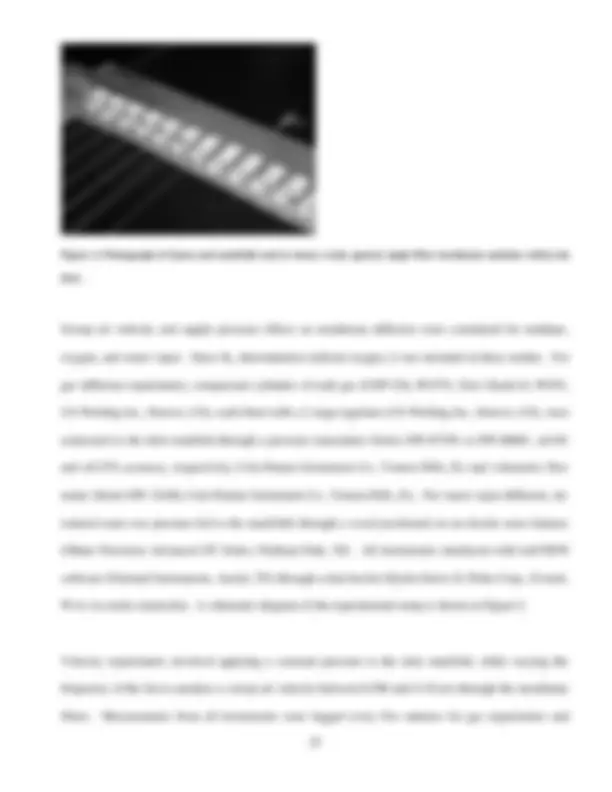
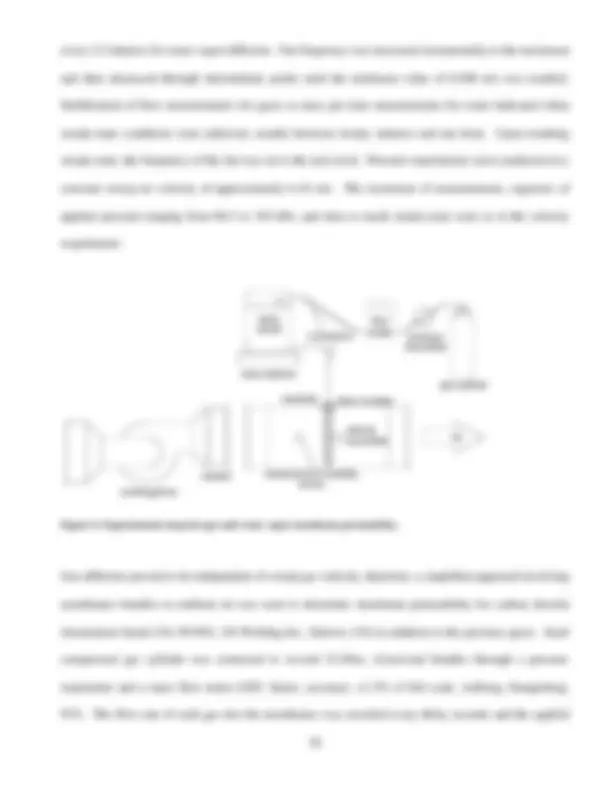
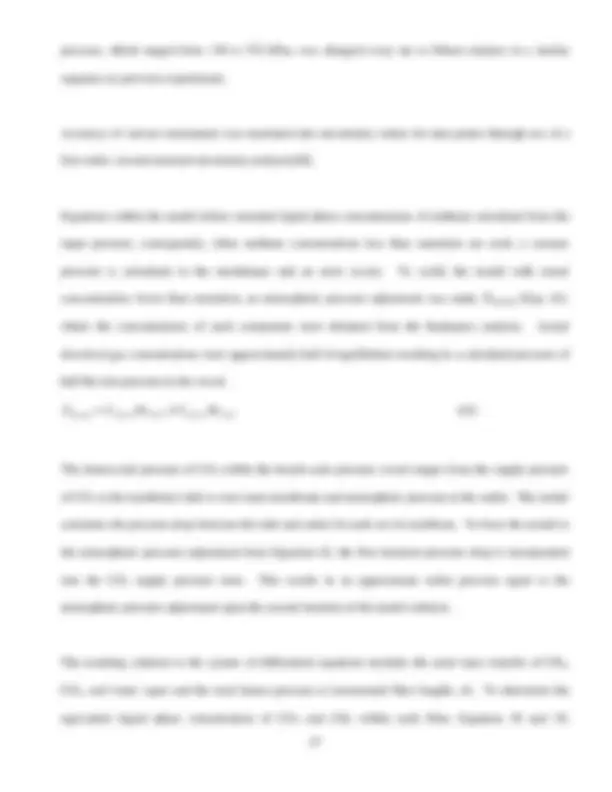
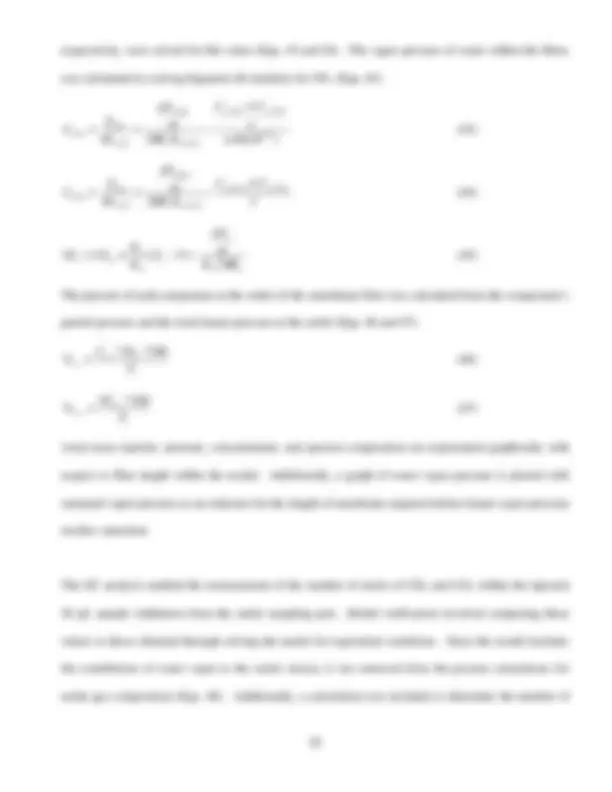
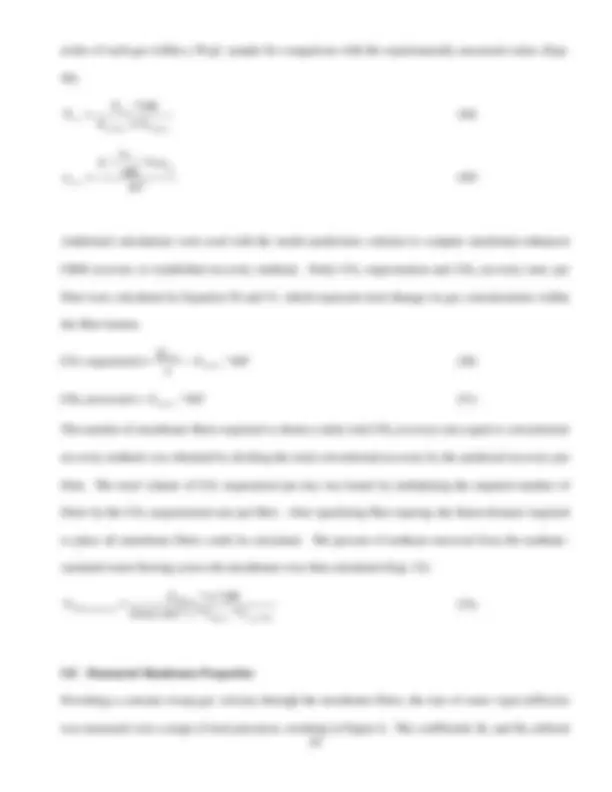
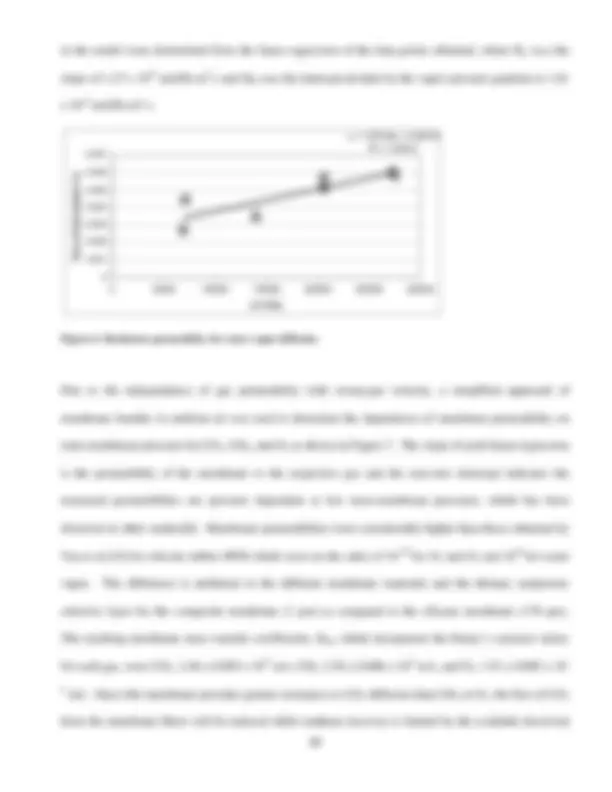
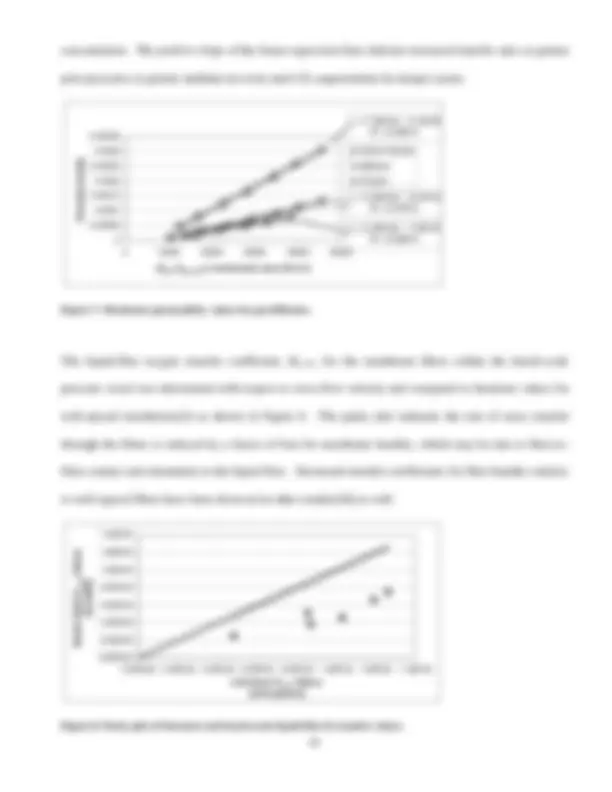
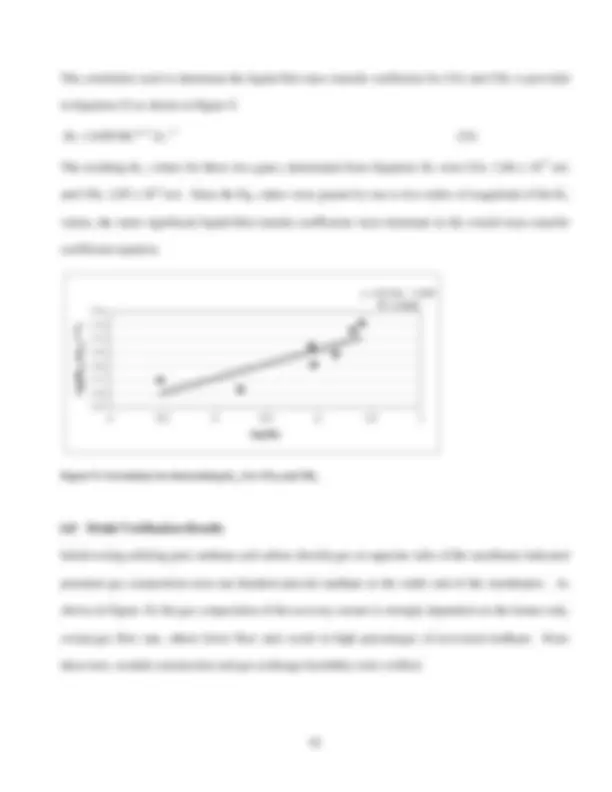
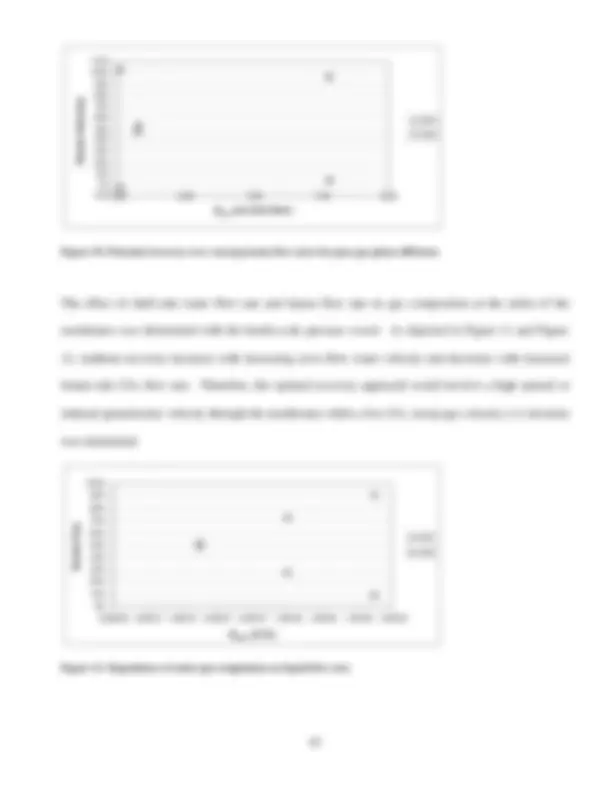
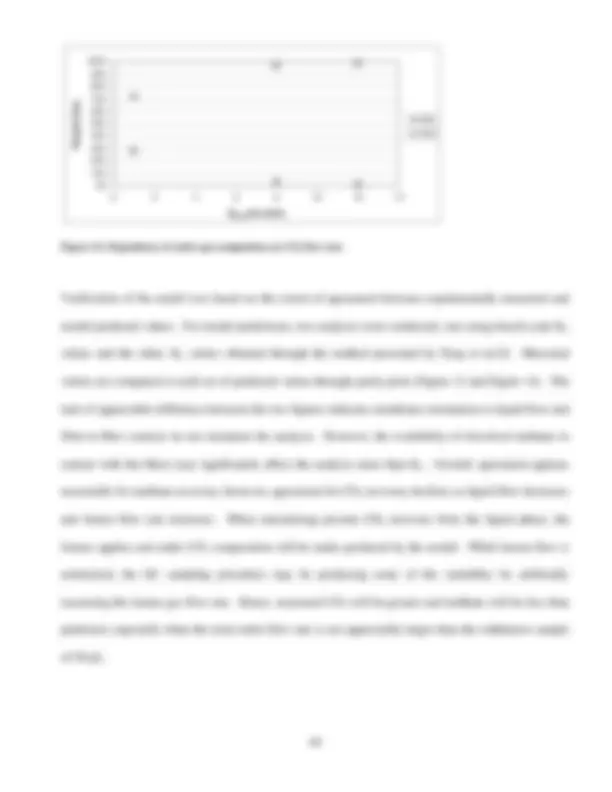
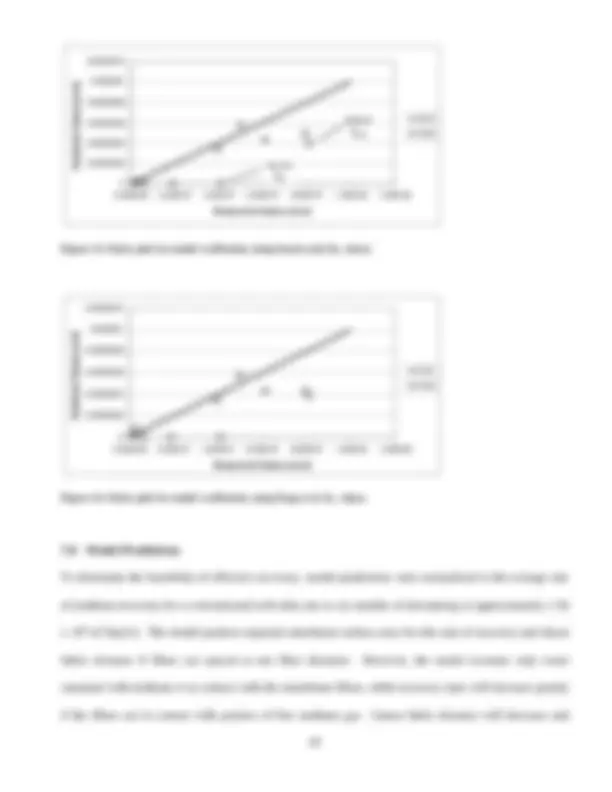
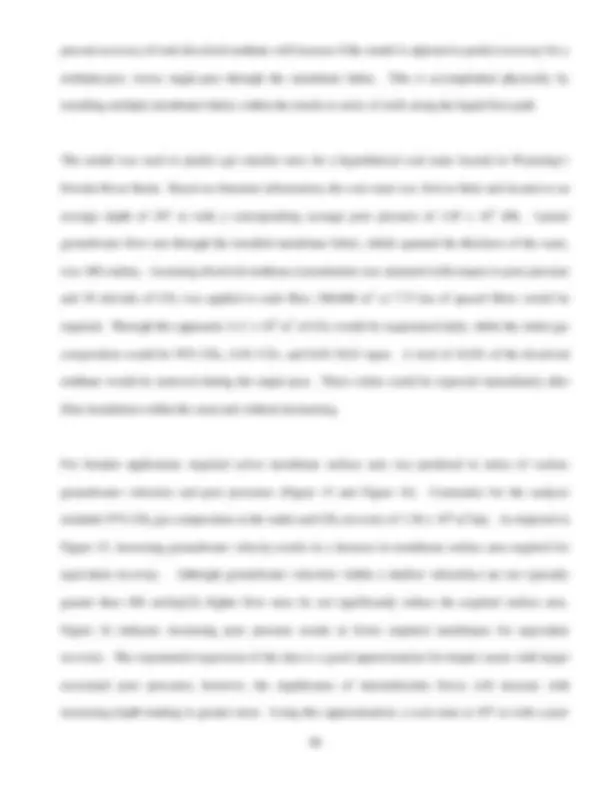
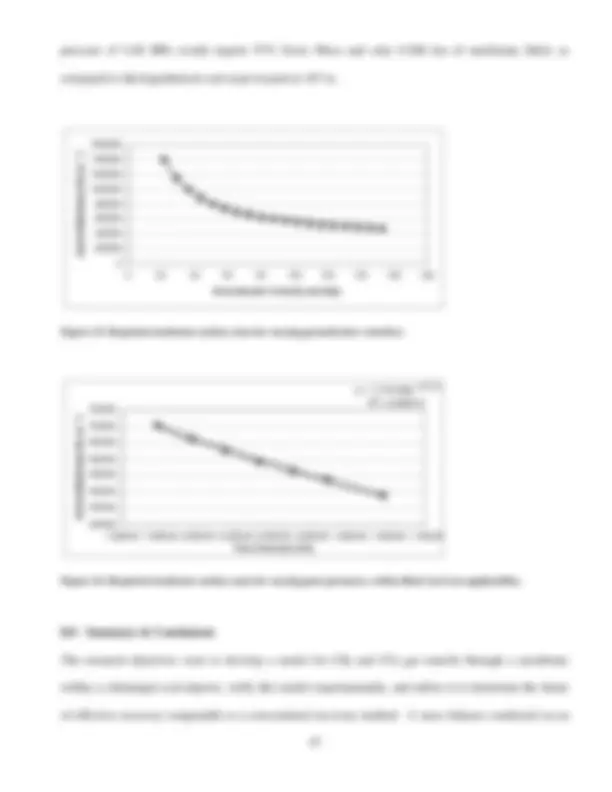
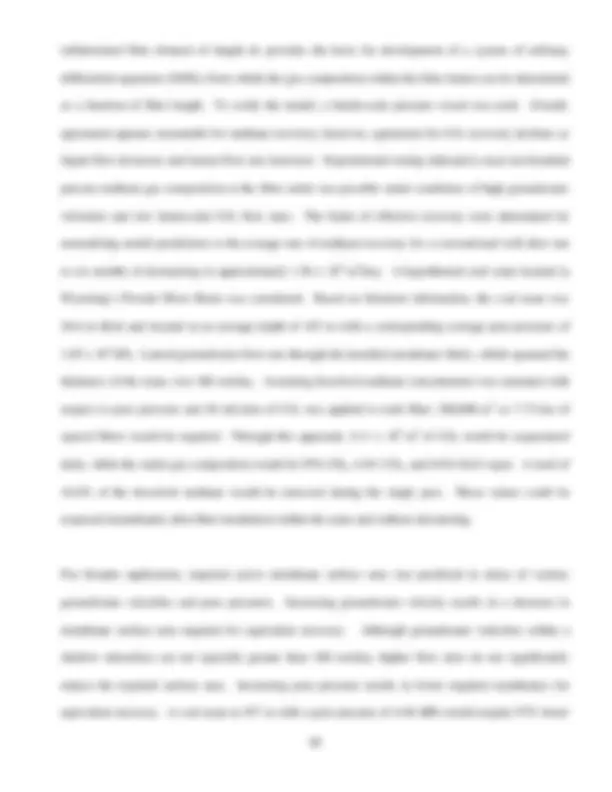
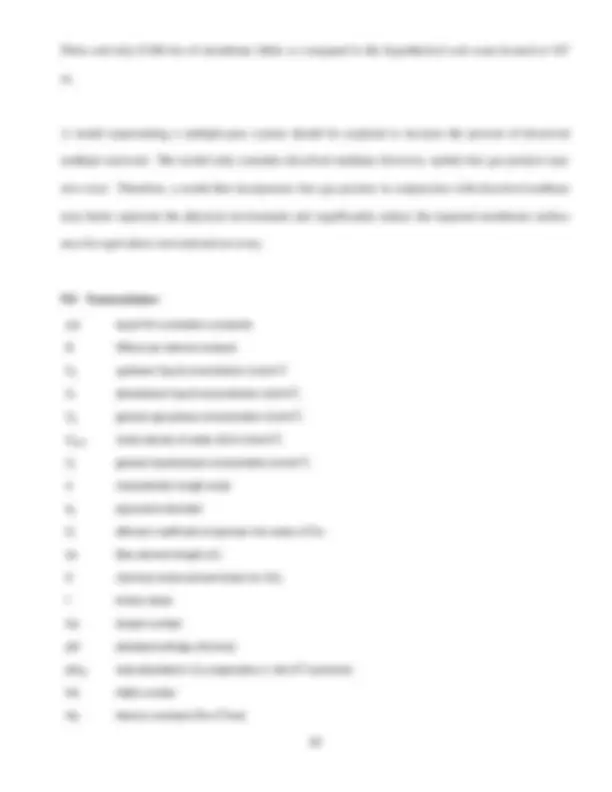
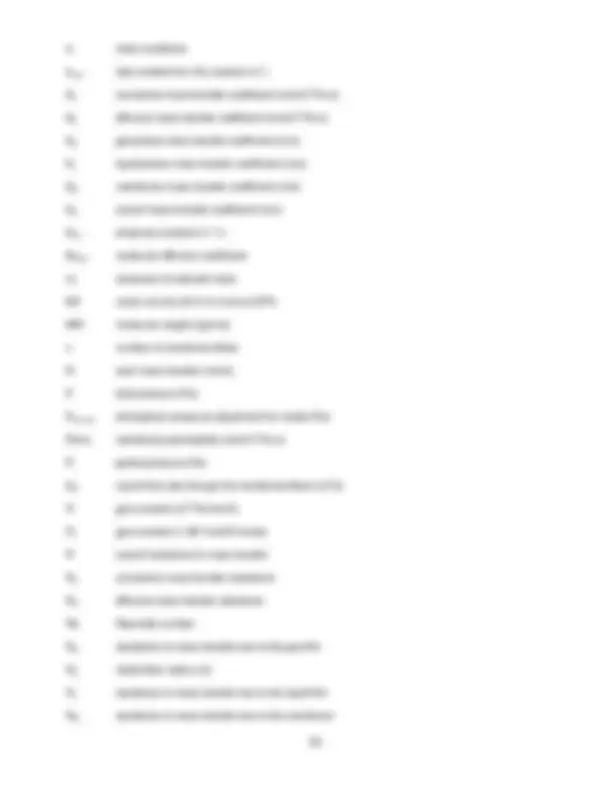
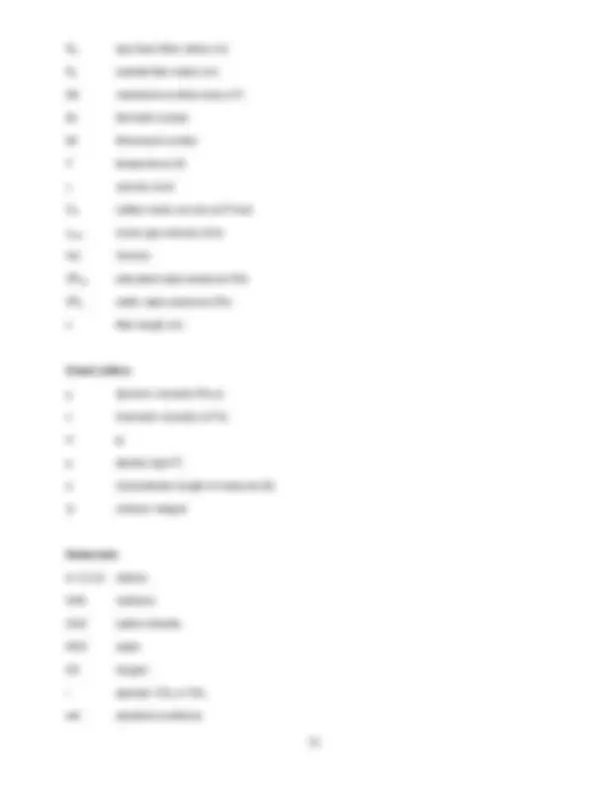
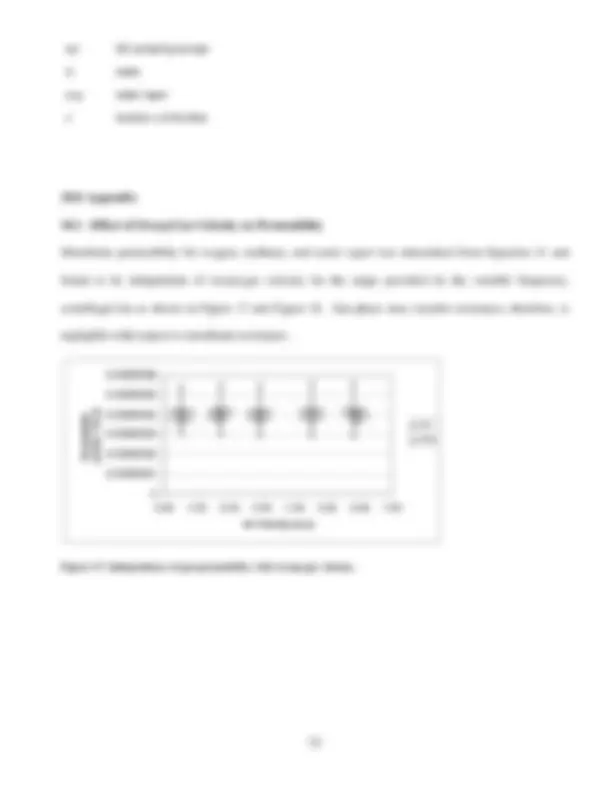
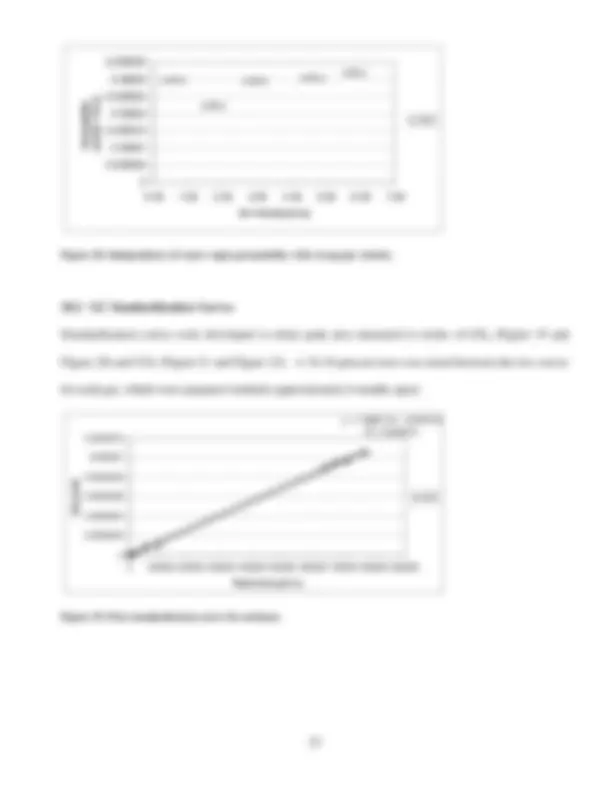
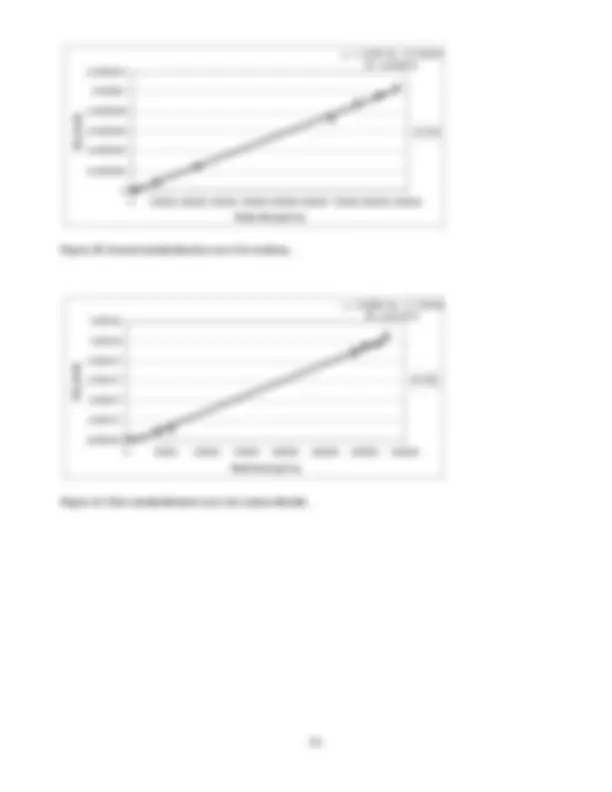
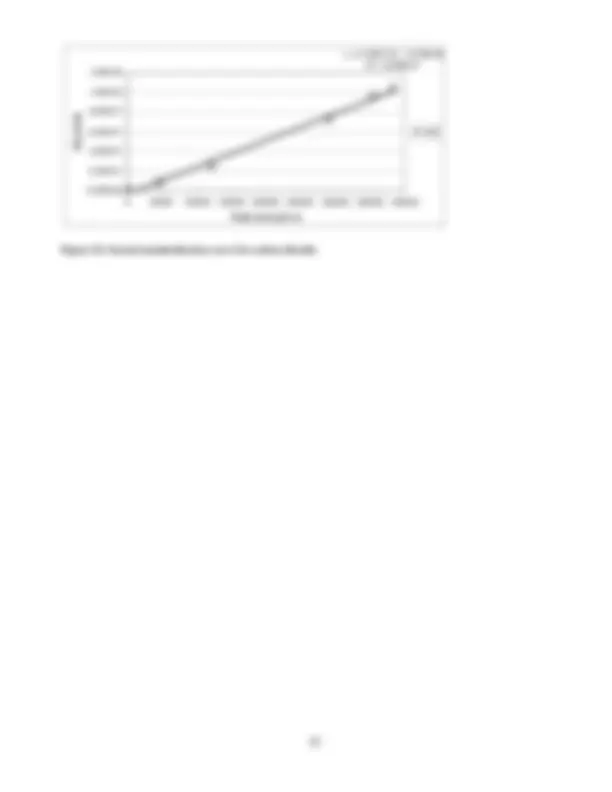
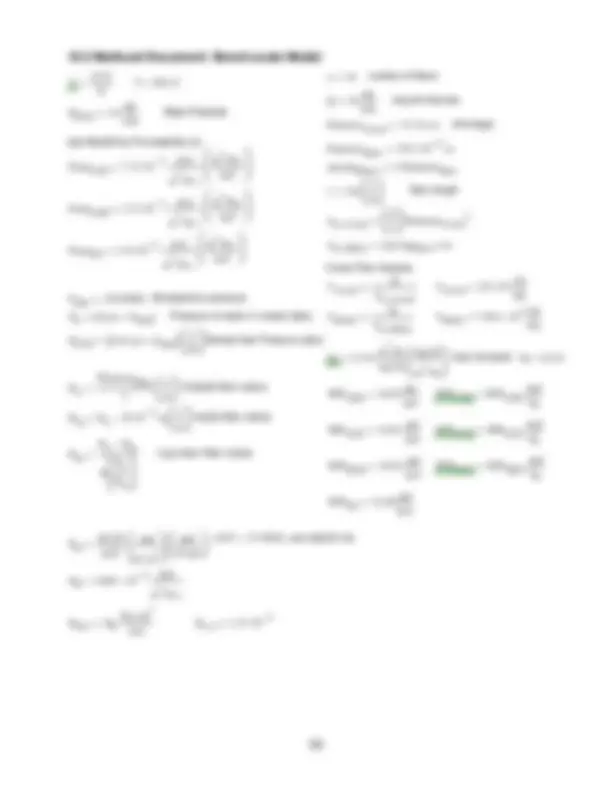
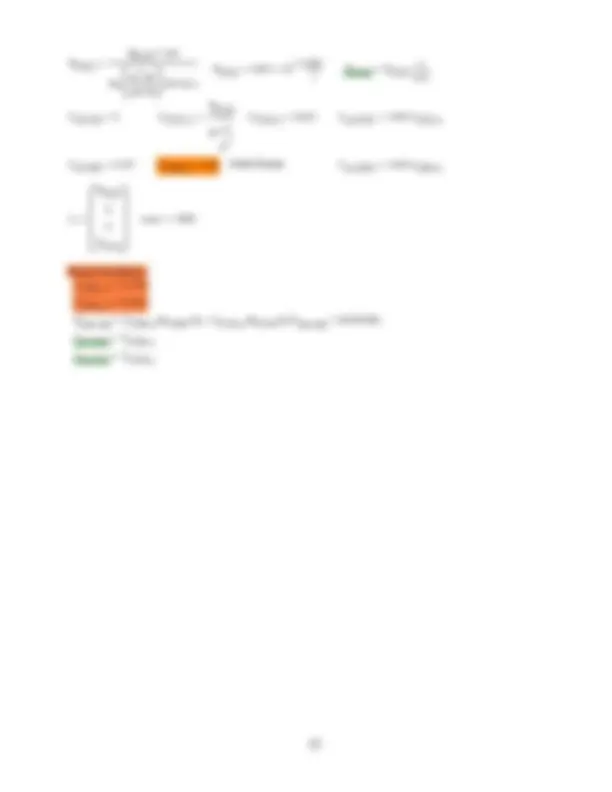
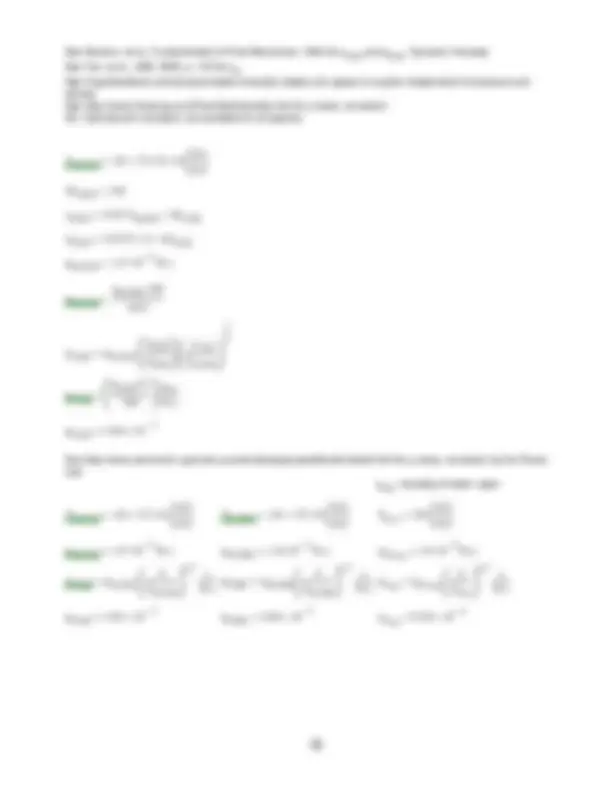
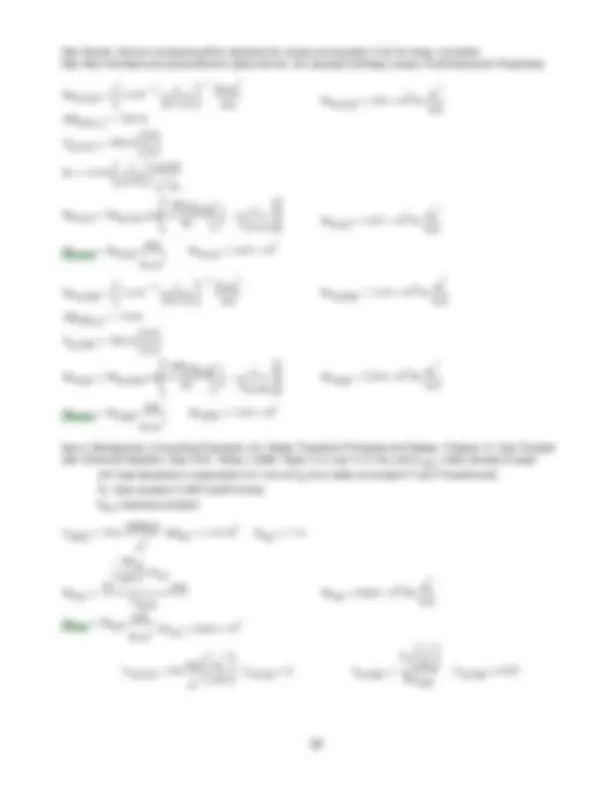
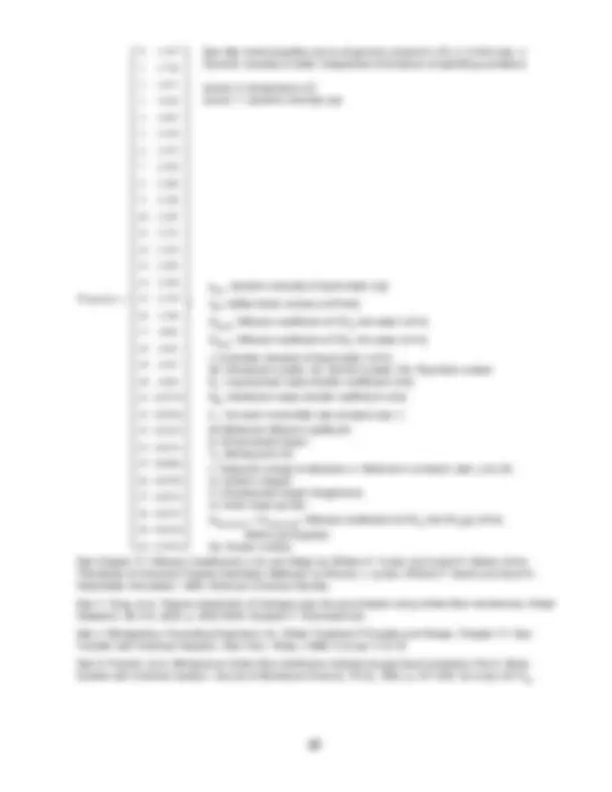
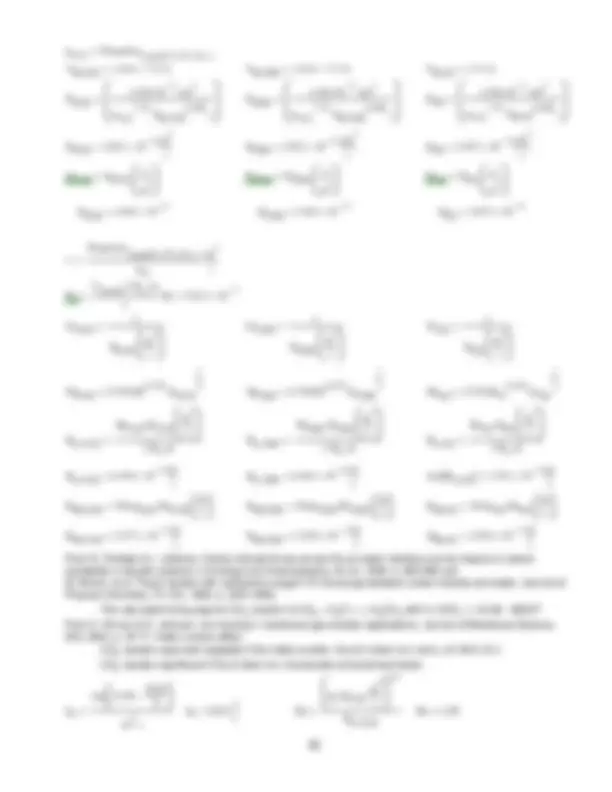
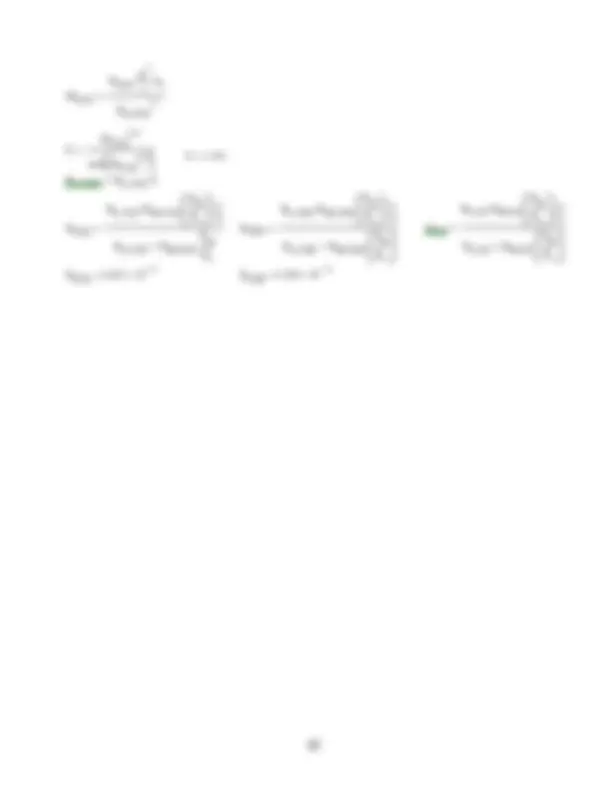
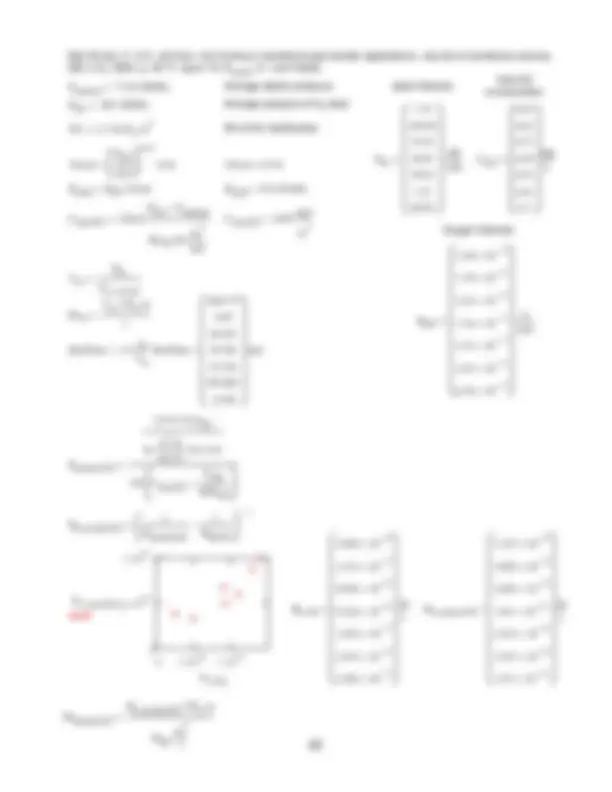
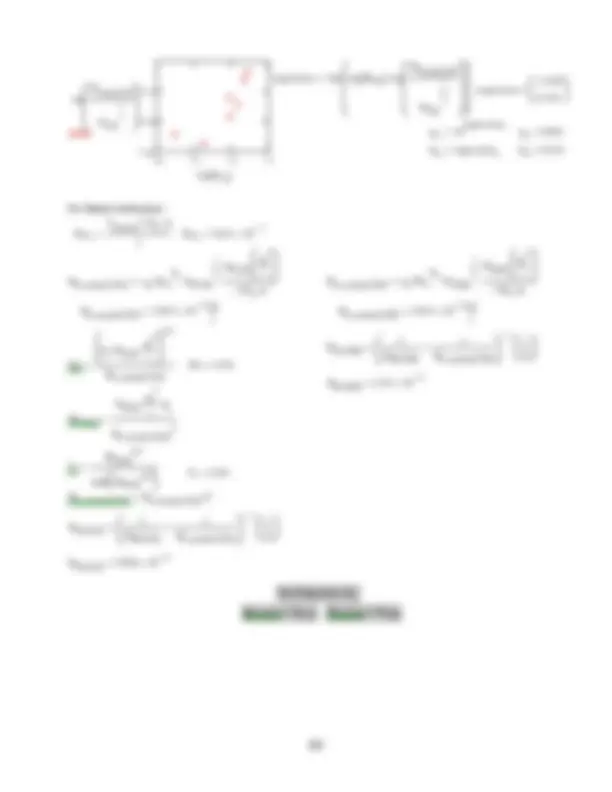
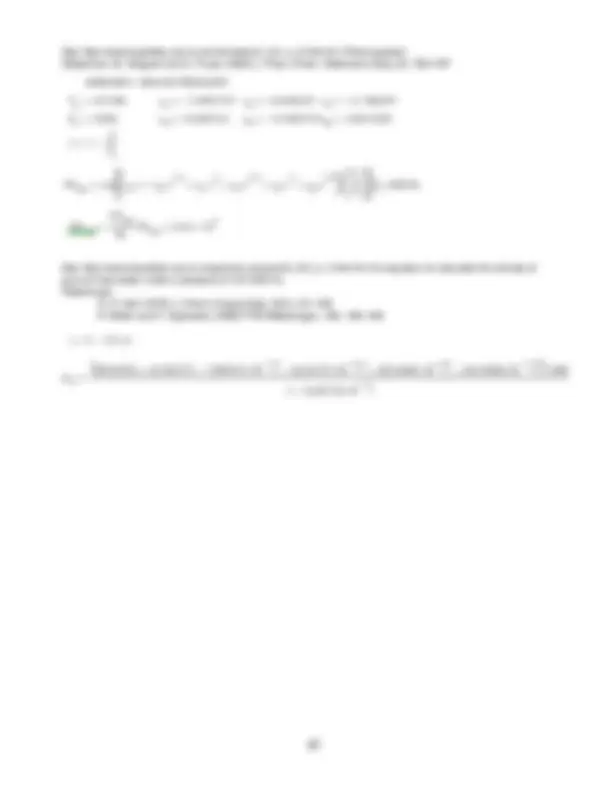
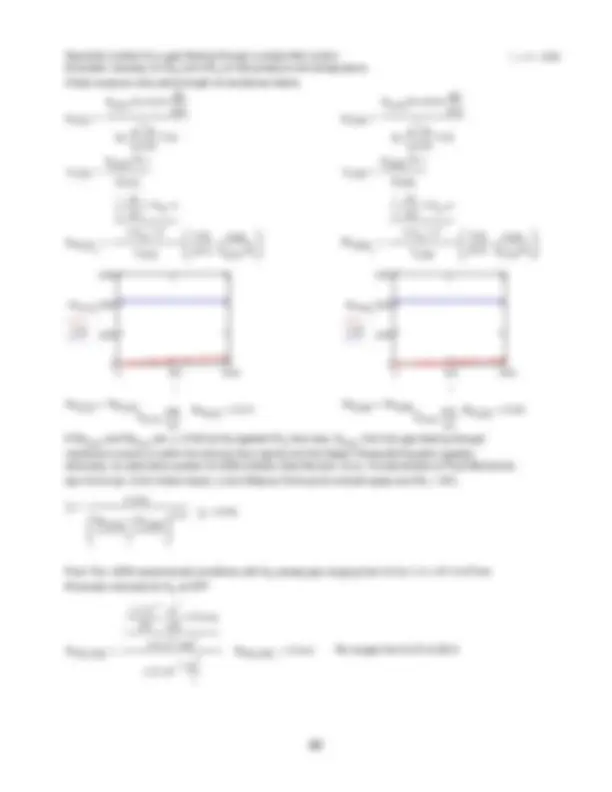
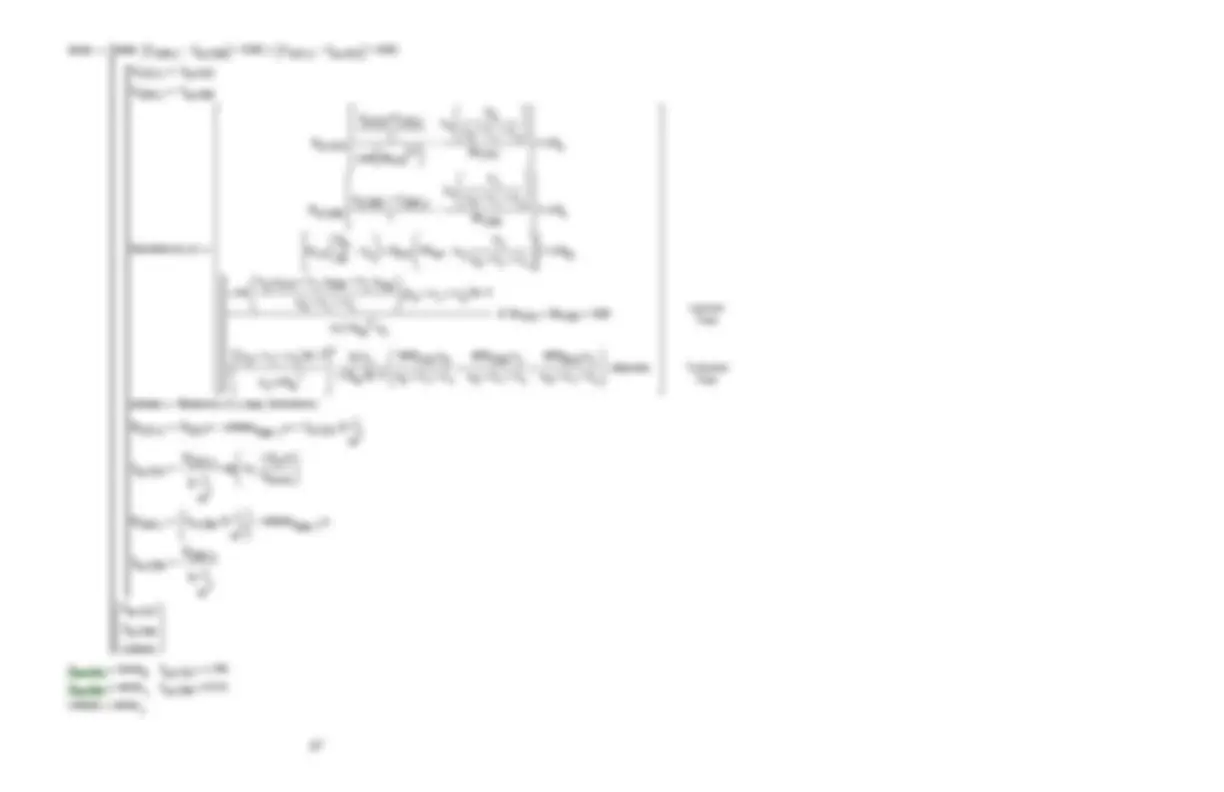
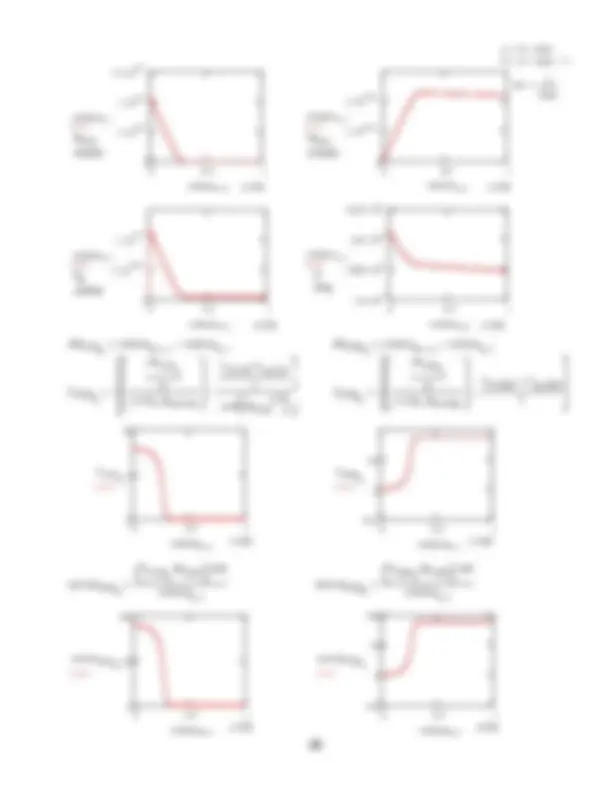
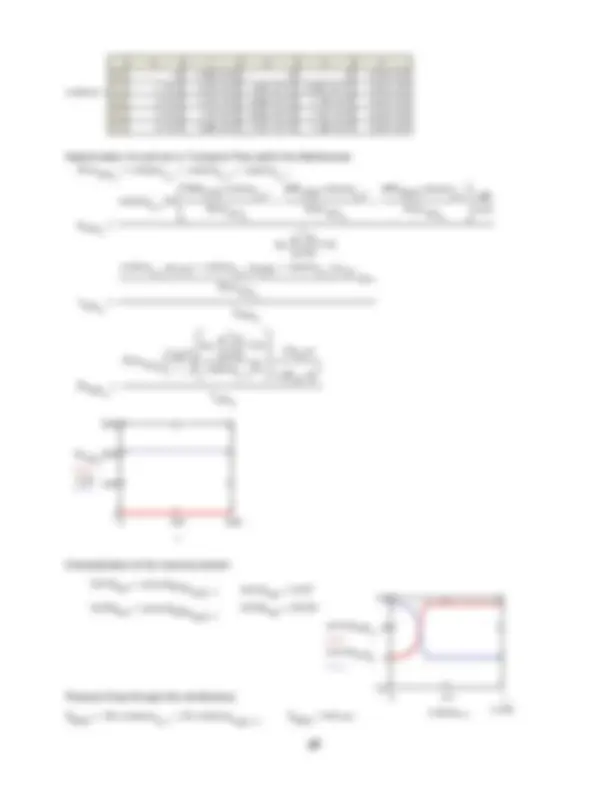
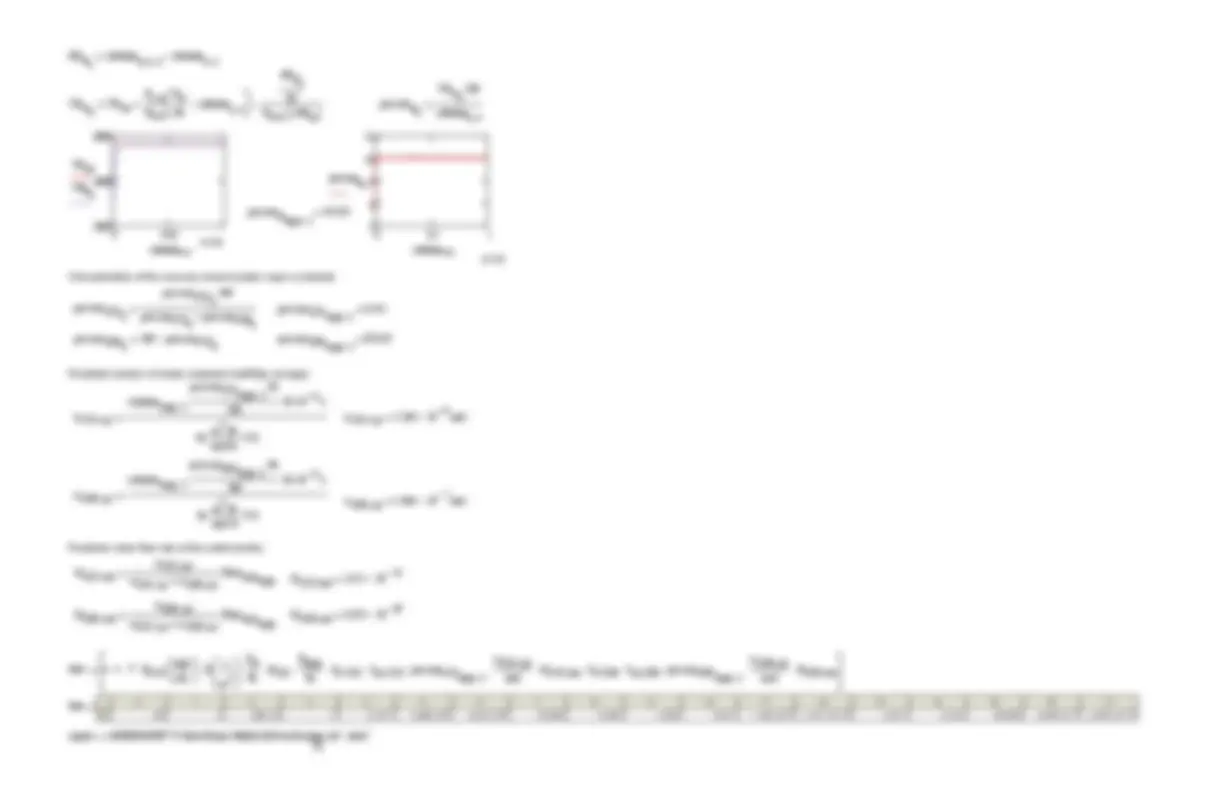
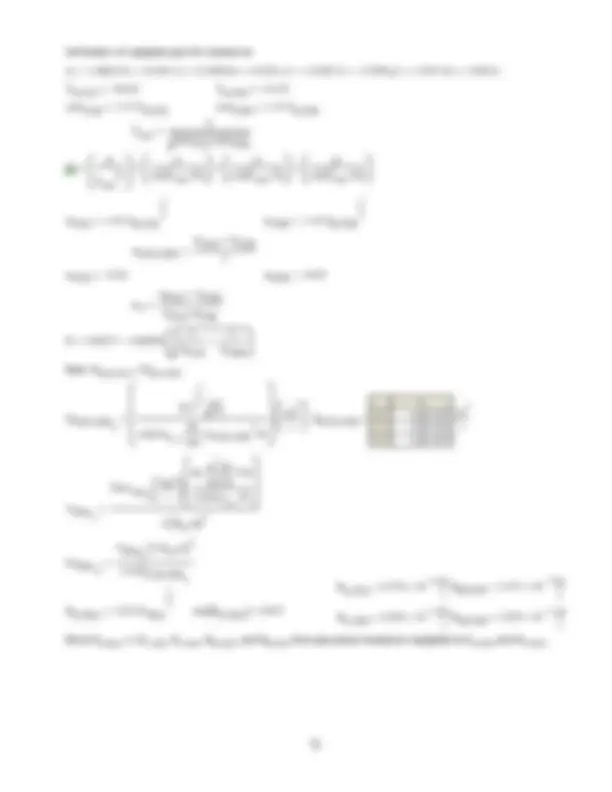
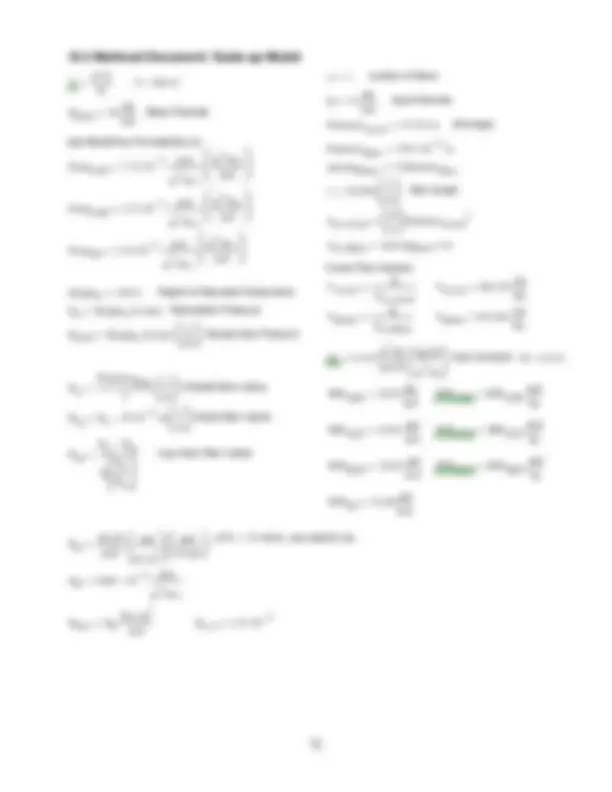
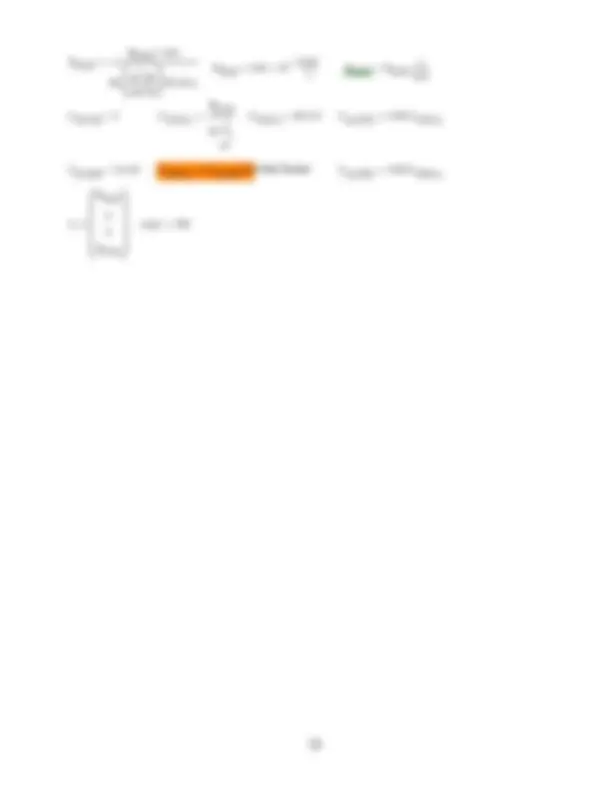
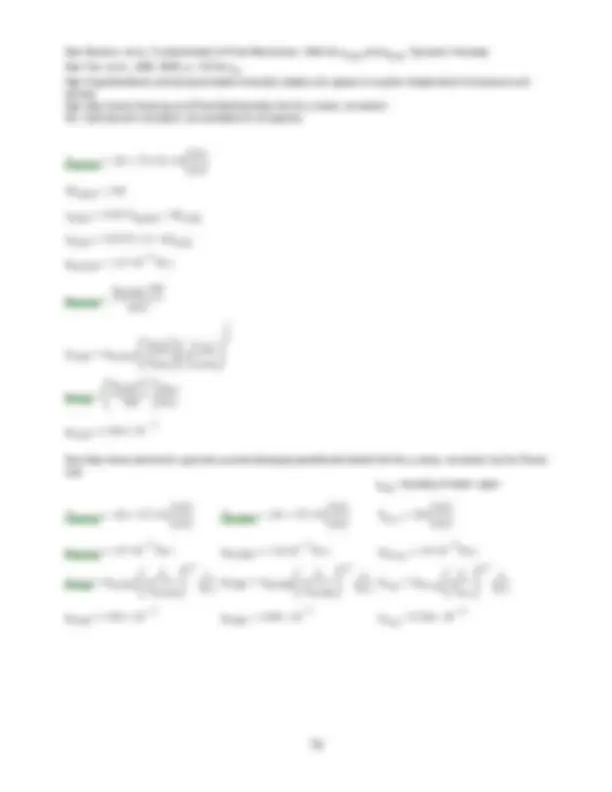
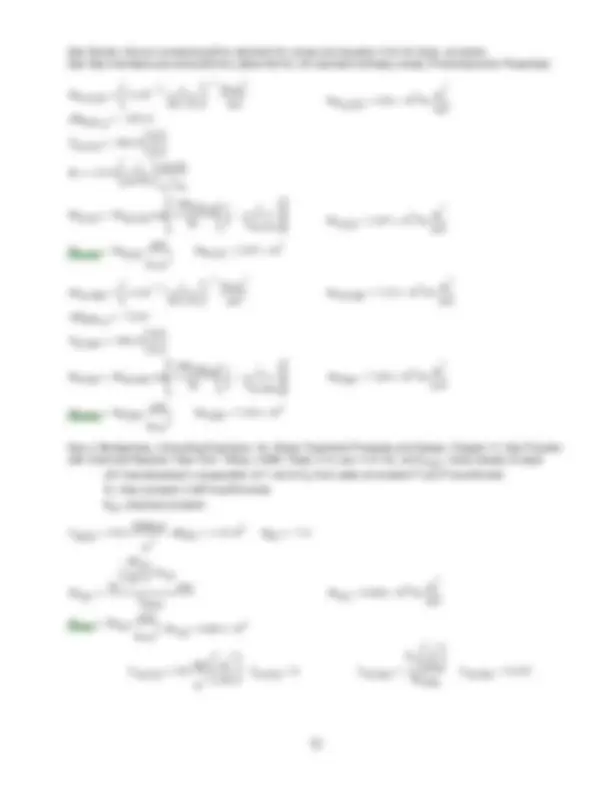
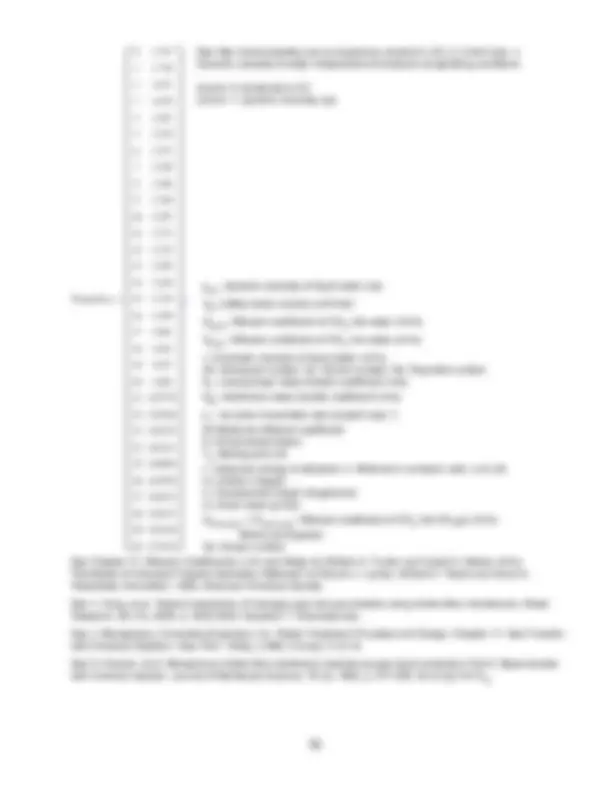
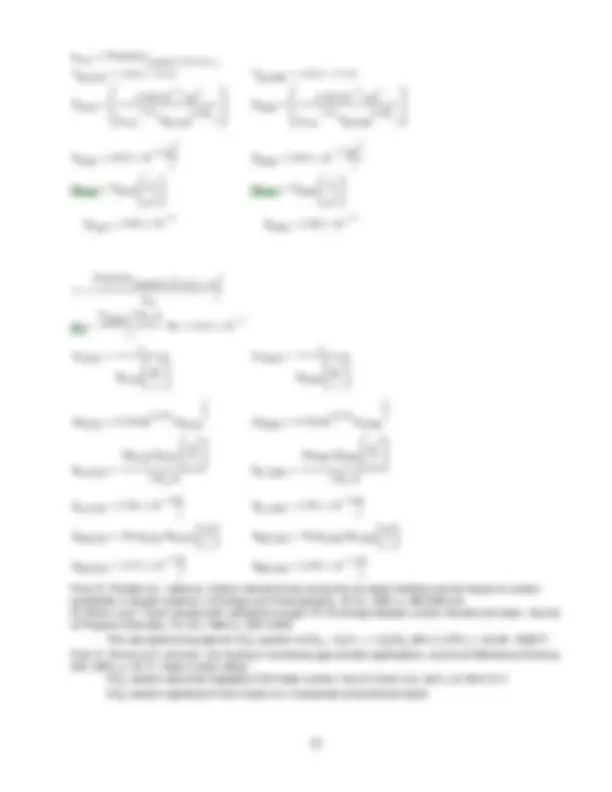
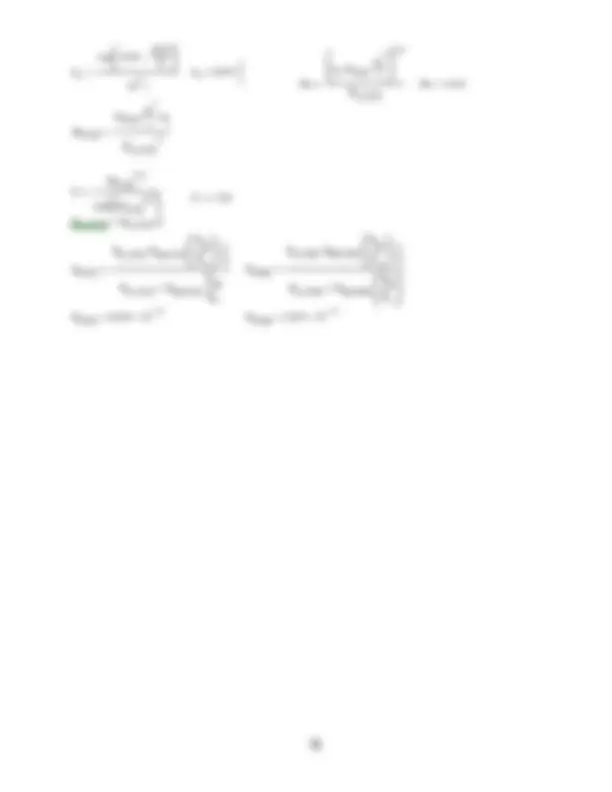
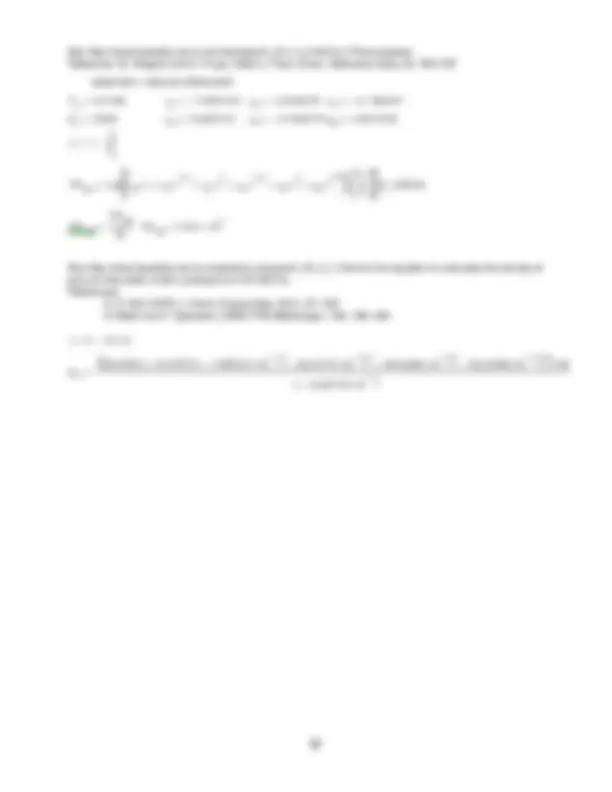
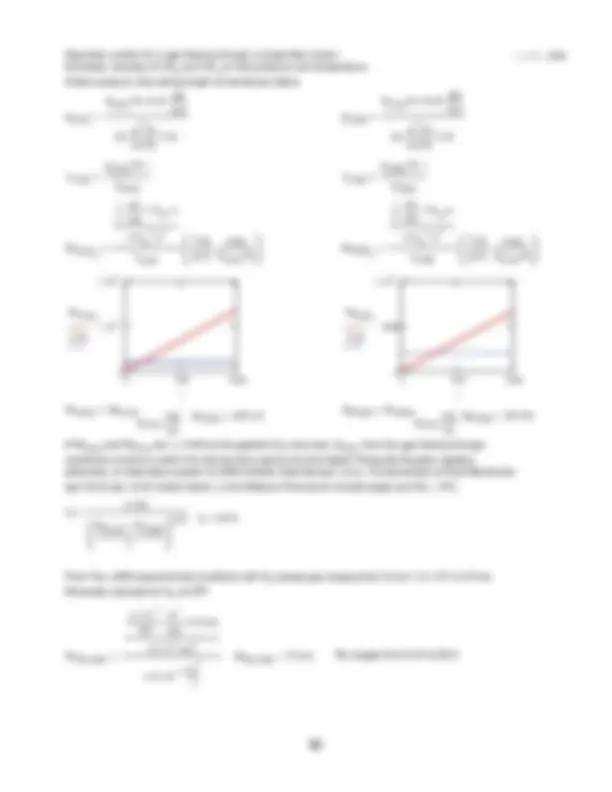
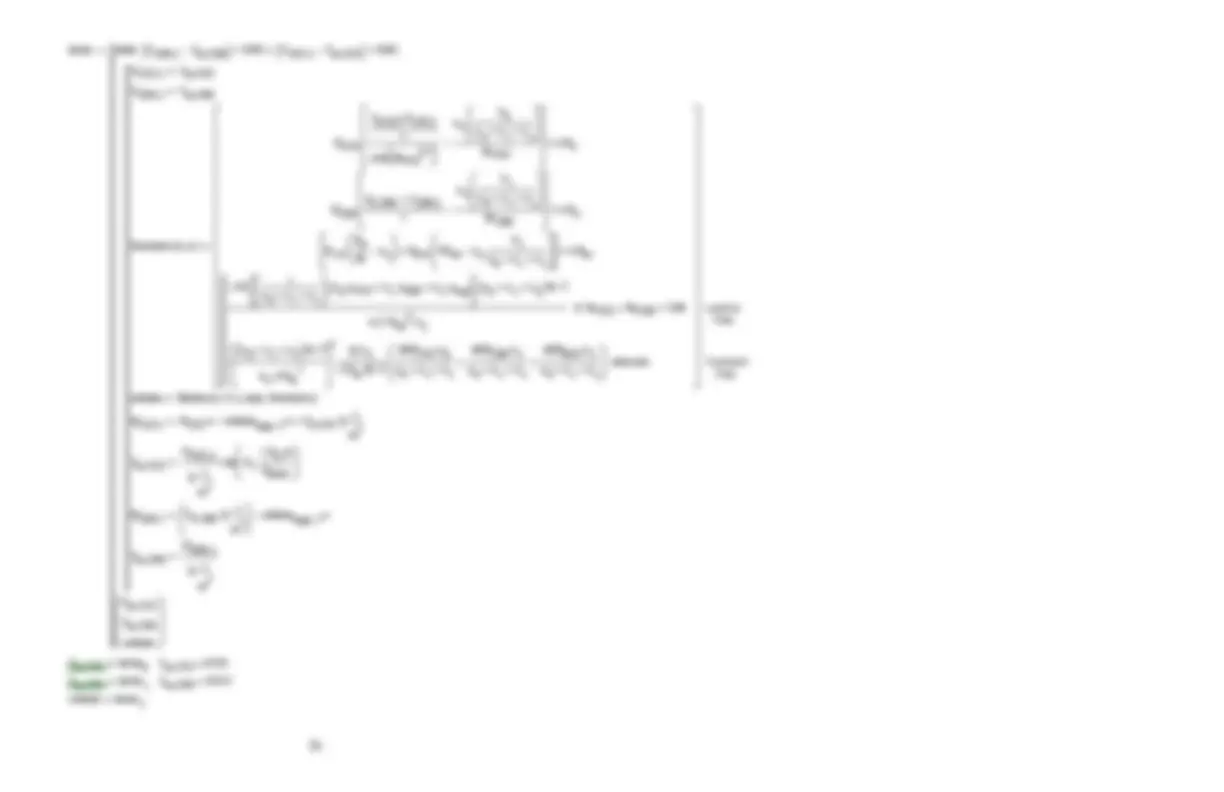
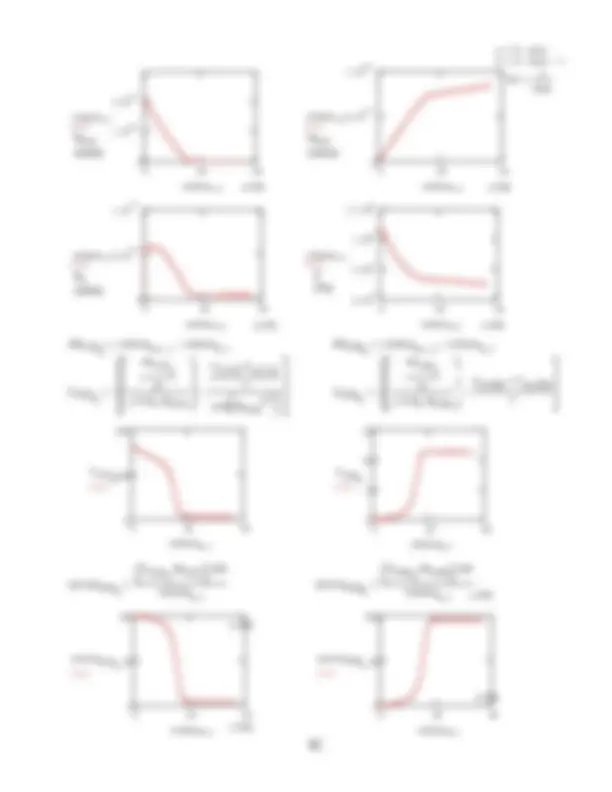
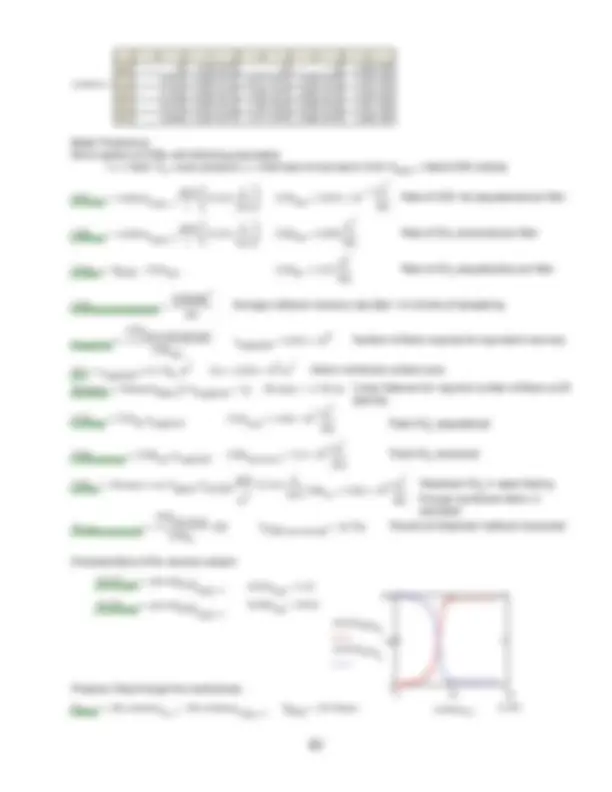
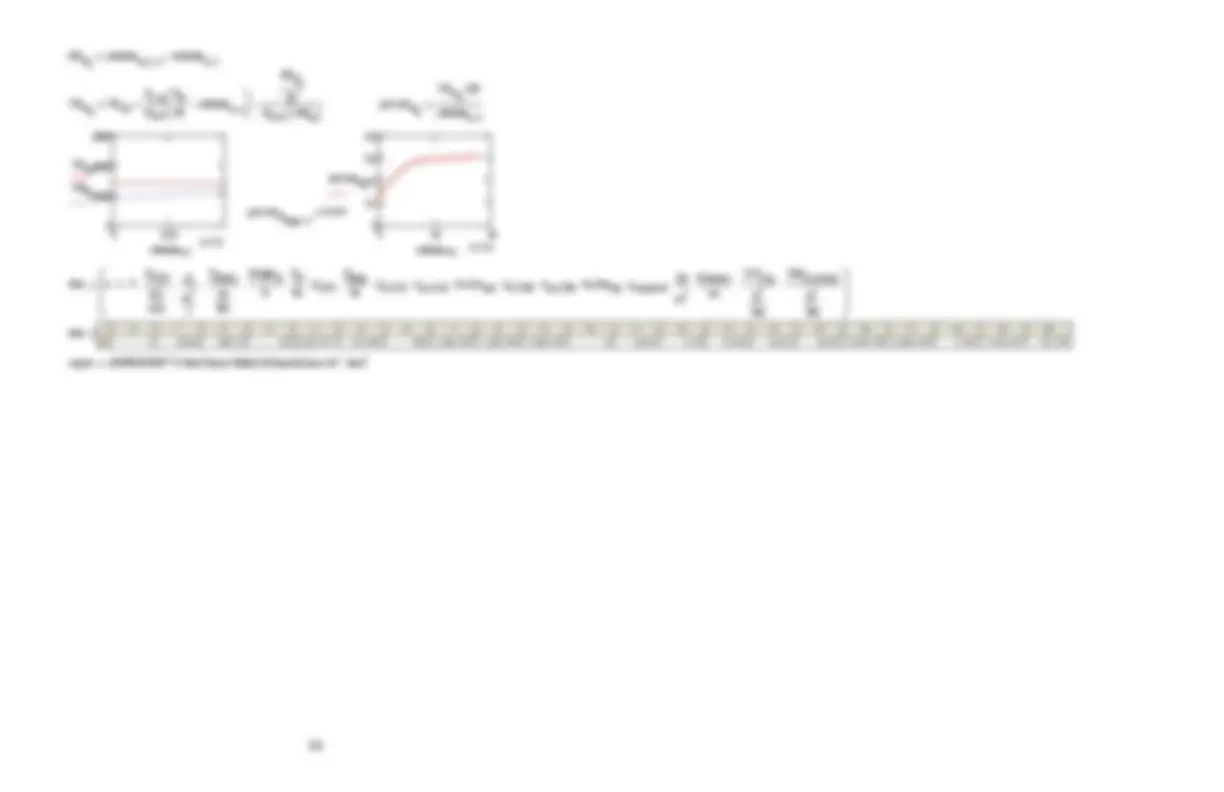
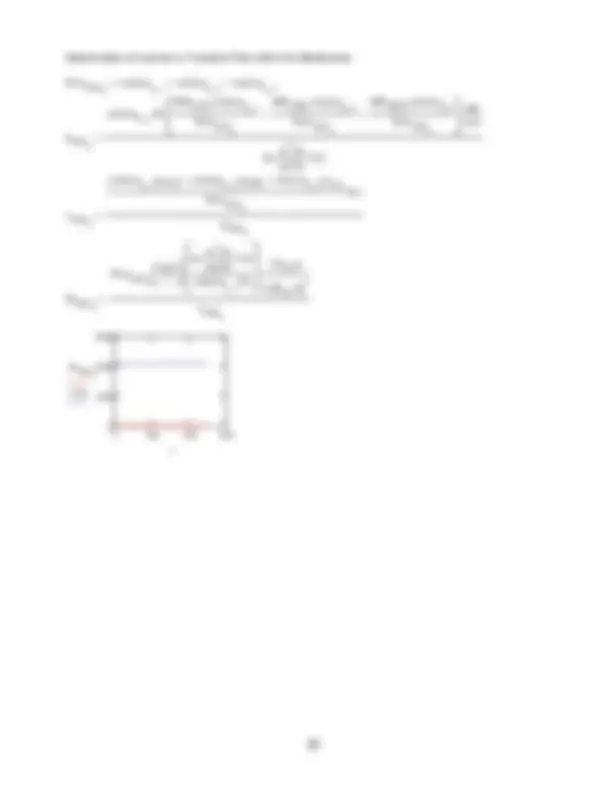
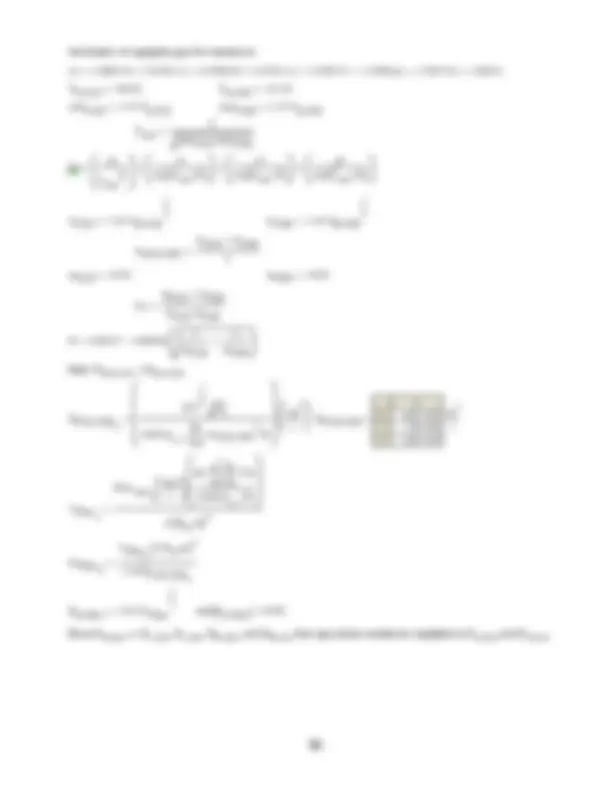
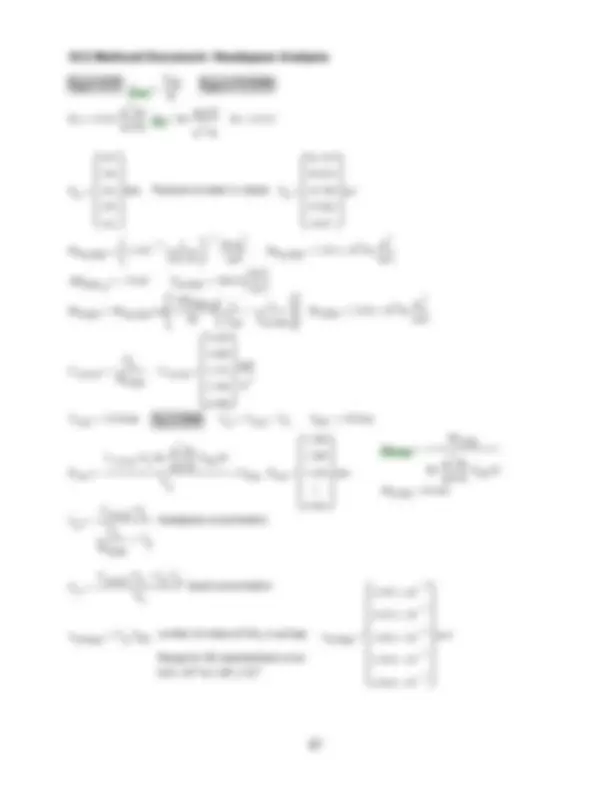
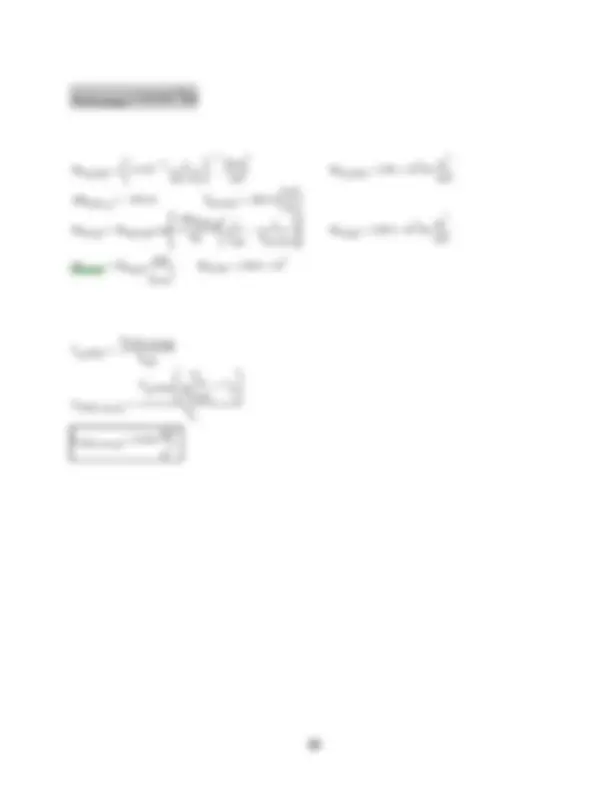
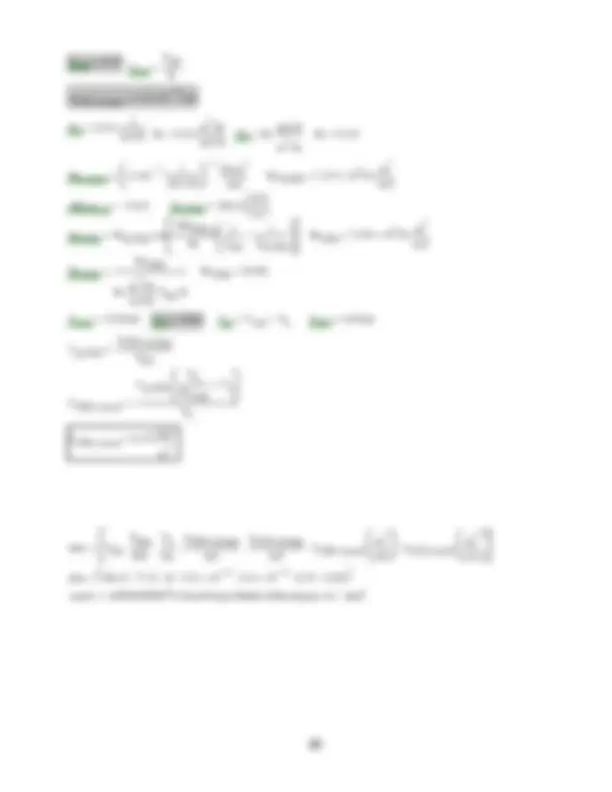
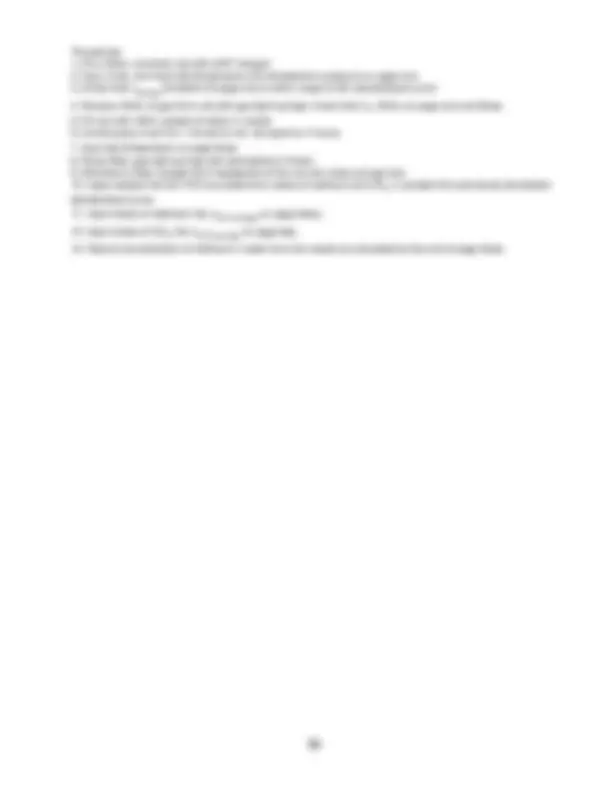
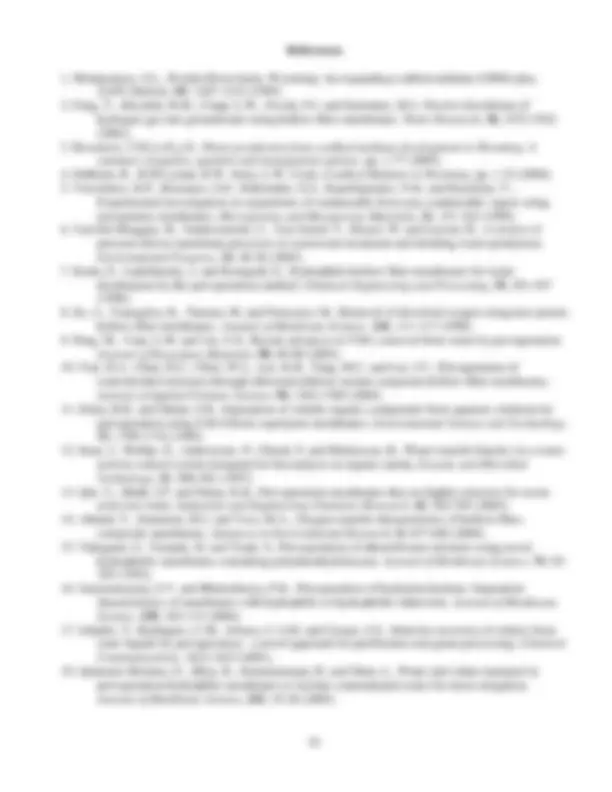
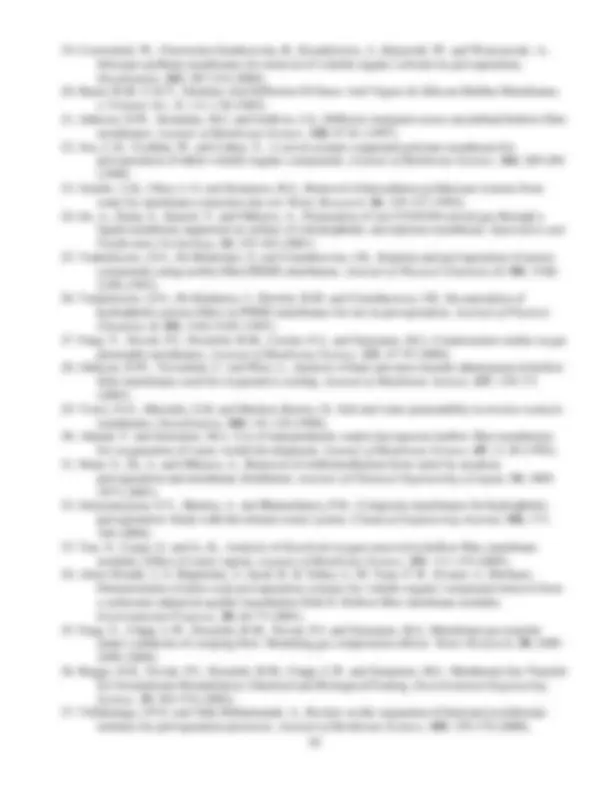
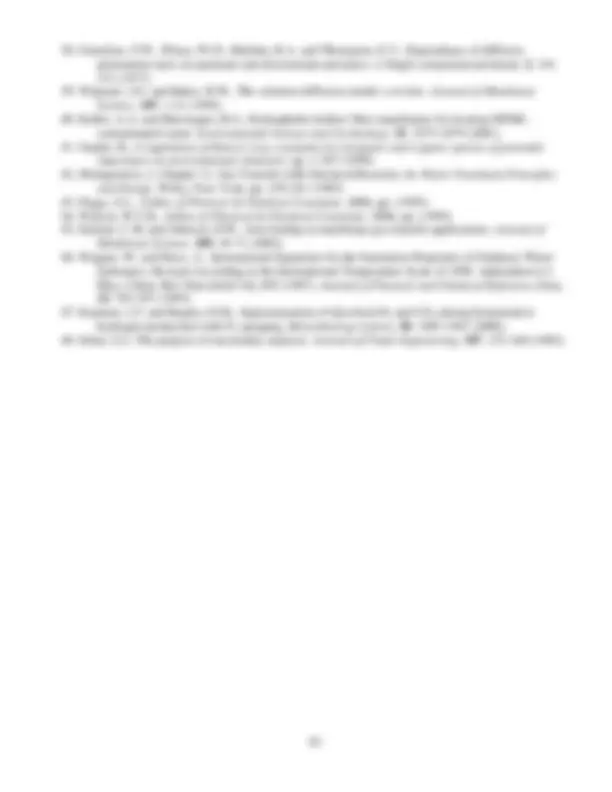
Study with the several resources on Docsity
Earn points by helping other students or get them with a premium plan
Prepare for your exams
Study with the several resources on Docsity
Earn points to download
Earn points by helping other students or get them with a premium plan
Community
Ask the community for help and clear up your study doubts
Discover the best universities in your country according to Docsity users
Free resources
Download our free guides on studying techniques, anxiety management strategies, and thesis advice from Docsity tutors
Material Type: Paper; Class: Arch Engr Graphics; Subject: Architectural Engineering; University: University of Wyoming; Term: Summer 2007;
Typology: Papers
1 / 99
This page cannot be seen from the preview
Don't miss anything!
To the Graduate School: The members of the Committee approve the thesis of Theodore A. Cramer presented on July 24,
Drew Johnson, Chairman
Michael Urynowicz
Maciej Radosz
Jay Puckett, Head, Department of Civil & Architectural Engineering
Don Roth, Dean, The Graduate School
Cramer, Theodore A., Membrane Gas Transfer of Methane and Carbon Dioxide in Submerged Coal Deposits, M.S., Department of Civil and Architectural Engineering, August 2007. Membrane degassing technology may prove to be a viable alternative to current CBM recovery. The proposed approach involves placing well-spaced membrane fibers directly within the saturated coal seam where a CO 2 sweep gas is supplied to the membrane lumens providing simultaneous CO 2 sequestration and CH 4 recovery. Specific objectives of the research are to: 1. develop a model that describes CH 4 and CO 2 membrane transfer in this environment; 2. verify the model experimentally through bench-scale testing; and 3. utilize the model to determine limits to effective recovery. A mass balance conducted on an infinitesimal fiber element provides the basis for development of a system of ordinary differential equations from which the gas composition within the fiber lumen can be determined as a function of fiber length. Verified through use of a bench-scale pressure vessel, agreement appears reasonable for CH 4 recovery; however, agreement for CO 2 recovery declines as liquid flow decreases and lumen flow rate increases. The average rate of CH 4 recovery for a conventional well after one to six months of dewatering is 1.56 x 10 4 m 3 /day. Model predictions for membrane degassing were normalized to this rate, yielding 290,000 m 2 or 7.73 km of spaced fiber fabric required for equivalent recovery within a hypothetical coal seam at 107 m. Through this approach, 4.11 x 10^5 m^3 of CO 2 would be sequestered daily, while the outlet gas composition would be 95% CH 4 , 4.4% CO 2 , and 0.6% H 2 O vapor. For broader application, required active membrane surface area was predicted in terms of groundwater velocity and pore pressure. Increased groundwater velocity and pore pressure each decrease the required membrane surface area for equivalent recovery. Although groundwater velocities within a shallow subsurface are not typically greater than 100 cm/day, higher flow rates do not significantly reduce the required surface area. However, a coal seam at 457 m with a pore pressure of 4.48 MPa would require 97% fewer fibers and only 0.206 km of membrane fabric as compared to the hypothetical coal seam.
Table of Contents
Section Page Table of Contents ii
iii Index of Figures
1.0 Literature Review 1.1 Coalbed Methane Coalbed methane (CBM) is a fossil fuel similar to natural gas that is found in coal deposits and formed by two processes, coalification and biological generation. Through coalification, water, carbon dioxide, and volatiles including mainly methane are expelled during “progressive burial,” the process where peat is transformed into coal. Late stage biogenic methane is generated through anaerobic bacterial activity within the groundwater system[1]. Most shallow deposits of coal are aquifers due to their well- developed cleat or fracture system, which becomes saturated with water. Lateral groundwater flow, which is dependant on the natural fracturing of the coal seam, ranges up to 100 cm/day[2, 1]. Within submerged coal deposits, methane is stored as free gas within the micropores and cleat system, dissolved gas within the water, adsorbed gas by molecular attraction, and absorbed gas within the molecular structure of the coal[1]. The extent of storage for a particular seam depends on various factors including coal rank, burial depth, volume, and water saturation; increased pressure and temperature within sub- bituminous and bituminous coals allows for increased storage[1].
The Rocky Mountain Region may contain as much as 79% of the estimated 19.1 trillion cubic meters (tcm) of methane gas reserves within the United States[1]. Although the coals found in Wyoming are relatively low rank, lignite to sub-bituminous, with sorbed gas contents for the Fort Union Formation between 0.031 and 2.31 m 3 /tonne, they are large, laterally extensive seams[1]. For comparison, coals from the Fruitland Formation of the San Juan basin in Colorado contain 2.19-16.8 m 3 /tonne[1]. The Paleocene Fort Union Formation within the Powder River Basin (PRB) has seams 15.2 to 45.7 m thick with relatively sizeable volumes of late-stage biogenic methane present as a free gas within the cleat system between 91.4 and 610 ft deep[1]. The Fort Union Formation, alone, is estimated to contain 0. to 0.34 tcm of Wyoming’s total estimated resource of 0.898 tcm[1], 95% of which was yet to be recovered as of December 2004[3]. The eastern portion of the PRB, 0.405 million hectares or more, is
composed of seams 24.4-45.7 m thick and continuous for 16.1-48.3 km[1]. Gas recovered from older fields in the Tongue River Member contained 95% methane, 4.98% nitrogen, and 0.02% carbon dioxide[1].
The current economical CBM recovery approach requires several wells to be drilled throughout the seam from which to pump the water that saturates the deposit. As the dewatering process continues, the hydrostatic pressure within the gas-bearing coal seam is reduced until the methane is released from the coal and migrates to the well. “Gas migration within the coal takes place by a combination of desorption, diffusion, and free-phase flow, and occurs as a direct result of pressure decrease”[1]. The methane is separated from the water either by equipment placed on the surface or by a submersible pump within the well. Utilizing the pump technology eliminates the need and economic burden of surface equipment while improving the total gas recovery[1].
Well spacing and extent of dewatering vary depending on the hydrologic character of the coal seam; where, the rate of recharge may prevent a regional aquifer from being easily dewatered for increased methane extraction[1]. On average, stable methane production occurs after one to six months of dewatering and is sustained for 12-24 months before declining at an annual rate of approximately 20%[4, 1]. Through the course of recovering Wyoming’s total estimated methane reserves by dewatering, 8. billion m^3 of water would be co-produced[3]. The water produced thus far has been discharged directly to surface drainages, on and off channel retentions for evaporation and/or infiltration, and exhausted coal deposits for re-injection[3]. Water quality for all individual basins and cumulative discharge effect on existing surface waters has not been fully assessed[3]. Both high quality water that generally meets drinking water standards and water that reduces soil infiltration rates due to its high salt concentration have been produced from the Powder River Basin; although, preliminary tests suggest substantially lower water quality may be produced from other deposits in Wyoming[3].
membrane area at a specific pressure[12]. For solid membranes, permeability is usually inversely proportional to membrane thickness; although, with elastomeric polymers, membrane thickness affected organics and water permeability inversely[9, 13]. Minimum thickness of the membrane, however, is dictated by manufacturing techniques and limits of mechanical stability for a particular application[9]. The disadvantage of decreasing gas permeability with increased membrane thickness may be negligible compared to the ability to operate at higher gas pressures without the formation of bubbles[14]. Selectivity or preferential diffusion of a particular component over its counterpart is caused by a variety of factors. These include size exclusion for porous membranes, rate of molecular diffusion for non- porous membranes, and affinity for water for hydrophobic or hydrophilic membranes. A particular selective factor may govern the overall selectivity of the membrane as is the case for separation of water- ethanol mixtures with hydrophobic and hydrophilic membranes. Ethanol, the molecularly larger component, permeates permselectively through hydrophobic membranes[15], while water is “selectively permeable”[9] only through a hydrophilic membrane, which is highly selective for water[7]. Also, selectivity and permeability are inversely related; where, a highly selective membrane does not typically deliver a high flux[11, 16]. For example, microporous membranes have increased selectivity, but lower permeabilities; while, mesoporous membranes, which have larger pores, have decreased selectivity and higher permeabilities[5].
Membranes are composed of various materials depending on the desired structure and application. For hydrophobic, microporous membranes, polypropylene, polyethylene, and Teflon have been used[14, 2]. Hydrophilic materials include sulfonated polyethylene[7], polyvinyl alcohol (PVA)[17], and thermoplastic copolyether esters elastomers[18]. Solid membranes are often composed of polydimethylsiloxane (PDMS) or silicone rubber due to its stability in ultra thin construction, hydrophobicity, which increases their selectivity for volatile organic compounds (VOCs) relative to
water[9, 15], heat resistance, low-temperature flexibility, and low surface tension[19]. Other materials include: polyether-block-polyamide (PEBA) for separation of toluene, 1,1,1-trichloroethane (TCA), dichloromethane, etc. from water; polyurethane (PUR) for removal of TCA, toluene and dichloromethane from aqueous solutions; polyvinylidene fluoride (PVDF) for benzene separation from water; ethylene propylene dienemonomer rubber (EPDM) for trichloroethylene (TCE) and toluene separation from water; poly[bis(phenoxy)phosphazene] (PPOP) for separation of methylene chloride from water;[9] silicone polycarbonate copolymer (SPC) for separation of TCA, toluene, and methylene chloride from water[11], and dimethylpolysiloxane elastomers for fractioning molecular mixtures at 25 to 40 times the rate of natural rubber[20]. Layered composite membranes have been developed by laminating a 1 μm thick, dense urethane layer between two microporous polyethylene support layers[14, 19, 21], modifying the surface of a highly structural porous ceramic membrane with a polyvinyl acetate (PVAc) active layer[22], casting a block copolymer of polystyrene and polybutadiene (S-B-S) on a hydrophobic PTFE thin film[11], casting siloxane, which increases the material’s hydrophobicity and permeability of organics[19], onto microporous polypropylene membranes[23], and supporting double-layer liquid membranes of diglycolamine (DGA) or triethylene glycol (TEG) on a microporous membrane[24], where liquid membranes were previously too unstable for practical applications[13]. Non-layered composite membranes include PDMS blended with hydrophobic zeolite (1-silicalite)[9] and PDMS with zeolite, carbon black, in situ methylated silica, or silylated silica fillers[25, 26].
Applications for membrane technology span several sectors. The mining industry uses membranes for separation of carbon dioxide from the water vapor saturated CO 2 /CH 4 stream collected during natural gas recovery to obtain pure methane[24]. Other industries utilize membranes for removing dissolved oxygen (DO) from process waters[27, 8], dehydration of alcohol-water streams[22, 18], separation of close
is applied on the other side to induce transport through the membrane[19, 31, 38, 17, 39]. While the vapor pressure of a particular permeable component in the gas phase is lower than the vapor pressure of that component in the liquid phase, pervaporation will occur[39]. For a rapid sweep stream, the vapor pressure of components in the permeate can be considered negligible[18]. A variation of pervaporation utilizes a low pressure sweep stream of non-volatile organic oil to induce permeation of VOCs from water to the oil through a microporous membrane[23]. To prevent wetting of the pores by the oil, which circulates counter-currently to the flow of contaminated feed water within the fiber lumens, the shell of the membrane was coated with a siloxane casting[23]. Another process resulted in the enhanced recovery of a hydrophobic, target component from the aqueous phase. First, a non-porous, hydrophilic membrane was used to remove a majority of the water then the concentrated stream was applied to a hydrophobic membrane to remove the target component at higher yields[17].
1.3 Membrane Modules & Configurations Membranes are typically manufactured as either flat sheets or hollow fibers. Sheet membranes have been used for reverse osmosis, VOC or TCE removal from water[19, 31], and to simplify the study of membrane materials for full-scale application with hollow fiber membranes (HFM). However, sheet membranes are limited to parallel fluid flow along the membrane surface. Reverse osmosis is a pressure driven, membrane separation process that utilizes non-porous, water permselective, sheet membranes to separate water from a salt solution typically for residential sized drinking water applications[6, 39]. Under normal osmosis (dialysis), water permeates through the membrane from the pure-water side to the less concentrated water or salt side[39]. By applying high pressure to the salt side while maintaining the pure-water side near atmospheric pressure[38], the osmotic pressure can be overcome and result in movement of water from the salt side to the pure-water side[39].
Hollow fiber membranes (HFM), or tubes on the order of 100 μm in diameter, are typically used when a very large surface area per unit volume is required[21, 40, 9]. Furthermore, HFM are very flexible in their configuration[33]. Closed-end operation entails sealing one end of the fiber so that either a positive or negative pressure can be applied to the inside or fiber lumen. Flow-through operation utilizes a sweep gas or alternative fluid that wicks the permeate from the surface of the membrane on either the shell or lumen side of the membrane. By utilizing shell-side liquid flow, high pressure drops through the membrane leading to large energy requirements for pumping are avoided and the fluid can flow either parallel or normal to the fibers[7, 33]; although, the pressure drop of gases flowing through a membrane fiber was found to be less than 1%[18]. Shell-side feed results in lower transfer kinetics and shorter membrane-fluid residence times[34], where the former can be increased by introducing turbulence into the feed stream[9]. The fluid flowing within the fiber lumens is parallel and laminar due to the small hydraulic diameter of the fibers[7, 9].
Individual hollow fibers can also be woven into a fabric that permits either parallel or normal shell-side flow[2]. In 2002, a study by Fang et al. utilized HFM fabric and membrane bundles for in-situ transfer of hydrogen gas into a shallow aquifer to stimulate biodegradation of a plume of chlorinated solvents. The membrane fabric, composed of thousands of evenly spaced gas-permeable, hollow-fiber membranes, was installed normal to groundwater flow; while, the membrane bundles were placed in closely spaced wells throughout the aquifer. The porosity of the fabric was similar to the porosity of the aquifer, approximately 33%, resulting in minimal resistance to lateral groundwater flow (Reynolds number ranging from 10 -3^ to 10-4) while providing a large area for gas transfer[2]. The membrane bundles were advantageous due to their relatively simple installation and lower cost resulting from using existing wells and established drilling techniques[2].
bubbleless aeration of water[34, 30]. Water vapor will continuously diffuse into the membrane, supersaturating the gas phase and lead to condensation as the feed diffuses into the water[27]. Placement of hydrophilic membrane material at the sealed end of the membranes allows accumulated condensate to diffuse back into the liquid phase while the lumen pressure exceeds that of the surrounding water[27] or by utilizing a flow-through approach, the water vapor is rapidly swept away by the sweep stream[34, 27].
Flow-through configuration has been used to deliver hydrogen gas to ground water with HFM. To maintain a similar concentration of hydrogen throughout the length of each fiber, a high gas flow rate (7mL/min) was used[35]. With flow-through configuration, however, transfer efficiency nears one hundred percent only at extremely low gas flow conditions. Alternatively, at low transfer efficiencies, wasting of the feed gas and any stripped contaminates occurs at the outlet end[27]; in the case of hydrogen, this may lead to explosive conditions at the outlet[35]. Therefore, means to capture and separate vented components should be included at the outlet. To avoid changes in gas composition within the fibers from back diffusion during low gas flow conditions, which results in non-uniform gas delivery, the contents of the membrane can be regularly flushed with a pulse of gas equal to the internal volume of the membranes, refilling them with pure gas[35]. Operating conditions included maintaining the feed pressure of hydrogen just above atmospheric, pressurizing the water to approximately 27.6 kPa or 3 meters of hydrostatic pressure, and pumping the water normal to the membranes to better simulate a groundwater environment[2]. To measure the amount of water vapor back diffusing into flow-through modules, several researchers have utilized a liquid-nitrogen water trap at the outlet end of the module[11, 27, 22]. Overall, membrane modules “must be designed to encourage the discharge of condensate as it forms”[27]. One method suggested installing the membrane modules vertically so that condensate would flow to the bottom as the gas was fed counter-currently, flowing to the top of the modules[27].
1.4 Membrane Equations for Gas and Water Vapor Transfer Gas transfer or flux, N for a particular component, i is defined as the overall mass transfer coefficient for the component, KO.i multiplied by the driving force. Driving force is a transmembrane gradient which enables components to diffuse through the membrane. Common gradients include concentration, pressure, temperature, and electromotive force[39]. For a dissolved component, the permeate flux is: N (^) i = KO. i ( C (^) L. i Cg. i ) (1)
where the driving force is defined as the difference between the concentration in the liquid phase, C (^) Li and the concentration or partial pressure of the component in the gas phase, C (^) gi. This gradient is either expressed in equivalent gas phase units by multiplying C (^) Li by the Henry’s law constant for the component, Hci [31], or liquid phase units by dividing the partial pressure of the component in the gas phase, P (^) i by Hci [24, 21, 33]. Thus, for the latter case:
N (^) i = KO. i ( CL. i HcPi i ) (2)
Since Henry’s Law constant is a function of temperature, the liquid phase saturation concentration of a component can be increased by increasing either pressure or temperature. Thus, the larger the hydrostatic pressure within a coal seam, the larger the potential dissolved concentration of methane. In closed-end, vacuum pervaporation modes, the partial pressures of the gases are low, creating a large driving force into the membranes. Equation 2 assumes the concentration of the component in the bulk phase does not change significantly as it flows across a membrane fiber; thus, C (^) Li is constant on either side of the fiber[30, 22]. Alternatively, an arithmetic average of upstream and downstream concentrations of the component[11] can be calculated to incorporate the effect of gas transfer from the bulk solution into the driving force as follows[35]:
N (^) i = KO. i ( C^0. i^ + 2 Cf. i HcPi i ) (3)
layer between two polyethylene support layers found the rate of gas diffusion, including through the support layers, was negligible to the overall mass transfer coefficient since it was approximately five orders of magnitude greater than the rate of liquid diffusion[21]. The resulting resistance-in-series model included the resistance due to the urethane layer and the resistance due to transport through the liquid film, where the urethane resistance contributed 53 to 82 percent of the overall resistance to gas transfer[14].
Gas transfer with microporous, hydrophobic membranes is limited by liquid film diffusion[27, 8, 9, 36, 23]; however, for non-porous and composite membranes, application and specific material structure influenced the effect of liquid film and membrane resistances on the overall rate of gas transfer. In application, however, membrane fouling by plugging, mineral precipitation, and biofilm formation may shift the rate limiting step to diffusion through the membrane[2]. Additionally, biofilm activity may increase gas transfer through the membrane, but reduce penetration depth into the bulk liquid through biological consumption within the liquid film[2]. Thicker membranes with fouling resistant coatings may be advantageous in application. While liquid film diffusion remains the rate limiting step, lower gas transfer through these membranes will not affect overall gas transfer performance[2].
Water flux, however, is not limited by liquid-film diffusion since water is the solvent[27]. Water evaporates from the liquid film into the membrane, molecularly diffuses across the membrane material and into the gas boundary layer, then into the bulk gas phase. Water vapor transport, therefore, is either membrane or gas resistance controlled[30, 27]. The overall mass transfer coefficient for water vapor is typically several orders of magnitude greater than gas transfer. As a result, “water vapor will saturate the feed gas within…the first few centimeters of the fiber entrance;” although, the water vapor will only contribute 2-3% of the gas stream at saturation[27]. Condensation within HFM occurs at four possible locations: “at the liquid–membrane surface, in the bulk gas phase, at the gas–membrane surface, or
within the fiber pores”[27]. Water condensation at the liquid-membrane surface is insignificant since liquid water is already in contact with the membrane. Condensation in the bulk gas phase may also be neglected for flow-through configuration as it will be swept to the module outlet. However, condensation at the gas-membrane surface and within the membrane material would increase the membrane resistance to gas transport and increase the permeability of the membrane to liquid water[27].
The overall mass transfer coefficient, KO.i and individual mass transfer coefficients are the reciprocal of the respective resistances. Thus:
K (^) O. i KM. i KL. i KG. i
The liquid phase mass transfer coefficient, K (^) L.i is determined from three dimensionless constants; these are the Sherwood number, Schmidt number, and Reynolds number. The Sherwood number represents the ratio of length scale to the diffusive boundary layer thickness. It is defined as:
D Sh = KL^ d (6)
where d is the characteristic length scale. The Schmidt number approximates the ratio of momentum diffusivity (viscosity) and mass diffusivity for fluid flows with simultaneous momentum and mass diffusion convection processes. It is defined as:
Sc D = (7)
where nu is the kinematic viscosity of the fluid. The Reynolds number is the ratio of inertial forces to viscous forces and is defined as:
Re =^ vd (8)