
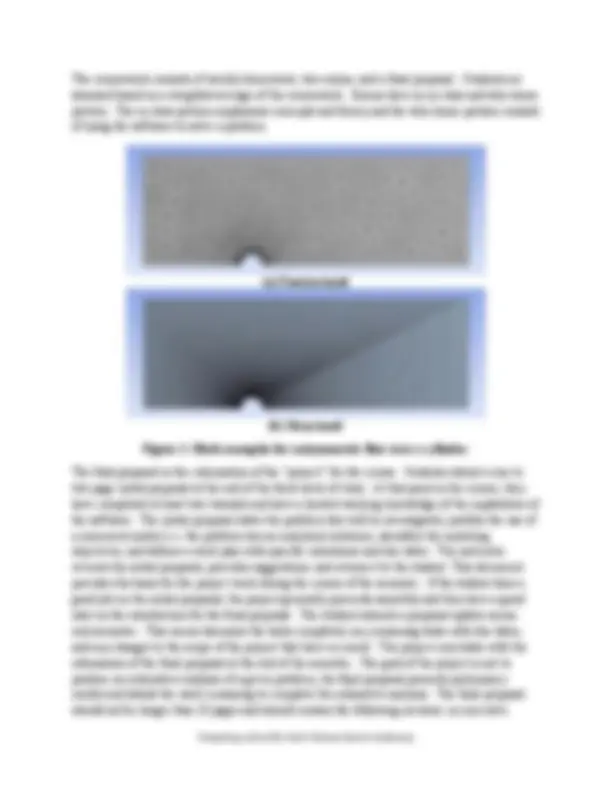
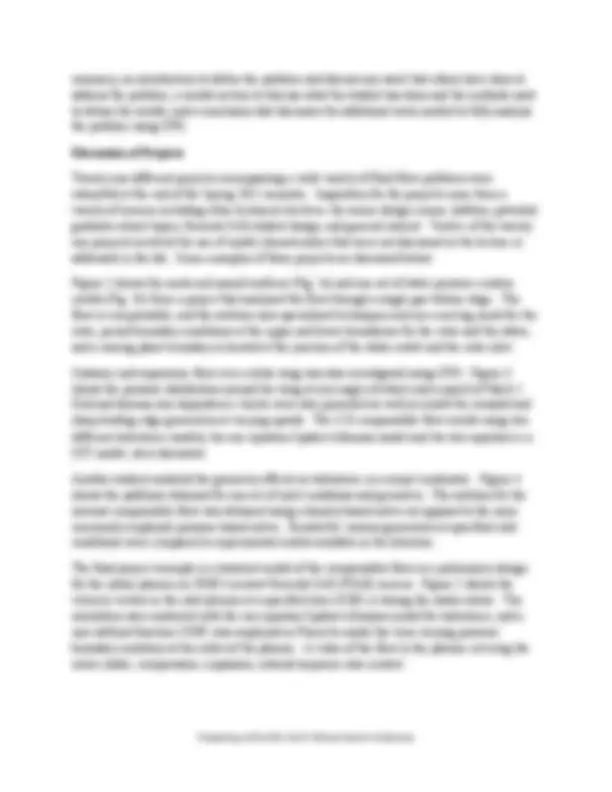
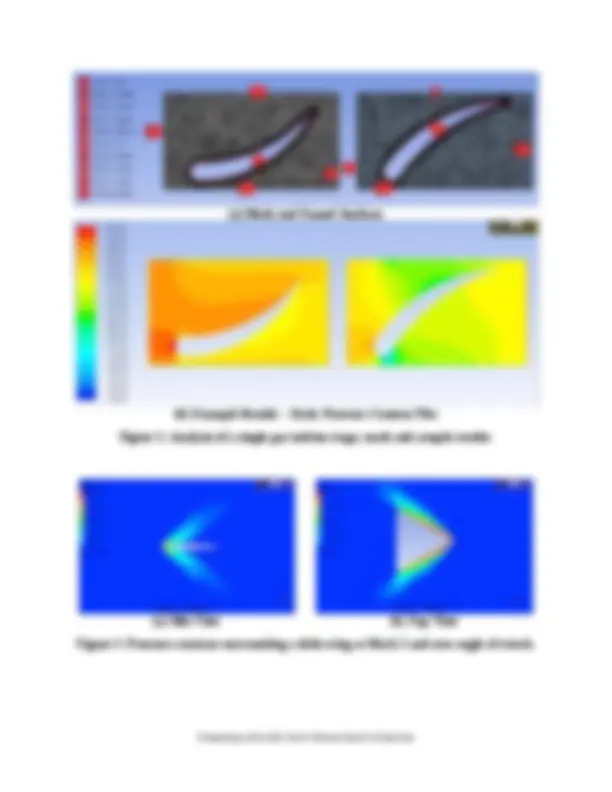
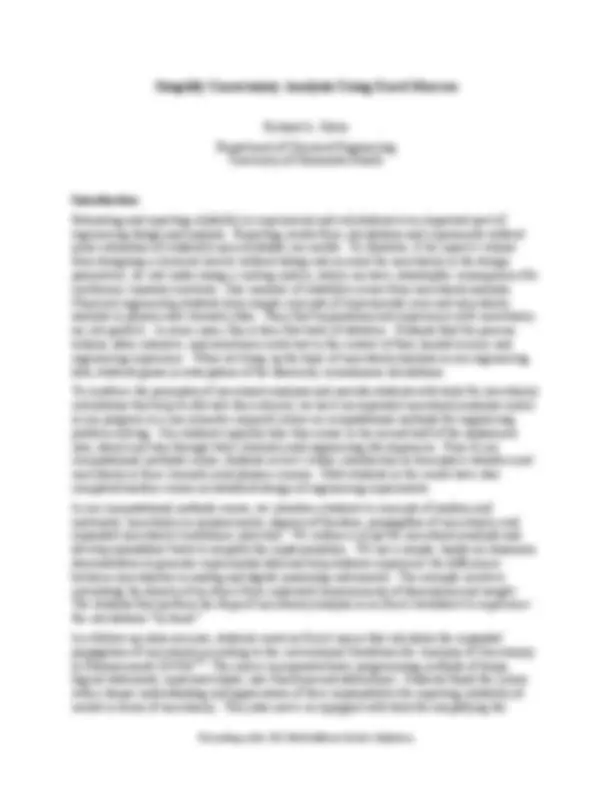
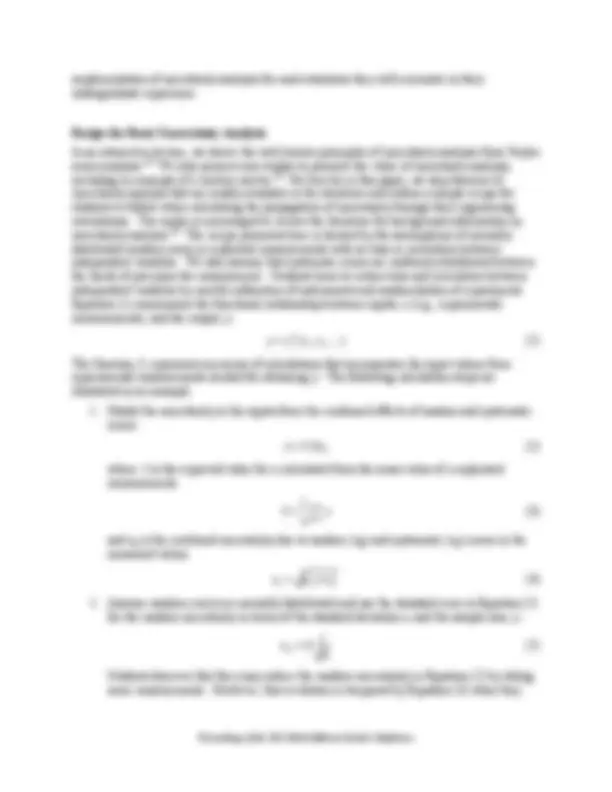
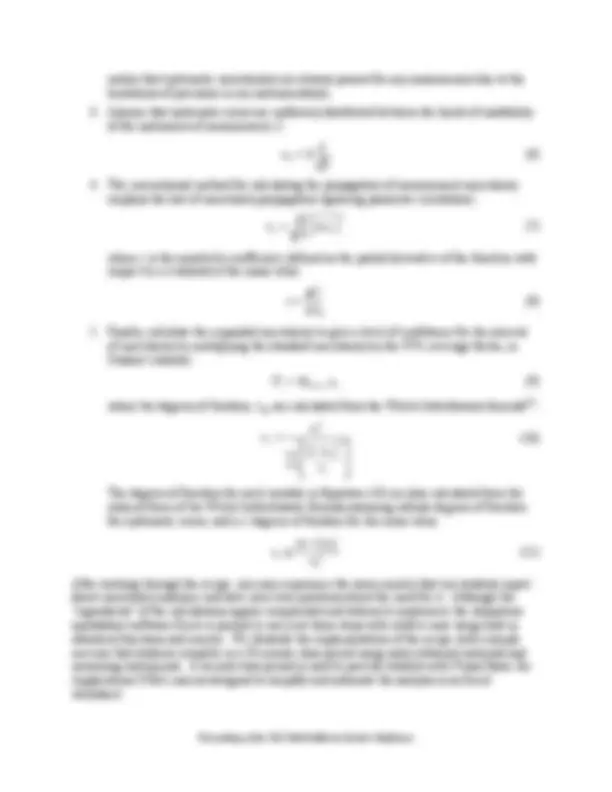
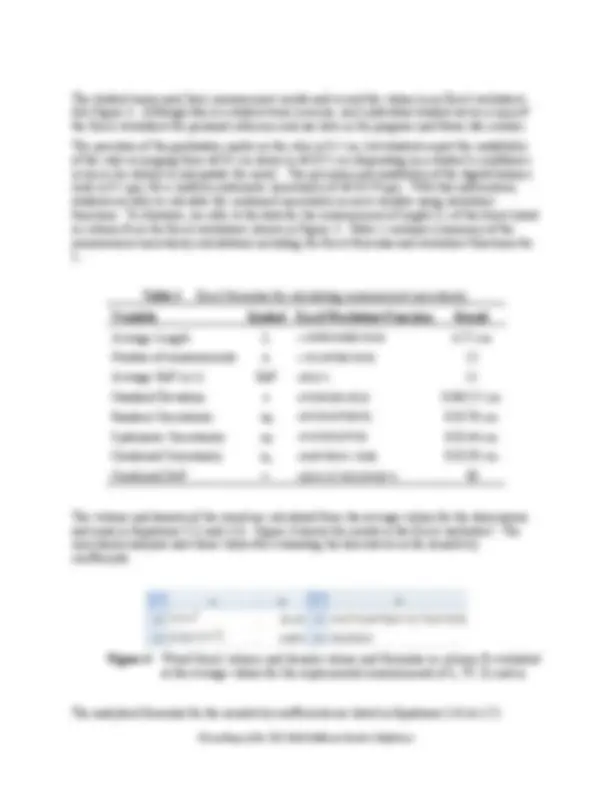
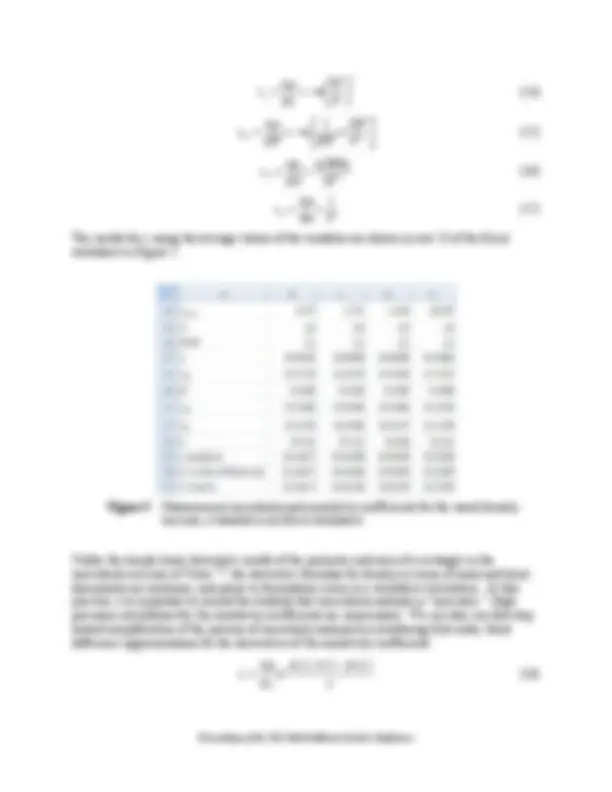
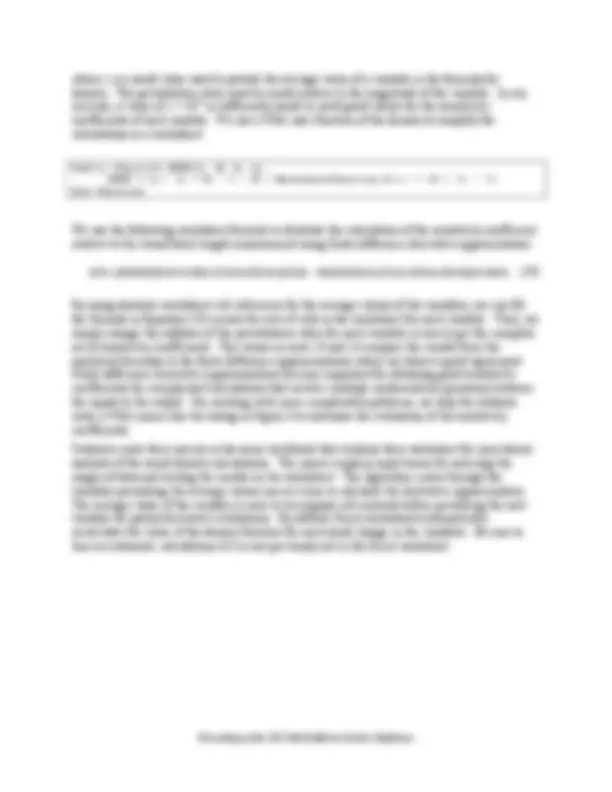
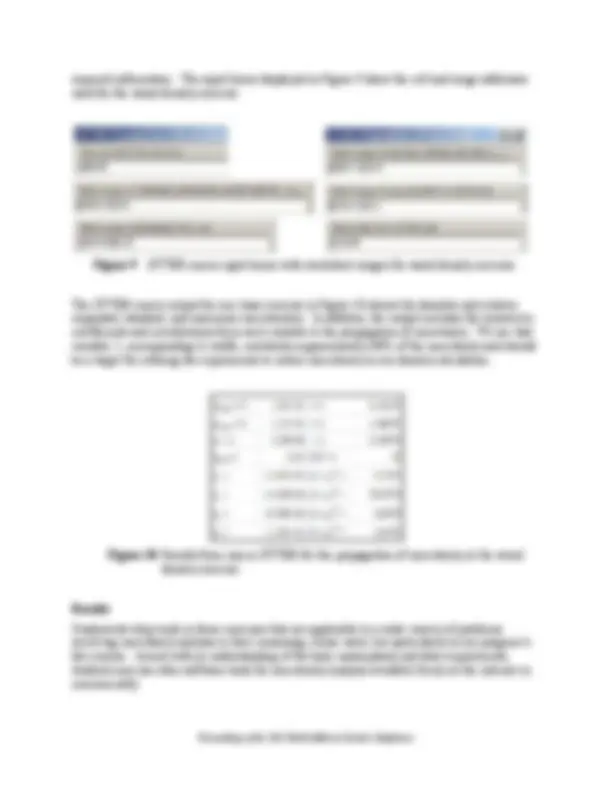
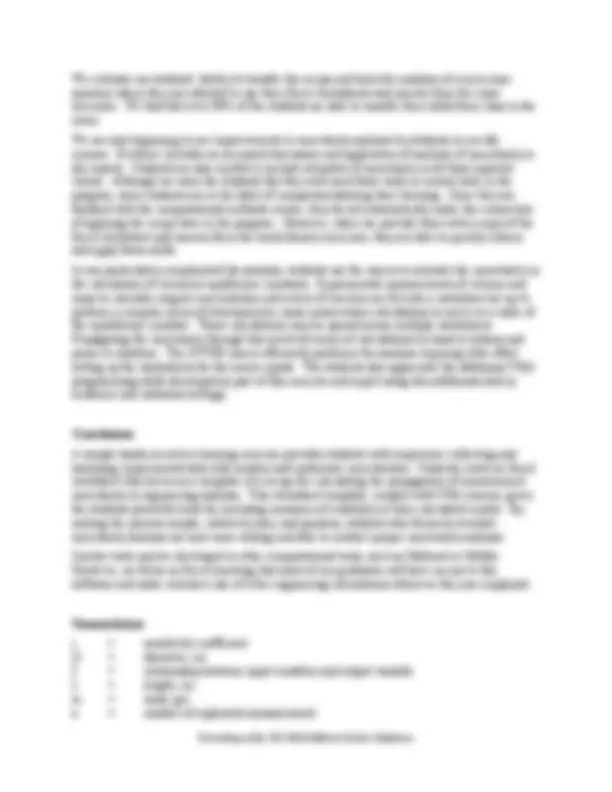
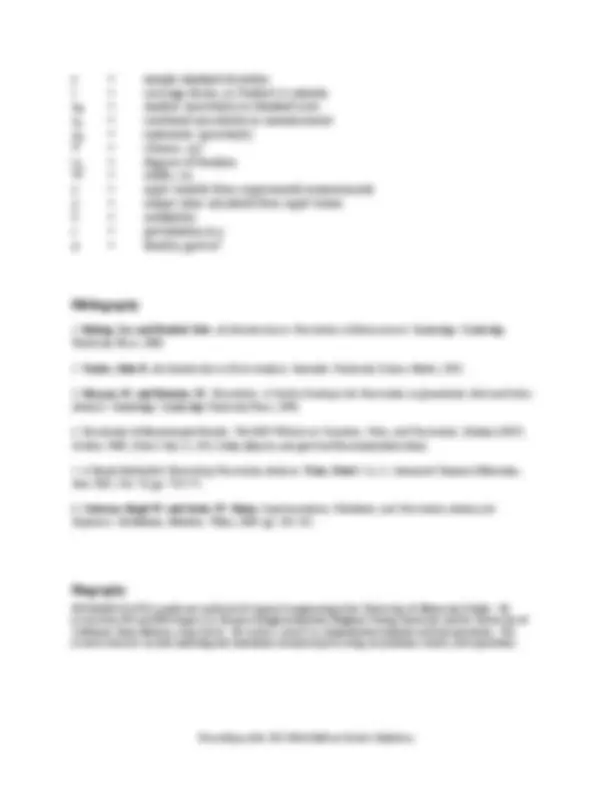
Study with the several resources on Docsity
Earn points by helping other students or get them with a premium plan
Prepare for your exams
Study with the several resources on Docsity
Earn points to download
Earn points by helping other students or get them with a premium plan
Community
Ask the community for help and clear up your study doubts
Discover the best universities in your country according to Docsity users
Free resources
Download our free guides on studying techniques, anxiety management strategies, and thesis advice from Docsity tutors
The use of final projects that are selected and designed by students in a senior level, undergraduate Computational Fluid Dynamics (CFD) course. The course utilizes a final project to address the shortcomings of the basic theory for pressure-based solutions on regular, structured meshes. Each student designs their own problem at the beginning of the semester with guidance from the instructor. the problems designed by the students, the models they employed, the challenges faced by the instructor, and the lessons learned.
Typology: Lecture notes
1 / 20
This page cannot be seen from the preview
Don't miss anything!
Daniel N. Pope University of Minnesota Duluth
Abstract
The use of final projects that are selected and designed by students in a senior level, undergraduate Computational Fluid Dynamics (CFD) course is discussed. Analysis of products and systems that include heat transfer and fluid flow using CFD software is becoming a required part of the design process. Prospective employers are looking for undergraduate students that have some experience performing CFD analyses. However, the techniques used in CFD are often problem dependent and can involve mathematics that is beyond the undergraduate level. In addition, CFD analysis is still somewhat of an art form where the adjusting of multiple solution ³SaUameWeUV´ can change a XVeleVV mRdel inWR a URbXVW, Sh\Vicall\ UealiVWic mRdel. In RUdeU WR provide undergraduate students with the necessary background, the basic theory for pressure- based solutions on regular, structured meshes is often presented with simple numerical examples to reinforce the lessons. The theory and the examples are limited in scope and they discuss only a fraction of the available CFD techniques. The course discussed here utilizes a final project to address these shortcomings. Each student designs their own problem at the beginning of the semester with guidance from the instructor. As a result, students generally take ownership of their projects, they learn material specific to their projects and beyond that taught in class, and Whe\ cRmmXnicaWe WhaW maWeUial WR WheiU claVVmaWeV. Since each VWXdenW¶V SURjecW iV diffeUenW, there is usually an increaVed demand Rn Whe inVWUXcWRU¶V Wime. ThiV SaSeU SUeVenWV Whe VWUXcWXUe of the CFD course, the problems designed by the students, the models they employed, the challenges faced by the instructor, and the lessons learned.
Introduction
The evolution of modern computers and simulation tools has had a profound effect on the
engineering profession. Engineering problems that were once addressed by government
researchers or industry research and design teams using custom computer codes can now be
routinely solved using commercial codes on desktop computers. Companies routinely use these codes to solve a wide range of engineering problems. Academic courses covering different
simulation techniques have been increasingly offered at the undergraduate level to address
industry needs.
TR UedXce bRWh Whe cRVW and deYelRSmenW Wime, WRda\¶V Sroducts and systems are now frequently
designed and analyzed using computational simulation tools. Many tools, such as computer-
aided design (CAD) codes and finite element analysis (FEA) packages, are well-established in
the mechanical engineering design process. Computational fluid dynamics (CFD) simulations
have been increasingly incorporated in the design process during the past decade. As a result,
ASME has recently published a standard governing the verification and validation of CFD
results 1.
The field of CFD addresses the modeling and prediction of fluid flow, heat and mass transfer,
chemical reactions, and other flow phenomena via the numerical solution of governing
mathematical equations. Courses that introduce CFD methods have been a part of graduate
programs in mechanical engineering for decades. Many prospective employers are looking for
undergraduate students that have some experience performing CFD analyses; however, CFD
courses are not always available to undergraduate students 2.
This paper discusses the undergraduate CFD course taught at the University of Minnesota Duluth
(UMD). The structure of the course is described, and a summary and discussion of the student- designed projects is presented. Finally, the conclusion addresses the lessons learned and future
plans for the course.
Course Structure
The CFD course taught at UMD is a senior level, advanced technical elective offered by the
Department of Mechanical and Industrial Engineering. The course is taught during the spring
semester of odd years (once every two years) and the author has taught the course four times
(spring of 2005, 2007, 2009, and 2011). Prerequisites for the CFD course include the computer programming, CAD, Calculus (I-III), Differential Equations, Fluid Dynamics, Thermodynamics,
and Heat and Mass Transfer courses. ANSYS Workbench 12.1 with the Meshing and Fluent
modules is the commercial code that is used within the course. A newer textbook by Tu et al. 3
was used in spring 2011; previous semesters utilized a book by Patankar 4. The course is three
credit hours and meets three hours per week; two hours per week are spent in lecture, and one
hour per week is spent in the computer lab.
Lectures covered the following topics over the course of the semester: the CFD solution
procedure, the governing equations for incompressible flow with heat transfer, the Reynolds
Averaged Navier Stokes equations, the k-H turbulence model, the finite-difference method
(FDM), the finite-volume method (FVM), numerical solution of algebraic equations, and CFD
solution analysis. Computer lab sessions focused on familiarizing the students with the
capabilities and use of the ANSYS software. Students were expected to perform various
tutorials available on the ANSYS Customer Portal 5 and at Cornell UniYeUViW\¶V SimCafe ZebViWe 6
and present a summary of the techniques and tools that they learned about in each tutorial. They
were also prompted to access materials appropriate to their individual project from the ANSYS
Customer Portal 5 and Resource Library^7. Several lab sessions where used to review meshing including structured and unstructured meshes. Figure 1 shows examples used in the lab of an
unstructured mesh (Fig. 1a) and a structured mesh (Fig. 1b) for axisymmetric flow over a
cylinder.
summary, an introduction to define the problem and discuss any work that others have done to
address the problem, a results section to discuss what the student has done and the methods used
to obtain the results, and a conclusion that discusses the additional work needed to fully analyze the problem using CFD.
Discussion of Projects
Twenty one different projects encompassing a wide variety of fluid flow problems were
submitted at the end of the Spring 2011 semester. Inspiration for the projects came from a
variety of sources including other technical electives, the senior design course, hobbies, potential
graduate school topics, formula SAE student design, and general interest. Twelve of the twenty
one projects involved the use of model characteristics that were not discussed in the lecture or
addressed in the lab. Some examples of these projects are discussed below.
Figure 2 shows the mesh and named surfaces (Fig. 2a) and one set of static pressure contour
results (Fig. 2b) from a project that analyzed the flow through a single gas turbine stage. The
flow is compressible, and the solution uses specialized techniques such as a moving mesh for the
rotor, period boundary conditions at the upper and lower boundaries for the rotor and the stator,
and a mixing plane boundary is located at the junction of the stator outlet and the rotor inlet.
Subsonic and supersonic flow over a delta wing was also investigated using CFD. Figure 3
shows the pressure distribution around the wing at zero angle of attack and a speed of Mach 2. Grid and domain size dependence checks were also presented as well as results for rounded and
sharp leading edge geometries at varying speeds. The 3-D compressible flow results using two
different turbulence models, the one equation Spalart-Allmaras model and the two equation k-Z
SST model, were discussed.
Another student modeled the geometry effects on turbulence in a ramjet combustor. Figure 4
shows the pathlines obtained for one set of inlet conditions and geometry. The solution for the
internal compressible flow was obtained using a density-based solver as opposed to the more
commonly employed pressure-based solver. Results for various geometries at specified inlet conditions were compared to experimental results available in the literature.
The final project example is a transient model of the compressible flow in a preliminary design
fRU Whe inWake SlenXm Rn UMD¶V neZeVW FRUmXla SAE (FSAE) UacecaU. Figure 5 shows the
velocity vectors in the inlet plenum at a specified time (0.001 s) during the intake stroke. The
simulation was conducted with the one equation Spalart-Allmaras model for turbulence, and a
user-defined function (UDF) was employed in Fluent to model the time-varying pressure
boundary condition at the outlet of the plenum. A video of the flow in the plenum covering the
entire intake, compression, expansion, exhaust sequence was created.
(a) Mesh and Named Surfaces
(b) Example Results – Static Pressure Contour Plot
Figure 2: Analysis of a single gas turbine stage; mesh and sample results.
(a) Side View (b) Top View
Figure 3: Pressure contours surrounding a delta wing at Mach 2 and zero angle of attack.
techniques and of the ANSYS software that was used in the course. A majority of the students
went beyond the material presented in class and took the initiative to learn the modeling
techniques required to solve their specific problem. The wide variety of problems and methods employed resulted in an increased demand on the inVWUXcWRU¶V Wime. As a result, the number of
students should be limited to a maximum of twenty five if the current course structure is
maintained.
Bibliography
DANIEL N. POPE Dr. Daniel N. Pope (Dan) is an Associate Professor in the Department of Mechanical and Industrial Engineering at the University of Minnesota Duluth. His education includes a B.S.M.E. (1989), a M.S.M.E. (1993) and a Ph.D. (2001) from the University of Nebraska-Lincoln (UNL), as well as Naval Nuclear Power School and Naval Prototype Training (1990). Dan has held jobs as an officer in the U.S. Navy, a consulting engineer for Black and VeaWch¶V PRZeU DiYiViRn, and a Research Assistant Professor in the Department of Mechanical Engineering at the University of Nebraska-Lincoln. He has over 15 years of teaching experience in Mechanical Engineering at the undergraduate level and has presented several lectures in graduate level thermal/fluids science courses. His research interests include computational fluid dynamics, the fundamental processes present in fuel droplet vaporization and combustion, biodiesel production and use, and sustainable energy systems. Dan is a member of ASME, SAE, ASEE, and The Combustion Institute. He currently serves as advisor for two UMD student organizations; the ASME student section, and the Formula SAE design team.
Richard A. Davis Department of Chemical Engineering University of Minnesota Duluth
Introduction
Estimating and reporting reliability in experiments and calculations is an important part of engineering design and analysis. Reporting results from calculations and experiments without some estimation of reliability may invalidate our results. To illustrate, if we report a volume from designing a chemical reactor without taking into account the uncertainty in the design parameters, we risk under sizing a cooling system, which can have catastrophic consequences for exothermic runaway reactions. One measure of reliability comes from uncertainty analysis. Chemical engineering students learn simple concepts of experimental error and uncertainty analysis in physics and chemistry labs. Their first impressions and experiences with uncertainty are not positive. In some cases, this is their first taste of statistics. Students find the process tedious, labor intensive, and sometimes irrelevant in the context of their limited science and engineering experience. When we bring up the topic of uncertainty analysis in our engineering labs, students groan in anticipation of the laborious, monotonous calculations.
To reinforce the principles of uncertainty analysis and provide students with tools for uncertainty calculations that help to alleviate their anxiety, we have incorporated uncertainty analysis earlier in our program in a one-semester required course on computational methods for engineering problem solving. Our students typically take this course in the second half of the sophomore year, about mid way through their chemistry and engineering lab sequences. Prior to our computational methods course, students receive a basic introduction to descriptive statistics and uncertainty in their chemistry and physics courses. Most students in the course have also completed another course on statistical design of engineering experiments.
In our computational methods course, we introduce students to concepts of random and systematic uncertainty in measurements, degrees of freedom, propagation of uncertainty, and expanded uncertainty (confidence intervals). We outline a recipe for uncertainty analysis and develop spreadsheet tools to simplify the implementation. We use a simple, hands-on classroom demonstration to generate experimental data and help students experience the differences between uncertainties in analog and digital measuring instruments. The example involves calculating the density of an object from replicated measurements of dimensions and weight. The students first perform the steps of uncertainty analysis in an Excel worksheet to experience the calculations “by hand.´
In a follow-up class-exercise, students create an Excel macro that calculates the expanded propagation of uncertainty according to the conventional Guidelines for Analysis of Uncertainty in Measurements (GUM).(1)^ The macro incorporates basic programming methods of loops, logical statements, input and output, user functions and subroutines. Students finish the course with a deeper understanding and appreciation of their responsibility for reporting reliability of results in terms of uncertainty. They also move on equipped with tools for simplifying the
realize that systematic uncertainties are always present for any measurement due to the limitations of precision in our instrumentation.
u Z
r (6)
where c is the sensitivity coefficient, defined as the partial derivative of the function with respect to x evaluated at the mean value:
x
f c x
w w
where the degrees of freedom, v (^) y, are calculated from the Welch-Satterthwaite formula (1)^ : 4 4
y y x x
u v c u v
The degrees of freedom for each variable in Equation (10) are also calculated from the reduced form of the Welch-Satterthwaite formula assuming infinite degrees of freedom for systematic errors, and n-1 degrees of freedom for the mean value: 4 4
x x
n u v u
After working through the recipe, you may experience the same anxiety that our students report about uncertainty analysis, and have your own questions about the need for it. Although the “ingredients´ of the calculations appear complicated and tedious to implement, the ubiquitous spreadsheet software Excel is primed to carry out these steps with relative ease using built-in statistical functions and macros. We illustrate the implementation of the recipe with a simple exercise that students complete in a 50-minute class period using easily obtained materials and measuring instruments. A second class period is used to provide students with Visual Basic for Applications (VBA) macros designed to simplify and automate the analysis in an Excel worksheet.
Classroom Exercise: Calculation of Wood Density
A simple classroom experiment was devised to allow students to generate random and systematic data for calculating the density of a wood sample from the dimensions of rectangular wooden blocks with a cylindrical hole drilled through their centers, as shown the schematic of Figure 1. Prior to the class, the instructor makes 12 rough copies of the small wood blocks from the same piece of wood, with slight deviations from the mean values of each dimension to introduce noise into the experimental data.
Figure 1 Schematic of wooden block with length L, width W, and hole diameter D.
This example extends the simpler exercise proposed by Yates, who distributed sheets of paper with hand-drawn rectangles to chemistry students for measuring the circumference and area. (5) The chemistry students used a ruler to measure the lengths of the sides of the rectangle. In our labs, however, students use combinations of analog and digital meters for collecting data. By extending the exercise to a density calculation, we allow for two different types of instruments of measurement. We also limit the number of measurements to four, which forces students to assume that the widths of the cross section are equal, a uniform hole diameter, and that the length of the hole is equal to the width of the block.
Students first derive an expression for the density of the block from the ratio of the mass to volume in terms of mass (m), length (L), width (W), and diameter (D).
m V
The volume is calculated from the dimensions of the block:
2
4
Students form teams with a minimum size of three. Each team is provided with a similar block of wood, an inexpensive plastic ruler for measuring length dimensions, and a portable digital scale for measuring the mass, as shown in Figure 2.
The student teams pool their measurement results and record the values in an Excel worksheet, like Figure 3. Although this is a student-team exercise, each individual student saves a copy of the Excel worksheet for personal reference and use later in the program and future lab courses.
The precision of the graduation marks on the ruler is 0.1 cm, but students report the readability of the ruler as ranging from ±0.05 cm down to ±0.025 cm (depending on a student¶s confidence in his or her ability to interpolate the scale). The precision and readability of the digital balance scale is 0.1 gm, for a uniform systematic uncertainty of ±0.05/√3 gm. With this information, students are able to calculate the combined uncertainty in each variable using worksheet functions. To illustrate, we refer to the data for the measurement of length (L) of the block listed in column B on the Excel worksheet, shown in Figure 3. Table 1 contains a summary of the measurement uncertainty calculations including the Excel formulas and worksheet functions for L.
Table 1 Excel formulas for calculating measurement uncertainty. Variable Symbol Excel Worksheet Function Result Average Length L = AVERAGE(B2:B13)^ 4.57 cm Number of measurements n = COUNT(B2:B13) 12 Average DoF (n-1) DoF =B15- 1 11 Standard Deviation s =STDEV(B2:B13) 0.06155 cm Random Uncertainty uR =B17/SQRT(B15)^ 0.0178 cm Systematic Uncertainty uZ =0.025/SQRT(3)^ 0.0144 cm Combined Uncertainty ux =SQRT(B18 + B20) 0.0229 cm Combined DoF v =(B15-1)*(B21/B18)^4 30
The volume and density of the wood are calculated from the average values for the dimensions and mass in Equations (12) and (13). Figure 4 shows the results in the Excel worksheet. The uncertainty analysis uses these values for evaluating the derivatives in the sensitivity coefficients.
Figure 4 Wood block volume and density values and formulas in column B evaluated at the average values for the experimental measurements of L, W, D, and m.
The analytical formulas for the sensitivity coefficients are listed in Equations (14) to (17):
2 L
c m L V
w (^) © ¹
2
W
c m W WV V
w (^) ¬ ¼
DWm c D V
w
c m (^) m V
w
The results for c using the average values of the variables are shown in row 23 of the Excel worksheet in Figure 5.
Figure 5 Measurement uncertainty and sensitivity coefficients for the wood density exercise, evaluated in an Excel worksheet.
Unlike the simple linear derivative results of the perimeter and area of a rectangle in the uncertainty exercise of Yates (5)^ , the derivative formulas for density in terms of mass and block dimensions are nonlinear, and prone to formulation errors in a worksheet calculation. At this juncture, it is important to remind the students that uncertainty analysis is “uncertain.´ High precision calculations for the sensitivity coefficients are unnecessary. We can take our first step toward simplification of the process of uncertainty analysis by introducing first-order, finite difference approximations for the derivatives of the sensitivity coefficients.
i i i i
x x c x
U U^ H^ U H
w ^
w
Public Sub dfdx() ' Calculate sensitivity coefficients from ' finite difference derivative approximations
' Get input from the worksheet Set x = Application.InputBox(Type:=8, Prompt:="Range of average variables:") Set f = Application.InputBox(Type:=8, Prompt≔ “Cell with function result:") Set sc = Application.InputBox(Type:=8, _ Prompt:="Range of sensitivity coefficients:")
' Specify number of variables, perturbation factor & save function value n = x.Count: eps = 0.0001: fi = f
' Loop through variables to calculate sensitivity coefficients For j = 1 To n temp = x(j).Formula ' save worksheet formula for average variable j x(j) = x(j) + eps ' perturb value of variable j in worksheet sc(j) = (f - fi) / eps ' calculate sensitivity coefficient for j x(j) = temp ' replace value/formula of j in worksheet Next j End Sub
Figure 6 VBA macro for calculating sensitivity coefficients in an Excel worksheet.
With the sensitivity coefficients, we now have all of the information needed to calculate the propagation of the uncertainty in the measurements for the variables (L, W, D, and m) through the calculation of density. First, we calculate the standard uncertainty from the law of propagation of uncertainty. Figure 7 shows the values for the product of the sensitivity coefficient and combined uncertainty required by Equation (7).
Figure 7 Excel worksheet calculation of standard uncertainty
The results for the square of the product (c·u) 2 guide the student in identifying which variable(s) contribute most to the uncertainty in y. We find that the contribution from the width measurement in column C is larger than the other variables by at least an order of magnitude. We can take steps to reduce the uncertainty in the width by taking more measurements, or using a higher precision ruler. We report the density with standard uncertainty as
Some practitioners recommend the retention of just one significant figure in the uncertainty,
Finally, students calculate the expanded uncertainty for a 95% confidence interval. We need the degrees of freedom from the Welch-Satterthwaite formulas in Equations (10) and (11). Table 2 summarizes the worksheet formulas and functions for calculating the propagation of uncertainty and coverage factor. Note how we rounded the result for the combined degrees of freedom down to the nearest integer value for a conservative value of the coverage factor:
Table 2 Excel worksheet formulas for calculating the propagation of uncertainty in the wood density exercise.
Variable Symbol Excel Worksheet Function Result Standard Uncertainty uy =SQRT(SUMSQ(B26:E26)) 0.013 gm/cm^3 Degrees of Freedom vy =ROUNDDOWN((B28^4)/(SUM(B29:E29)),0)^38 Coverage Factor t =TINV(0.05,B30)^ 2. Expanded Uncertainty Uy =B28*B31 0.026 gm/cm^3
We now have the expanded uncertainty for wood density:
or
Figure 8 Excel worksheet with results for expanded uncertainty in density.
Jitter Macro
A VBA macro JITTER that automates the complete recipe for uncertainty propagation is provided to the students. (6)^ The macro incorporates the VBA code from the student-generated macros from the class exercises. To use the macro, students must set up a worksheet with a cell containing the final value of the function ultimately calculated from the average values of experimental inputs. In addition, the worksheet must include ranges of values for the average variables, random uncertainties, readability, and degrees of freedom. In most cases, the degrees of freedom for averaged values are the number of replicated experiments, less one (n-1). An example of a different number of degrees of freedom is the use of least-squares regression parameters, such as the slope or intercept of a line, where the degrees of freedom is the number of regression data points less two. The macro uses input boxes to prompt the user for the
We evaluate our students¶ ability to transfer the recipe and tools for analysis of a new exam question where they are allowed to use their Excel worksheets and macros from the class exercises. We find that over 90% of the students are able to transfer their skills from class in the exam.
We are also beginning to see improvements in uncertainty analysis by students in our lab courses. Evidence includes an increased discussion and application of analysis of uncertainty in lab reports. Students are also careful to include estimates of uncertainty in all final reported values. Although we warn the students that they will need these tools in courses later in the program, some students are in the habit of compartmentalizing their learning. Once they are finished with the computational methods course, they do not automatically make the connection of applying the recipe later in the program. However, when we provide them with a copy of the Excel worksheet and macros from the wood density exercises, they are able to quickly relearn and apply these skills.
In one particularly complicated lab analysis, students use the macro to estimate the uncertainty in the calculation of chemical equilibrium constants. Experimental measurements of volume and mass to calculate reagent concentration and extent of reaction are fed into a worksheet set up to perform a complex series of stoichiometric mass conservation calculations to arrive at a value of the equilibrium constant. These calculations may be spread across multiple worksheets. Propagating the uncertainty through this involved series of calculations by hand is tedious and prone to mistakes. The JITTER macro efficiently performs the analysis requiring little effort setting up the worksheets for the macro inputs. The students also appreciate the additional VBA programming skills developed as part of this exercise and report using this additional skill in academic and industrial settings.
Conclusions
A simple hands-on active-learning exercise provides students with experience collecting and analyzing experimental data with random and systematic uncertainties. Students create an Excel worksheet that serves as a template of a recipe for calculating the propagation of measurement uncertainty in engineering analysis. This worksheet template, coupled with VBA macros, gives the students powerful tools for including measures of reliability in their calculated results. By making the process simple, relatively easy, and painless, students who formerly avoided uncertainty analysis are now more willing and able to conduct proper uncertainty analysis.
Similar tools may be developed in other computational tools, such as Mathcad or Matlab. However, we focus on Excel knowing that most of our graduates will have access to this software and make extensive use of it for engineering calculations wherever they are employed.
Nomenclature
c = sensitivity coefficient D = diameter, cm f = relationship between input variables and output variable L = length, cm m = mass, gm n = number of replicated measurements
s = sample standard deviation t = coverage factor, or Student¶s t-statistic u (^) R = random uncertainty or standard error u (^) x = combined uncertainty in measurements u (^) Z = systematic uncertainty V = volume, cm^3 v (^) x = degrees of freedom W = width, cm x = input variable from experimental measurements y = output value calculated from input values į = readability İ = perturbation in x U = density, gm/cm^3
Bibliography
Biography
RICHARD DAVIS is professor and head of chemical engineering at the University of Minnesota Duluth. He received his BS and PhD degrees in Chemical Engineering from Brigham Young University and the University of California Santa Barbara, respectively. He teaches courses in computational methods and unit operations. His research interests include modeling and simulation of mineral processing, air pollution control, and separations.