
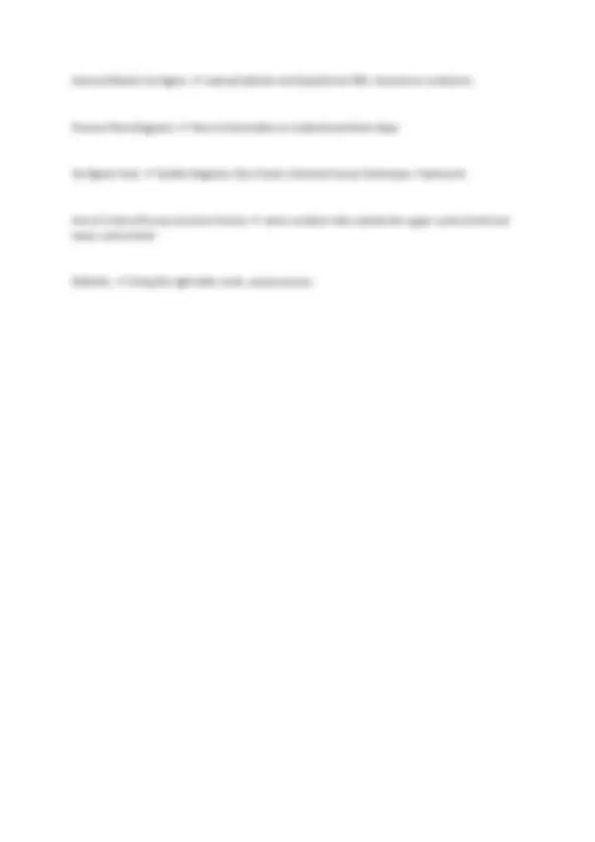
Study with the several resources on Docsity
Earn points by helping other students or get them with a premium plan
Prepare for your exams
Study with the several resources on Docsity
Earn points to download
Earn points by helping other students or get them with a premium plan
Community
Ask the community for help and clear up your study doubts
Discover the best universities in your country according to Docsity users
Free resources
Download our free guides on studying techniques, anxiety management strategies, and thesis advice from Docsity tutors
Six Sigma Complete Methodology Guide with Key Concepts and Exam Practice
Typology: Exams
1 / 3
This page cannot be seen from the preview
Don't miss anything!
Six Sigma Management Philosophy ✔ well developed approach to quality improvement, uses statistics and management by fact, is effective in manufacturing and services firms Six Sigma ✔ A comprehensive and flexible system for achieving, sustaining and maximizing business success. Driven by a close understanding of customer needs, disciplined use of facts, data, and statistical analysis and diligent attention to managing, improving, and reinventing business processes. Sigma ✔ amount of variation in a process around the mean value for that process 6 Sigma ✔ 3.4 defects per million 5 Sigma ✔ 230 defects per million 4 Sigma ✔ 6,210 defects per million 3 Sigma ✔ 66,800 defects per million 2 Sigma ✔ 308,000 defects per million 1 Sigma ✔ 690,000 defects per million Measure of Central Tendency ✔ what the average piece/metric looks like Measure of Dispersion ✔ how the data looks around median; range, sample variation and deviation In Control Process (Control Charts) ✔ when variation falls within the upper control limit and lower control limit
Quality Function Deployment (QFD) ✔ how to get where we want to go, plan Pareto ✔ 80/20 rule, critical few vs. trivial many Design of Experiments (DOE) ✔ setting up a controlled experiment to find the cause of difference Process ✔ Measure, Analyze, Improve, Control Measure ✔ Identify customer needs and quality defect levels, find goals Analyze ✔ Determine root causes of defects, look for patterns Improve ✔ Permanently identify root causes, make a change Control ✔ Maintain gains over time, continuous improvement Six Sigma Key Roles ✔ Leadership team, Champions, Master Black Belts (Mentors), Black Belts (Experts), Green Belts (Participants) Leadership Group ✔ Top Level (money making decision makers), select projects and allocate resources Champions ✔ coaching, motivate Master Black Belts (Mentors) ✔ coach and support project leads, train on tools Black Belts (Experts) ✔ trained experts, project team leaders Green Belts (Participants) ✔ trained on tools, participate on teams