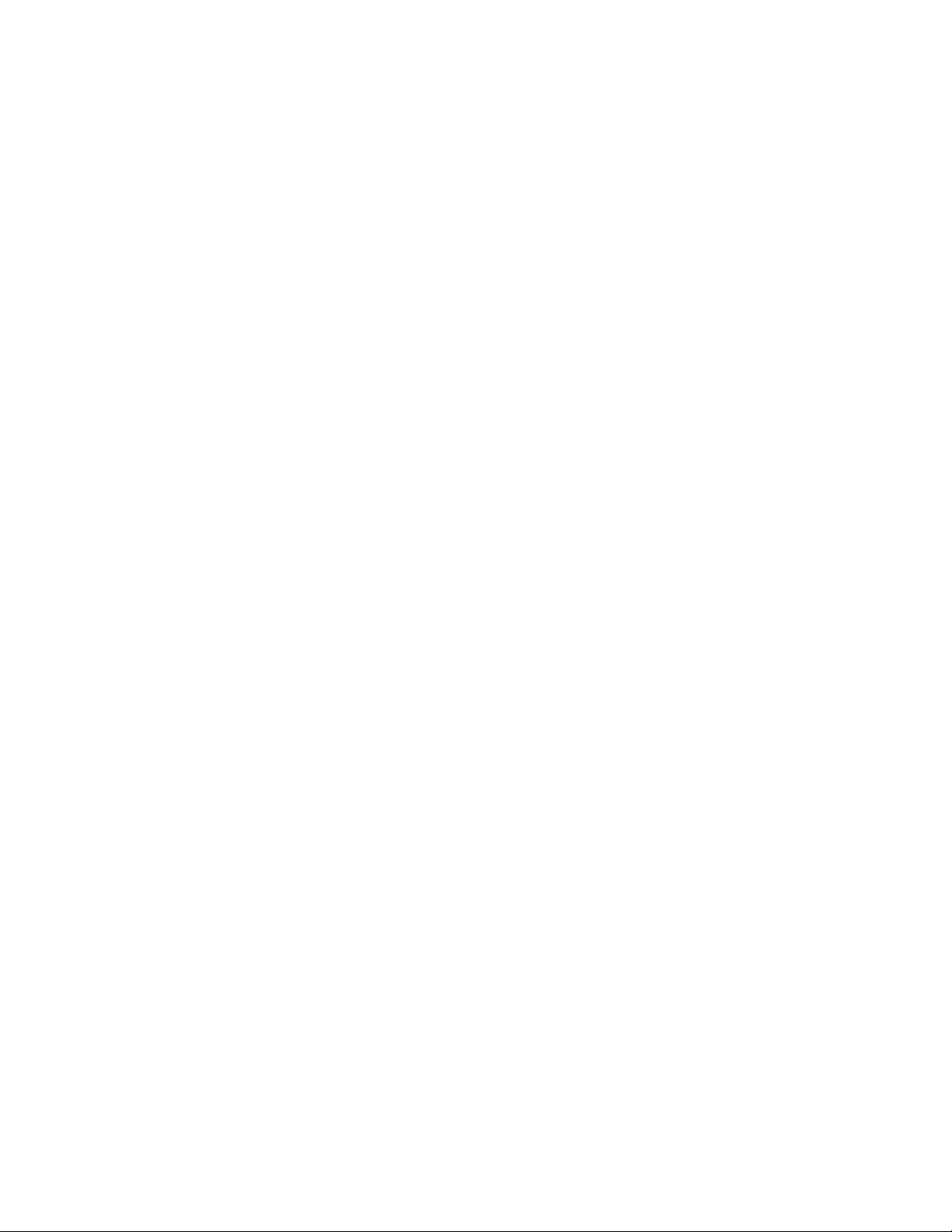
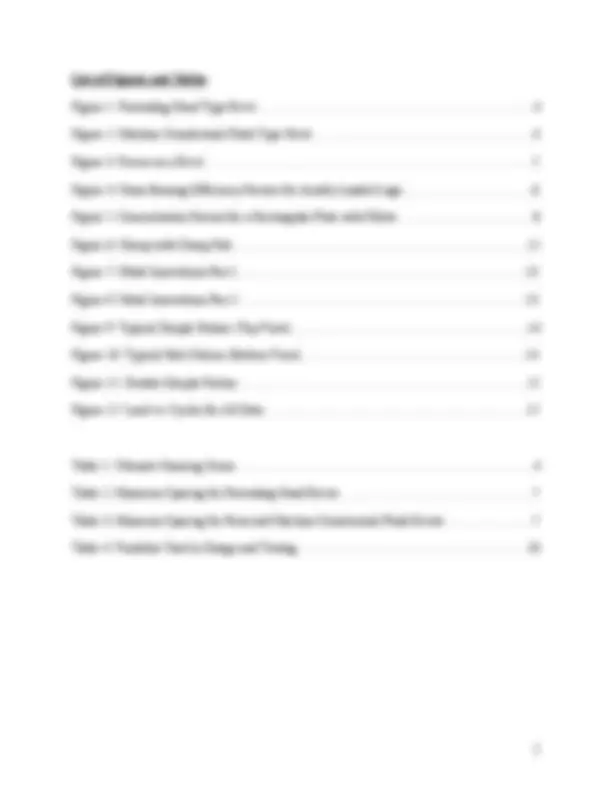
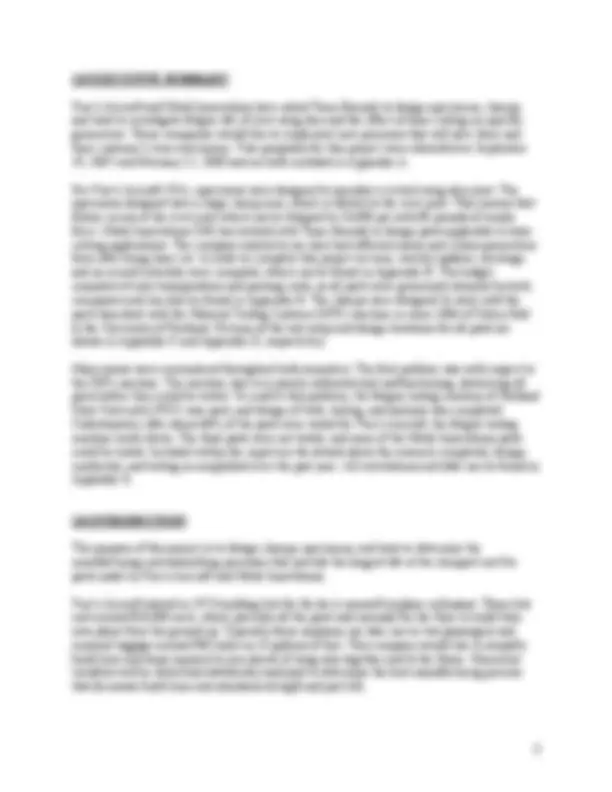
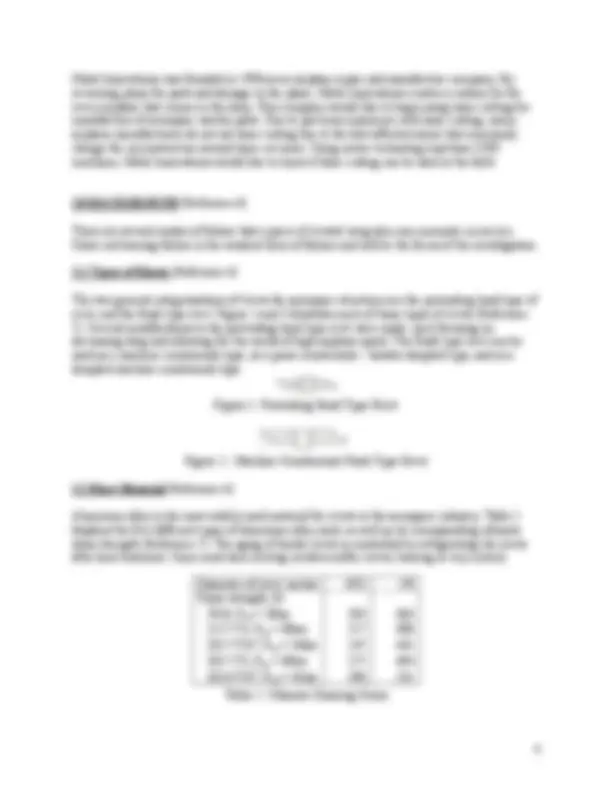
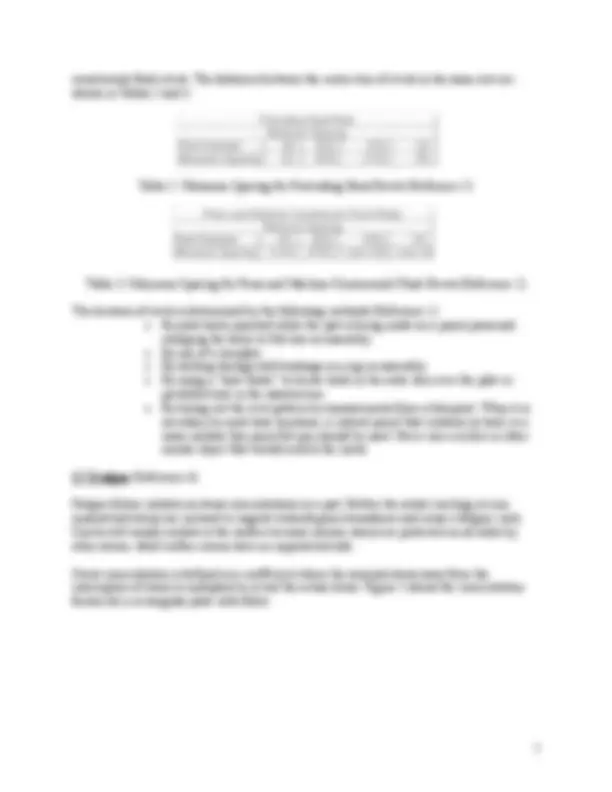
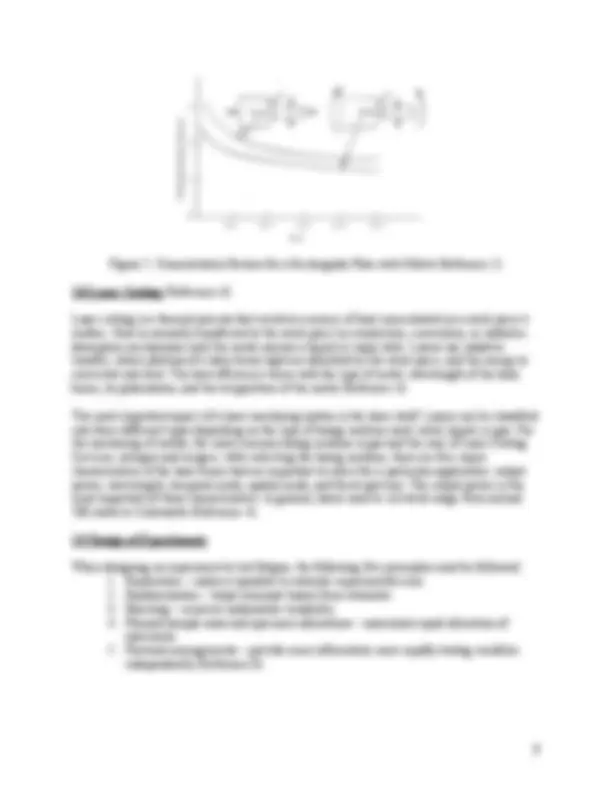
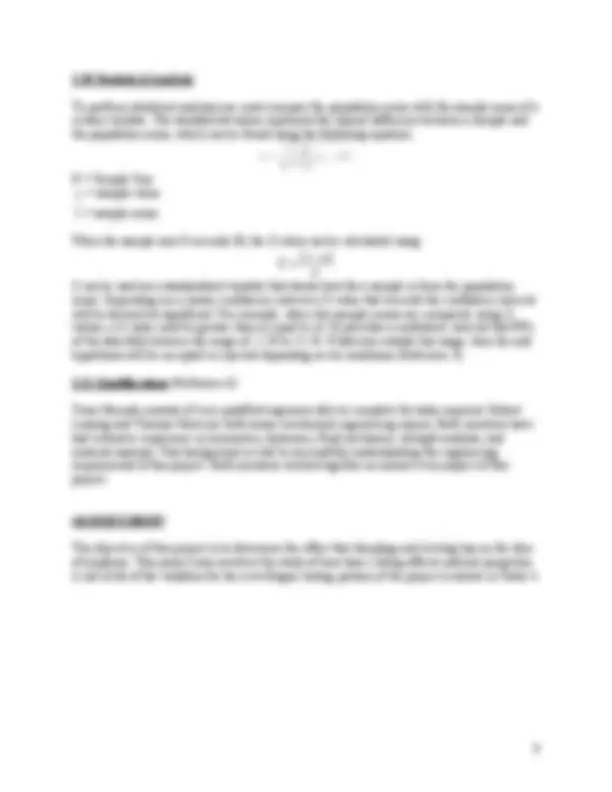
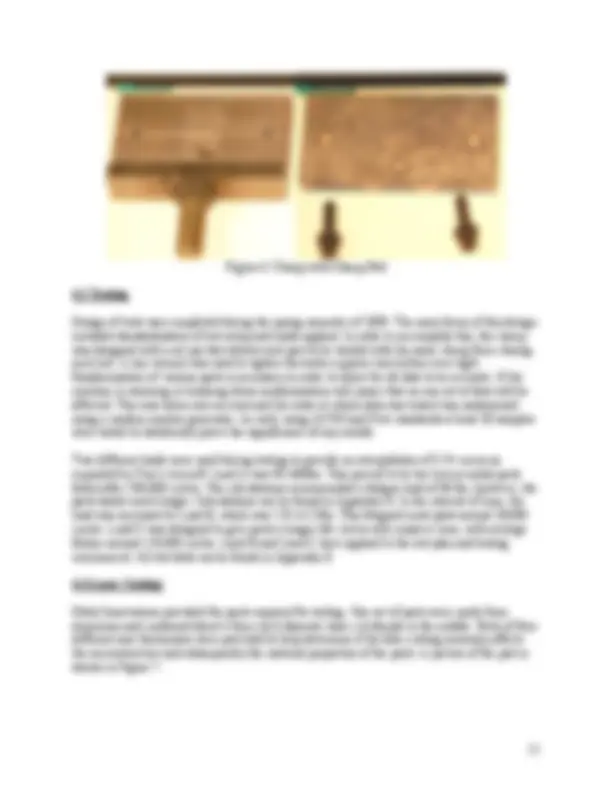
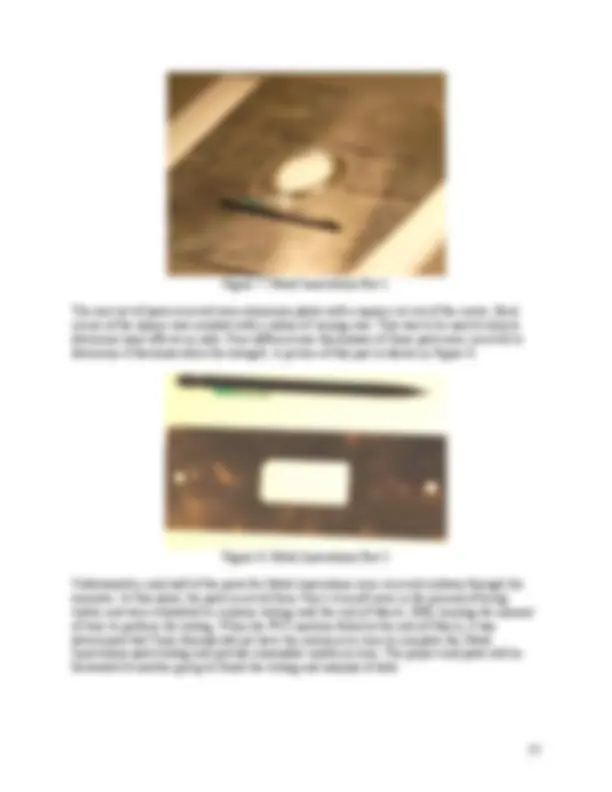
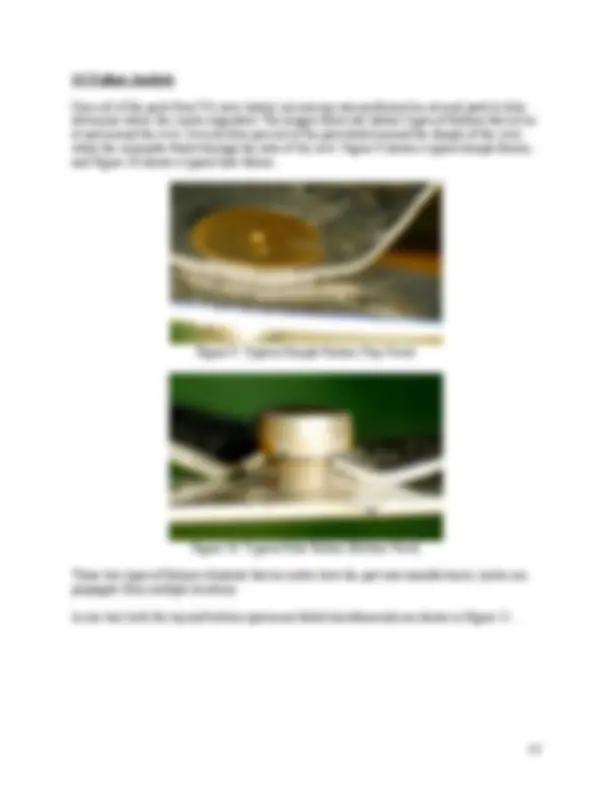
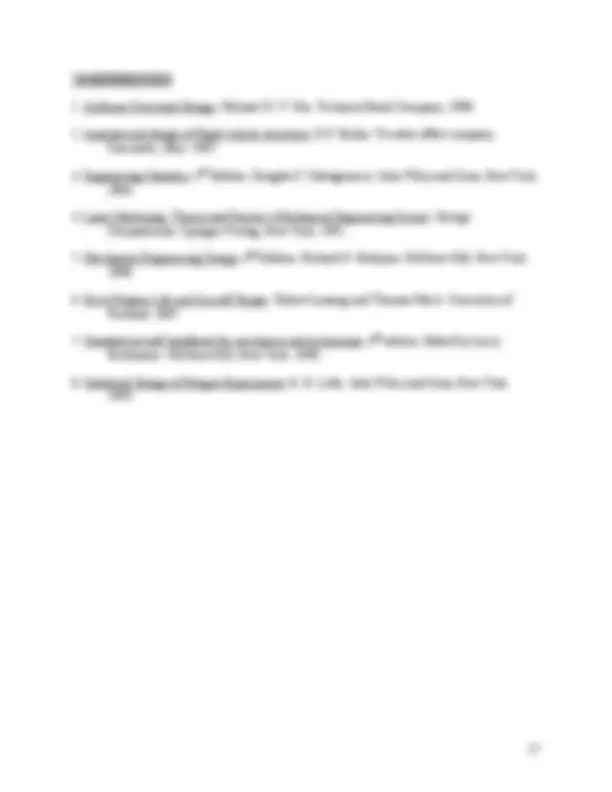
Study with the several resources on Docsity
Earn points by helping other students or get them with a premium plan
Prepare for your exams
Study with the several resources on Docsity
Earn points to download
Earn points by helping other students or get them with a premium plan
Community
Ask the community for help and clear up your study doubts
Discover the best universities in your country according to Docsity users
Free resources
Download our free guides on studying techniques, anxiety management strategies, and thesis advice from Docsity tutors
A report submitted to dr. Lulay, professor me 482, by team booyah, test engineers, on their investigation into the manufacturing and assembling processes that provide the longest life at the cheapest cost for parts made by van’s aircraft and metal innovations. The report covers the design of clamps, specimens, and tests to determine the best manufacturing process that decreases build time and maintains strength and part life. The study also explores metal innovations' desire to use laser cutting for aerospace parts and the impact of laser cutting on rivet wing skin, specifically focusing on rivet types, strength, and fatigue.
Typology: Study Guides, Projects, Research
1 / 18
This page cannot be seen from the preview
Don't miss anything!
Rivet Fatigue Life and Aircraft Repair Department of Mechanical Engineering University of Portland Senior Design – ME 482 April 1 7 , 2008 Report Submitted to: Dr. Lulay, Professor ME 482 Report Submitted by: Team Booyah, Test Engineers Robert Lansing Thomas Mock
Appendices Design Proposal…………………………………………………………………………………..A Weekly Updates…………………………………………………………………………………..B Design Schematics………………………………………………………………………………..C MTS/Instron Machine Pictures…………………………………………………………………...D
Van’s Aircraft and Metal Innovations have asked Team Booyah to design specimens, clamps, and tests to investigate fatigue life of rivet wing skin and the effect of laser cutting on specific geometries. These companies would like to implement new processes that will save them and their customer’s time and money. Two proposals for this project were submitted on September 19, 2007 and February 12, 2008 and are both included in Appendix A. For Van’s Aircraft (VA), specimens were designed to simulate a riveted wing skin joint. The specimens designed have a large clamp area, which is filleted to the rivet joint. This ensures that failure occurs at the rivet joint which can be fatigued to 34 ,000 psi with 88 pounds of tensile force. Metal Innovations (MI) has worked with Team Booyah to design parts applicable to laser cutting applications. The company wanted to see how heat affected zones and certain geometries form after being laser cut. In order to complete this project on time, weekly updates, meetings, and an overall schedule were compiled, which can be found in Appendix B. The budget consisted of only transportation and parking costs, as all parts were generously donated by both companies and can also be found in Appendix B. The clamps were designed to work with the parts described with the Material Testing Systems (MTS) machine in room 1006 of Shiley Hall at the University of Portland. Pictures of the test setup and design iterations for all parts are shown in Appendix C and Appendix D, respectively. Many issues were encountered throughout both semesters. The first problem was with respect to the MTS machine. The machine was very poorly calibrated and malfunctioning, destroying all parts before they could be tested. To resolve this problem, the fatigue testing machine at Portland State University (PSU) was used, and design of tests, testing, and analysis was completed. Unfortunately, after about 60% of the parts were tested for Van’s Aircraft, the fatigue testing machine broke down. The final parts were not tested, and none of the Metal Innovations parts could be tested. Included within the report are the details about the research completed, design conducted, and testing accomplished over the past year. All calculations and data can be found in Appendix E. 2.0 INTRODUCTION The purpose of this project is to design clamps, specimens, and tests to determine the manufacturing and assembling processes that provide the longest life at the cheapest cost for parts made by Van’s Aircraft and Metal Innovations. Van’s Aircraft started in 1973 building kits for the do-it-yourself airplane enthusiast. These kits cost around $20,000 each, which provides all the parts and manuals for the flyer to build their own plane from the ground up. Typically these airplanes can take one to two passengers and minimal luggage around 900 miles on 42 gallons of fuel. This company would like to simplify build time and steps required to join sheets of wing skin together and to the frame. Numerous variables will be tested and statistically analyzed to determine the best manufacturing process that decreases build time and maintains strength and part life.
Metal Innovations was founded in 1996 as an airplane repair and manufacture company. By reviewing plans for parts and damage to the plane, Metal Innovations creates a custom fix for every airplane that comes in the shop. This company would like to begin using laser cutting for manufacture of aerospace worthy parts. Due to previous experience with laser cutting, many airplane manufacturers do not use laser cutting due to the heat affected zones that commonly change the microstructure around laser cut areas. Using newer technology and laser CNC machines, Metal Innovations would like to know if laser cutting can be used in the field. 3.0 BACKGROUND (Reference 6) There are several modes of failure that a piece of riveted wing skin can encounter in service. Shear-out bearing failure is the weakest form of failure and will be the focus of the investigation. 3.1 Types of Rivets (Reference 6) The two general categorizations of rivets for aerospace structures are the protruding head type of rivet, and the flush type rivet. Figure 2 and 3 illustrates each of these types of rivets (Reference 7 ). Several modifications to the protruding head type rivet were made, each focusing on decreasing drag and allowing for the needs of high airplane speed. The flush type rivet can be used as a machine countersunk type, as a press countersunk – double dimpled type, and as a dimpled machine countersunk type. Figure 1: Protruding Head Type Rivet Figure 2 : Machine Countersunk Flush Type Rivet 3.2 Rivet Material (Reference 6) Aluminum alloy is the most widely used material for rivets in the aerospace industry. Table 1 displays the five different types of aluminum alloy used, as well as its corresponding ultimate shear strength (Reference 7). The aging of harder rivets is controlled by refrigerating the rivets after heat treatment. Since most skin riveting involves softer rivets, bearing is very critical. Table 1: Ultimate Shearing Stress Diameter of rivet, inches 3/32 1/ Shear strength, lb: 5056, Fsu = 28ksi 203 363 2117 - T3, Fsu = 30ksi 217 388 2017 - T31a, Fsu = 34ksi 247 442 2017 - T3, Fsu = 38ksi 275 494 2024 - T a , Fsu = 41ksi 296 531
t
: Double shear strength = Basic allowable double shear strength "[ 1! 0. 13 "(! 1. 5 )] t
Edge distance should not be less than = 1. 5 D e because bulging at the end of the sheet might occur. e represents the edge distance measured from the edge of the plate to the center of the hole, and D is the diameter.
3. 4 Shear-Out Bearing Strength (Reference 6) Failure due to shear-out is covered by a single calculation based on empirical curves. The ultimate allowable tension load is given in the following equation: Pbry = Kbr! Ftu! A br Kbr is the shear bearing efficiency factor and can be found in Figure 1. Ftu is the ultimate tensile strength of the material, and Abr is smallest bearing area of bushing on the pin or the lug. Figure 4: Shear-Bearing Efficiency Factors for Axially Loaded Lugs (Reference 1) 3. 5 Rivet Size (Reference 6) Common rivet sizes are 1/8, 5/32, 3/16, and 1/4 inch diameter rivets, because they are easy to handle. In sheet splices, larger size rivets should not be used because the sheet might buckle. The ideal joint is when the allowable rivet shear strength and the bearing strength of the sheets are practically equal to one another. 3. 6 Rivet Spacing and Location (Reference 6) The edge distance in a joint should be greater than or equal to two times the rivet diameter for protruding head rivets, and two and a half times the rivet diameter for press and machine
countersunk flush rivets. The distances between the center-line of rivets in the same row are shown in Tables 2 and 3. Table 2: Minimum Spacing for Protruding Head Rivets (Reference 2) Table 3: Minimum Spacing for Press and Machine Countersunk Flush Rivets (Reference 2) The location of rivets is determined by the following methods (Reference 1): o By pilot holes punched while the part is being made on a punch press and enlarging the holes to full size on assembly. o By use of a template. o By drilling through drill bushings in a jog on assembly. o By using a “hole finder” to locate holes in the outer skin over the pilot or predrilled hole in the substructure. o By laying out the rivet pattern by measurements from a blueprint. When it is necessary to mark hole locations, a colored pencil that contains no lead, or a water soluble fine point felt pen should be used. Never use a scriber or other similar object that would scratch the metal. 3.7 Fatigue (Reference 6) Fatigue failure initiates as stress concentrations in a part. Before the initial cracking occurs, mismatched atoms are inclined to migrate towards grain boundaries and cause a fatigue crack. Cracks will usually initiate at the surface because interior atoms are protected on all sides by other atoms, while surface atoms have an unprotected side. Stress concentration is defined as a coefficient where the nominal stress away from the interruption of stress is multiplied to reveal the actual stress. Figure 5 shows the concentration factors for a rectangular plate with fillets.
3.10 Statistical Analysis To perform statistical analysis one must compare the population mean with the sample mean of a certain variable. The standard deviation represents the typical difference between a sample and the population mean, which can be found using the following equation: N = Sample Size x i = sample value x = sample mean When the sample size N exceeds 30, the Z-value can be calculated using: ! ( " μ) = x Z Z can be used as a standardized variable that shows how far a sample is from the population mean. Depending on a chosen confidence interval a Z-value that exceeds the confidence interval will be deemed as significant. For example, when two sample means are compared, using Z- values, a Z-value must be greater than or equal to ±2.58 provides a confidence interval that 99% of the data falls between the range of - 2.58 to +2.58. If data lies outside this range, then the null hypothesis will be accepted or rejected depending on its conditions (Reference 3). 3.11 Qualifications (Reference 6) Team Booyah consists of very qualified engineers able to complete the tasks required. Robert Lansing and Thomas Mock are both senior mechanical engineering majors. Both members have had extensive experience in kinematics, dynamics, fluid mechanics, strength analysis, and material analysis. This background is vital to successfully understanding the engineering requirements of this project. Both members worked together on almost every aspect of this project. 4.0 DISCUSSION The objective of this project is to determine the effect that dimpling and riveting has on the skin of airplanes. This project also involves the study of how laser cutting affects material properties. A list of all of the variables for the rivet fatigue testing portion of the project is shown in Table 4.
Material Thickness Punched Hole Size Edge Distance Drilled (B efore Deburr & Dimple) Deburred (Before Dimple) Dimpled (Y With Punch Dirction) 2024 - T 3 0. 016 0. 144 2 D+ N Y Y 2024 - T 3 0. 016 0. 144 2 D+ N Y N 2024 - T 3 0. 016 0. 144 2 D+ N N N 2024 - T 3 0. 016 0. 144 2 D+ N N Y 2024 - T 3 0. 016 0. 128 2 D+ 0. 144 Y Y 2024 - T 3 0. 016 0. 128 2 D+ 0. 144 Y N 2024 - T 3 0. 016 0. 128 2 D+ 0. 144 N N 2024 - T 3 0. 016 0. 128 2 D+ 0. 144 N Y 2024 - T 3 0. 032 0. 144 2 D+ N Y Y 2024 - T 3 0. 032 0. 144 2 D+ N Y N 2024 - T 3 0. 032 0. 144 2 D+ N N N 2024 - T 3 0. 032 0. 144 2 D+ N N Y 2024 - T 3 0. 032 0. 128 2 D+ 0. 144 Y Y 2024 - T 3 0. 032 0. 128 2 D+ 0. 144 Y N 2024 - T 3 0. 032 0. 128 2 D+ 0. 144 N N 2024 - T 3 0. 032 0. 128 2 D+ 0. 144 N Y Table 4: Variables Used in Design and Testing (Reference 6) The MTS Load Frame in room 1006 of the Engineering Building at the University of Portland was originally going to be used to perform this testing. However, due to poor calibration, testing was moved to Portland State University. Pictures of both machines are shown in Appendix C. 4.1 Test Specimens (Reference 6) The focus of the design of the test specimens was to center the stress concentrations at the rivet. This ensures failure at the rivet every time, assuming appropriate clamping force and uniaxial load is applied. The fillet located on these parts is also of significant size as to not contain critical stresses for the part. Drawings of all design iterations as well as the final design are illustrated in Appendix D. Initially, a design consisting of sloping curves leading to the rivet was conceived. However, having two radii over complicates the design. This would lead to unnecessary manufacturing considerations when the stress concentrations are overwhelmingly centered at the rivet. The final design began to take shape when only one radius was put in place to neck the part down from 2.362 inches to 0.625 inches. This shoulder does not contain any significant stress concentrations when designed in Solidworks. Final adjustments were made by expanding the height and width of the part to accommodate sufficient clamping area. The edge distance between the rivet hole and the leading edge is 0.25 inches on both the large rivet and small rivet specimens. This is greater than 1.5 times the diameter of the hole as suggested by Bruhn (Reference 2). Since the distance between rivets on typical wing skin is only one inch, this was simulated in the test specimens by distancing the hole at least 0.5 inches from
Figure 6: Clamp with Clamp Pad 4.3 Testing Design of tests was completed during the spring semester of 2008. The main focus of this design included standardization of test setup and loads applied. In order to accomplish this, the clamp was designed with a set pin that allows each part to be loaded with the same clamp force during each test. A hex wrench was used to tighten the bolts a quarter turn before over-tight. Randomization of various parts is necessary in order to allow for all data to be accurate. If the machine is warming or breaking down randomization will insure that no one set of data will be affected. This was taken into account and the order at which data was tested was randomized using a random number generator. As well, using ASTM and FAA standards at least 30 samples were tested to statistically prove the significance of any results. Two different loads were used during testing to provide an interpolation of S-N curves as requested by Van’s Aircraft. Load A was 90 ±80lbs. This proved to be too low as initial parts failed after 500,000 cycles. The calculations recommended a fatigue load of 88 lbs; however, the parts lasted much longer. Calculations can be found in Appendix E. In the interest of time, the load was increased to Load B, which was 150 ±125lbs. This fatigued most parts around 30, cycles. Load C was designed to give parts a longer life, but to still conserve time, with average failure around 150,000 cycles. Load B and Load C were applied to the test plan and testing commenced. All test data can be found in Appendix E.
4. 4 Laser Cutting Metal Innovations provided the parts required for testing. One set of parts were made from aluminum and contained about a three inch diameter laser cut dimple in the middle. Parts of four different size thicknesses were provided to help determine if the laser cutting seriously affects the microstructure and subsequently the material properties of the parts. A picture of the part is shown in Figure 7.
Figure 7: Metal Innovations Part 1 The next set of parts received were aluminum plates with a square cut out of the center. Each corner of the square was rounded with a radius of varying size. This was to be used to help to determine laser effects on radii. Four different size thicknesses of these parts were received to determine if thickness alters the strength. A picture of this part is shown in Figure 8. Figure 8 : Metal Innovations Part 2 Unfortunately, only half of the parts for Metal Innovations were received midway through the semester. At this point, the parts received from Van’s Aircraft were in the process of being tested, and were scheduled to continue testing until the end of March, 2008, limiting the amount of time to perform the testing. When the PSU machine failed at the end of March, it was determined that Team Booyah did not have the resources or time to complete the Metal Innovations parts testing and provide reasonable results on time. The project and parts will be forwarded to another group to finish the testing and analysis of data.
Figure 11: Double-Dimple Failure
4. 6 Statistical Analysis Statistical analysis was completed by comparing the sample mean of certain processes to the total population mean. For example, with the null hypothesis that drilling is not better than punching parts to final size, the mean value of all data was compared to that of drilled or punched data. Z-values of - 1.66 and 3.16 were calculated, respectively. Assuming a confidence interval of Z = ±2.58 one can reject the null hypothesis by saying that the means are significantly different (Reference 3). One can say that punching is better than drilling parts to final size by running a second test. This analysis was mainly conducted on parts that were submitted to load B (150 ±125lbs) conditions with the larger rivet. This was done because this population had the largest sample size and could provide the best answers as to statistical significance. The data table showing these completed calculations and sample calculations are located in Appendix E. 4.7 S-N Curves S-N, load vs. fatigue life, curves were calculated using all data available. Some curves were used to compare various variables by graphing two curves on the same graph and a fifth can be used in design at Van’s Aircraft. This fifth curve is displayed in Figure 1 2. Load (ksi) vs. Cycles (N) y = - 2. 8266 Ln(x) + 44. 493 0 2 4 6 8 10 12 14 16 18 20 0 20000 40000 60000 80000 100000 120000 140000 160000 180000 Cycles (N) Load (ksi) All Data )Log. (All Data Figure 1 2 : Load vs. Cycles for All Data
The comparative S-N curves can be found in Appendix E. 5.0 CONCLUSIONS Testing showed that not only did the clamp withstand the forces applied, but the parts failed at the rivet through dimple and hole failure. This mode of failure is different that that calculated due to the nature of fatigue and stress concentrations. The staff and faculty at PSU have been instrumental in helping Team Booyah complete a majority of the testing required. By assisting with test design alterations, Dr. Bill Wood and Mr. Kevin Cuddihy have aided in the tweaking of loads and rate at which fatigue testing is conducted. Through the testing of 52 parts at two load types, enough data has been collected to make confident conclusions. By grouping data by process type and using statistical analysis to determine the significance of certain variability in the data, Team Booyah concludes that parts that fail through the hole of the rivet will, on average, last longer with regard to fatigue cycles than those parts that fail around the dimple of the rivet. As well, it is interesting to note that holes punched to final size also lasted significantly longer than those drilled to final size. This was true for both small and large rivet parts. Both deburring and punch direction did not seem to have an effect on fatigue cycle life of a part. It is recommended to Van’s Aircraft that new manufacturing processes be put into place to punch and dimple the rivet holes on wing skin in the factory to aid customers in the building of their airplanes and to increase productivity and revenue. 6.0 RECOMMENDATIONS Throughout the year, there were several things that could have been done to make this project even more successful. The first item involved the communication with Metal Innovations. When originally meeting with this company, Team Booyah was not entirely sure the type of results that they wanted researched. The main source of communication was via e-mail, which increased response time to over two weeks at some points. The company was located in Aurora, OR, so traveling back and forth weekly was not ideal. When a problem like this arises, it is recommended to sort out all questions early, have a clear concept of what is expected, and set out a detailed schedule of times to meet. The biggest problem encountered was finding a fatigue testing machine that worked for the parts created. Once the fatigue testing machine was identified and available at PSU, more time was taken getting the machine ready and adapters made to accommodate the new machine. Dr. Wood and his team were a huge help in completing this testing, but more time should have been allotted for testing to accommodate for issues like machine breakage or part changes.