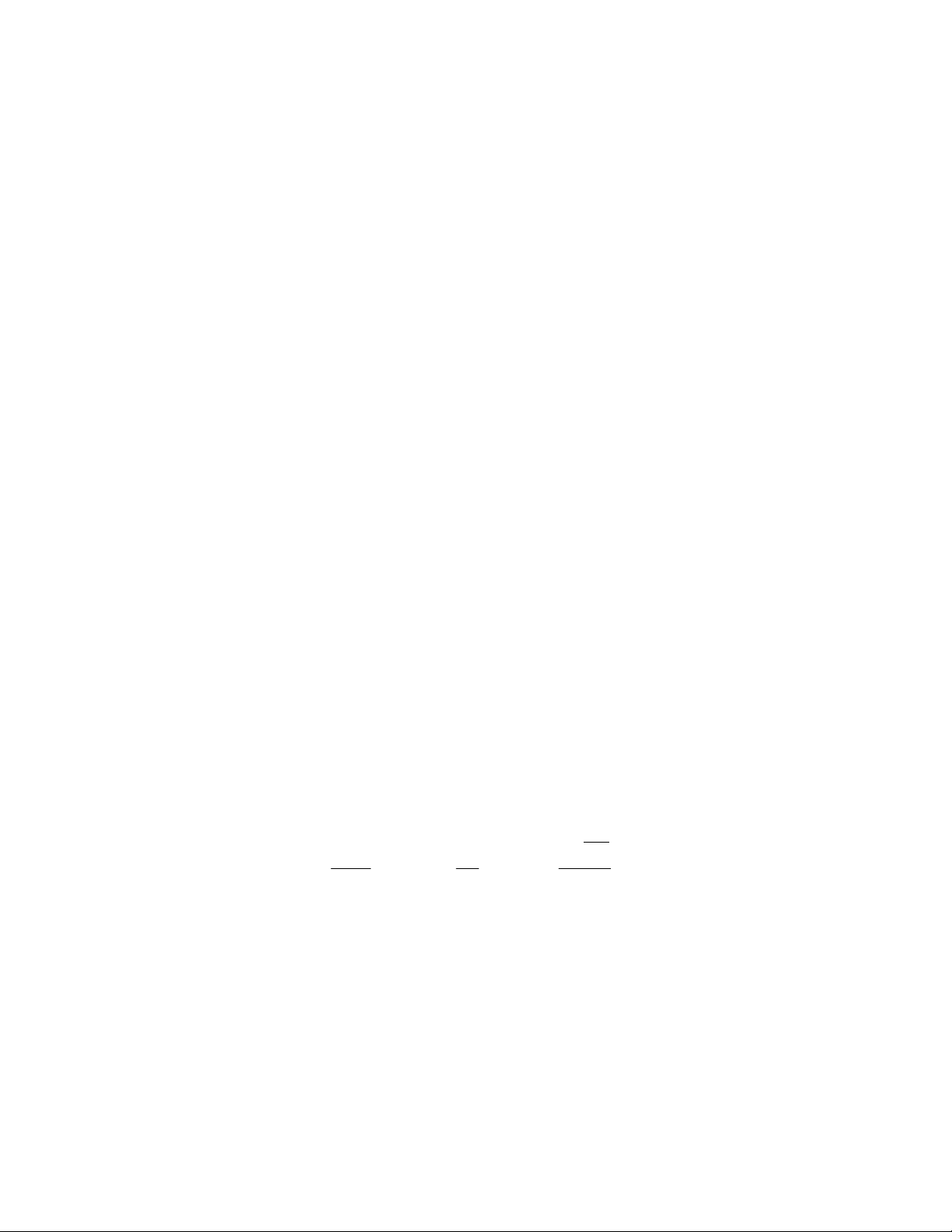
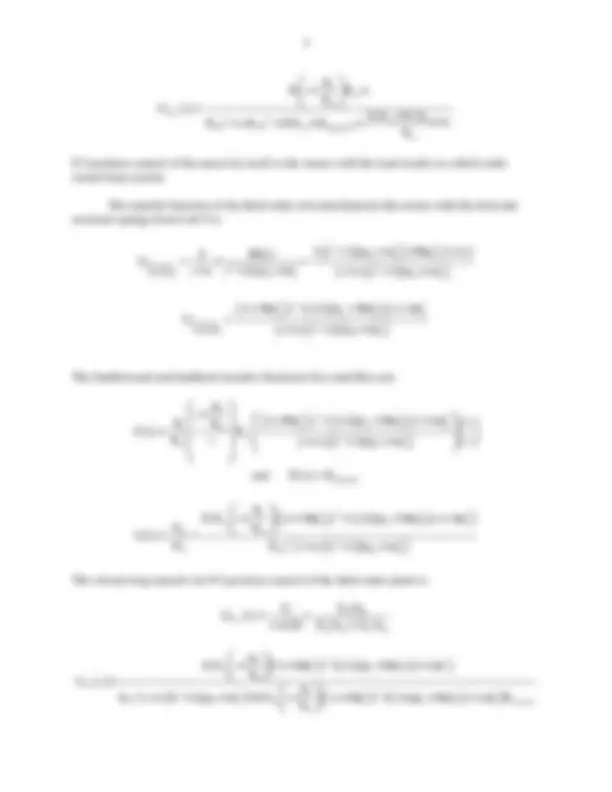
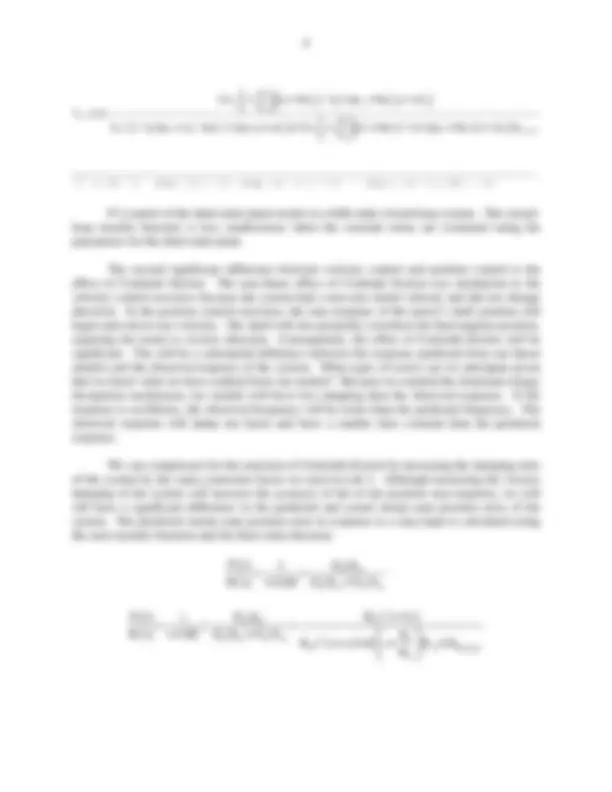
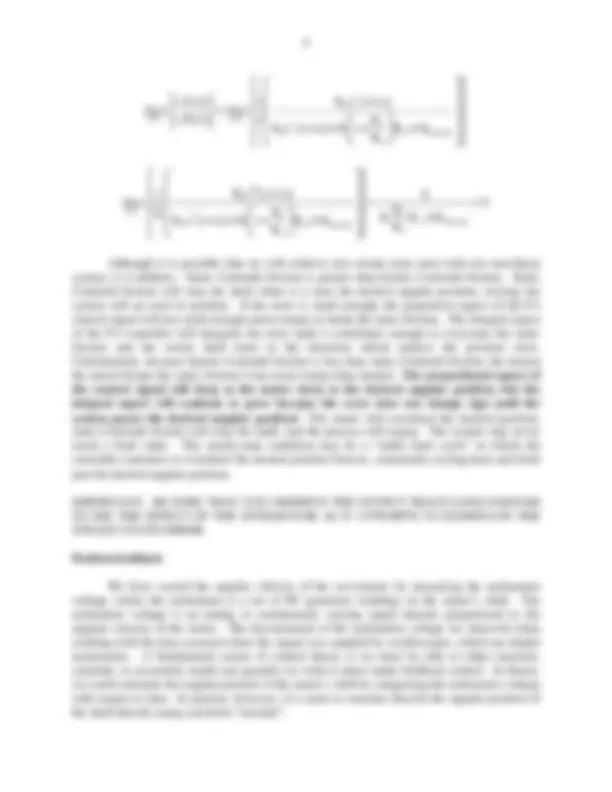
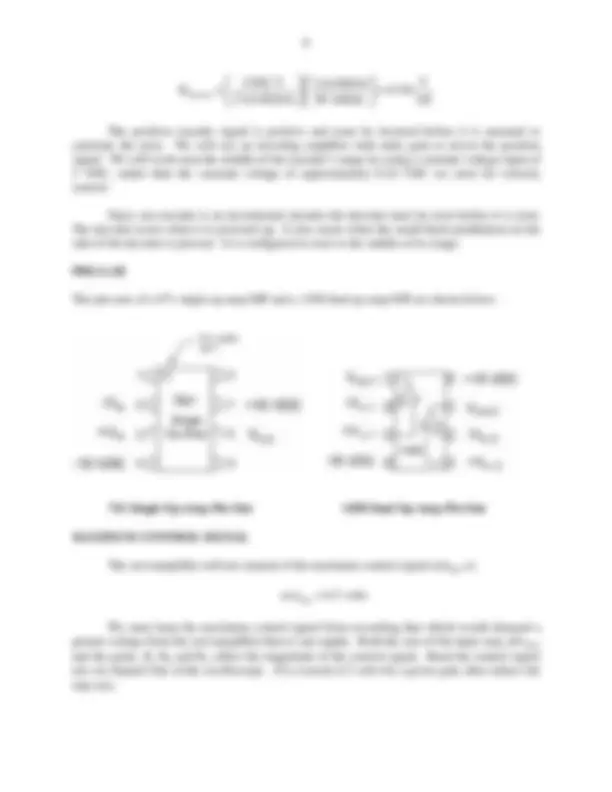
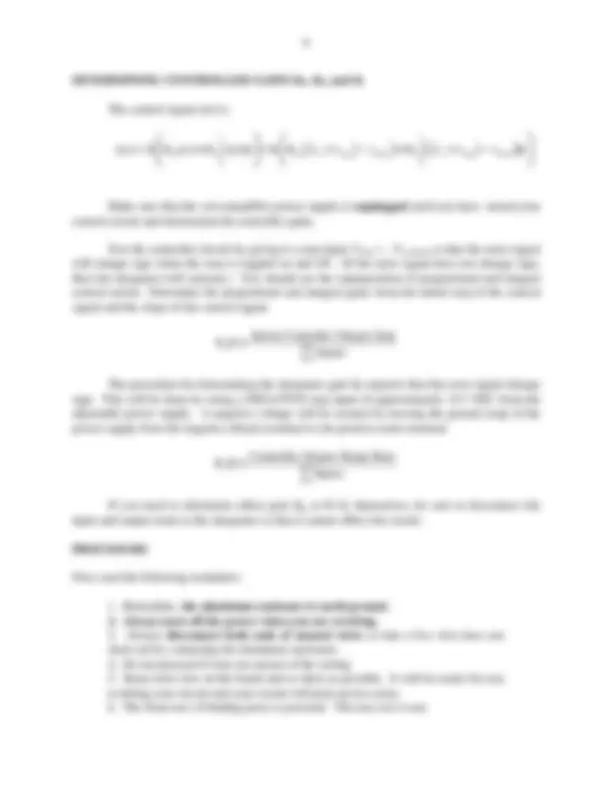
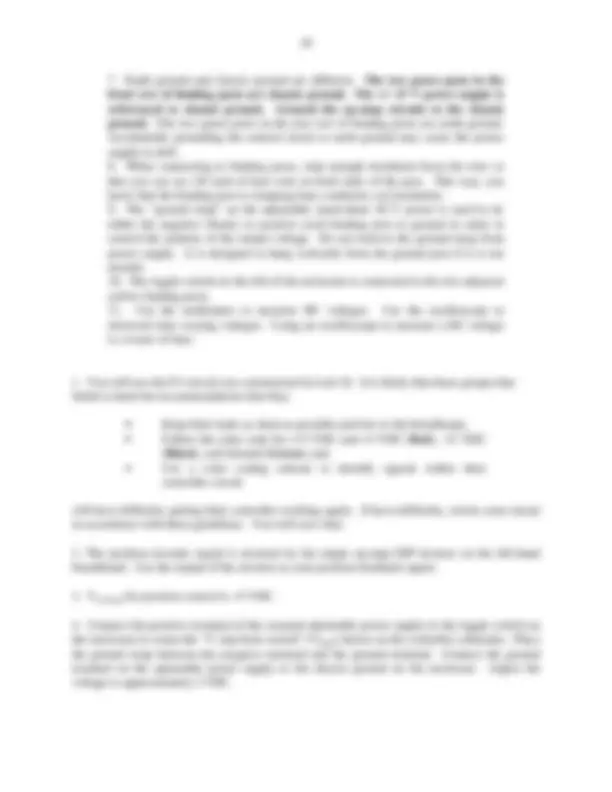
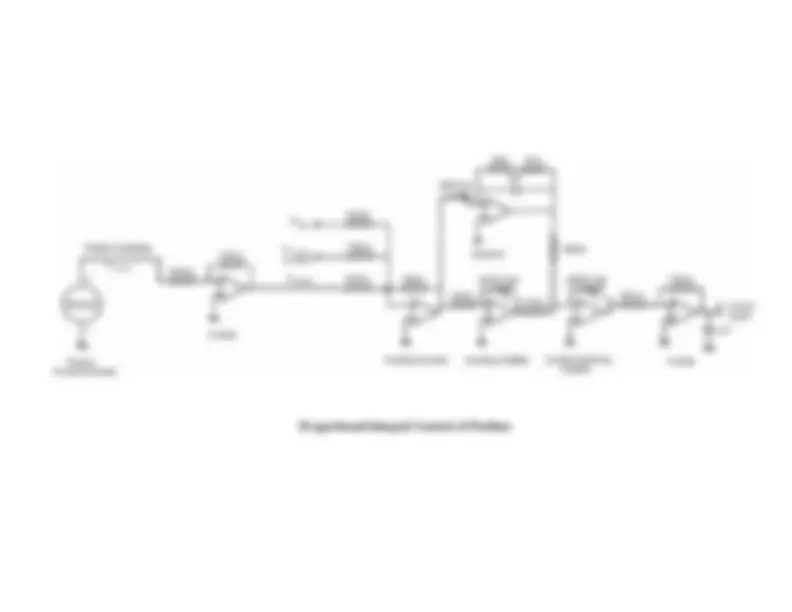
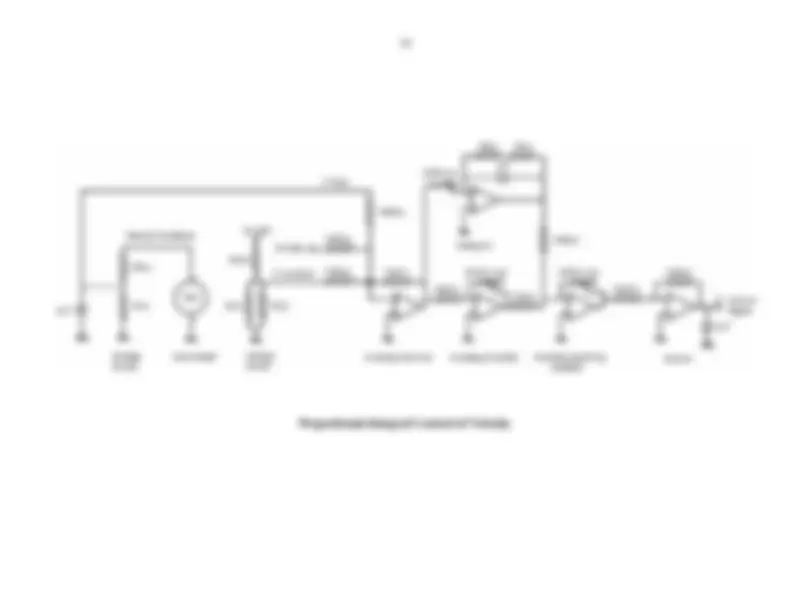
Study with the several resources on Docsity
Earn points by helping other students or get them with a premium plan
Prepare for your exams
Study with the several resources on Docsity
Earn points to download
Earn points by helping other students or get them with a premium plan
Community
Ask the community for help and clear up your study doubts
Discover the best universities in your country according to Docsity users
Free resources
Download our free guides on studying techniques, anxiety management strategies, and thesis advice from Docsity tutors
The concept of p-i position control in a third order servomechanism. It explains the role of proportional and integral actions in producing control signals, the effect of coulomb friction, and the determination of controller gains. The document also mentions the use of encoders and the importance of grounding in control circuits.
Typology: Lab Reports
1 / 14
This page cannot be seen from the preview
Don't miss anything!
© Dr. Seeler Department of Mechanical Engineering Fall 2004 Lafayette College ME 479: Dynamic Systems, Controls and Mechatronics Laboratory
Lab 11: Proportional-Integral (P-I) Control of Angular Position
The objective of Lab 11 is to place the angular position of servomechanism under proportional and integral (P-I) control.
THEORETICAL BACKGROUND
Proportional – Integral (P-I) Control
Investigating P-I control in both the time domain and the root locus yields two complementary perspectives. The time domain interpretation views the proportional action and the integral action as simultaneously operating on the error signal and producing control signals which are summed to yield the output of the controller.
t P I 0
u t K K e t K e t dt
∫
The proportional action yields an instantaneous control action in response to an error. The integral action will increase the control signal in response to persistent error. We will be able to physically experience this aspect of P-I control when we place the servomotor under closed-loop feedback control. We the system is configured with the load inertia, manually rotate the inertia through an angular displacement and hold it there. You will feel the torque exerted by the controller increase as the integral action ramps up.
The root locus interpretation considers the effect of P-I control on the root locus of the closed-loop system. P-I controls adds an open-loop zero and a pole at the origin.
I I P P P
s U s (^) K K K K K K E s s s
The controller pole cannot be moved from the origin. The controller zero can be positioned on the real axis, within the limit of the controller gains. We will observed the effect of varying the controller gain as evidenced by the change of the frequency and damping ratio of the step response.
In Lab 10, we investigated P-I velocity control and found that we achieved excellent agreement between the closed-loop step responses predicted using control theory and the observed closed-loop step responses. We can attribute our accuracy to the facts that the open- loop plant transfer functions we used to predict the closed-loop step response were derived from
velocity step response data, which minimized the errors in the plant transfer functions, and that velocity control from a non-zero initial velocity was accurately described by linear plant transfer functions. The Coulomb friction torque acting on the motor shaft that we identified in Lab 2 could be neglected because the angular velocity was never zero and never changed direction.
In Lab 11, we will place the angular position of the servomotor’s shaft under proportional-integral control. Rather than feeding back angular velocity by reading the tachometer signal, we will feedback position using the digital position encoder on the motor’s shaft. There will be two significant differences between P-I position control and P-I velocity control. The first is the addition of an integrator in the feedforward path. We will still use the plant transfer functions we determined from the open-loop step responses in Lab 9, where output
plant M
s G s V s
=. We must add an integrator
to the closed-loop block diagram so as to integrate angular velocity Ω(s) and yield angular position Θ(s). NOTE: Keep in mind that we are in fact adding nothing to the servomechanism or to our controller. However, by using the position signal as our feedback, effectively add an integrator to the system.
Adding an integrator to the feedforward path increases the order of the closed loop system.
The closed-loop transfer for P-I position control for the motor by itself or the motor with the load is:
I P A P
s K K A G s K K s s a s
I A G H P CL G H G H (^2) I P A P
K s K A G N D K G s 1 GH D D N N (^) K K s s a K s K A K K
Encoder
I^2 2 2 A n n n n P CL P 2 3 n 2 2 n^ n 2 n^ A I^2 n^2 n n^2 2 n Encoder P
K K s K A B s A2 B a s A G s K K s s 2 a s 2a s a K K s K A B s A2 B a s A K K
⎛ (^) + ⎞ + ω + ζω + ω + ω ⎜ ⎟ = ⎝^ ⎠
G (^2) n + 4 s a ωs +P 2 Kζω (^) n + 2an K KA Encoder +K ω 2 A (^) +n 3 B (^) ω s (^2) P (^) K an K KA Encoder Kζω + A 2ω (^) n + (^2) n B +a ω 2 A (^) n+ B 2 s (^) AK K Encoder K ζω + A 2ω (^) n 2 + (^) n B aω (^) AK K (^2) + (^) nA s AK
P-I control of the third order plant results in a fifth order closed-loop system. The closed- loop transfer function is less cumbersome when the constant terms are evaluated using the parameters for the third order plant.
The second significant difference between velocity control and position control is the effect of Coulomb friction. The non-linear effect of Coulomb friction was minimized in the velocity control exercises because the system had a non-zero initial velocity and did not change direction. In the position control exercises, the step response of the motor’s shaft position will begin and end at zero velocity. The shaft will also generally overshoot the final angular position, requiring the motor to reverse direction. Consequently, the effect of Coulomb friction will be significant. The will be a substantial difference between the response predicted from our linear models and the observed response of the system. What types of errors can we anticipate given that we know what we have omitted from our models? Because we omitted the dominant energy dissipation mechanism, our models will have less damping than the observed response. If the response is oscillatory, the observed frequency will be lower than the predicted frequency. The observed response will damp out faster and have a smaller time constant than the predicted response.
We can compensate for the omission of Coulomb friction by increasing the damping ratio of the system by the same correction factor we used in Lab 3. Although increasing the viscous damping of the system will increase the accuracy of the of the position step response, we will still have a significant difference in the predicted and actual steady-state position error of the system. The predicted steady-state position error in response to a step input is calculated using the error transfer function and the final value theorem:
G H G H G H
E s (^1) D D R s 1 GH D D N N
2 G H P G H G H (^2) I P A P
E s (^1) D D K s s a R s 1 GH D D N N (^) K K s s a K s K A K K
Encoder
2 P s 0 s (^0 2) I P A P
1 E s^1 K s^ s^ a lim s lim s s R s s (^) K K s s a K s K A K K
→ → Encoder
s 0
lim s → s
2
(^2) I I P A Encoder A^ Encoder P P
s a (^0) 0 K K K s s a K s K A K K^ K A K K K
Although it is possible that we will achieve zero steady-state error with our non-linear system, it is unlikely. Static Coulomb friction is greater than kinetic Coulomb friction. Static Coulomb friction will stop the shaft when it is near the desired angular position, leaving the system will an error in position. If the error is small enough, the proportion aspect of the P-I control signal will not yield enough motor torque to break the static friction. The integral aspect of the P-I controller will integrate the error until it contributes enough to overcome the static friction and the motor shaft turns in the direction which reduces the position error. Unfortunately, because kinetic Coulomb friction is less than static Coulomb friction, the instant the motor breaks the static friction it has more torque than needed. The proportional aspect of the control signal will drop as the motor turns to the desired angular position, but the integral aspect will continue to grow because the error does not change sign until the system passes the desired angular position! The motor will overshoot the desired position, static Coulomb friction will stop the shaft, and the process will repeat. The system may never reach a final value. The steady-state condition may be a “stable limit cycle” in which the controller continues to overshoot the desired position forever, continually cycling back and forth past the desired angular position.
IMPORTANT: BE SURE THAT YOU OBSERVE THE OUTPUT TRACE LONG ENOUGH TO SEE THE EFFECT OF THE INTEGRATOR AS IT ATTEMPTS TO ELIMENATE THE STEADY-STATE ERROR.
Position feedback
We have sensed the angular velocity of the servomotor by measuring the tachometer voltage, where the tachometer is a set of DC generator windings on the motor’s shaft. The tachometer voltage is an analog or continuously varying signal linearly proportional to the angular velocity of the motor. The discretization of the tachometer voltage we observed when working with the data occurred when the signal was sampled by oscilloscopes, which are digital instruments. A fundamental axiom of control theory is we must be able to either measure, calculate, or accurately model any quantity we wish to place under feedback control. In theory, we could calculate the angular position of the motor’s shaft by integrating the tachometer voltage with respect to time. In practice, however, it is easier to measure directly the angular position of the shaft directly using a position “encoder”.
Quadrature Decoding Scheme Position in Square Wave Cycle Signal 0 o^90 o^180 o^270 o A 1 1 0 0 B 0 1 1 0
Encoder lines represented as a square wave. Sensors A and B, indicated by the circles, are shown 90o^ apart, or at quadrature.
In the illustration above, positive displacement of the square wave is from right to left, since sensor A is shown to the right of sensor B. A third, separate signal, the “index”, (called “channel Z” by Baldor) is provided by incremental encoders to indicate a complete revolution. Although we will not use the index signal, it can be used to extend the range of the decoder.
We will decode the position signal with a US Digital EDAC2, which stands for Encoder Digital to Analog Converter. The decoder is configured to output a 0 to 9.962 VDC signal for its full range of 0 to 4000 counts. The quadrature decoding of 500 lines per revolution of the motor yields 2000 counts per revolution. Hence, the decoder can count two full revolutions before it reaches its limit.
The position decoder constant is:
Encoder
9.962 V 1 revolution V K 0. 2 revolutions 2 radians rad
⎝ ⎠⎝ π ⎠
The position encoder signal is positive and must be inverted before it is summed to calculate the error. We will use an inverting amplifier with unity gain to invert the position signal. We will work near the middle of the encoder’s range by using a constant voltage input of 5 VDC, rather than the constant voltage of approximately 0.24 VDC we used for velocity control.
Since our encoder is an incremental encoder the decoder must be reset before it is used. The decoder resets when it is powered up. It also resets when the small black pushbutton on the side of the decoder is pressed. It is configured to reset to the middle of its range.
PRE-LAB
The pin-outs of a 471 single op-amp DIP and a 1458 dual op-amp DIP are shown below.
741 Single Op-Amp Pin Out 1458 Dual Op-Amp Pin Out
The servoamplifier will not saturate if the maximum control signal u(t)max is:
u(t) max <6.5 volts
We must keep the maximum control signal from exceeding that which would demand a greater voltage from the servoamplifier than it can supply. Both the size of the input step, ∆Vstep, and the gains, K, Kp and KI, affect the magnitude of the control signal. Read the control signal u(t) on channel One of the oscilloscope. If it exceeds 6.5 volts for a given gain, then reduce the step size.
will have difficulty getting their controller working again. If have difficulty, rewire your circuit in accordance with these guidelines. You will save time.
Be sure to add the constant voltage, VC, to the sum of inputs or your gains will be in error.
Debugging Procedure
If you must wait for assistance because your instructor is busy helping another group, use your time to your advantage by performing the following checks:
(a) make sure the power supply of the enclosure is turned on. (b) check the power supply voltages for the op-amp. On single op-amp DIPs Pin 4 should be -15 VDC and Pin 7 should be +15 VDC. On dual op-amp DIPs, Pin 4 should be -15 VDC and Pin 8 should be +15 VDC. (c) check the circuit once more to see if all of the components are present and properly connected. (d) check to see that you are not saturating the op-amp by using too high a gain or too large an input. (e) check the oscilloscope time and voltage settings relative to the time constant or period and magnitude of the signal you expect. (f) break the connection between cascaded op-amp circuits and identify which circuit is not performing properly. (g) if you attempted to disconnect the integrator output to characterize the controller gains, check if you removed the correct lead.
The two most common problems are missing components and missing or erroneous connects. NEATNESS and COLOR CODING helps eliminate both types of errors!!
If none of these steps resolves the problem, then use your time reducing your data on Mathcad.
Proportional-Integral Control of Position
Proportional-Integral Control of Velocity