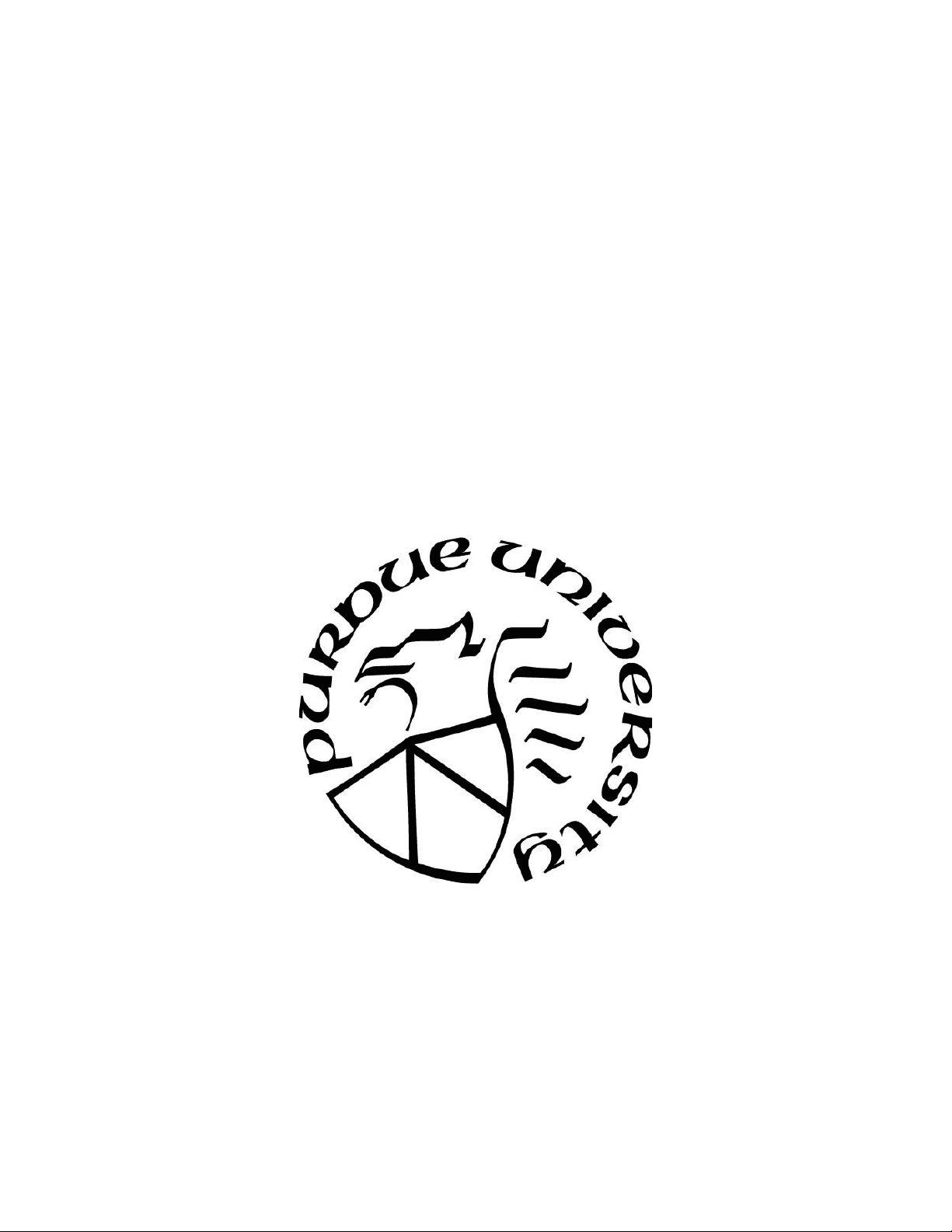
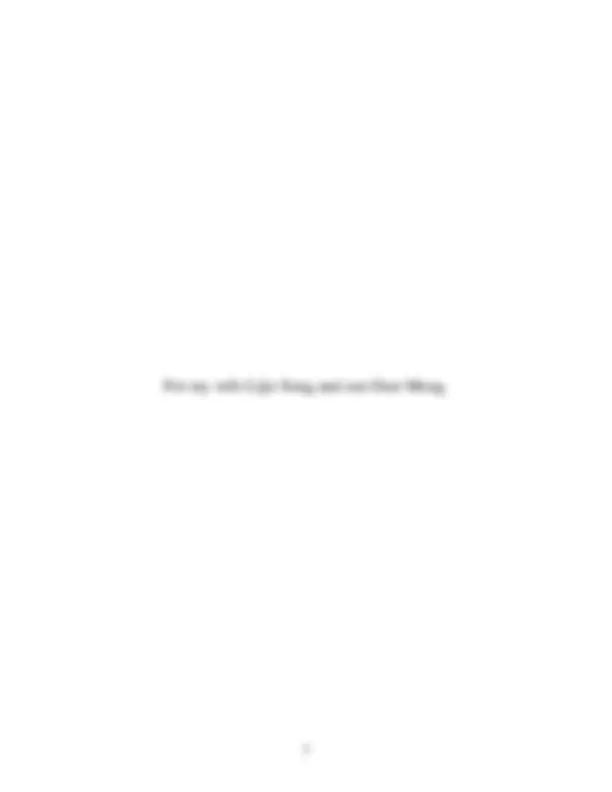
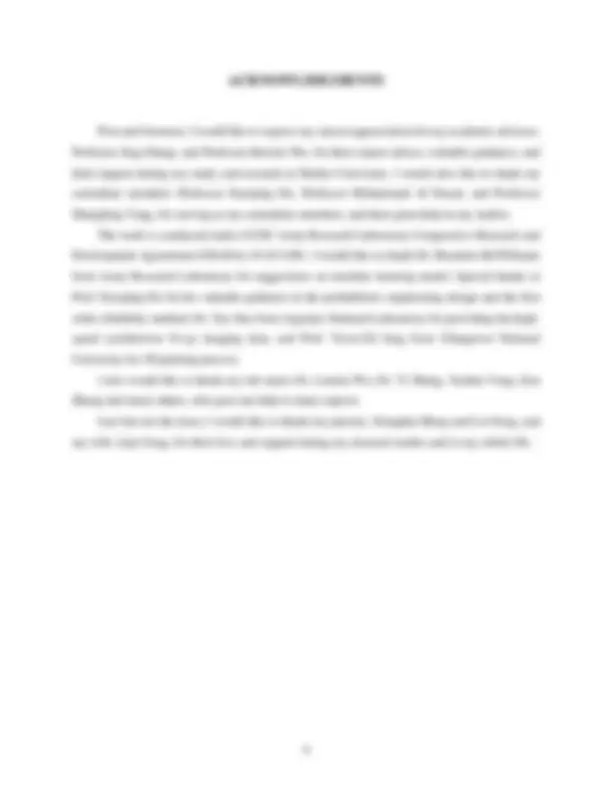
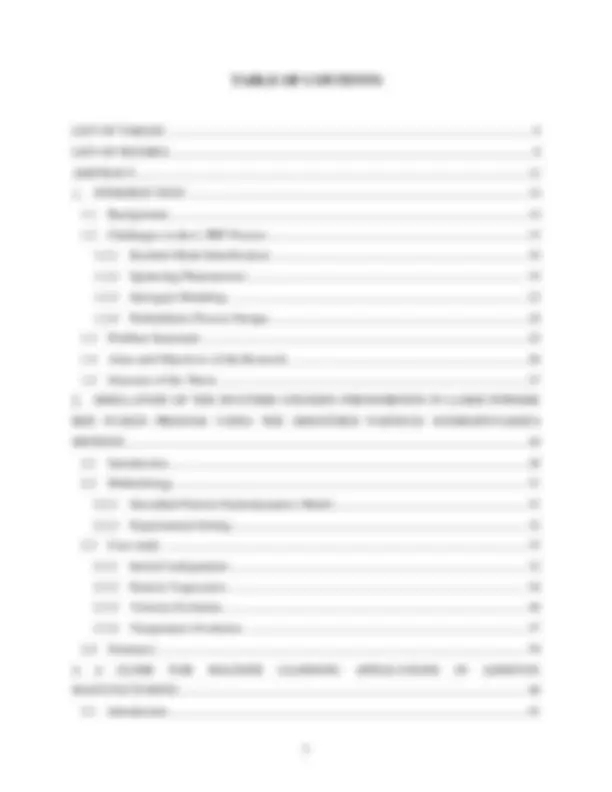
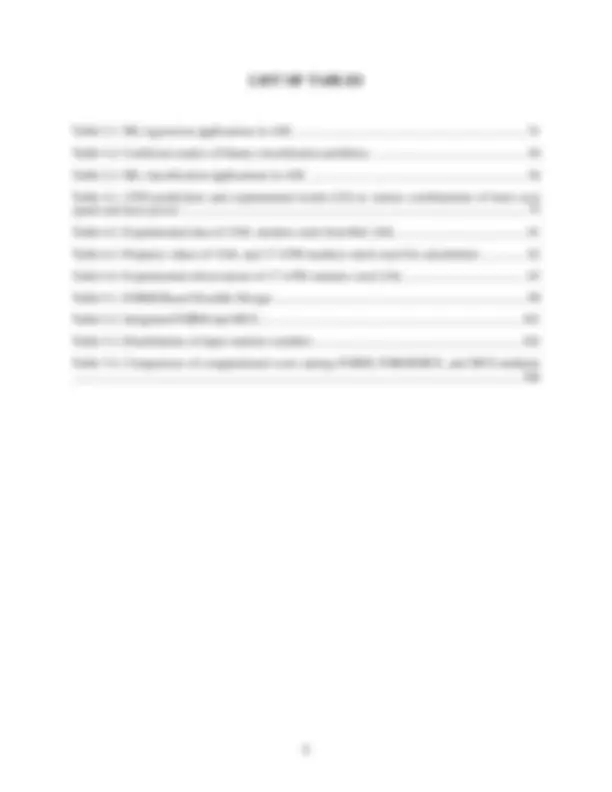
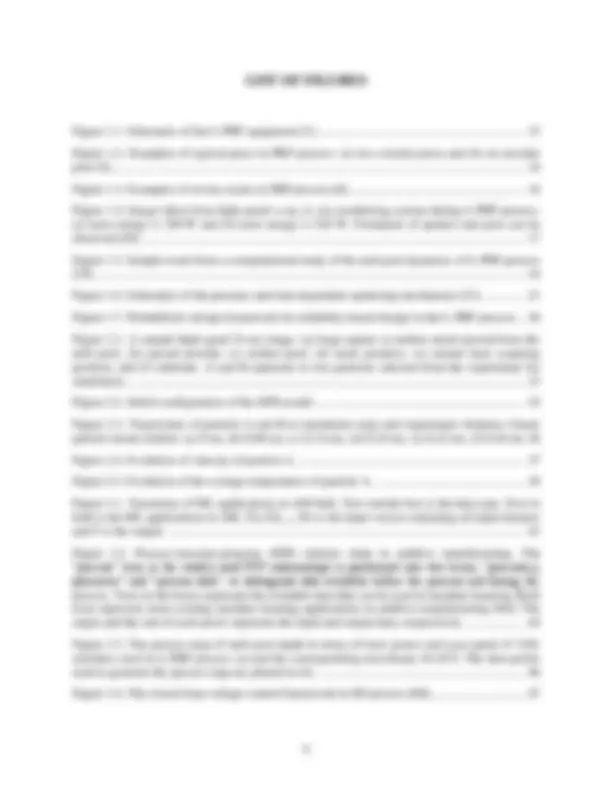
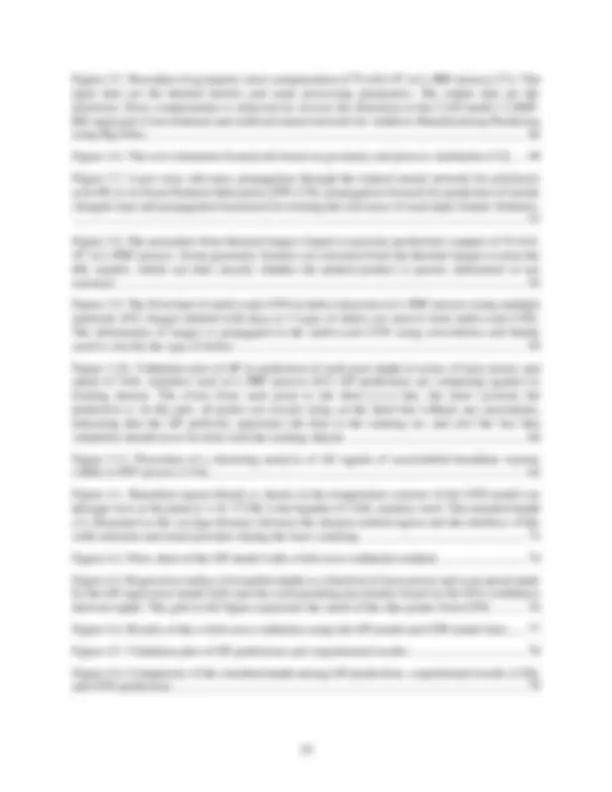
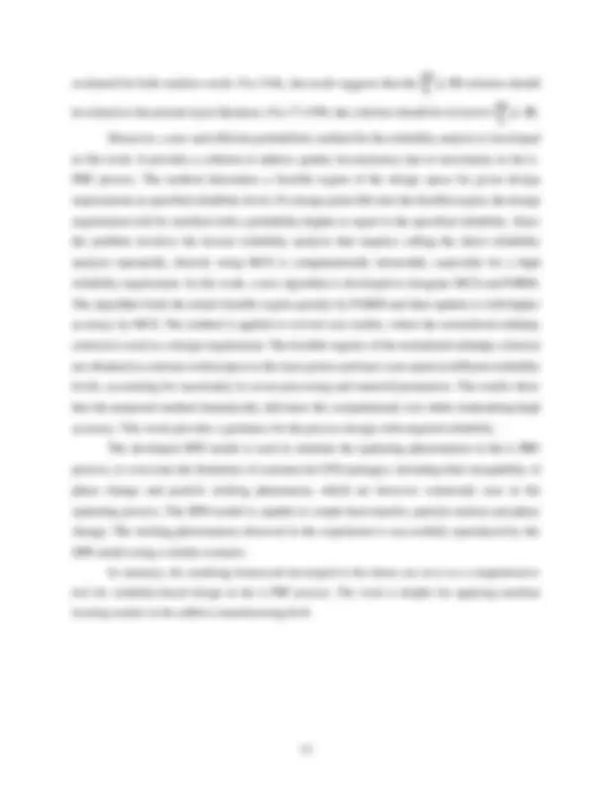

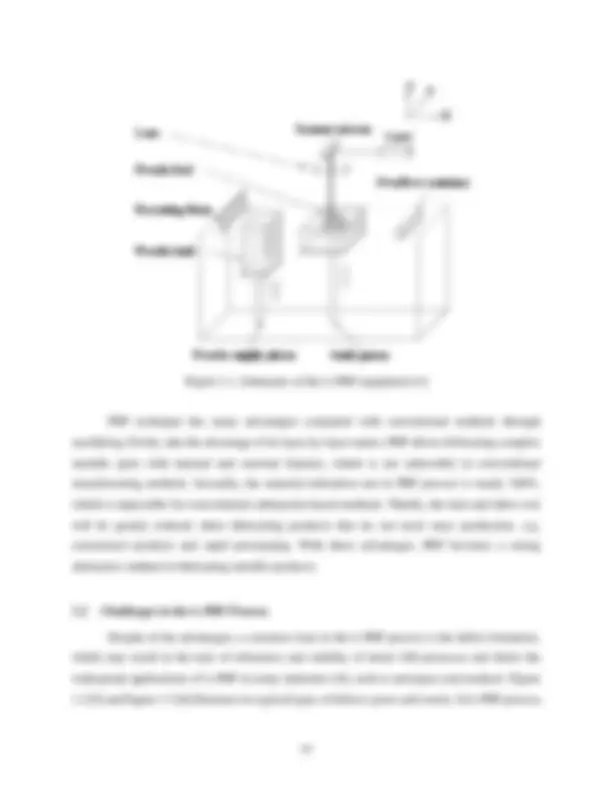
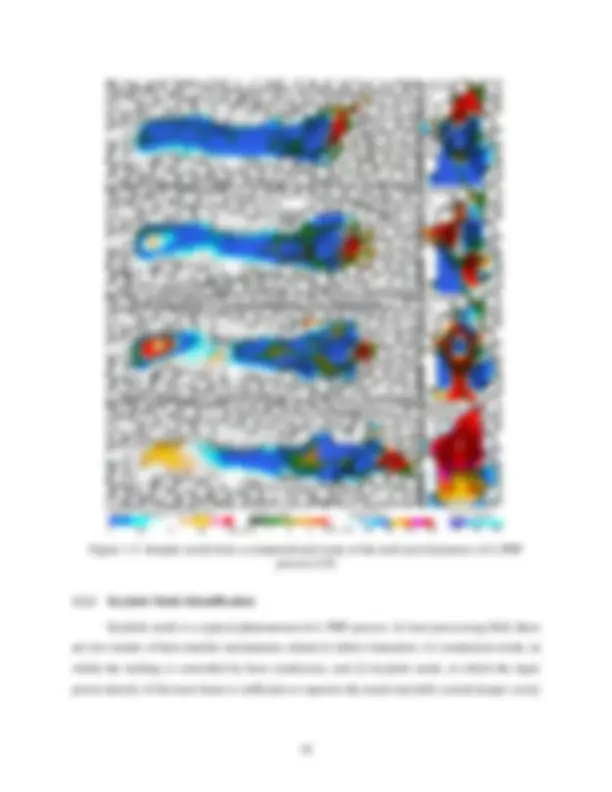
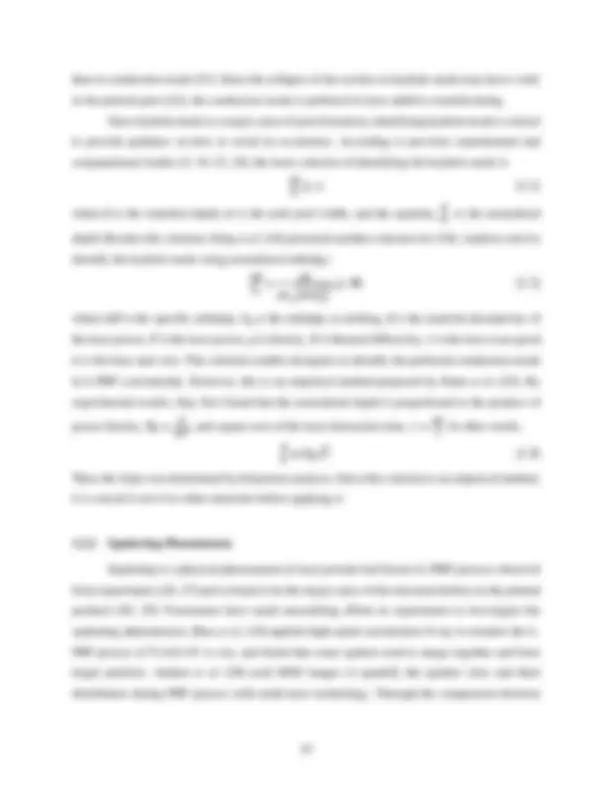
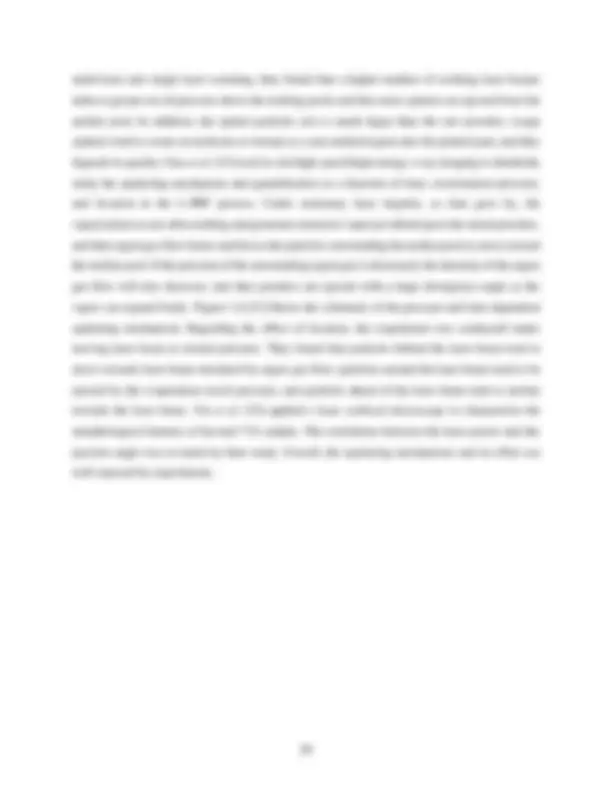
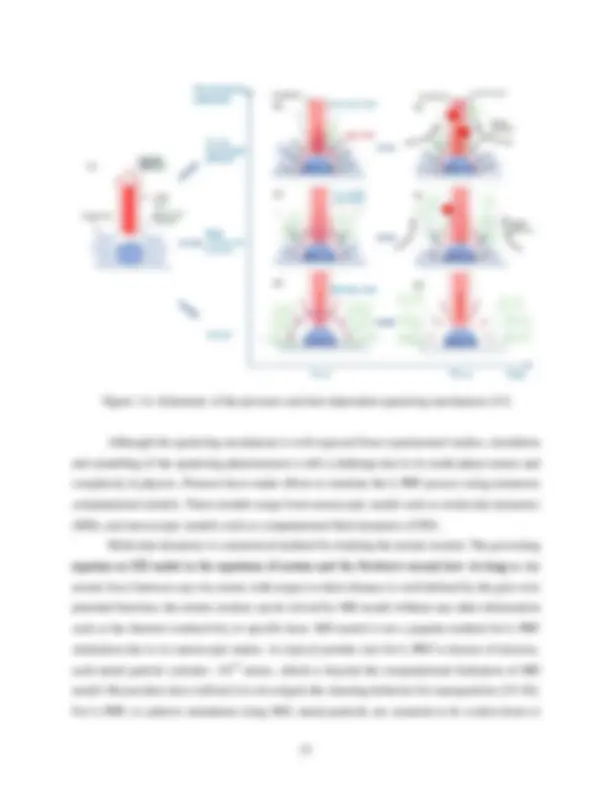
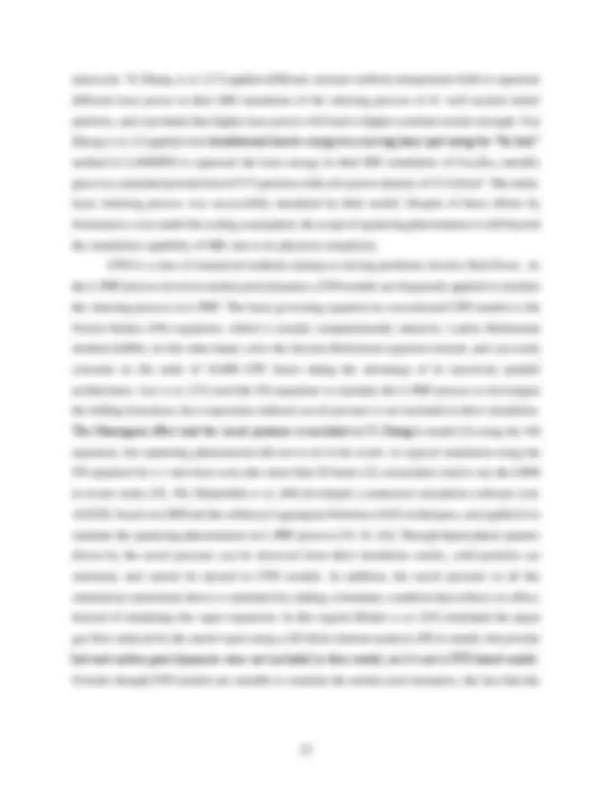
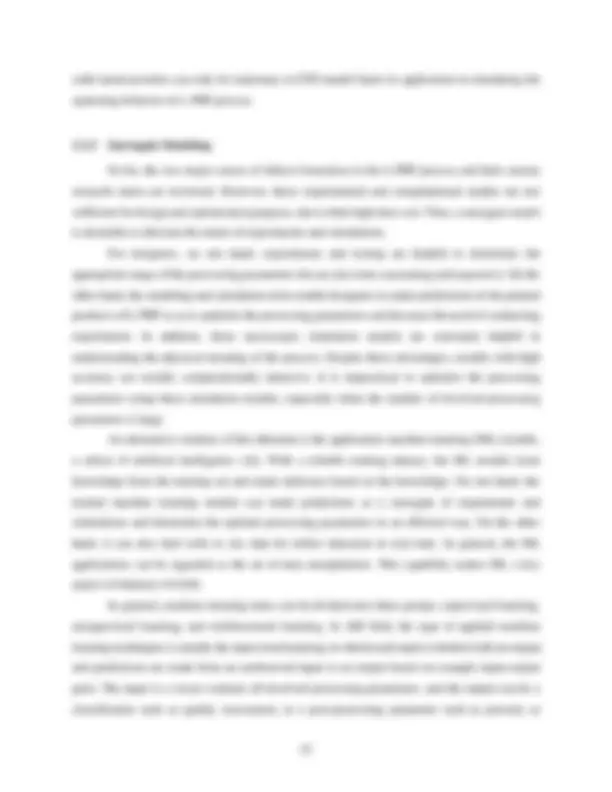
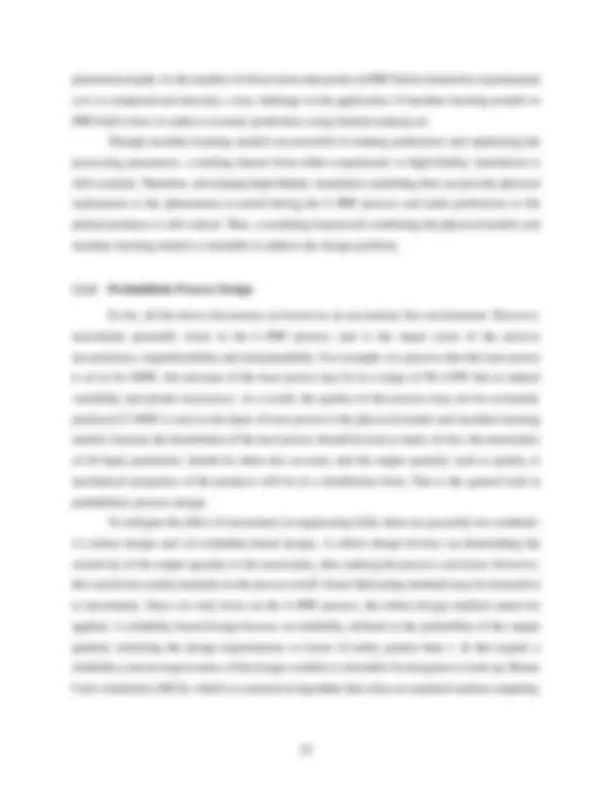
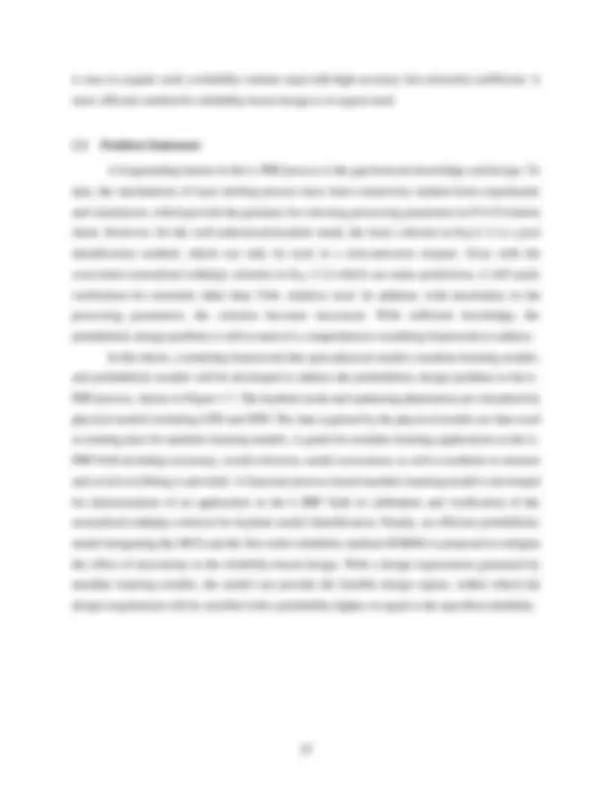
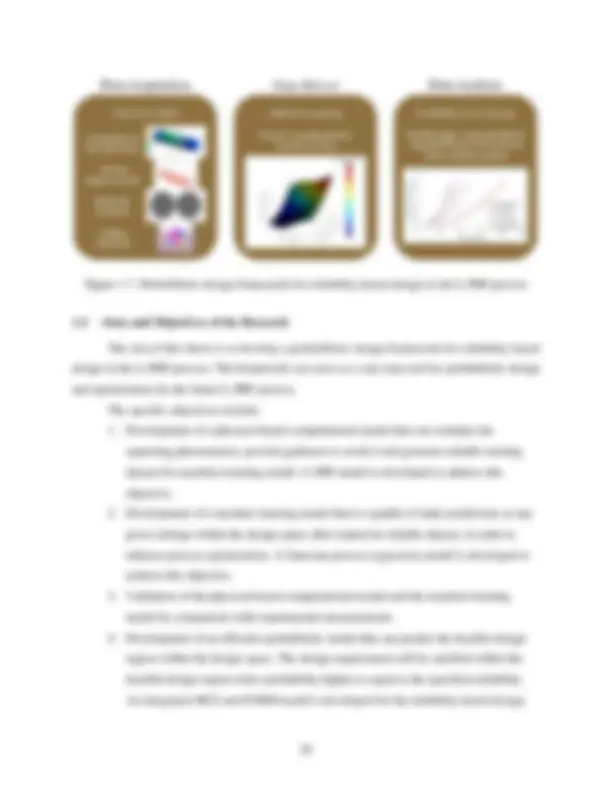
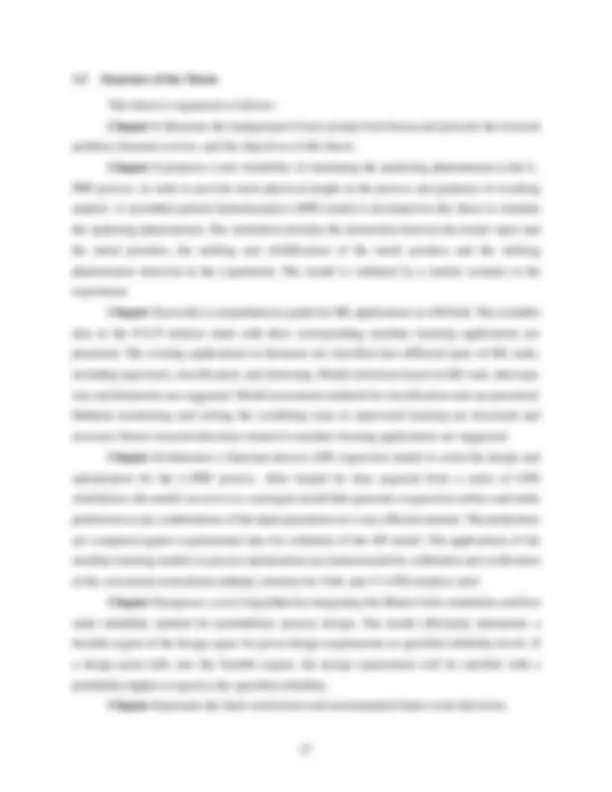
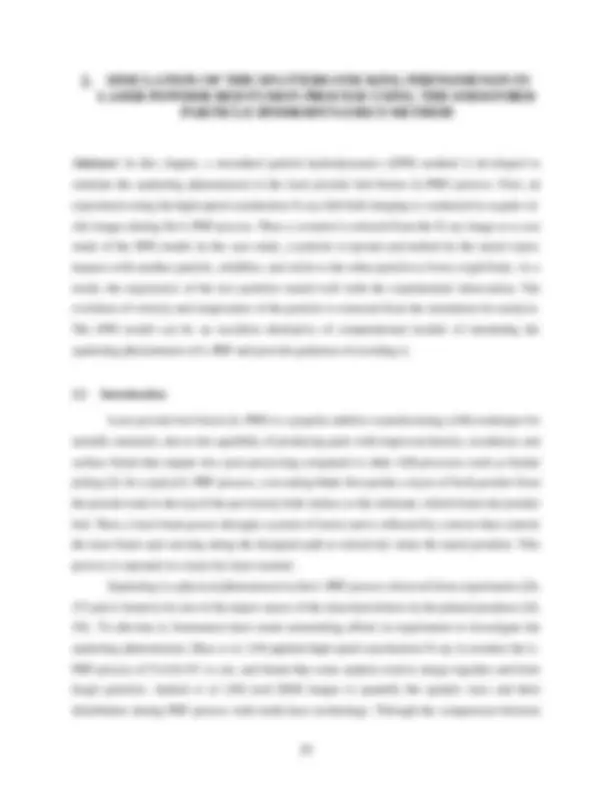
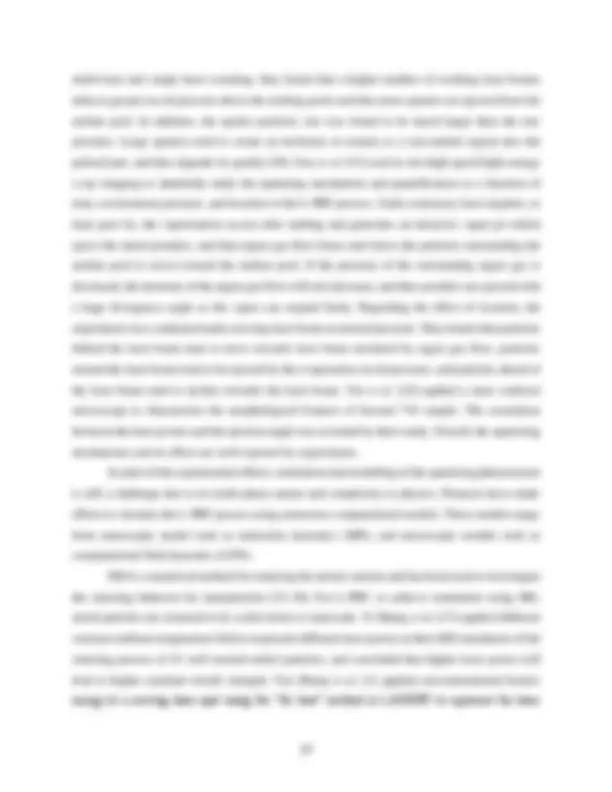
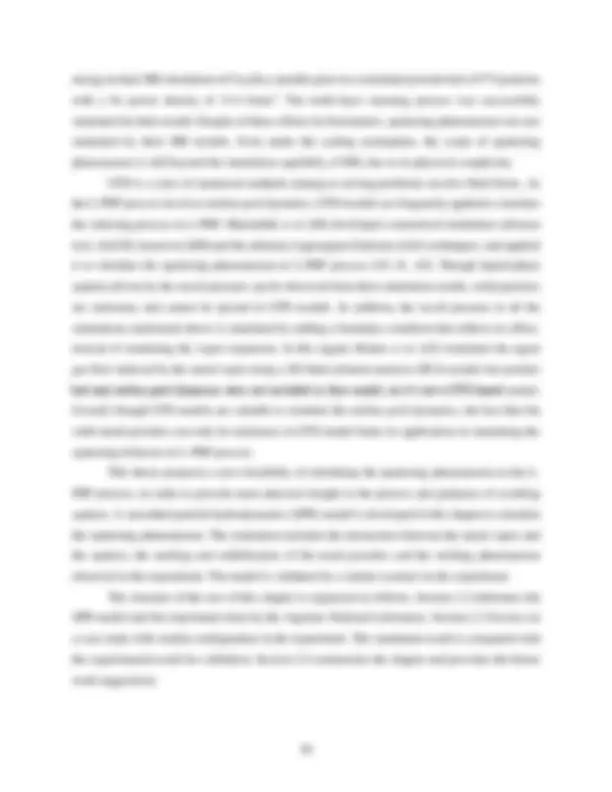
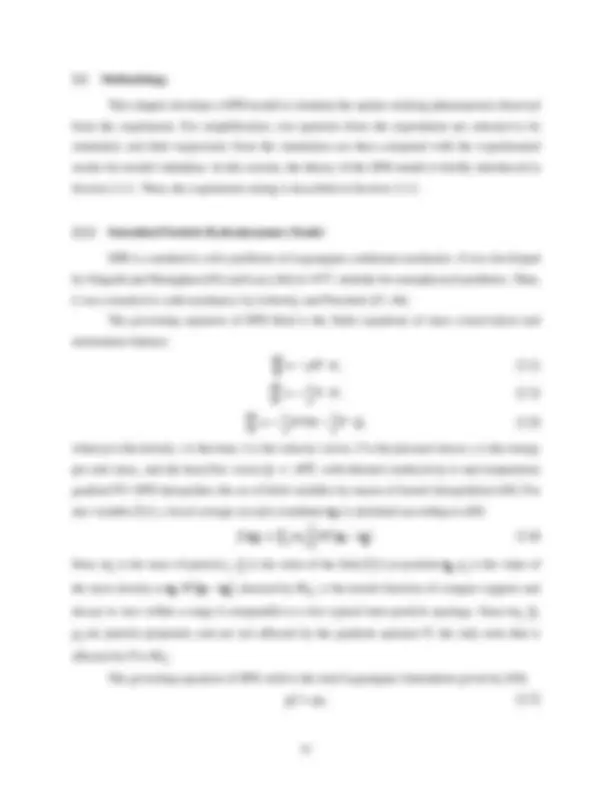
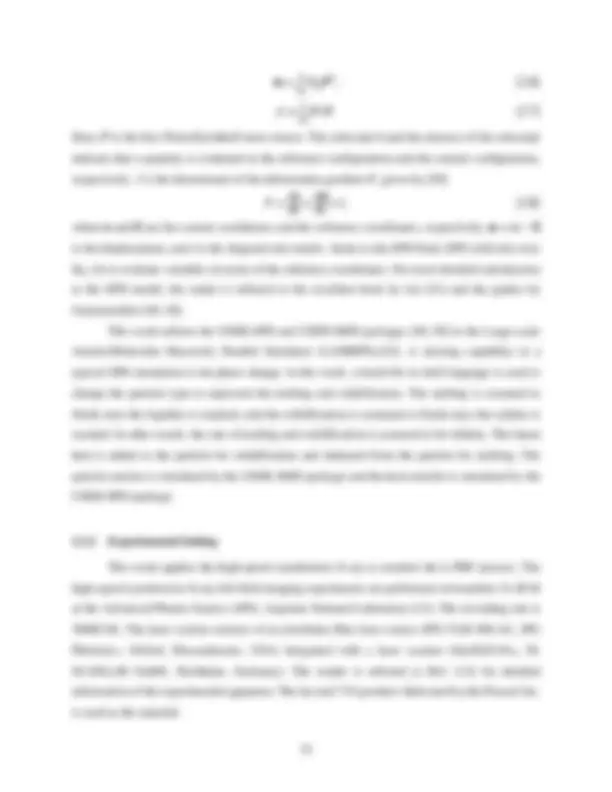
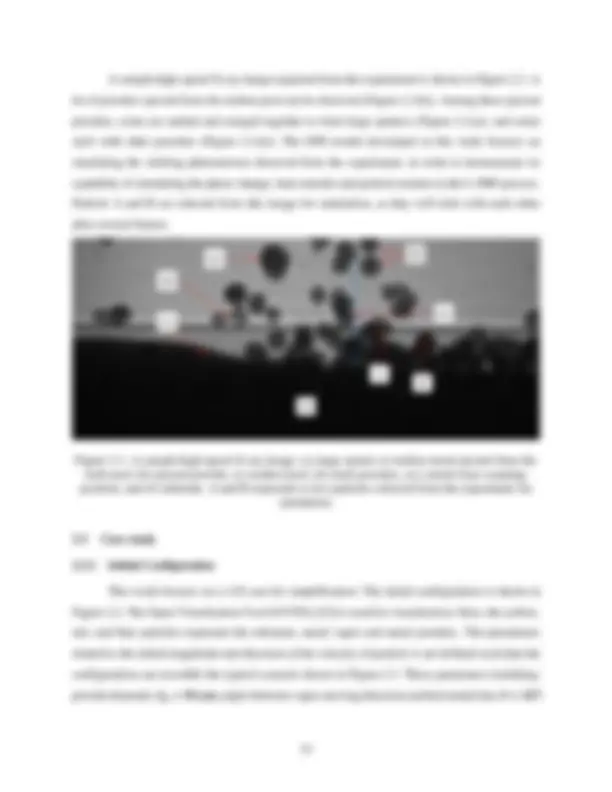
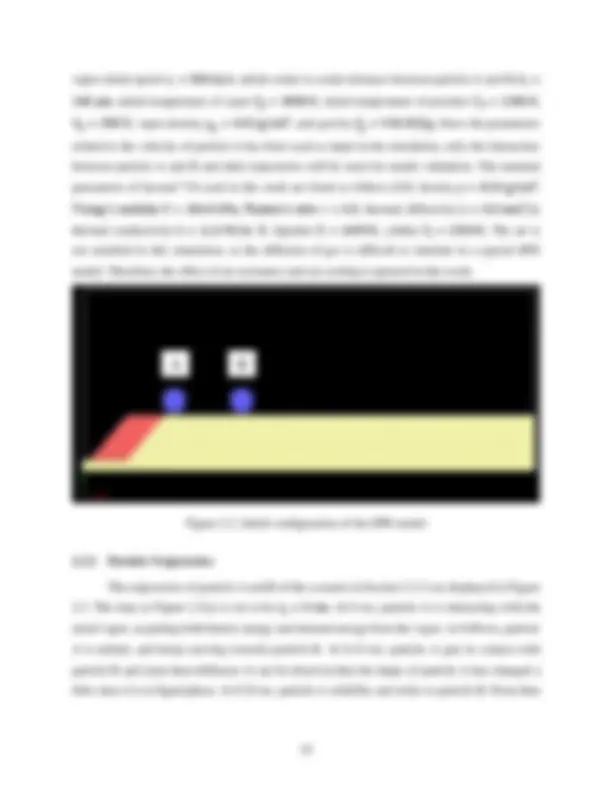
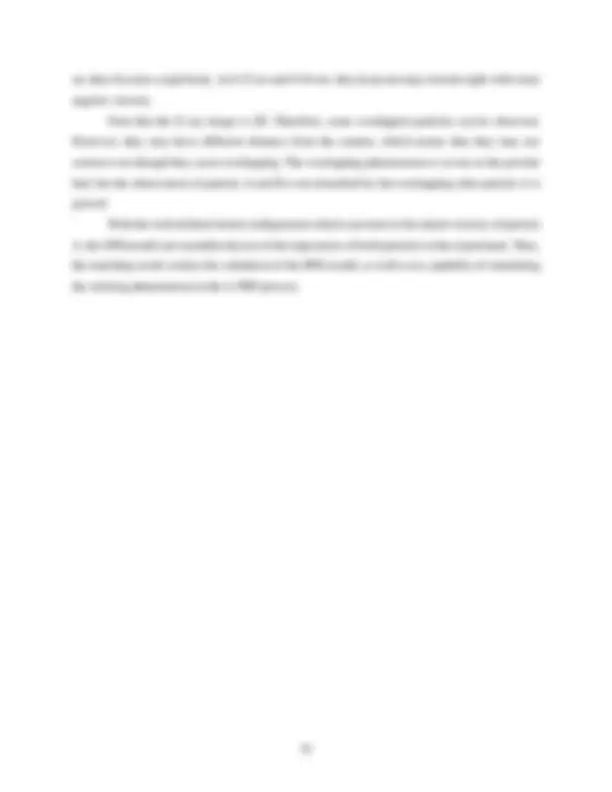
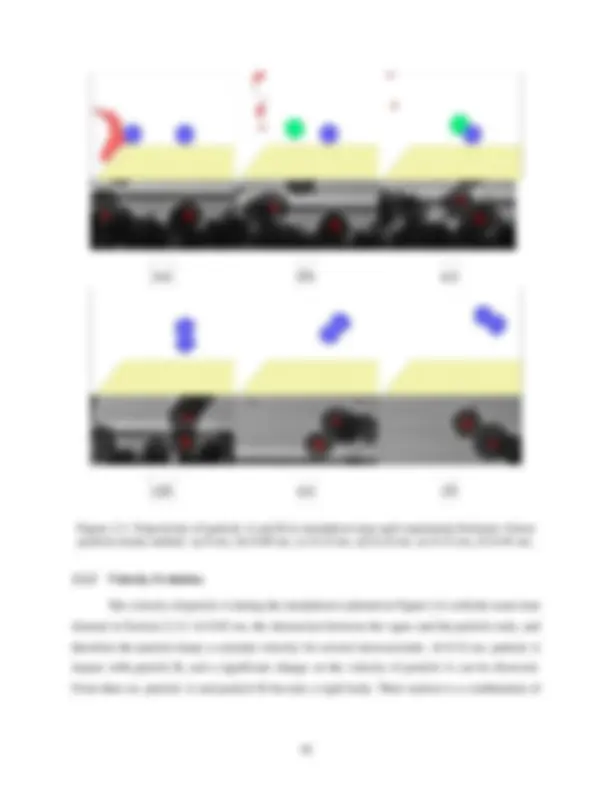
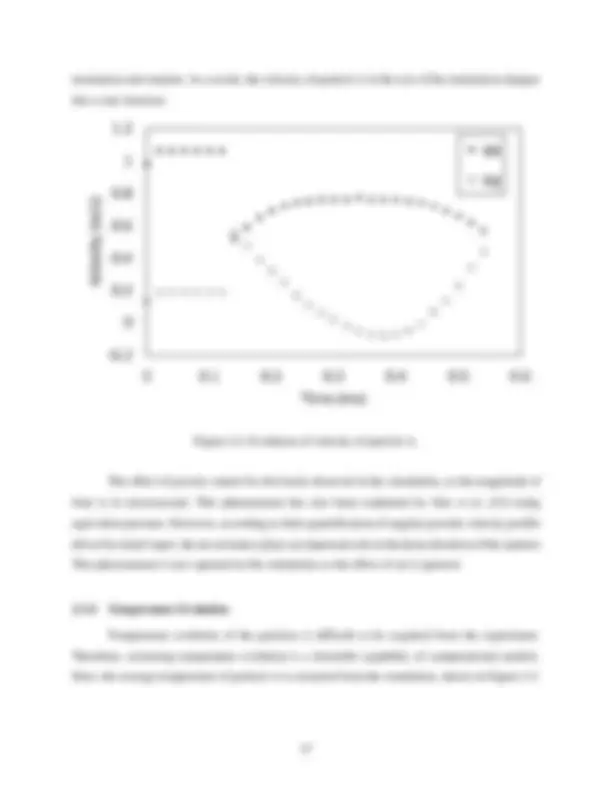
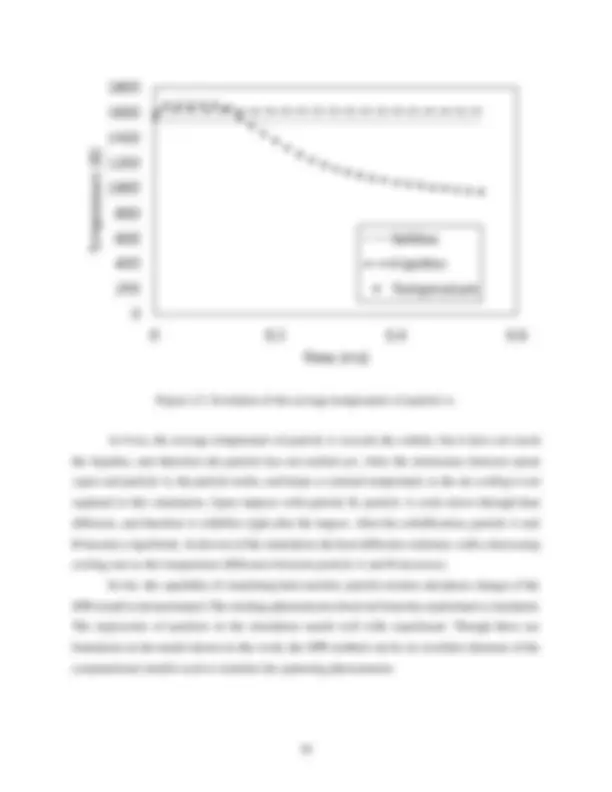
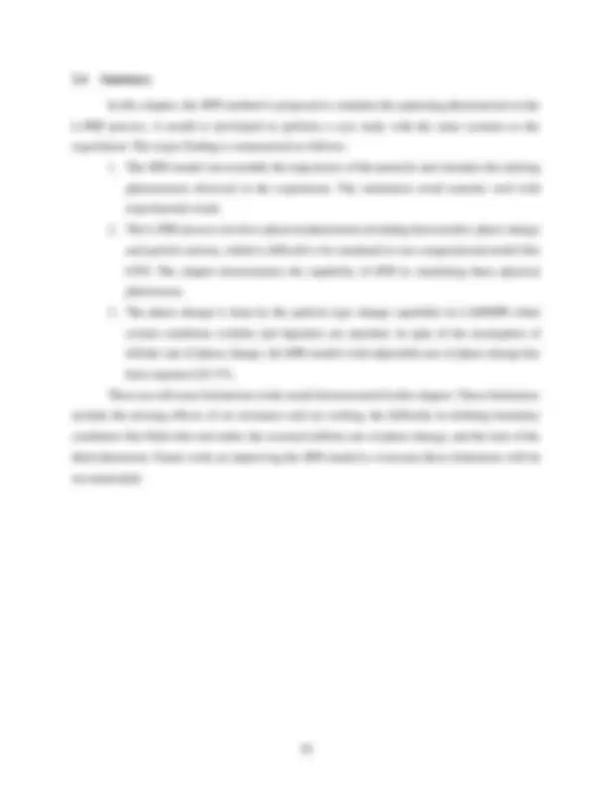
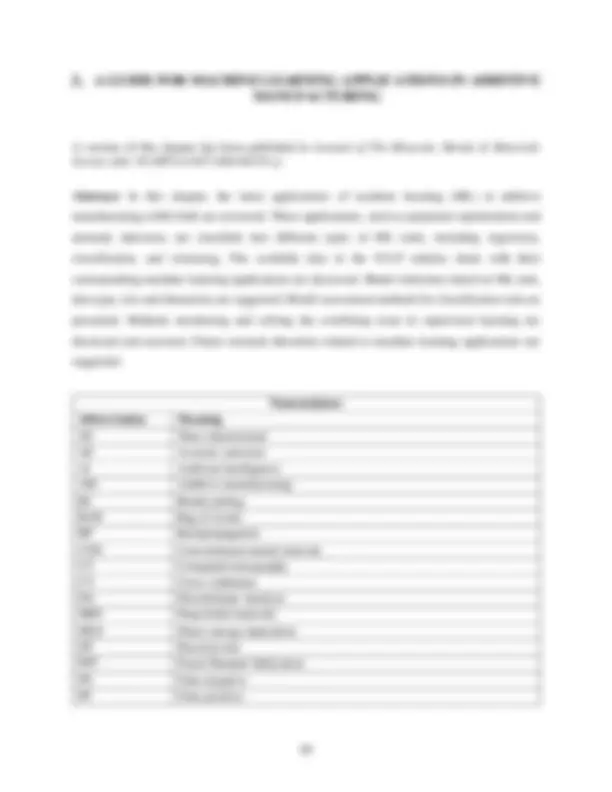
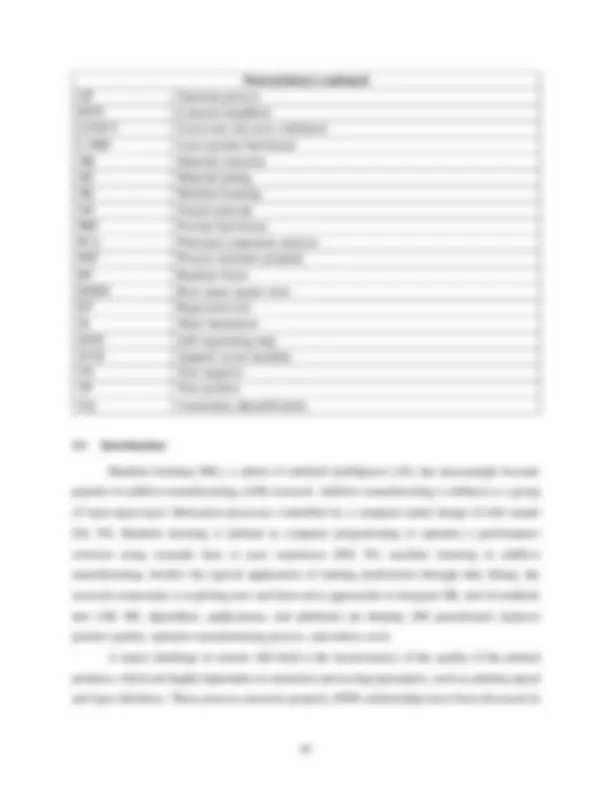
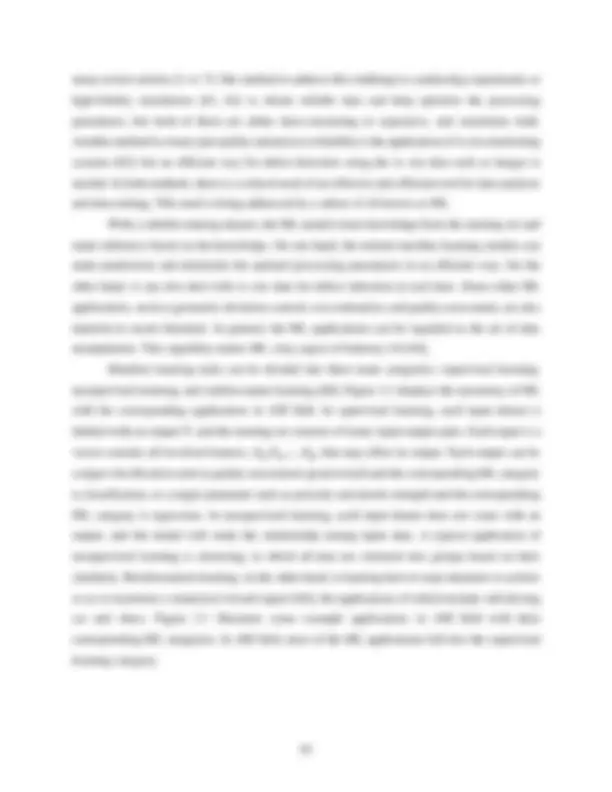
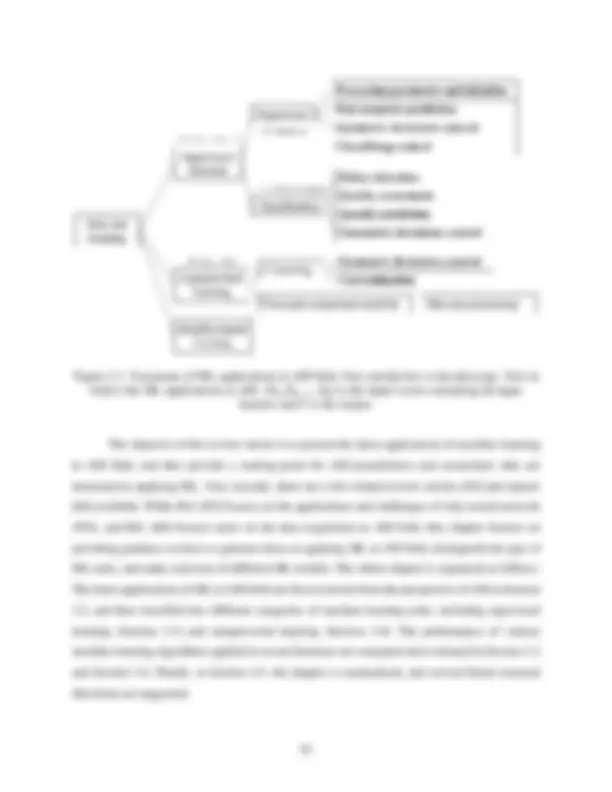
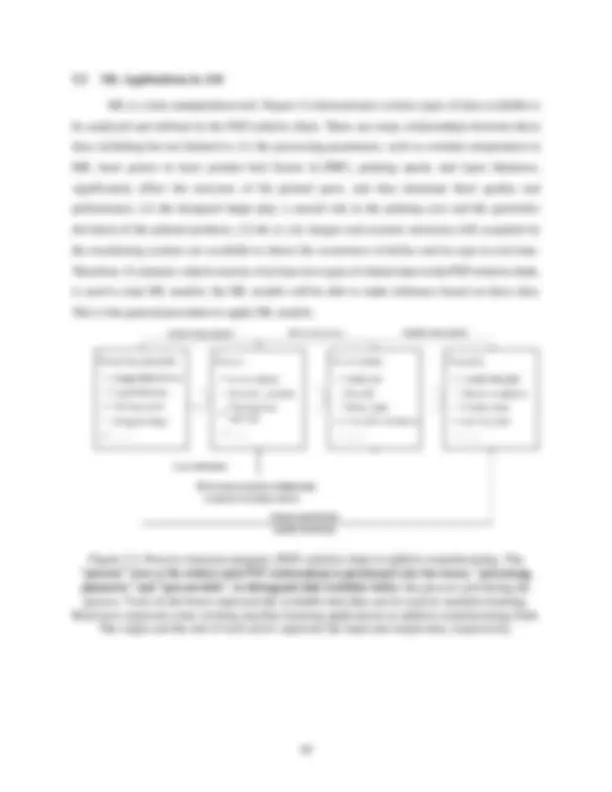
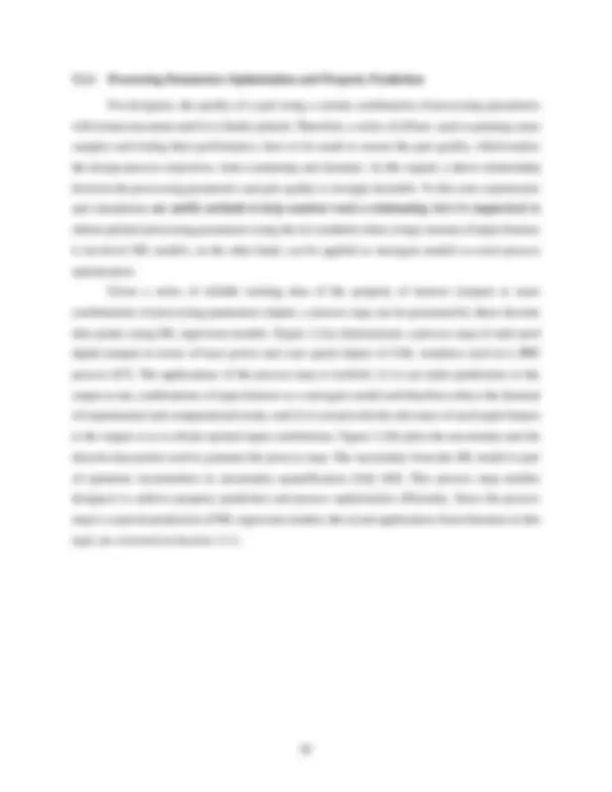
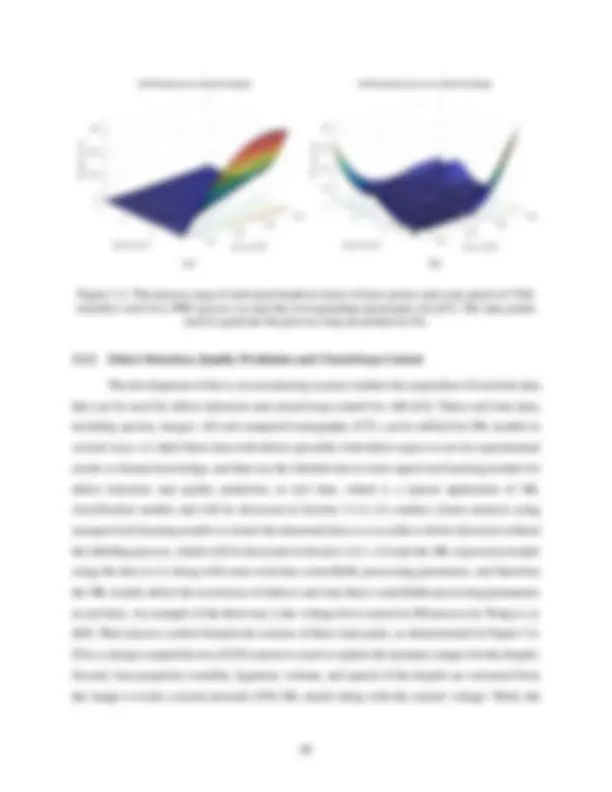
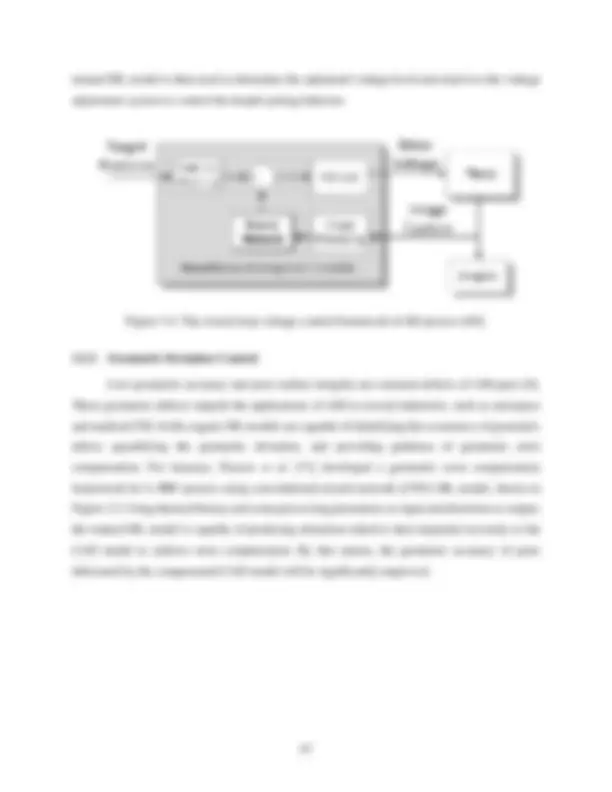
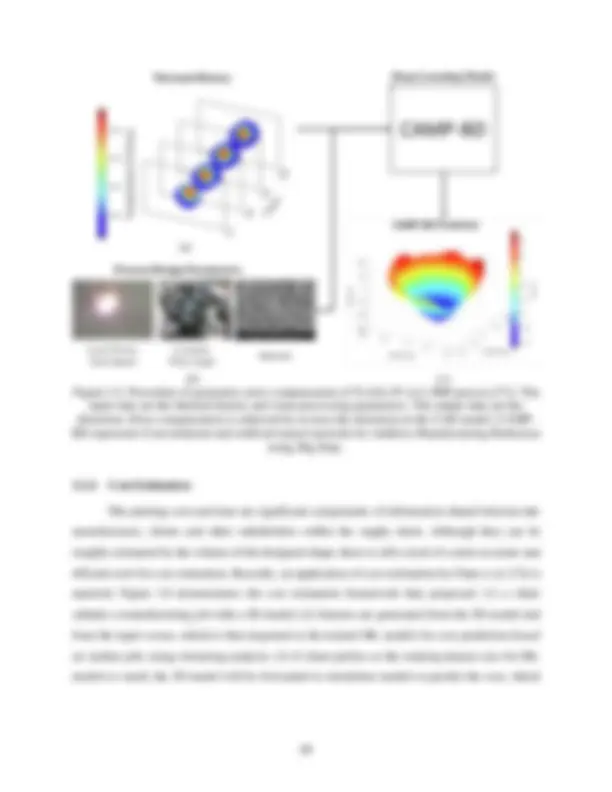
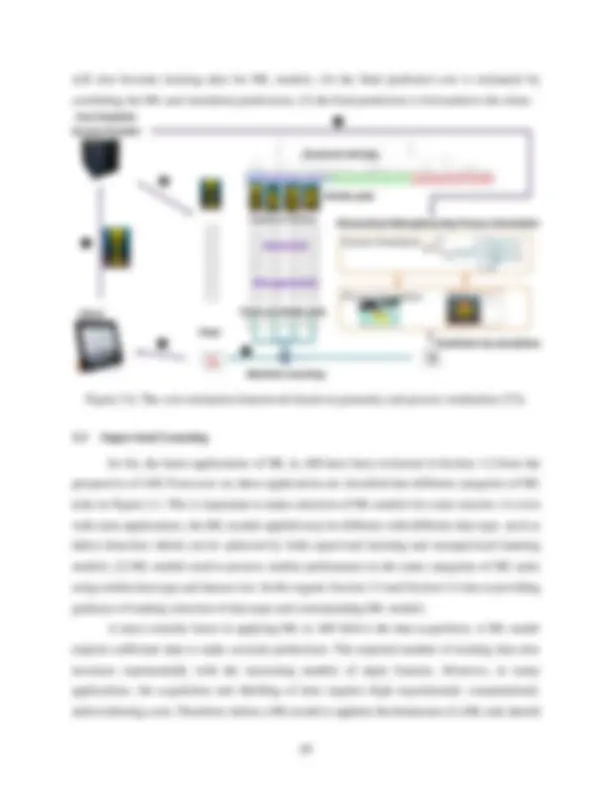
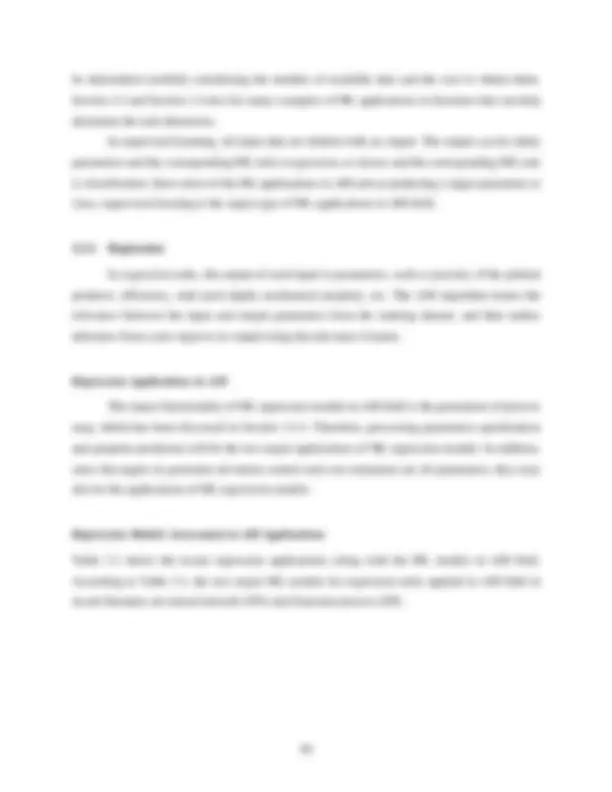
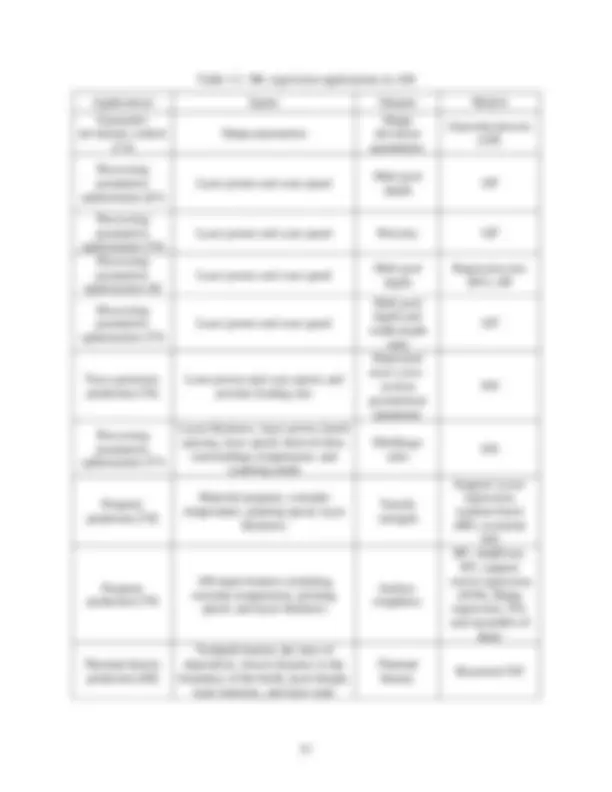
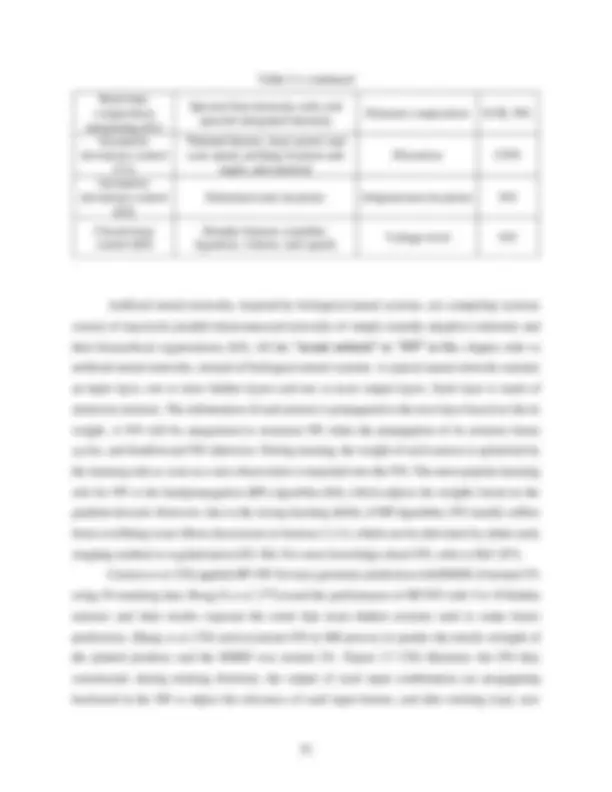
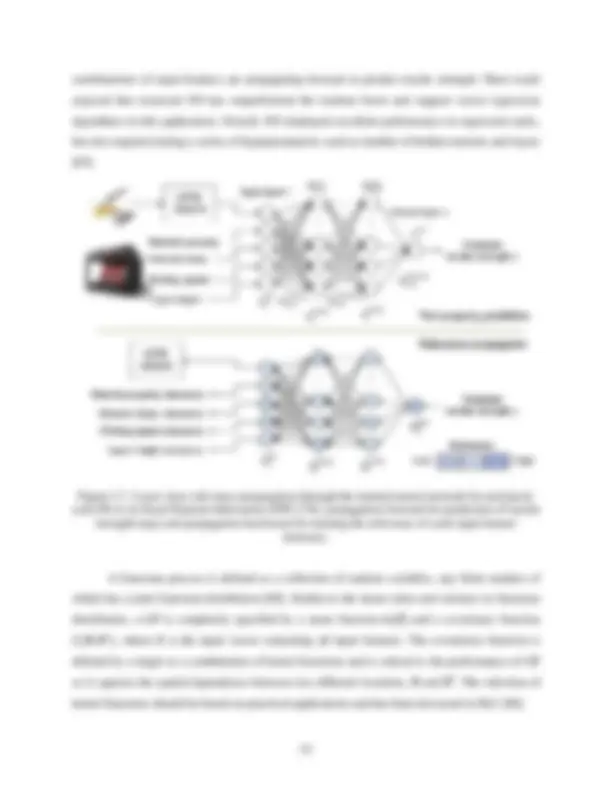
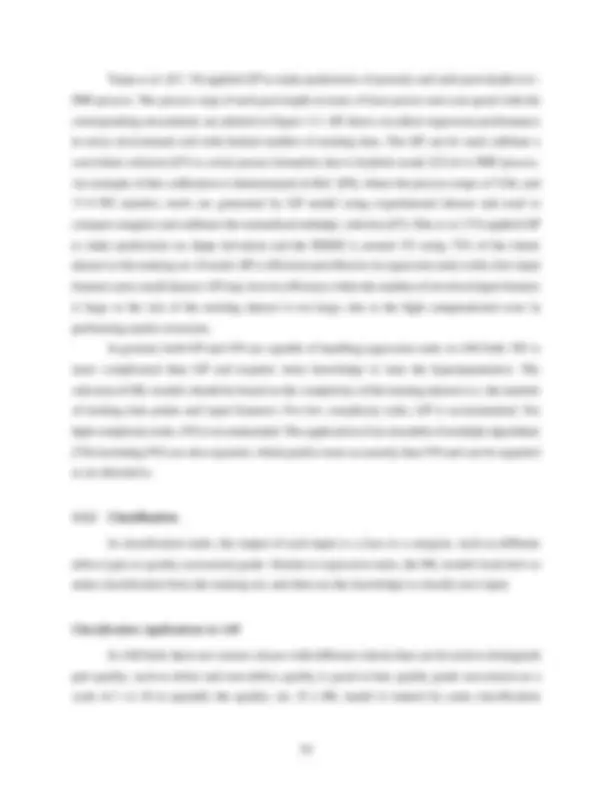
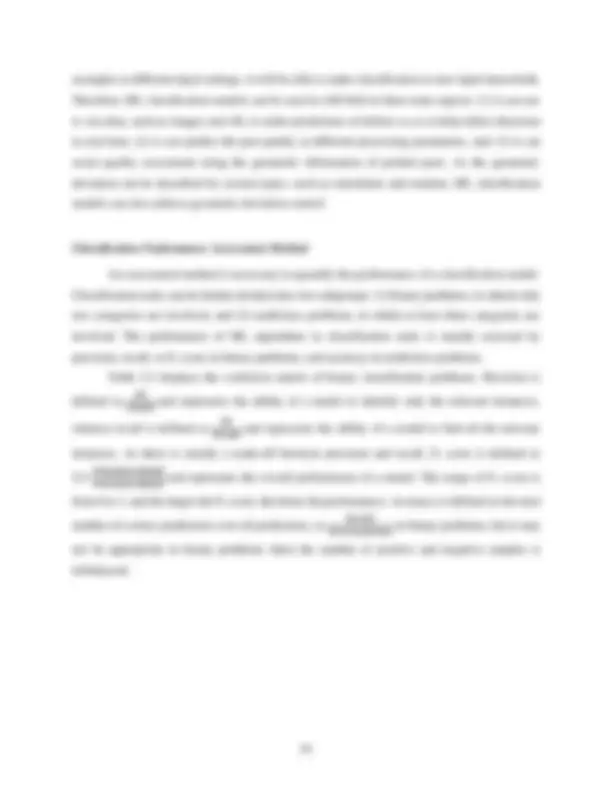
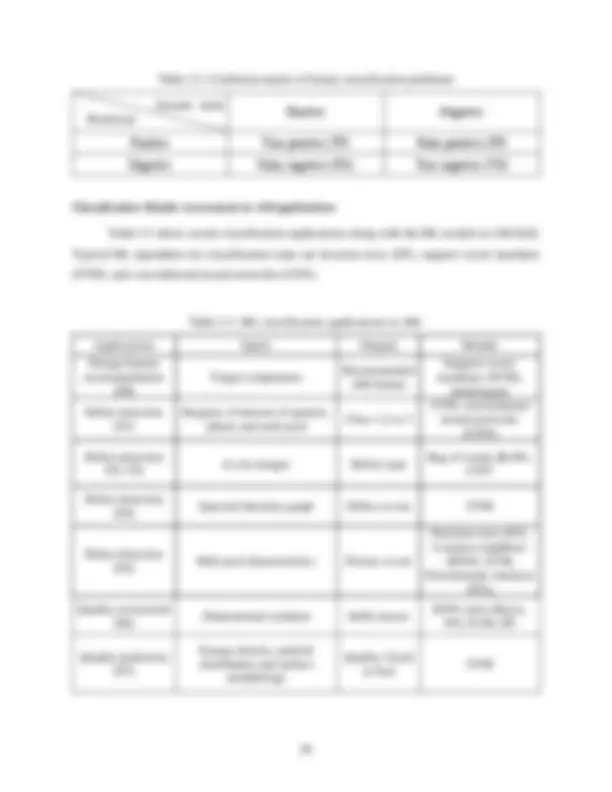
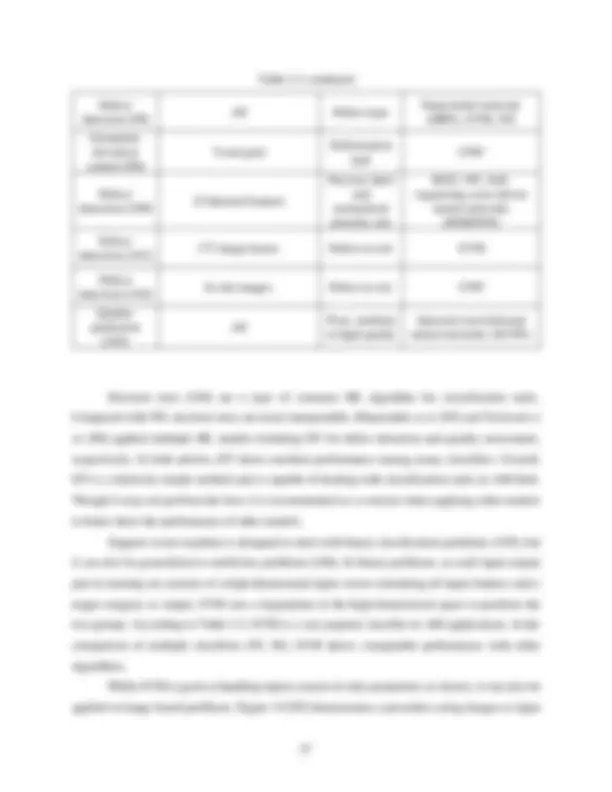
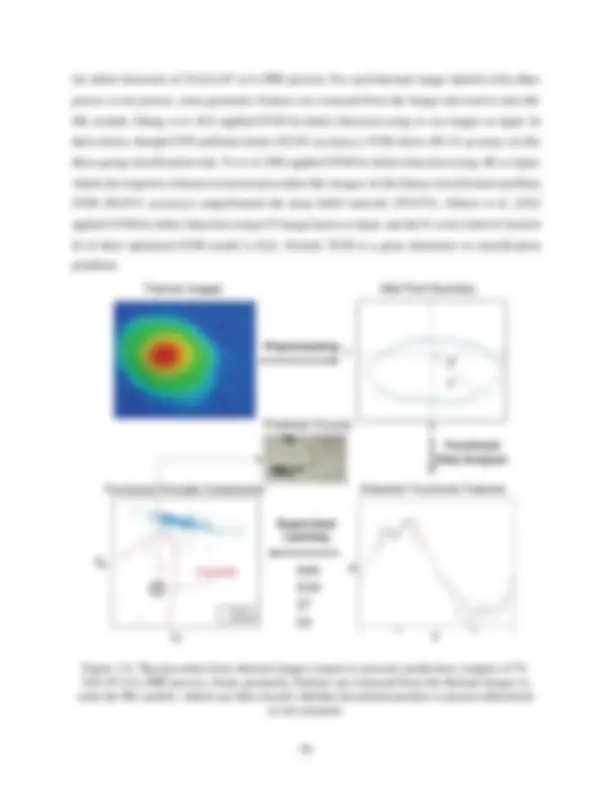
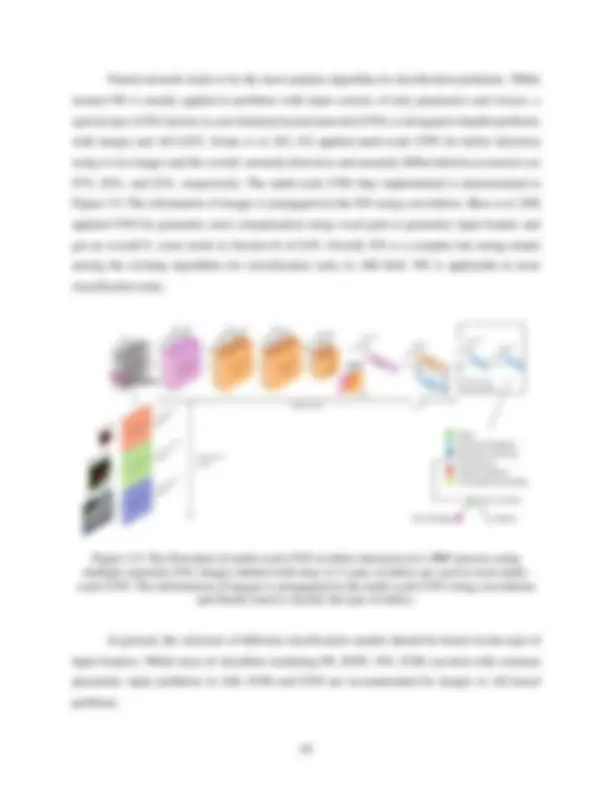
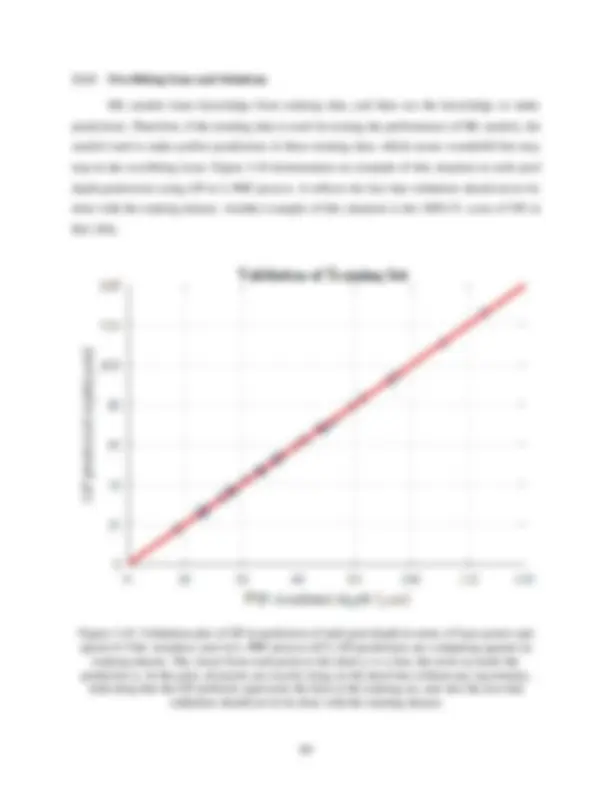
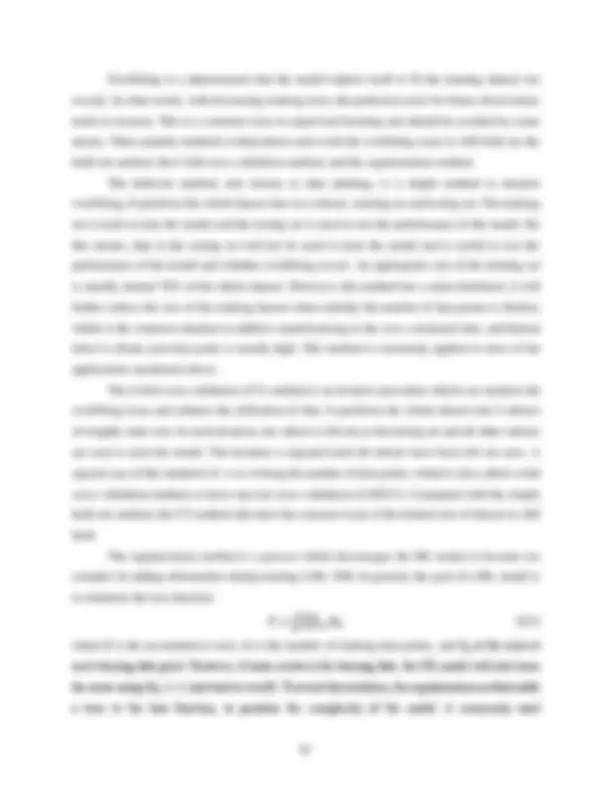
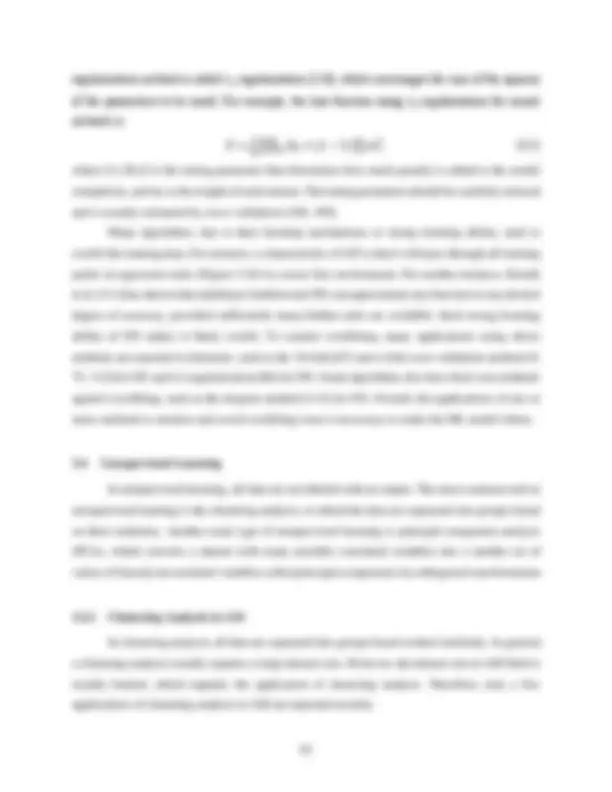
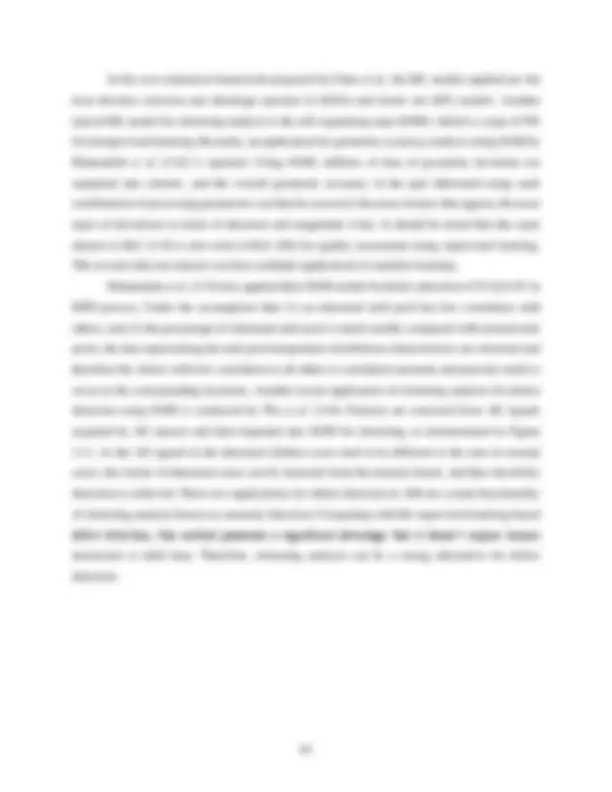
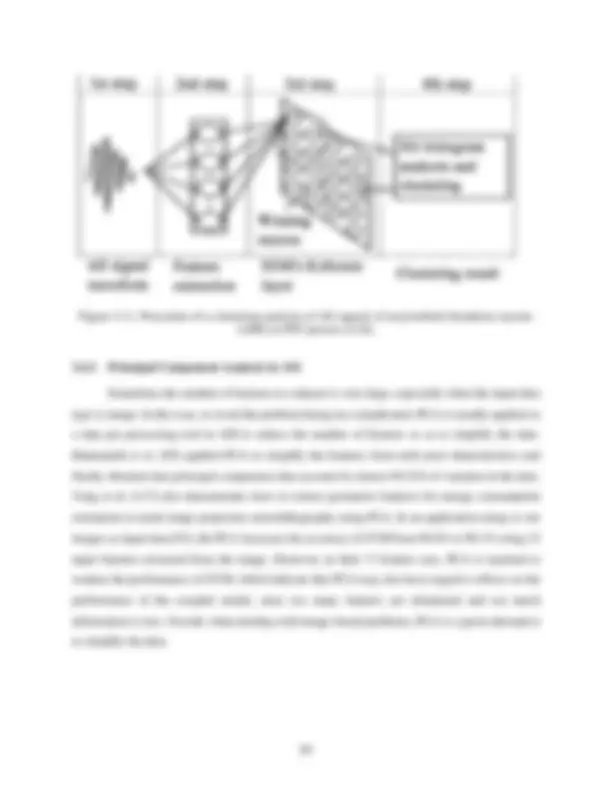
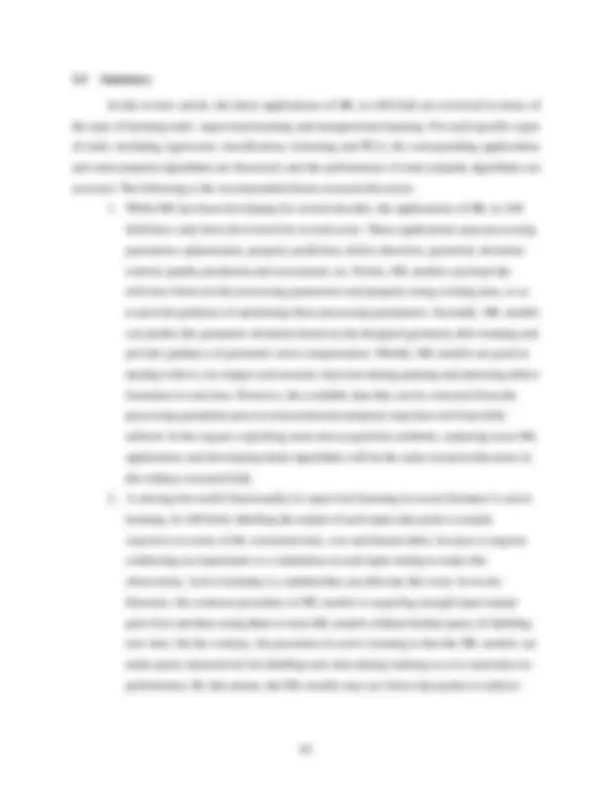

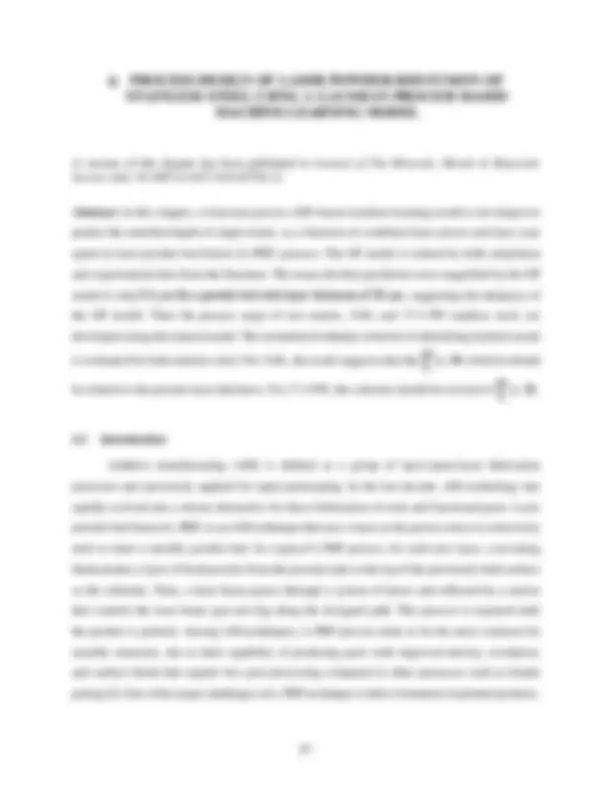
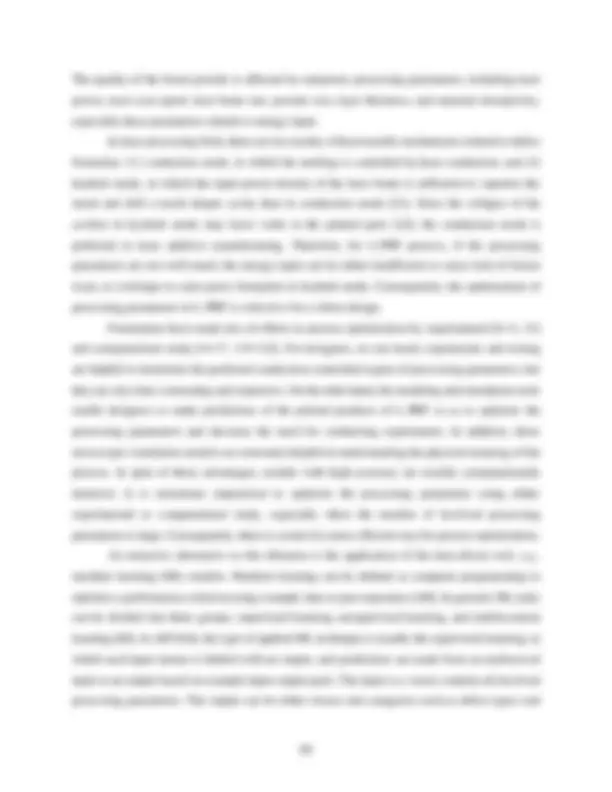
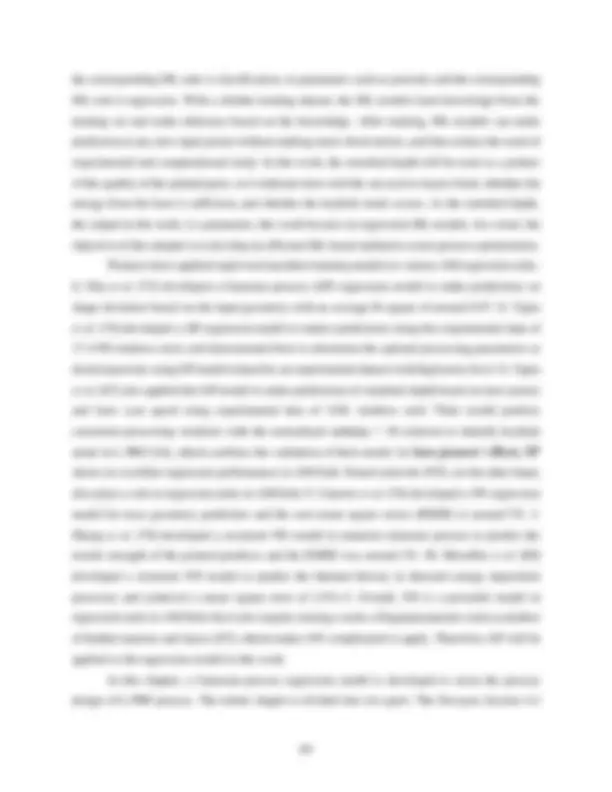
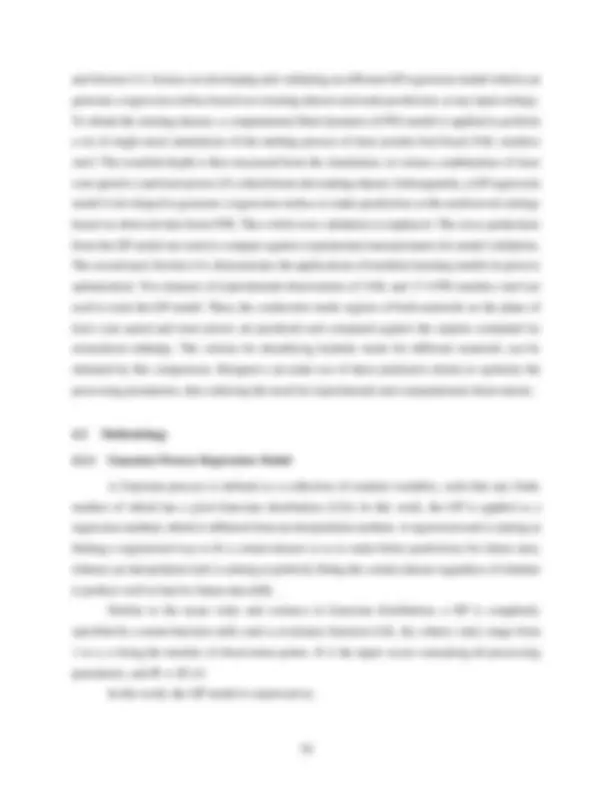
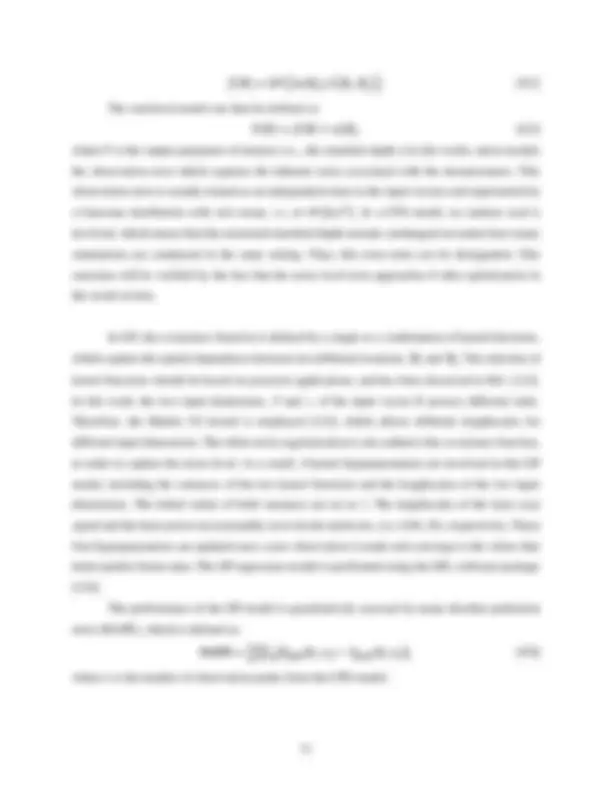
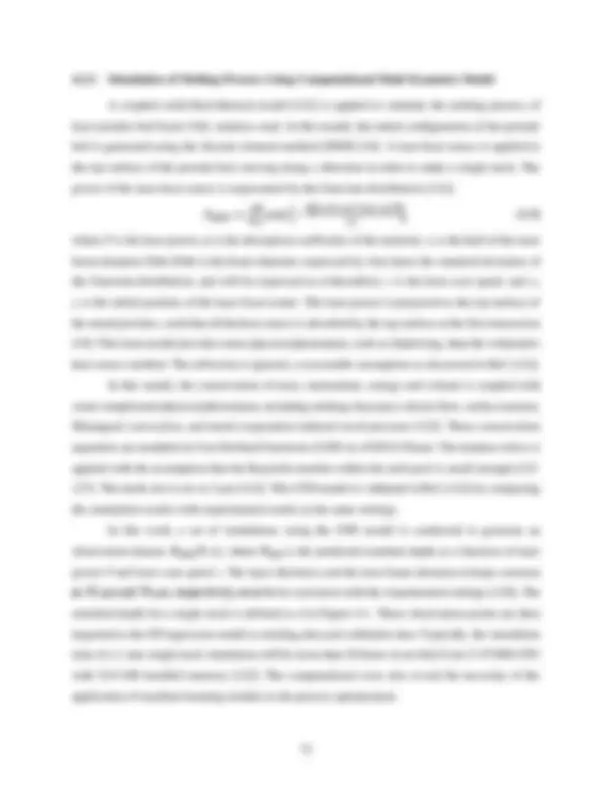
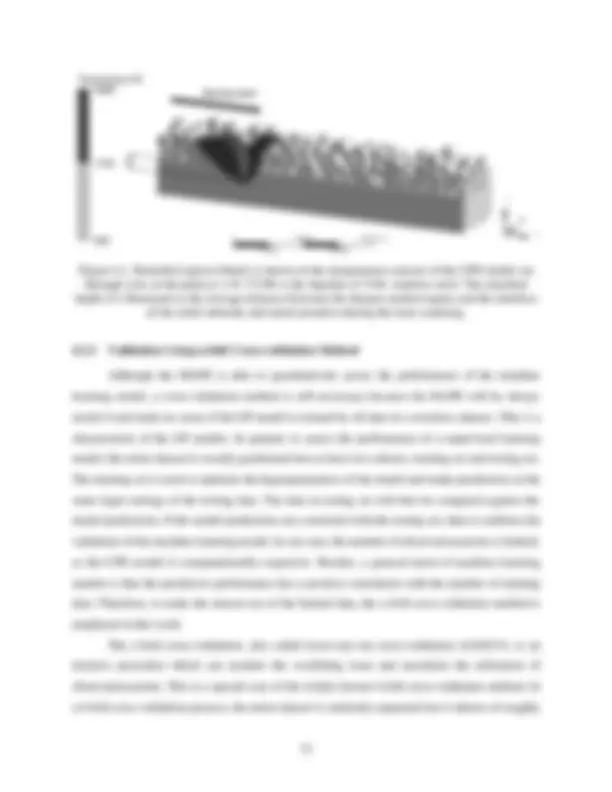
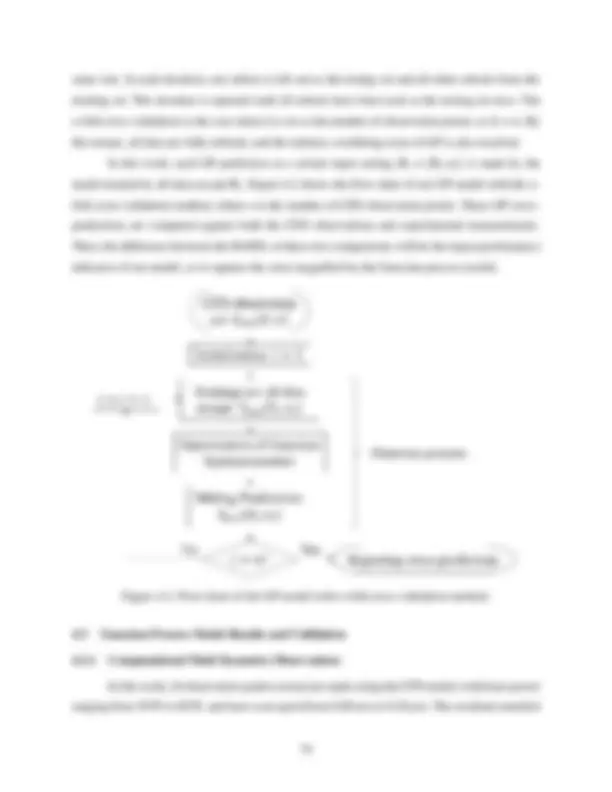
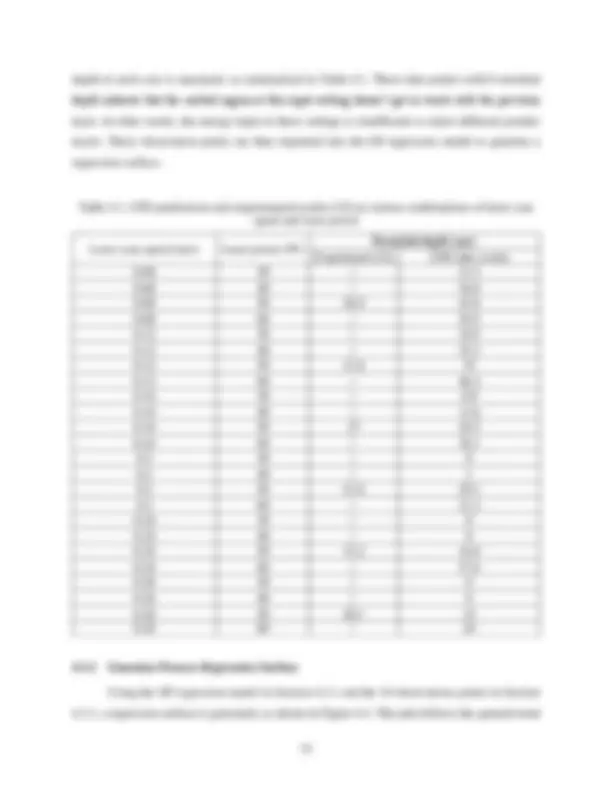
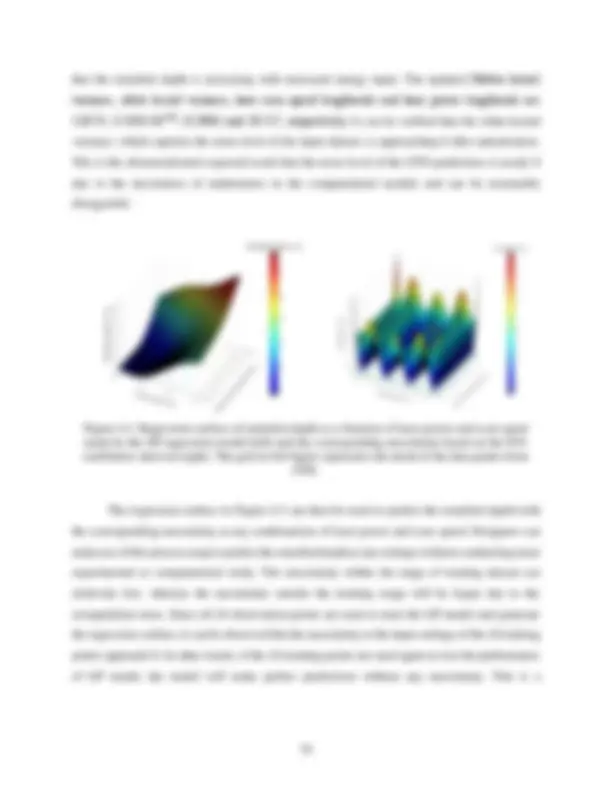

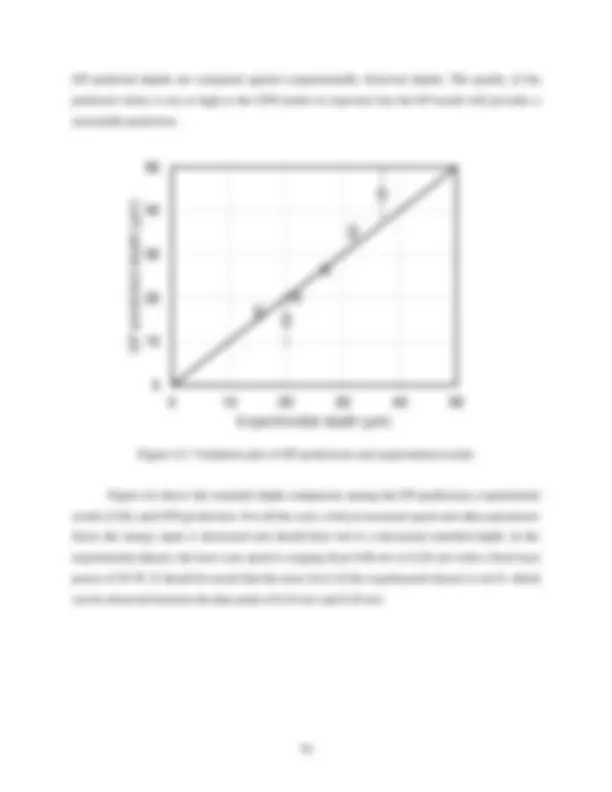
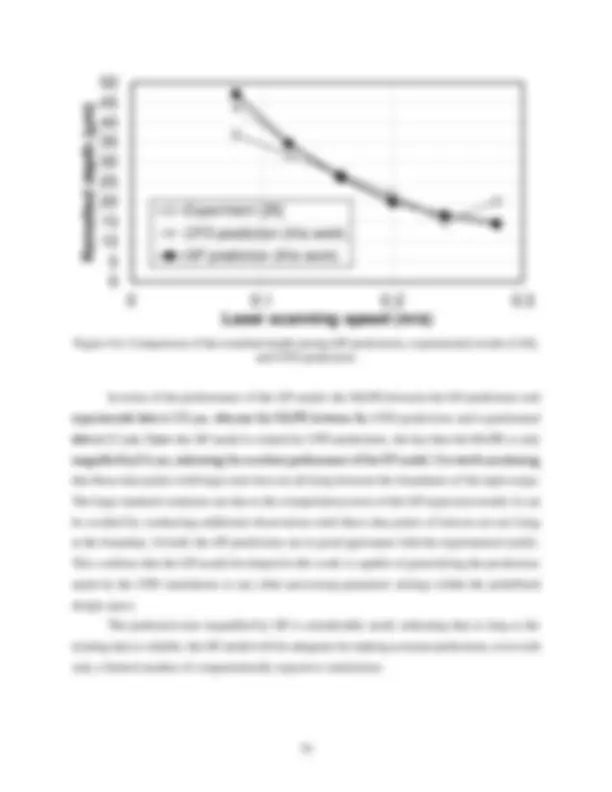
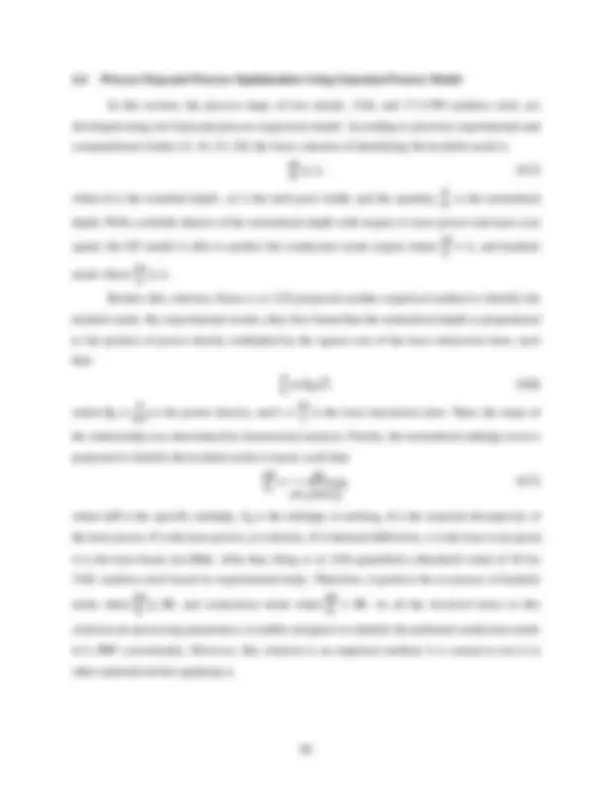
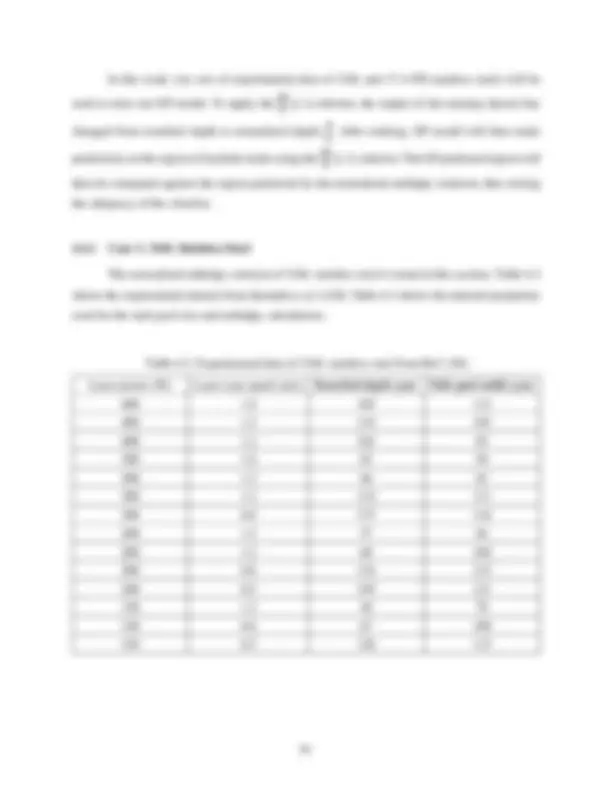
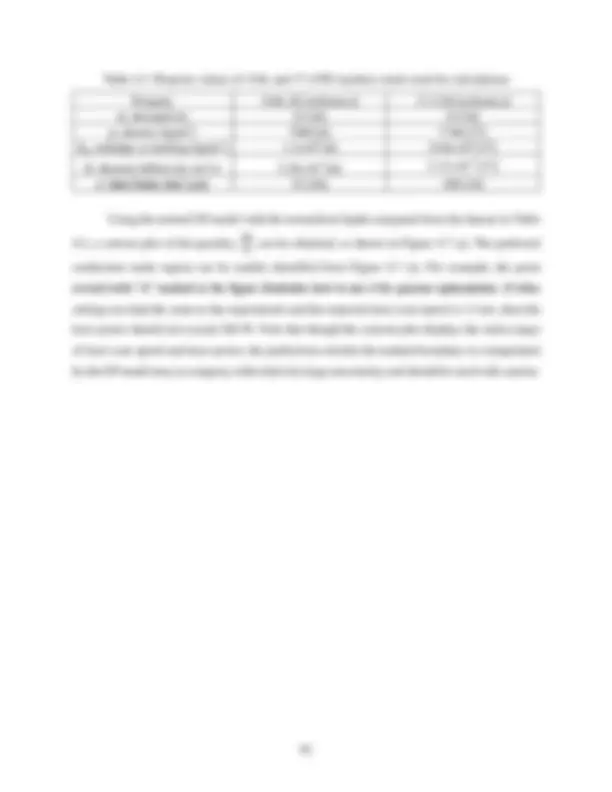
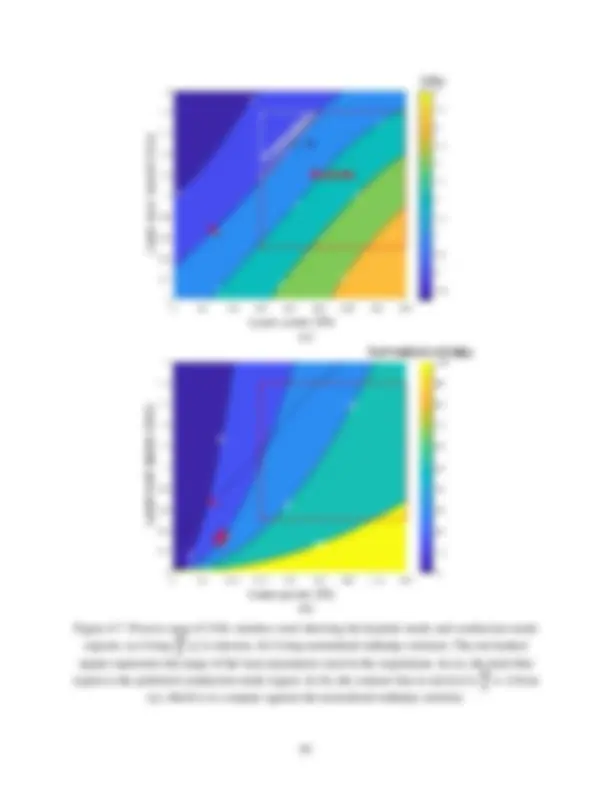
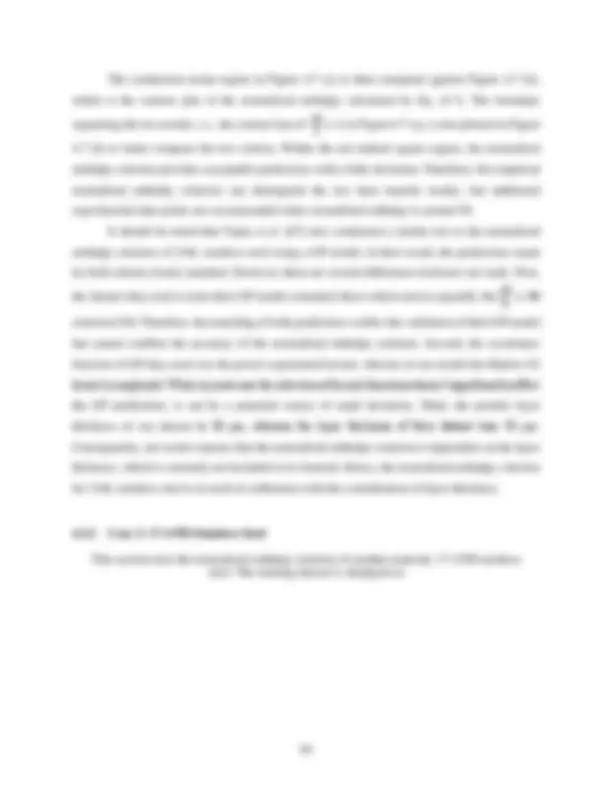

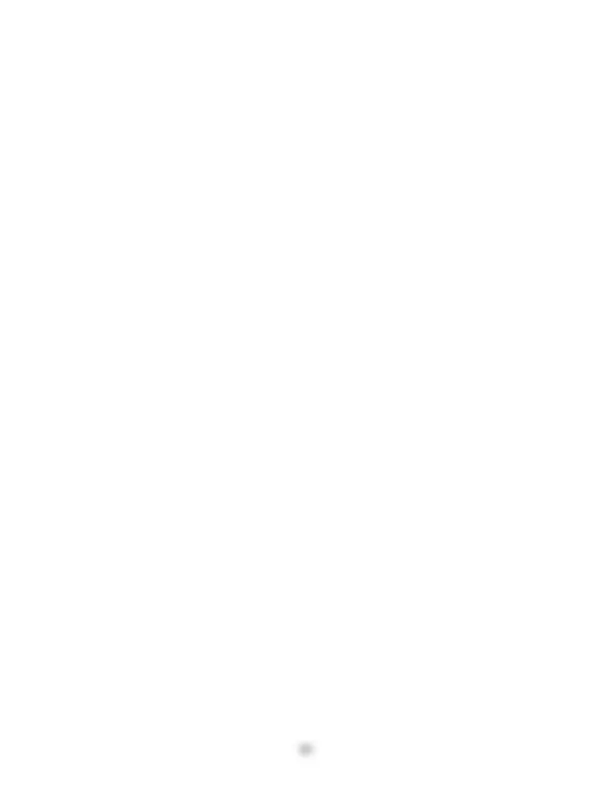
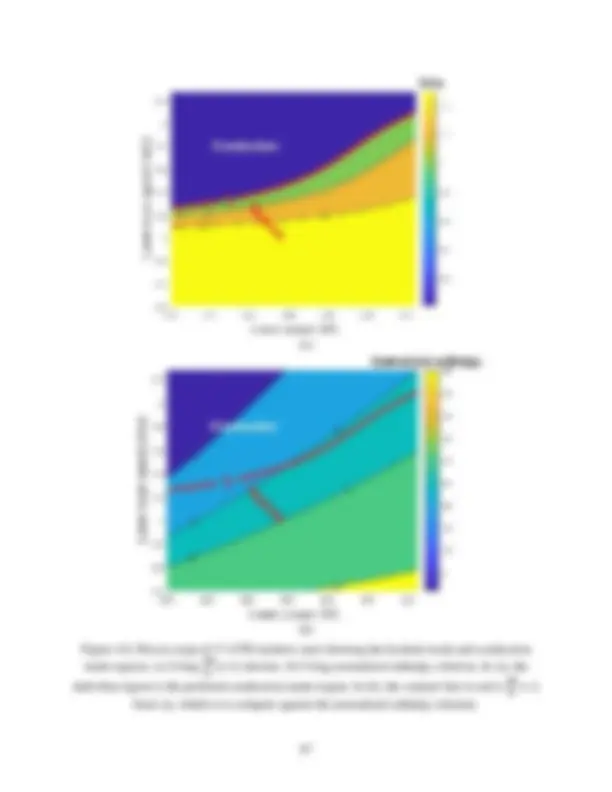
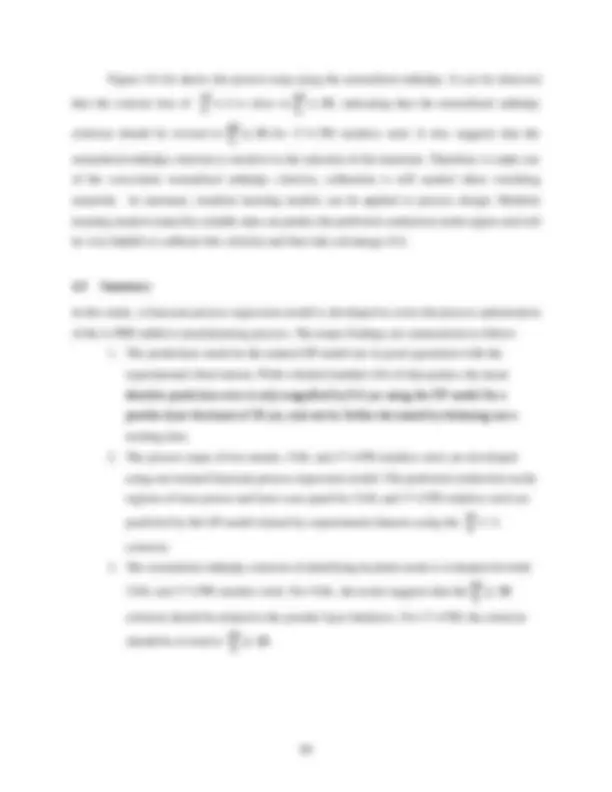
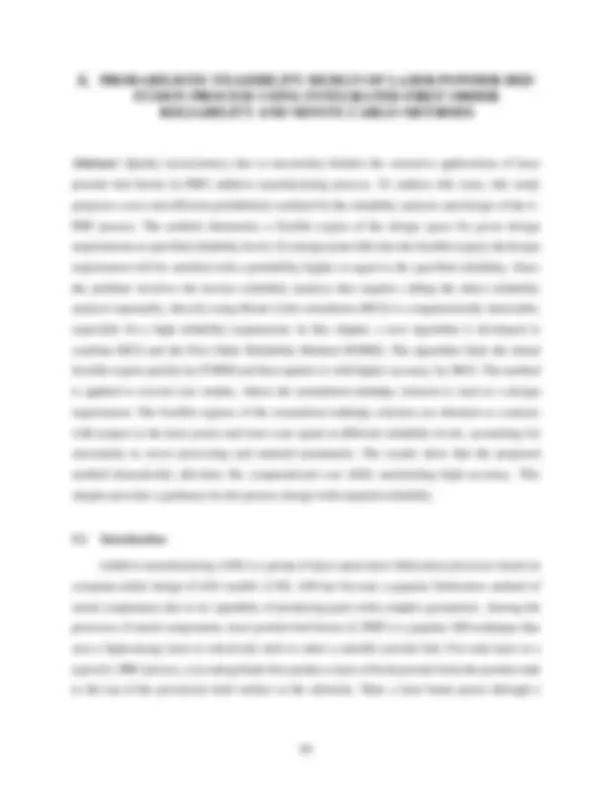
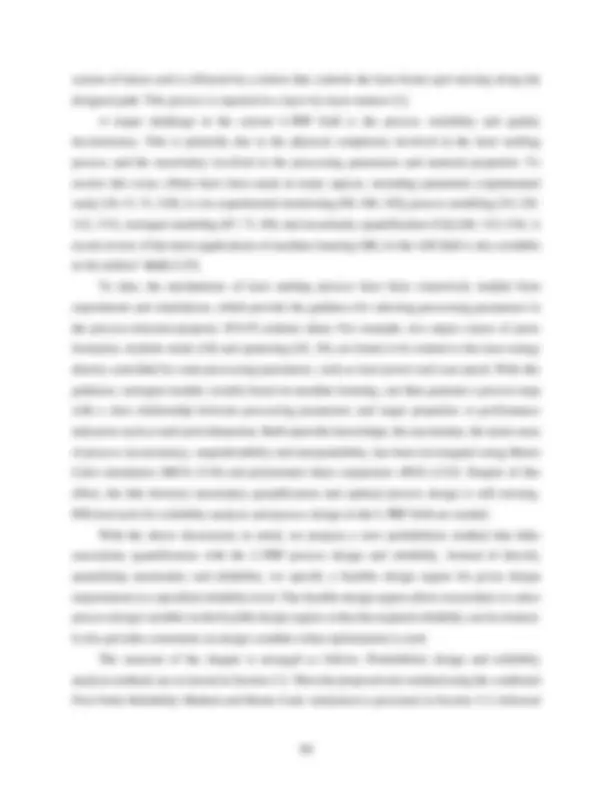
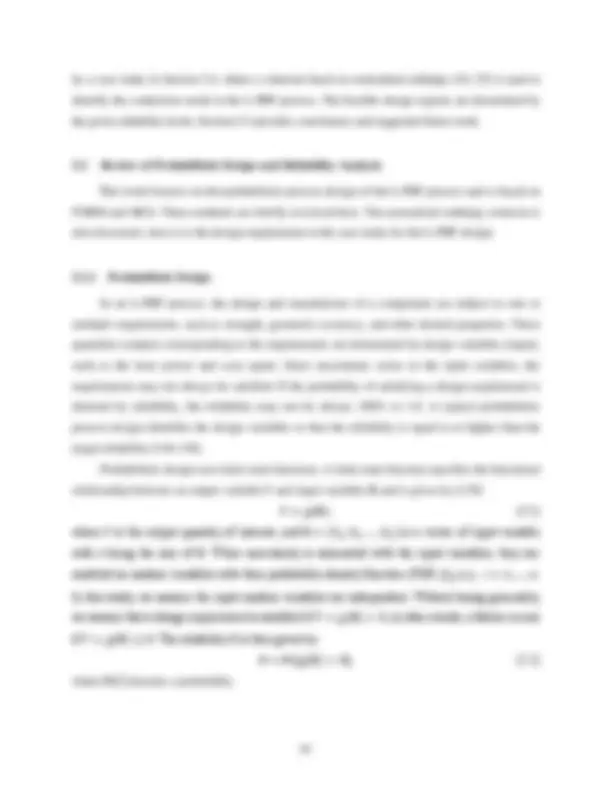
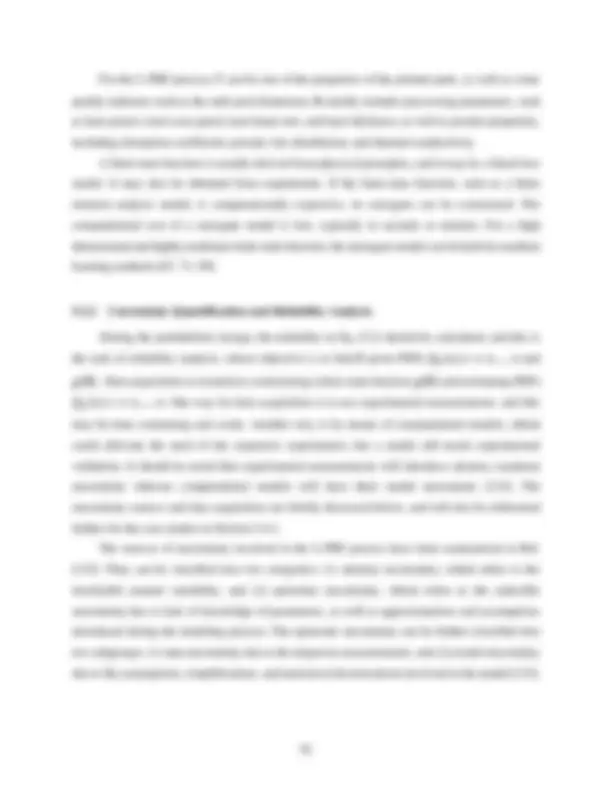
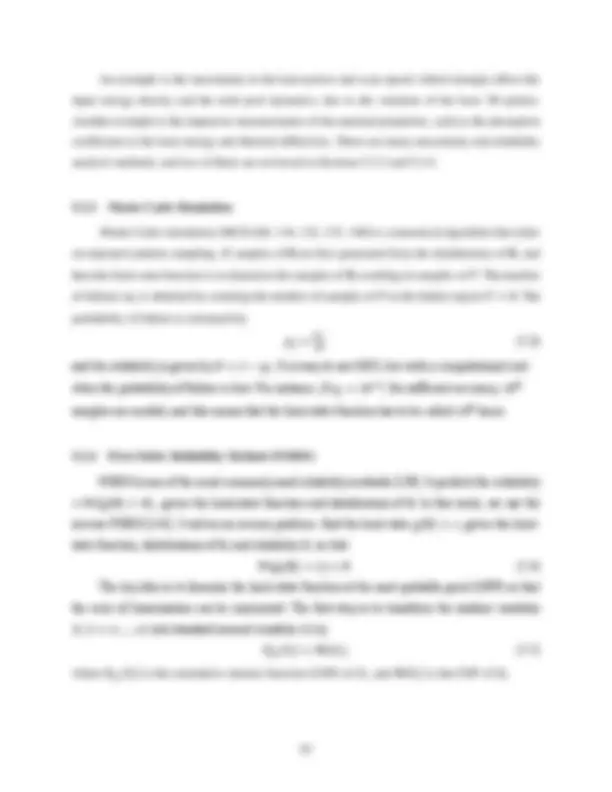
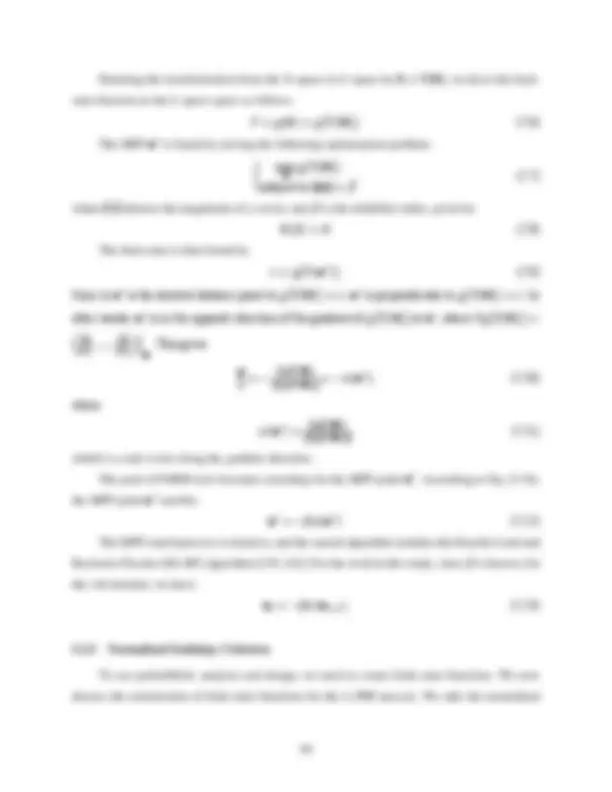
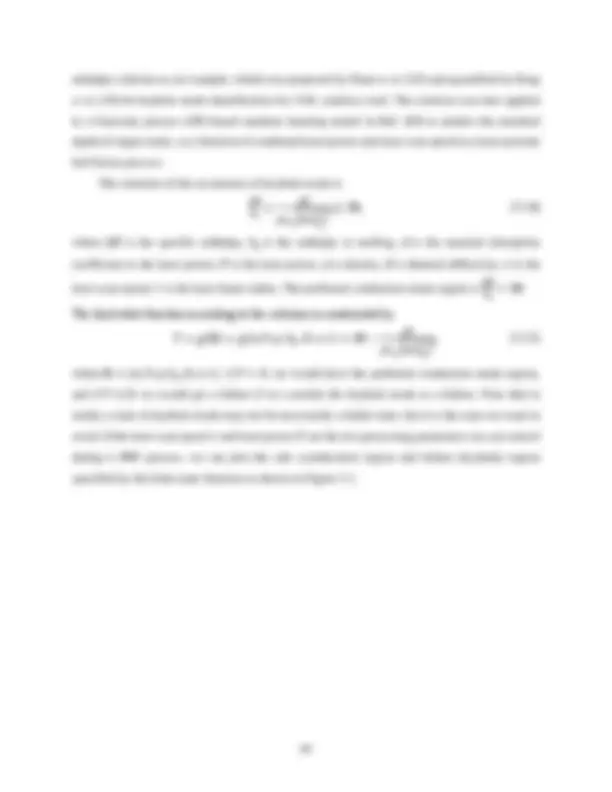
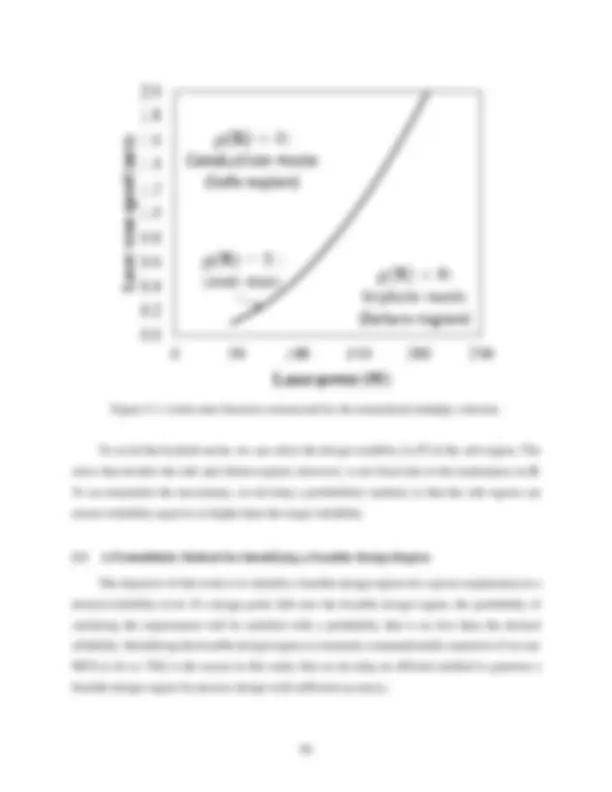
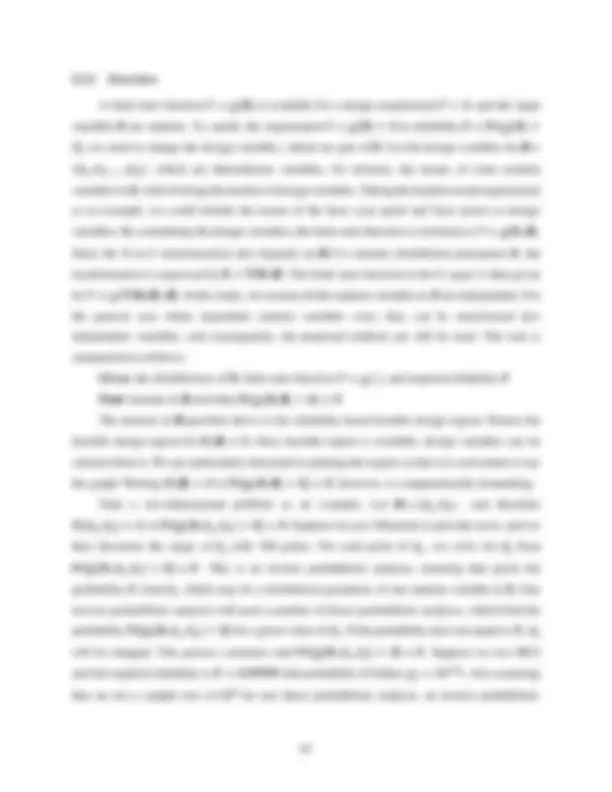
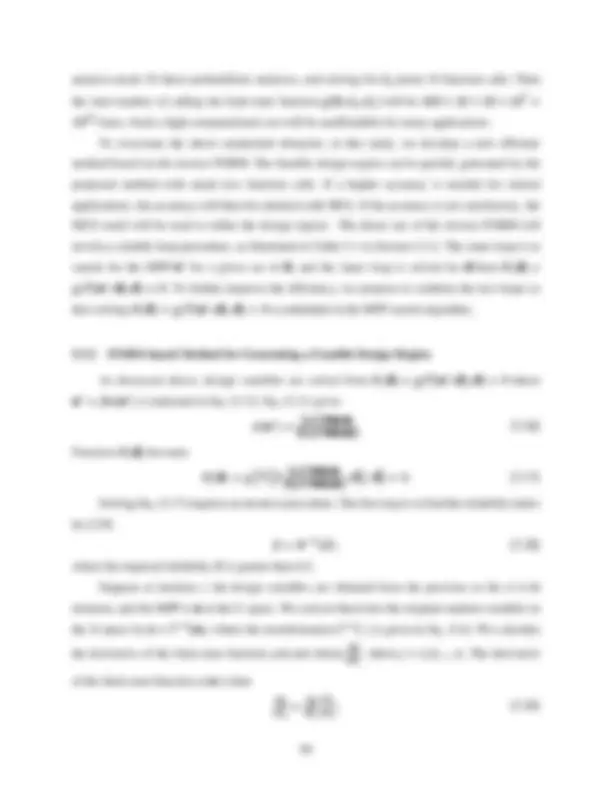
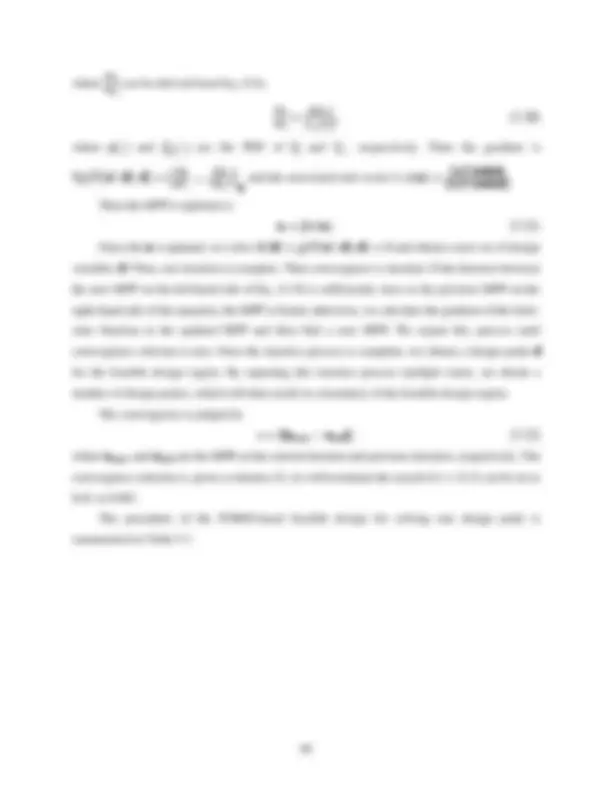
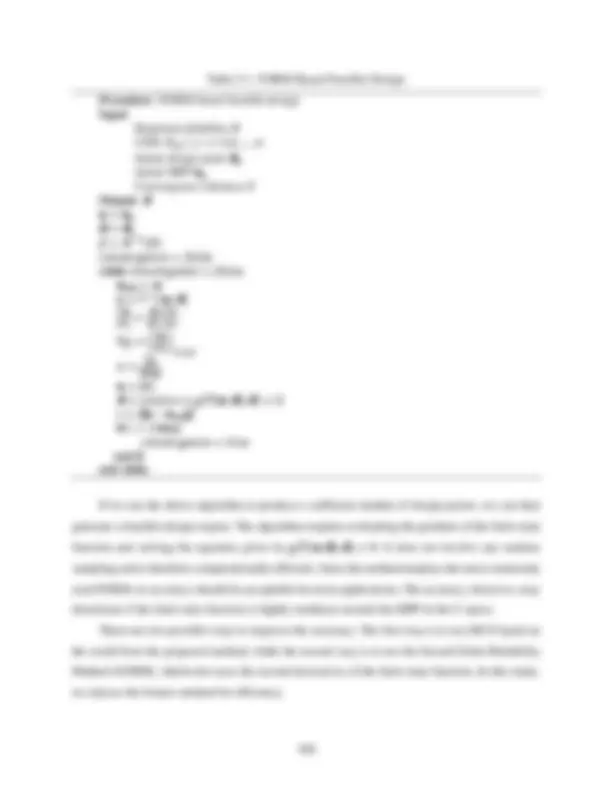
Study with the several resources on Docsity
Earn points by helping other students or get them with a premium plan
Prepare for your exams
Study with the several resources on Docsity
Earn points to download
Earn points by helping other students or get them with a premium plan
Community
Ask the community for help and clear up your study doubts
Discover the best universities in your country according to Docsity users
Free resources
Download our free guides on studying techniques, anxiety management strategies, and thesis advice from Docsity tutors
from Army Research Laboratory for suggestions on machine learning model. Special thanks to. Prof. Xiaoping Du for his valuable guidance in the probabilistic ...
Typology: Study notes
1 / 127
This page cannot be seen from the preview
Don't miss anything!
by Lingbin Meng A Dissertation Submitted to the Faculty of Purdue University In Partial Fulfillment of the Requirements for the degree of Doctor of Philosophy Department of Mechanical and Energy Engineering at IUPUI Indianapolis, Indiana May 2020
Dr. Jing Zhang, Co-Chair Department of Mechanical and Energy Engineering Dr. Bexin Wu, Co-Chair School of Mechanical Engineering Dr. Xiaoping Du Department of Mechanical and Energy Engineering Dr. Mohammad Al Hasan School of Computer & Information Science Shengfeng Yang Department of Mechanical and Energy Engineering Approved by: Dr. Jie Chen
First and foremost, I would like to express my sincere appreciation for my academic advisors, Professor Jing Zhang, and Professor Benxin Wu, for their expert advice, valuable guidance, and kind support during my study and research at Purdue University. I would also like to thank my committee members Professor Xiaoping Du, Professor Mohammad Al Hasan, and Professor Shengfeng Yang, for serving as my committee members, and their great help in my studies. The work is conducted under CCDC Army Research Laboratory Cooperative Research and Development Agreement (CRADA) 19- 013 - 001. I would like to thank Dr. Brandon McWilliams from Army Research Laboratory for suggestions on machine learning model. Special thanks to Prof. Xiaoping Du for his valuable guidance in the probabilistic engineering design and the first order reliability method, Dr. Tao Sun from Argonne National Laboratory for providing the high- speed synchrotron X-ray imaging data, and Prof. Yeon-Gil Jung from Changwon National University for 3D printing process. I also would like to thank my lab mates Dr. Linmin Wu, Dr. Yi Zhang, Xuehui Yang, Jian Zhang and many others, who gave me help in many aspects. Last but not the least, I would like to thank my parents, Xianghai Meng and Lei Feng, and my wife, Lijie Song, for their love and support during my doctoral studies and in my whole life.
5.4.1 Case 1: Normal Distribution and Standard Deviations are Fractions of Their Means ..
Table 3.1. ML regression applications in AM. ............................................................................. 51 Table 3.2. Confusion matrix of binary classification problems. ................................................... 56 Table 3.3. ML classification applications in AM. ........................................................................ 56 Table 4.1. CFD predictions and experimental results [32] at various combinations of laser scan speed and laser power ................................................................................................................... 75 Table 4.2. Experimental data of 316L stainless steel from Ref. [36] ........................................... 81 Table 4.3. Property values of 316L and 17-4 PH stainless steels used for calculations ............... 82 Table 4.4. Experimental observations of 17-4 PH stainless steel [34] ......................................... 85 Table 5.1. FORM-Based Feasible Design .................................................................................... 99 Table 5.2. Integrated FORM and MCS ....................................................................................... 101 Table 5.3. Distributions of input random variables .................................................................... 102 Table 5.4. Comparison of computational costs among FORM, FORM/MCS, and MCS methods ..................................................................................................................................................... 106
Figure 3.5. Procedure of geometric error compensation of Ti-6Al-4V in L-PBF process [71]. The input data are the thermal history and some processing parameters. The output data are the distortion. Error compensation is achieved by reverse the distortion in the CAD model. CAMP- BD represents Convolutional and artificial neural network for Additive Manufacturing Prediction using Big Data............................................................................................................................... 48 Figure 3.6. The cost estimation framework based on geometry and process similarities [72]. .... 49 Figure 3.7. Layer-wise relevance propagation through the trained neural network for polylactic acid (PLA) in fused filament fabrication (FFF) [78]: porpagation forward for prediction of tensile strength (top) and propagation backward for training the relevance of each input feature (bottom). ....................................................................................................................................................... 53 Figure 3.8. The procedure from thermal images (input) to porosity predictions (output) of Ti-6Al- 4V in L-PBF process. Some geometric features are extracted from the thermal images to train the ML models, which can then classify whether the printed product is porous (abnormal) or not (normal)......................................................................................................................................... 58 Figure 3.9. The flowchart of multi-scale CNN in defect detection in L-PBF process using multiple materials [93]. Images labeled with okay or 5 types of defect are used to train multi-scale CNN. The information of images is propagated in the multi-scale CNN using convolution and finally used to classify the type of defect. ................................................................................................ 59 Figure 3.10. Validation plot of GP in prediction of melt pool depth in terms of laser power and speed of 316L strainless steel in L-PBF process [67]. GP predictions are comparing against its training dataset. The closer from each point to the ideal 𝑦 = 𝑥 line, the more accurate the prediction is. In this plot, all points are exactly lying on the ideal line without any uncertainty, indicating that the GP perfectly represents the data in the training set, and also the fact that validation should never be done with the training dataset. ........................................................... 60 Figure 3.11. Procedure of a clustering analysis of AE signals of acrylonitrile butadiene styrene (ABS) in FFF process [116]. ......................................................................................................... 64 Figure 4.1. Remelted region (black) is shown in the temperature contour of the CFD model cut through view at the plane y = 0. 1723K is the liquidus of 316L stainless steel. The remelted depth d is illustrated as the average distance between the deepest melted region and the interface of the solid substrate and metal powders during the laser scanning. ...................................................... 73 Figure 4.2. Flow chart of the GP model with n - fold cross-validation method. ............................ 74 Figure 4.3. Regression surface of remelted depth as a function of laser power and scan speed made by the GP regression model (left) and the corresponding uncertainty based on the 95% confidence interval (right). The grid in left figure represents the mesh of the data points from CFD. ........... 76 Figure 4.4. Results of the n - fold cross-validation using the GP model and CFD model data ...... 77 Figure 4.5. Validation plot of GP predictions and experimental results ....................................... 78 Figure 4.6. Comparison of the remelted depth among GP predictions, experimental results [128], and CFD predictions ..................................................................................................................... 79
Figure 4.7. Process map of 316L stainless steel showing the keyhole mode and conduction mode regions. (a) Using 2 𝑑𝑤 ≤ 1 criterion. (b) Using normalized enthalpy criterion. The red dashed square represents the range of the laser parameters used in the experiment. In (a), the dark blue region is the preferred conduction mode region. In (b), the contour line in red text is 2 𝑑𝑤 = 1 from (a), which is to compare against the normalized enthalpy criterion. ................................... 83 Figure 4.8. Process map of 17-4 PH stainless steel showing the keyhole mode and conduction mode regions. (a) Using 2 𝑑𝑤 ≥ 1 criterion. (b) Using normalized enthalpy criterion. In (a), the dark blue region is the preferred conduction mode region. In (b), the contour line in red is 2 𝑑𝑤 = 1 from (a), which is to compare against the normalized enthalpy criterion. ................................ 86 Figure 5.1. Limit-state function constructed by the normalized enthalpy criterion. ..................... 95 Figure 5.2. Reliability contours at 𝑝𝑓 = 10 − 6 from FORM, FORM/MCS, MCS and deterministic methods in Case 1 ................................................................................................. 104 Figure 5.3. Reliability feasible design regions for different probabilities of failure (pf) in Case 1 ..................................................................................................................................................... 105 Figure 5.4. Reliability contours at 𝑝𝑓 = 10 − 6 from FORM, FORM/MCS, and deterministic methods in Case 2 ....................................................................................................................... 106 Figure 5.5. Reliability contours at 𝑝𝑓 = 10 − 6 from FORM, FORM/MCS, and deterministic methods in Case 3 ....................................................................................................................... 107
evaluated for both stainless steels. For 316L, the result suggests that the ∆𝐻 ℎ𝑠 ≥ 30 criterion should be related to the powder layer thickness. For 17-4 PH, the criterion should be revised to ∆𝐻 ℎ𝑠
Moreover, a new and efficient probabilistic method for the reliability analysis is developed in this work. It provides a solution to address quality inconsistency due to uncertainty in the L- PBF process. The method determines a feasible region of the design space for given design requirements at specified reliability levels. If a design point falls into the feasible region, the design requirement will be satisfied with a probability higher or equal to the specified reliability. Since the problem involves the inverse reliability analysis that requires calling the direct reliability analysis repeatedly, directly using MCS is computationally intractable, especially for a high reliability requirement. In this work, a new algorithm is developed to integrate MCS and FORM. The algorithm finds the initial feasible region quickly by FORM and then updates it with higher accuracy by MCS. The method is applied to several case studies, where the normalized enthalpy criterion is used as a design requirement. The feasible regions of the normalized enthalpy criterion are obtained as contours with respect to the laser power and laser scan speed at different reliability levels, accounting for uncertainty in seven processing and material parameters. The results show that the proposed method dramatically alleviates the computational cost while maintaining high accuracy. This work provides a guidance for the process design with required reliability. The developed SPH model is used to simulate the spattering phenomenon in the L-PBF process, to overcome the limitation of commercial CFD packages, including their incapability of phase change and particle sticking phenomena, which are however commonly seen in the spattering process. The SPH model is capable to couple heat transfer, particle motion and phase change. The sticking phenomenon observed in the experiment is successfully reproduced by the SPH model using a similar scenario. In summary, the modeling framework developed in this thesis can serve as a comprehensive tool for reliability-based design in the L-PBF process. The work is helpful for applying machine learning models in the additive manufacturing field.
1.1 Background Additive manufacturing (AM) is defined as a group of layer-upon-layer three-dimensional fabrication processes and previously applied for rapid prototyping. In the last decade, AM technology has rapidly evolved into a decent alternative for direct fabrication of tools and functional parts. Powder bed fusion (PBF) is an AM technique that uses a high-energy power source to selectively melt or sinter a metallic powder bed [1]. Due to the capability of producing parts with improved density, resolution, and surface finish, PBF tends to be the dominant AM technique for metallic materials [2]. Figure 1. 1 shows the schematic of the L-PBF equipment [1]. In a typical PBF process, for each new layer which is usually in the range of 20-50 μm thickness, a recoating blade pushes a layer of fresh powder from the powder tank to the top of the previously built surface or the substrate. Then, a high-energy power source is fired along the designed path controlled by a computer-aided design (CAD) model. Metal powders are selectively sintered by the high-energy power source. This process is repeated in a layer-upon-layer manner until the product is printed. Finally, the unfused powders will be wiped off from the powder bed for recycle and the printed product will be ready for use or post-processing. Based on the type of the energy source, PBF can be further divided into two major techniques [3]: (1) laser powder bed fusion (L-PBF), also known as selective laser sintering (SLS), selective laser melting (SLM) and direct metal laser sintering (DMLS), which uses a high-intensity laser beam as the power source, and (2) electron beam melting (EBM), which uses an electron beam. This thesis focuses on the L-PBF process.
the occurrence of the defects is highly dependent on numerous processing parameters [4], including laser power, laser scan speed, laser spot size, powder size, layer thickness, external pressure and material absorptivity, especially those parameters related to energy input. These process-structure-property (PSP) relationships have been discussed in many review articles [1, 6, 7]. Figure 1. 2. Examples of typical pores in PBF process: (a) two circular pores and (b) an acicular pore [5] Figure 1. 3. Examples of severe cracks in PBF process [6] Forerunners have made lots of efforts in process optimization by experimental [8-13] and computational study [14-17]. Figure 1. 4 [18] shows an image from an experimental study of L-
PBF process using high-speed x-ray in situ monitoring system. The formation of pore and spatters can be observed from this image. Figure 1. 5 [19] shows sample result from a computation study of L-PBF process. The melt pool dynamics is simulated by this study. Through these experimental and computational studies, the two major causes of defects in the L-PBF process, keyhole mode and spattering, have been well exposed and understood. They are discussed detailedly in Section 1.2.1 and 1.2.2, respectively. Both defect sources are highly dependent to many processing parameters. Thus, the optimization of processing parameters is critical to avoid these phenomena and ensure the quality of the printed parts. Figure 1. 4. Image taken from high-speed x-ray in situ monitoring system during L-PBF process: (a) laser energy is 340 W and (b) laser energy is 520 W. Formation of spatters and pore can be observed [20]
than in conduction mode [21]. Since the collapse of the cavities in keyhole mode may leave voids in the printed parts [22], the conduction mode is preferred in laser additive manufacturing. Since keyhole mode is a major cause of pore formation, identifying keyhole mode is critical to provide guidance on how to avoid its occurrence. According to previous experimental and computational studies [3, 10, 23, 24], the basic criterion of identifying the keyhole mode is 2 𝑑 𝑤
where 𝑑 is the remelted depth, 𝑤 is the melt pool width, and the quantity, 𝑑 𝑤 , is the normalized depth. Besides this criterion, King et al. [10] presented another criterion for 316L stainless steel to identify the keyhole mode using normalized enthalpy: ∆𝐻 ℎ𝑠
𝐴𝑃 𝜌ℎ𝑠√𝜋𝐷𝑣(𝜎 4 )
where ∆𝐻 is the specific enthalpy, ℎ𝑠 is the enthalpy at melting, 𝐴 is the material absorptivity of the laser power, 𝑃 is the laser power, 𝜌 is density, 𝐷 is thermal diffusivity, 𝑣 is the laser scan speed, 𝜎 is the laser spot size. This criterion enables designers to identify the preferred conduction mode in L-PBF conveniently. However, this is an empirical method proposed by Hann et al. [25]. By experimental results, they first found that the normalized depth is proportional to the product of power density, 𝑃𝑑 = 𝑃 𝜋𝜎^2 , and square root of the laser interaction time, 𝜏 = 2 𝜎 𝑣
. In other words, 𝑑 𝑤
Then, the slope was determined by dimension analysis. Since this criterion is an empirical method, it is crucial to test it to other materials before applying it. 1.2.2 Spattering Phenomenon Spattering is a physical phenomenon in laser powder bed fusion (L-PBF) process observed from experiments [26, 27] and is found to be the major cause of the structural defects in the printed products [28, 29]. Forerunners have made unremitting efforts in experiments to investigate the spattering phenomenon. Zhao et al. [18] applied high-speed synchrotron X-ray to monitor the L- PBF process of Ti-6Al-4V in situ , and found that some spatters tend to merge together and form larger particles. Andani et al. [30] used SEM images to quantify the spatters sizes and their distribution during PBF process with multi-laser technology. Through the comparison between
multi-laser and single laser scanning, they found that a higher number of working laser beams induces greater recoil pressure above the melting pools and thus more spatters are ejected from the molten pool. In addition, the spatter particles size is much larger than the raw powders. Large spatters tend to create an inclusion or remain as a non-melted region into the printed part, and thus degrade its quality. Guo et al. [31] used in-situ high-speed high-energy x-ray imaging to detailedly study the spattering mechanism and quantification as a function of time, environment pressure, and location in the L-PBF process. Under stationary laser impulse, as time goes by, the vaporization occurs after melting and generates intensive vapor jet which ejects the metal powders, and then argon gas flow forms and forces the particles surrounding the molten pool to move toward the molten pool. If the pressure of the surrounding argon gas is decreased, the intensity of the argon gas flow will also decrease, and thus powders are ejected with a large divergence angle as the vapor can expand freely. Figure 1. 6 [31] Shows the schematic of the pressure and time dependent spattering mechanism. Regarding the effect of location, the experiment was conducted under moving laser beam at normal pressure. They found that particles behind the laser beam tend to move towards laser beam entrained by argon gas flow, particles around the laser beam tend to be ejected by the evaporation recoil pressure, and particles ahead of the laser beam tend to incline towards the laser beam. Yin et al. [32] applied a laser confocal microscope to characterize the morphological features of Inconel 718 sample. The correlation between the laser power and the ejection angle was revealed by their study. Overall, the spattering mechanisms and its effect are well exposed by experiments.