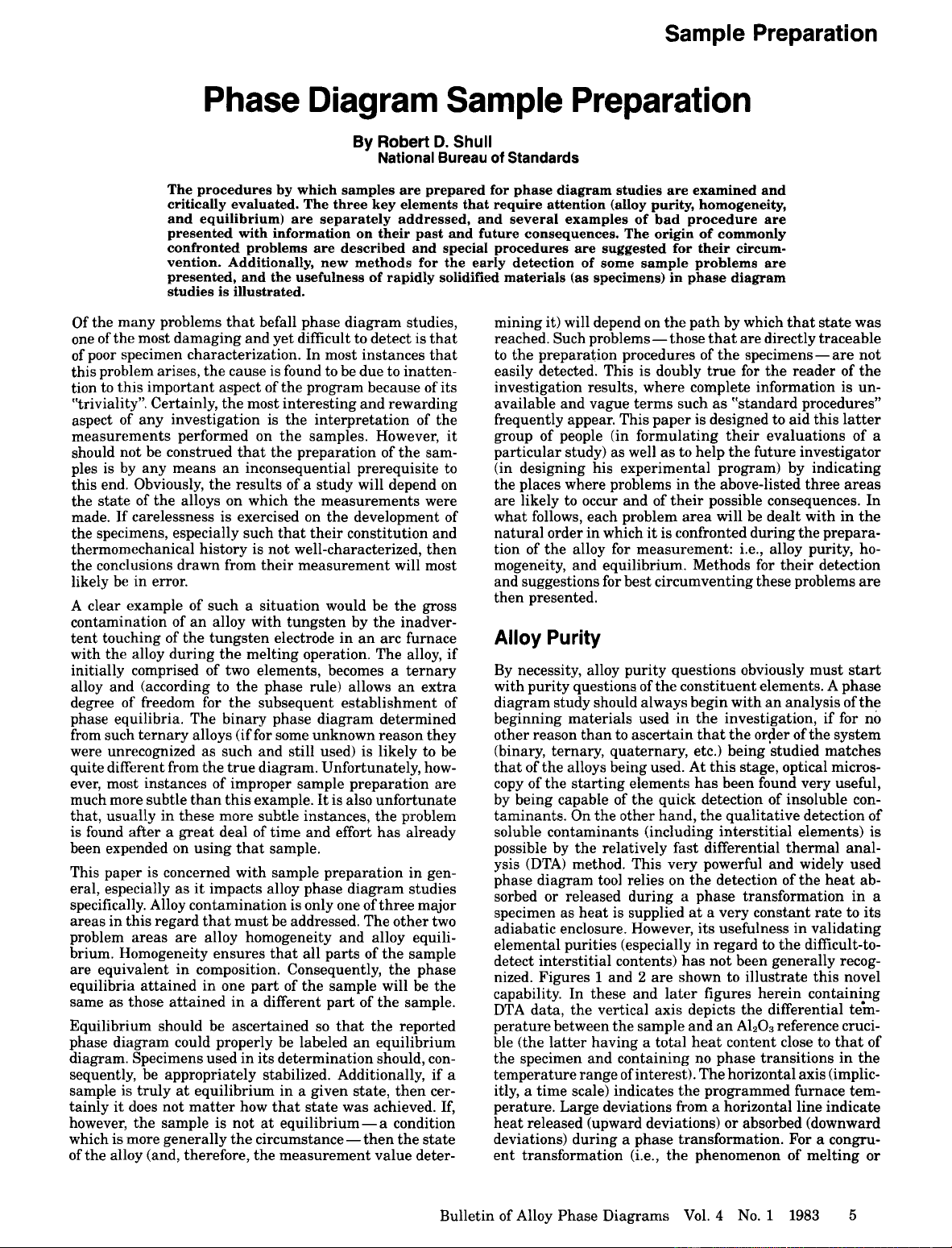

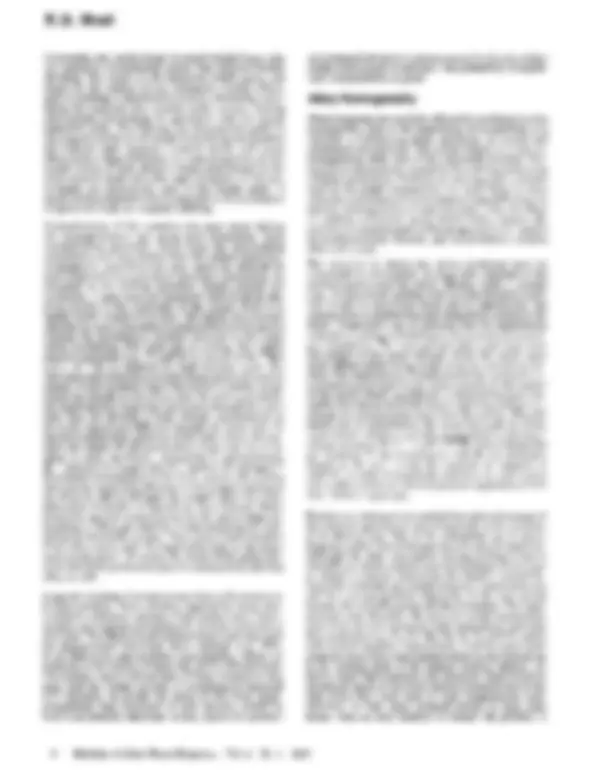
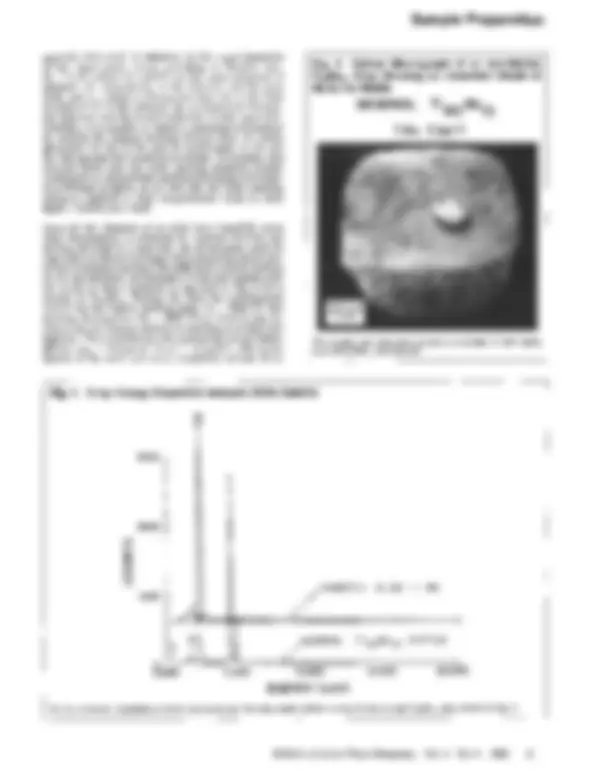
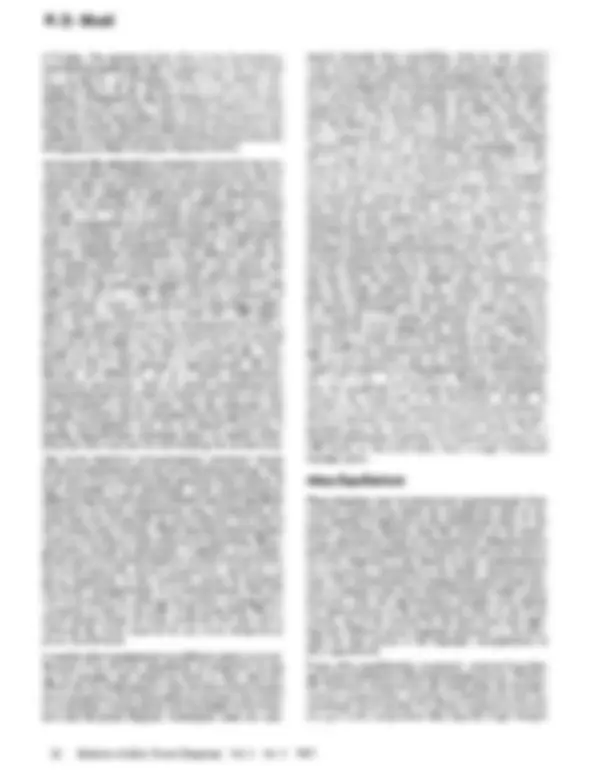
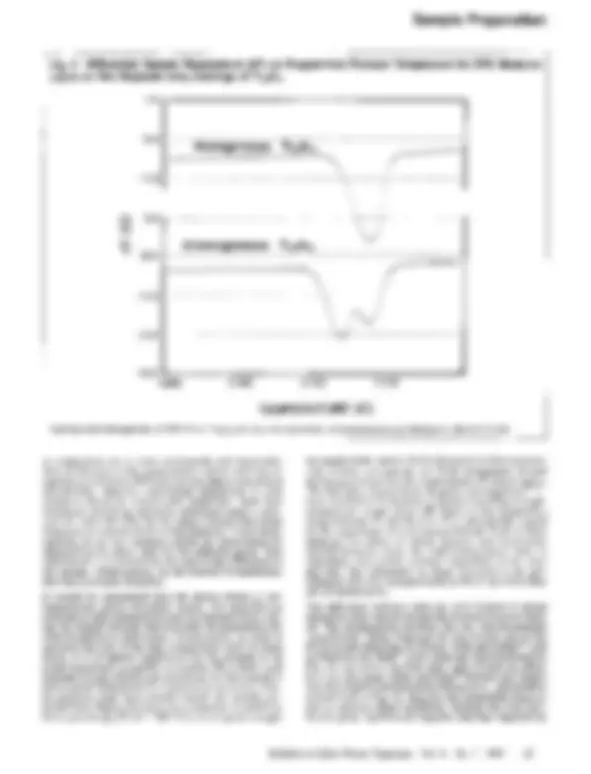
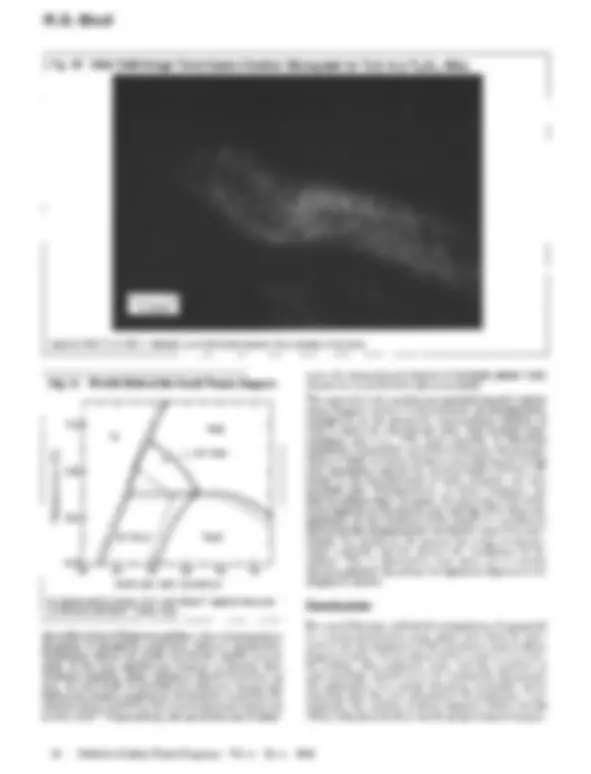
Study with the several resources on Docsity
Earn points by helping other students or get them with a premium plan
Prepare for your exams
Study with the several resources on Docsity
Earn points to download
Earn points by helping other students or get them with a premium plan
Community
Ask the community for help and clear up your study doubts
Discover the best universities in your country according to Docsity users
Free resources
Download our free guides on studying techniques, anxiety management strategies, and thesis advice from Docsity tutors
Typology: Lecture notes
1 / 11
This page cannot be seen from the preview
Don't miss anything!
Phase Diagram Sample Preparation
The procedures by which samples are prepared for phase diagram studies are examined and critically evaluated. The three key elements that require attention (aHoy purity, homogeneity, and equilibrium) are separately addressed, and several examples of bad procedure are presented with information on their past and future consequences. The origin of commonly confronted problems are described and special procedures are suggested for their circum- vention. Additionally, n e w methods for the early detection of some sample problems are presented, and the usefulness of rapidly solidified materials (as specimens) in phase diagram studies is illustrated.
Of the many problems that befall phase diagram studies, one of the most damaging and yet difficult to detect is that of poor specimen characterization. In most instances that this problem arises, the cause is found to be due to inatten- tion to this important aspect of the program because of its "triviality". Certainly, the most interesting and rewarding aspect of any investigation is the interpretation of the measurements performed on the samples. However, it should not be construed that the preparation of the sam- ples is by any means an inconsequential prerequisite to this end. Obviously, the results of a study will depend on the state of the alloys on which the measurements were made. ]f carelessness is exercised on the development of the specimens, especially such that their constitution and thermomechanical history is not well-characterized, then the conclusions drawn from their measurement will most likely be in error. A clear example of such a situation would be the gross contamination of an alloy with tungsten by the inadver- tent touching of the tungsten electrode in an arc furnace with the alloy during the melting operation. The alloy, if initially comprised of two elements, becomes a ternary alloy and (according to the phase rule) allows an extra degree of freedom for the subsequent establishment of phase equilibria. The binary phase diagram determined from such ternary alloys (if for some unknown reason they were unrecognized as such and still used) is likely to be quite different from the true diagram. Unfortunately, how- ever, most instances of improper sample preparation are much more subtle than this example. It is also unfortunate that, usually in these more subtle instances, the problem is found after a great deal of time and effort has already been expended on using that sample.
This paper is concerned with sample preparation in gen- eral, especially as it impacts alloy phase diagram studies specifically. Alloy contamination is only one of three major areas in this regard that must be addressed. The other two problem areas are alloy homogeneity and alloy equili- brium. Homogeneity ensures that all parts of the sample are equivalent in composition. Consequently, the phase equilibria attained in one part of the sample will be the same as those attained in a different part of the sample.
Equilibrium should be ascertained so that the reported phase diagram could properly be labeled an equilibrium diagram. Specimens used in its determination should, con- sequently, be appropriately stabilized. Additionally, if a sample is truly at equilibrium in a given state, then cer- tainly it does not matter how that state was achieved. If, however, the sample is not at e q u i l i b r i u m - - a condition which is more generally the circumstance-- then the state of the alloy (and, therefore, the measurement value deter-
mining it) will depend on the path by which that state was reached. Such p r o b l e m s - - those that are directly traceable to the preparation procedures of the s p e c i m e n s - - a r e not easily detected. This is doubly true for the reader of the investigation results, where complete information is un- available and vague terms such as "standard procedures" frequently appear. This paper is designed to aid this latter group of people (in formulating their evaluations of a particular study) as well as to help the future investigator (in designing his experimental program) by indicating the places where problems in the above-listed three areas are likely to occur and of their possible consequences. In what follows, each problem area will be dealt with in the natural order in which it is confronted during the prepara- tion of the alloy for measurement: i.e., alloy purity, ho- mogeneity, and equilibrium. Methods for their detection and suggestions for best circumventing these problems are then presented.
By necessity, alloy purity questions obviously must start with purity questions of the constituent elements. A phase diagram study should always begin with an analysis ofth e beginning materials used in the investigation, if for no other reason than to ascertain that the or.der of the system (binary, ternary, quaternary, etc.) being studied matches that of the alloys being used. At this stage, optical micros- copy of the starting elements has been found very useful, by being capable of the quick detection of insoluble con- taminants. On the other hand, the qualitative detection of soluble contaminants (including interstitial elements) is possible by the relatively fast differential thermal anal- ysis (DTA) method. This very powerful and widely used phase diagram tool relies on the detection of the heat ab- sorbed or released during a phase transformation in a specimen as heat is supplied at a very constant rate to its adiabatic enclosure. However, its usefulness in validating elemental purities (especially in regard to the difficult-to- detect interstitial contents) has not been generally recog- nized. Figures 1 and 2 are shown to illustrate this novel capability. In these and later figures herein containing DTA data, the vertical axis depicts the differential tem- perature between the sample and an A1203 reference cruci- ble (the latter having a total heat content close to that of the specimen and containing no phase transitions in the temperature range of interest). The horizontal axis (implic- itly, a time scale) indicates the programmed furnace tem- perature. Large deviations from a horizontal line indicate heat released (upward deviations) or absorbed (downward deviations) during a phase transformation. For a congru- ent transformation (i.e., the phenomenon of melting or
R. D. Shull
o.o
0 ~'~- 1.o i - -o
........ ,-~. , - - ~
\ .'
\ ,
........................................... : ............................................. ................... .............................................
T E M P E R A T U R E ( C ) Measured during heating at a rate of 2.5 ~
Fig. 2 Differential Sample Temperature (dT) vs
\ / / ...................................................... ................. i/ ...........................................................................
\
GASSY Ti o..................................................................................... \
- 2.o ............................................i~.... .. .... ., :
that of an allotropic crystal structure change of a pure element), it can be shown 1 that the shape of the DTA curve would be triangular, as is shown in Fig. 1 for the melting of a sample of pure Au. The critical aspects of the curve, insofar as purity is concerned, are the high sharpness of the initial deviation from the horizontal (occurring at the temperature of transformation), the linearity of the sub-
sequent deviation, and the abruptness of the transfor- mation conclusion (indicated by the reduction in devia- tion). The relatively fast exponential decay in d T back to the horizontal also is a result of the high purity of the sample, but is less quantitative. If the sample was not pure, the range in transformation t e m p e r a t u r e s that would consequently result would be reflected by signifi- cant rounding of the DTA curve at the beginning and end- ing points of the transformation as well as the loss of linearity in the central region. The thermal response char- acteristics of the measurement equipment also will con- tribute to a lack of sharpness in the transformation, but the effect is small. Observe, for example, the very slight effect at the beginning and end of the DTA arrest, shown in Fig. 1, fbr the melting of a sample of pure Au. Now, compare this curve with those shown in Fig. 2 for the a(cph) --*/3(bcc) congruent phase transition in two nomi- nally pure pieces of titanium. The top curve is for a sample of as pure a piece of bulk titanium as one is able to obtain. However, it is obvious (primarily from the lack of linearity immediately following the initial deviation in d T from the horizontal) that even this material is not completely pure. In fact, a later chemical analysis confirmed a 99.9% purity, but a content of 150 ppm oxygen and 20 ppm nitrogen (by weight). The bottom curve, however, is for a more typically obtained piece of high-purity t i t a n i u m - - 9 9. 9 % pure (300 ppm oxygen and 30 ppm nitrogen). The DTA analysis shows this sample contains a considerable interstitial con- tent. One might also note the effect of this interstitial contamination in raising the transition temperature for the transformation (i.e., as reflected by the increase in furnace temperature at which the first deviation in d T is detected). In this particular instance, the increase was approximately 3 ~
In general, most investigations pay attention to the purity of the starting materials. Therefore, problems in alloy contamination--for instance, that of the unintentional
R.D. Shull
Alloy Homogeneity
partially alleviated. A reduction in the vapor pressures of the constituents occurs according to Raoult's law: PA = XAP~ (where PA and P~ are the vapor pressures of element "A", respectively, in the solution and the pure form, and Xa, which is always less than 1.0, is the mole fraction of "A" in the solution). In an electric-arc furnace, the elements may be heated unevenly. In this apparatus, therefore, it is possible to obtain a controlled composition by melting the highest melting element first. Its initial placement on top of the pile of constituents in the arc furnace ensures this condition is realized. On melting, this element flows onto the lower melting elements located underneath it, immediately melting and fusing with them. If performed properly, at no time are the lower melting elements exposed to high temperatures while in their highly volatile pure state.
Once all the elements of an alloy have liquefied, gross alloy homogeneity is obtained by vigorous stirring and mixing, followed by a fast cool. An investigator must be especially careful at this stage when preparing alloys com- prised of elements having wide differences in both melting points and densities. An example of what m a y happen only too easily in these instances is depicted in Fig. 4 for a sample of TigoMolo. During the time the molybdenum (which has the higher melting point, TM = 2610 ~ was heating, the titanium (TM = 1668 ~ on which it was sit- ting in the arc furnace reached its melting point first and liquefied. The molybdenum, also possessing a much higher density (PMo = 10.2 g/cm 3 vs PTi -----4.5 g/cm3), fell to the bottom of the melt and never completely melted. Even
Fig. 4 Optical Macrograph of an Arc-Melted TigoMol0 Alloy Showing an Unmelted Chunk of Mo in the Middle
NOMINAL Ti9oMOlo
Fig. 5
X-ray Energy Dispersive Analysis (EDX) Spectra
M
1000
3000
2000
0 0.000 5.
10.000 15.000 20.
Sample Preparation
A O
Cu55Ti45 (As Cost)
--------.,,._..~ ................................................ le~ ............................................................................................................
. t l - 9 : "%. ,'- , ~,~ "4 \ / ' ' :.--,.,.;
o
.................................................................... , .............. .~ ............................... 9 ................................. ........
T E M P E R A T U R E (C)
o V
Cu55Ti45 (As Crystollized) r , ,. , , i i,,,
........................................................................................... '. ~..................................................................
-4.5 I I I
T E M P E R A T U R E (C)
R.D. Shull
Because the magnitude of the derivative, IdC/dX], is
Alloy Equilibrium
R. D. Shull
Fig. 10 Dark Field Image Transmission Electron Micrograph for Ti3AI in a Ti79AI21 Alloy
Aged at 1050 ~ for 165 h, followed by an immediate quench into a solution of icy brine.
Fig. 11 Fe-rich End of the Fe-AI Phase Diagram
I I [ i I p~' I i I ' I
700 il~II FeAI -
t
t / "'"
' , , / O~+Fe3A, ,I / F'e3A, i I I r
Atom per cent o l u m i n u m
As determined by Swann, Duff, and Fisher16 (dashed lines) and by Okamoto and Beck '7 (solid lines).
Conclusion
Sample Preparation
The assumption should be made that specimen problems do exist unless proven otherwise. The absence of prepara- tion data (or the presence of very cursory data) implies either inattention or blatant disregard for this factor. Ob- viously, neither attitude is conducive to good samples, and such investigations should be viewed with reservation.
Acknowledgment
The author would like to express his sincere appreciation to Dr. Archie McAlister for measuring much of the DTA data shown in this paper, Dr. Robert Reno for the TEM pictures, and Mr. Charles Brady for the optical metallo- graphy. The author would also like to thank Dr. John Cahn for helping interpret some of the data presented here. Special gratitude is also expressed to Prof. Paul A. Beck at the University of Illinois for initially imparting to the author a few years ago the importance of good alloy prepa- ration technique.
Utilization of Phase Diagrams
Phase diagrams are justifiably regarded as an important component of our technological society; the Bulletin will publish examples that illustrate their value in the development of new science, trouble shooting, manufacturing control, and the development of new materials. Readers are invited to share their experiences by submitting items to the Editor, in any area of application.
Phase Diagrams in Dental Metallurgy
All metals used in dentistry must have exceptional corro- sion resistance and high strength. They may be classified according to use into: (a) metals used for direct restora- tions; (b) metals used for casting indirect restorations; and (c) wrought metal wires and appliances used in orthodon- tics and oral surgery.
Gold foil and silver amalgam are compacted directly into a cavity for restoration. Silver-amalgam alloy consists of Ag3Sn, to which has been added copper and sometimes other alloying elements. Particles of this material are agi- tated with mercury and react with it to form a plastic mass that hardens rapidly. The phase relationships in the qua- ternary Ag-Sn-Cu-Hg system involved in this hardening reaction are not yet fully understood. The phases found in dental amalgam are, however, identifiable as phases found in the corresponding binary and ternary systems.
Many of the casting alloys are gold-base, and they are commonly used in the as-cast condition. Platinum, pal- ladium, and silver are used for solid solution strength- ening; iridium and ruthenium, which are nearly insoluble in gold, are used for grain refinement. Sometimes alloys containing 5% or more of copper are age-hardened by pre- cipitation of Au~Cu. In recent years, the high cost of gold has led to the use of alloys at both ends of the silver-
palladium system. These two metals exhibit complete mis- cibility in the solid state. Cobalt-chromium-base alloys have been used for casting for several decades, though the cobalt-chromium phase diagram still has not been fully established. Recently, nickel-chromium alloys have come into wider use. For this system the equilibrium structure for the range of chromium contents normally used is a solid solution of chromium in nickel. The wrought wires used in orthodontics are of austenitic stainless steel, nitinol (TiNi), and ELGILOY ~ alloy.* Phase relationships in these systems are well established. In oral surgery, austenitic stainless steel and alloys in the nickel-chromium and cobalt-chromium systems are used predominately. Overall, it is clear that the evolution of dental alloys has tended to be empirical. In some instances their metallurgy is understood in terms of phase diagrams, but, in others, e.g., ternary and higher-order alloys based on the cobalt- chromium system, basic information needed for such un- derstanding (such as the avoidance of sigma and other embrittling phases) is still missing.
*ELGILOY~is a registered trademark ofthe ElgiloyCo.,Div.ofAmerican Gage and Machine Co.~Elgin, IL 60120.
Contributed by A. A. Johnson and J.A. Von Fraunhofer, University of Louisville, Louisville, KY 40292.