
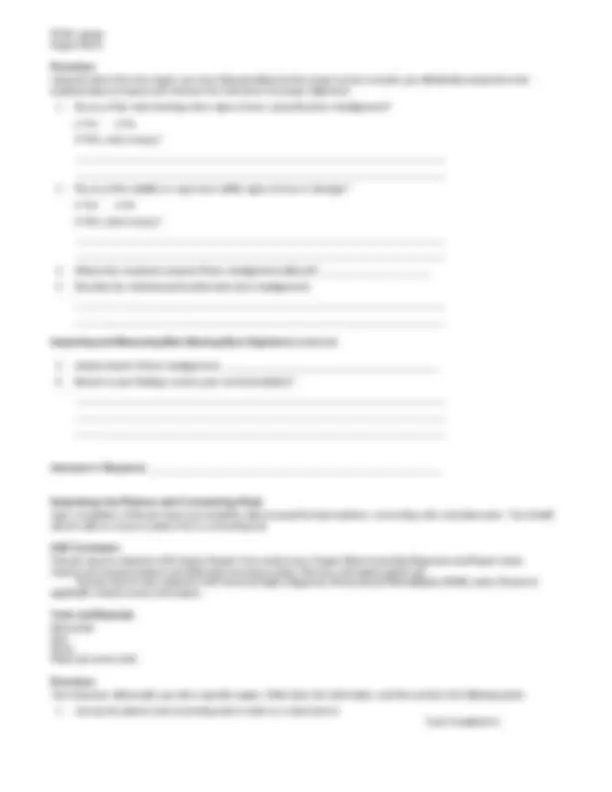
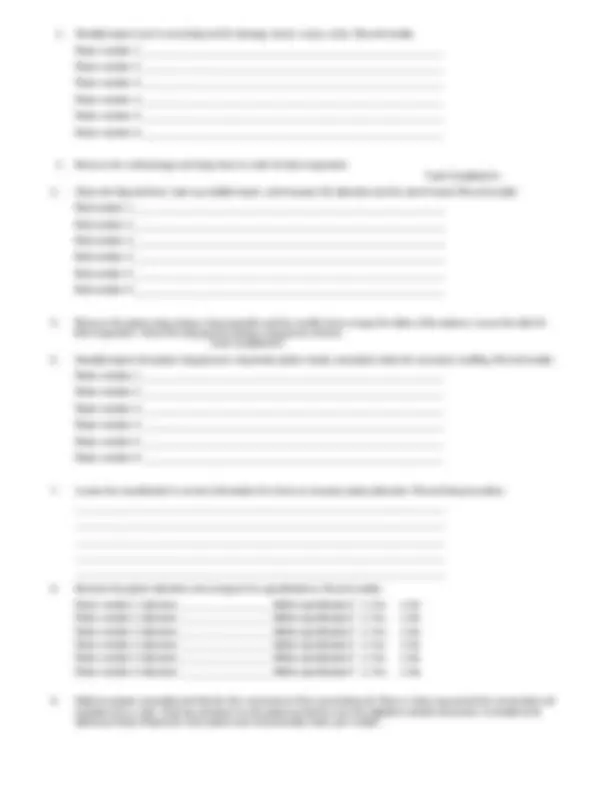
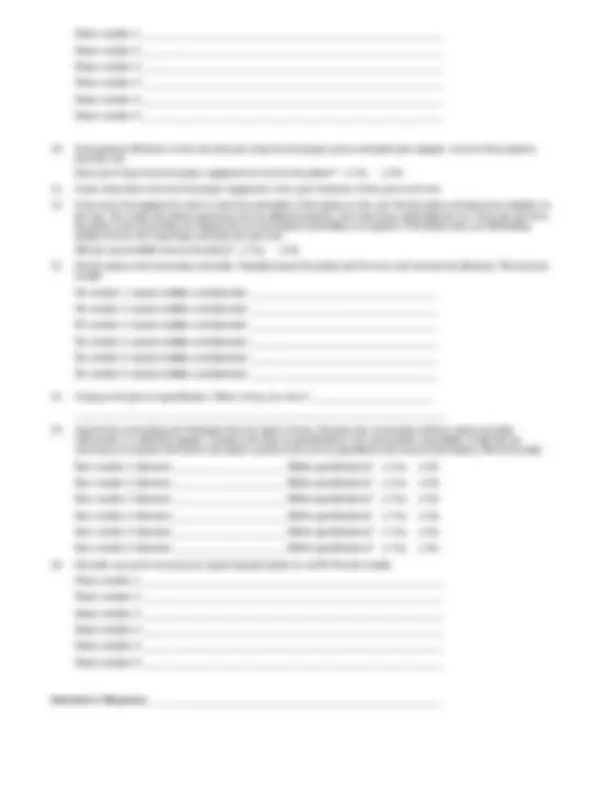
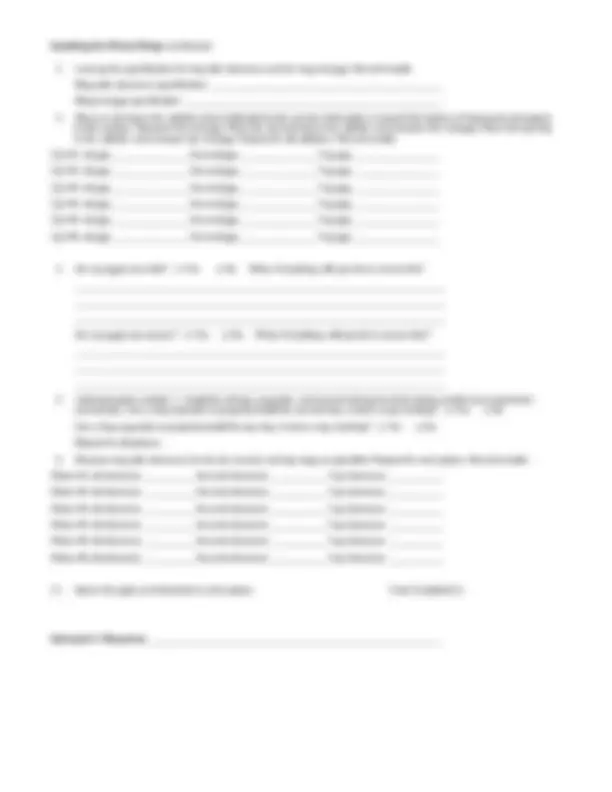
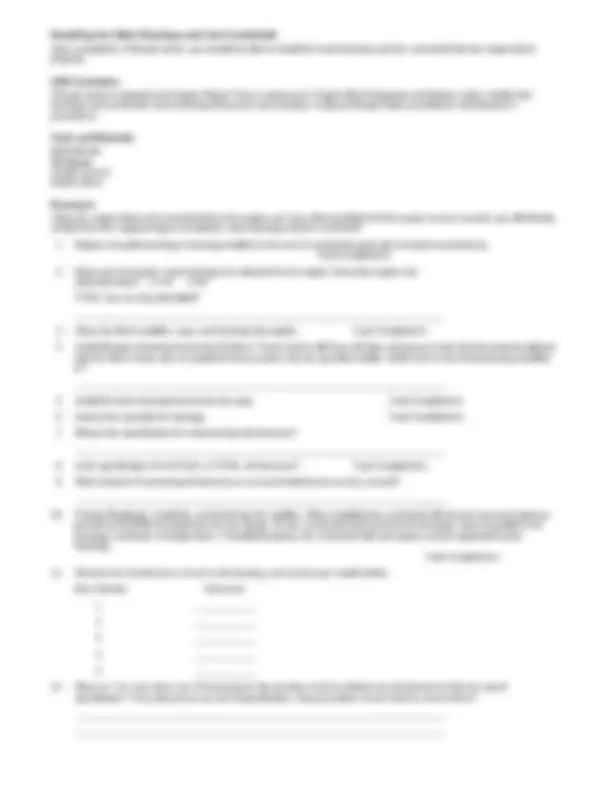
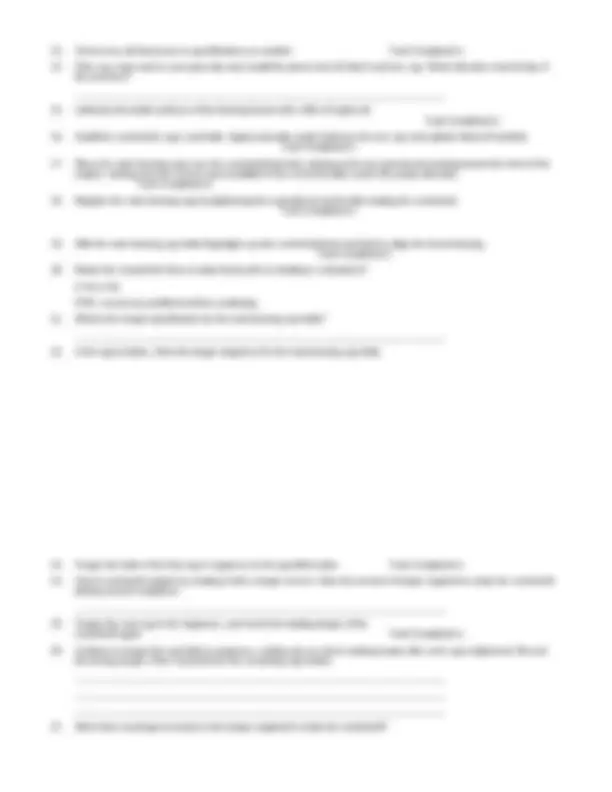
Study with the several resources on Docsity
Earn points by helping other students or get them with a premium plan
Prepare for your exams
Study with the several resources on Docsity
Earn points to download
Earn points by helping other students or get them with a premium plan
Community
Ask the community for help and clear up your study doubts
Discover the best universities in your country according to Docsity users
Free resources
Download our free guides on studying techniques, anxiety management strategies, and thesis advice from Docsity tutors
Material Type: Assignment; Professor: Reed; Class: Auto Eng Mech Repair; Subject: Automotive Technology; University: Community College of Philadelphia; Term: Spring 2008;
Typology: Assignments
1 / 11
This page cannot be seen from the preview
Don't miss anything!
AT 181 - Block, Crank, and Pistons worksheet. Names ________________________________________________________________ Date _______________________
Upon completion of this job sheet, you should be able to properly inspect and measure the engine block deck for warpage. ASE Correlation This job sheet is related to the Engine Repair Test’s content area: Engine Block Diagnosis and Repair; tasks: Visually inspect engine block for cracks, corrosion, passage condition, core and gallery plug holes, and surface warpage; determine necessary action. Tools and Materials Straightedge Feeler gauge Engine block Procedure Using the engine you have disassembled and the proper service manual, you will identify and perform the required steps to inspect and measure the engine block deck for warpage. 1 1. Specification for maximum warpage allowed. _______________________ 1 2. Special tools required to perform this procedure? 1 3. Make sure the deck surface is clean. Task Completed □ 1 4. Note any damage (nicks, scratches, etc.) to the deck surface.
1 5. Actual warpage measurement. Left bank _________________ Right bank _____________ 1 6. Based on your findings, what is your recommendation?
Instructor’s Response __________________________________________________________
Upon completion of this job sheet, you should be able to properly inspect and measure the cylinder walls for wear. ASE Correlation This job sheet is related to the Engine Repair Test’s content area: Engine Block Diagnosis and Repair; tasks: Inspect and measure cylinder walls; remove cylinder wall ridges; hone and clean cylinder walls; determine need for further action. Tools and Materials Dial bore gauge Engine block Procedure Using the block from the engine you have disassembled and the proper service manual, you will identify and perform the required steps to inspect and measure the cylinder walls for wear. 1 1. Do any of the cylinders have visible signs of wear or damage? □ Yes □ No If YES, which one(s)?
1 2. Is the cross-cut pattern still visible on all cylinder walls? □ Yes □ No If NO, on which ones is it no longer visible?
1 3. What is the specification for the bore? _____________________ 1 4. At what location in the cylinder is the bore measurement to be taken?
1 5. What is the specification for the maximum amount of taper? _________________ 1 6. At what locations in the cylinder is the taper measured?
1 7. What is the specification for the maximum amount of out-of-round? _________________
1 8. At what location in the cylinder is out-of-round measured?
1 9. Measure each cylinder at the locations required, and record your results. Bore Taper Out-of-Round Cylinder 1 _____ _____ ___________ Cylinder 2 _____ _____ ___________ Cylinder 3 _____ _____ ___________ Cylinder 4 _____ _____ ___________ Cylinder 5 _____ _____ ___________ Cylinder 6 _____ _____ ___________
Instructor’s Response __________________________________________________________
Upon completion of this job sheet, you should be able to properly inspect and measure the main bore alignment. ASE Correlation This job sheet is related to the Engine Repair Test’s content area: Engine Block Diagnosis and Repair; tasks: Inspect and measure main bearing bores and cap alignment and fit. Tools and Materials Straightedge
1 2. Visually inspect each connecting rod for damage, bend, cracks, nicks. Record results. Piston number 1 ____________________________________________________________ Piston number 2 ____________________________________________________________ Piston number 3 ____________________________________________________________ Piston number 4 ____________________________________________________________ Piston number 5 ____________________________________________________________ Piston number 6 ____________________________________________________________ 1 3. Remove the rod bearings and keep them in order for later inspection. Task Completed □
Piston number 1 ____________________________________________________________ Piston number 2 ____________________________________________________________ Piston number 3 ____________________________________________________________ Piston number 4 ____________________________________________________________ Piston number 5 ____________________________________________________________ Piston number 6 ____________________________________________________________
Rod bearing indications:
Corrective actions:
Instructor’s Response __________________________________________________________
Upon completion of this job sheet, you should be able to properly install piston rings. ASE Correlation This job sheet is related to ASE Engine Repair Test content area: Engine Block Assembly Diagnosis and Repair; tasks: Inspect, measure, and install piston rings. This job sheet is also related to ASE General Engine Diagnosis; Removal and Reinstallation (R&R) tasks: Research applicable vehicle service information. Tools and Materials Ring expander Feeler gauges Procedure Your instructor will provide you with a specific engine. Write down the information, and then perform the following tasks: 1 1. Locate the correct rings for your engine. Look up the correct installation of the ring gaps and draw a diagram showing it below:
Installing the Piston Rings (continued) 1 2. Look up the specification for ring side clearance and for ring end gap. Record results: Ring side clearance specification: ______________________________________________ Ring end gap specification: ___________________________________________________ 1 3. Place an oil ring in the cylinder where indicated by the service information or toward the bottom of ring travel and square it with a piston. Measure the end gap. Place the second ring in the cylinder and measure the end gap. Place the top ring in the cylinder and measure the end gap. Repeat for all cylinders. Record results: Cyl. #1: oil gap _______________ Second gap _______________ Top gap _________________ Cyl. #2: oil gap _______________ Second gap _______________ Top gap _________________ Cyl. #3: oil gap _______________ Second gap _______________ Top gap _________________ Cyl. #4: oil gap _______________ Second gap _______________ Top gap _________________ Cyl. #5: oil gap _______________ Second gap _______________ Top gap _________________ Cyl. #6: oil gap _______________ Second gap _______________ Top gap _________________ 1 4. Are any gaps too wide? □ Yes □ No What, if anything, will you do to correct this?
Are any gaps too narrow? □ Yes □ No What, if anything, will you do to correct this?
1 5. Lubricate piston number 1. Install the oil ring, expander, and second oil ring by hand, being careful not to twist them excessively. Use a ring expander to properly install the second ring. Is there a top marking? □ Yes □ No Use a ring expander to properly install the top ring. Is there a top marking? □ Yes □ No Repeat for all pistons. 1 6. Measure ring side clearance for the oil, second, and top rings as specified. Repeat for each piston. Record results: Piston #1 oil clearance __________ Second clearance ___________ Top clearance ___________ Piston #2 oil clearance __________ Second clearance ___________ Top clearance ___________ Piston #3 oil clearance __________ Second clearance ___________ Top clearance ___________ Piston #4 oil clearance __________ Second clearance ___________ Top clearance ___________ Piston #5 oil clearance __________ Second clearance ___________ Top clearance ___________ Piston #6 oil clearance __________ Second clearance ___________ Top clearance ___________
□ Yes □ No If YES, stop and locate the cause of the problem.